PCD 刀具车削铝合金表面粗糙度的研究
2016-10-27 来源:阳江职业技术学院 深圳信息职业技术学院 作者:乔龙阳 刘白
摘 要:影响PCD 刀具车削铝合金表面粗糙度的主要因素是切削速度、进给量、背吃刀量。以黄金分割法设计了实验方案,优选了三因素的水平范围,用等距法设置了水平值。实验结果表明,对工件车削表面粗糙度影响最大的因素是进给量,次之是切削深度,切削速度的影响最小。通过正交实验法验证了上述实验数据并筛选了含优区间,获得了本工艺的最佳切削参数。
关键词:PCD 刀具;车削;铝合金;黄金分割法;表面粗糙度
0. 引言
为满足使用性能、外形美观等要求,5052 铝合金产品的表面粗糙度需达到Ra0.4 以上的技术要求。但是,传统加工普遍采用硬质合金刀具低速车削加工,切屑容易与刀具发生“胶焊”或粘连,形成积屑瘤,加工质量差、生产效率非常低[1-2] 。
PCD 刀具材料硬度高、导热性好、摩擦系数小,使得切屑变形和切削力降低、刀具磨损缓慢、切削过程更为稳定,有利于降低表面粗糙度[3-5] ,高速车削[6] 时零件表面可达到镜面效果,是目前车削铝合金理想的刀具材料。不足之处是针对5052 铝合金的研究,大多是面向其生产工艺[7] 、焊接组织和性能[8-9] 等方面的研究,而针对其车削加工性能的实验研究很少,因此开展PCD 刀具车削铝合金表面粗糙度的研究,对于提高这类材料产品质量和生产效率有着现实的意义。
铝合金车削性能相关的实验研究,大多采用正交实验或单因素实验等方法,这些方法存在实验次数多、实验精度不高的缺点。现以黄金分割法优选影响5052 铝合金表面粗糙度的切削参数因素水平范围,以等距法确定因素水平值,以正交实验筛选验证,得出影响表面粗糙度的主要因素,确定临界区域,以黄金分割法为单因素考察方法,确定PCD 刀具车削5052 铝合金表面粗糙度的最佳工艺条件。
1. 黄金分割法实验原理
黄金分割法是通过逐步缩小搜索区间,来求得一元函数极值点近似值的一种方法,又称为0.618 法。黄金分割法实验点选取,如图1 所示,实验范围[a,b] ,将第一个实验点x1安排在实验范围内的0.618 处(距左端点a),即x1 =a+(b-a)×0.618,得到实验结果f(x1 );再在x1的对称点x2 ,即x2 = a+(b -a) ×0. 382,得到实验结果f(x2 ),且f(x) 值越大,效果越好。若f(x1 ) >f(x2 ),即f(x1 )比f(x2 )好,则根据“留好去坏”的原则,去掉实验范围[a,x2 ] 部分,在[x2 ,b] 内继续实验。以后每次取一个试点,比较2 个结果,去坏留好,进一步缩小范围,进一步做实验。
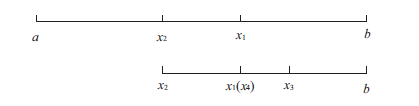
图1 黄金分割法实验点提取示意图
在生产实践和科学实验中,应用黄金分割法单因素实验可以有效减少实验次数,去掉“劣”点部分,保留“优”点部分,快速逼近真实值,并得到更为精准的实验数据。
2. 实验条件
实验材料:5052 铝合金,规格为Φ60 mm×55 mm 的铝合金管,壁厚4 mm,采用专用向心结构夹具装夹定位。
刀具材料:三菱公司PCD
材质MD220。
实验机床:XKNC-50G 精密数控车床,主轴最大转速6 000 r/ min。
实验仪器:JB-3C 粗糙度测试仪,分辨率0.001 μm,Ra 值测量范围0.001-10 μm。
车削环境:湿式车削,采用煤油作为切削液。
评价方法:取轮廓算术偏差Ra作为评价参数,测量时取样长度为1 mm,评定长度为5 mm。
3. 实验方法
为了获得较好的实验效果,对影响表面粗糙度较大的切削参数三因素切削速度、进给量和背吃刀量,开展黄金分割法优选实验,逐步缩小实验范围,直至取得最佳的实验数据。
3.1 黄金分割法优选实验
1) 利用黄金分割法确定进给量的水平范围
依据王洪祥等[10] 金刚石车削表面微观形貌形成机理的研究,认为表面粗糙度值与进给量和刀尖圆弧半径存在如下关系:

依据此经验公式,选取进给量实验范围[0.02,0.20]、背吃刀量0.3 mm、切削速度600 m/ min。按黄金分割法实验点的提取步骤,在[0.02,0.20]的0.618 处取值,选取第1 实验点为:
P1 =0.02+0.618(0.20-0.02)= 0.131 2
第2 实验点为:
P2 =0.02+0.382(0.20-0.02)= 0.088 7
实验测得P2的表面粗糙度值Ra1.375 μm 优于P1 的表面粗糙度值Ra1.841 μm,则舍弃不包括P1 点的以外部分,在留下部分再找出P2的对称点P3。
第3 实验点为:
P3 =0.02+0.382(0.131 2-0.02)= 0.062 5
实验测得P3的表面粗糙度值Ra0.843 μm 好于P2 的表面粗糙度值Ra1.275 μm,则舍弃不包括P2 点的以外部分,在留下的部分中找到P3的对称点。
第4 实验点为:
P4 =0.02+0.382(0.088 7-0.02)= 0.046 2
实验测得的P4的表面粗糙度值Ra0.495 μm 好于P3的表面粗糙度值Ra0.843 μm,则舍弃不包括P3 的以外部分,在留下的部分中找到P4的对称点。
P5 =0.02+0.382(0.062 5-0.02)= 0.036 2
实验测得的P5的表面粗糙度值Ra0.371 μm 好于P4的表面粗糙度值Ra0.495 μm,则舍弃不包括P4 的以外部分。
进给量对表面粗糙度的影响,如图2 所示。随着进给量的增大,工件表面粗糙度值显著增大。实验点所在实验范围包括含优点,则实验结束,优选实验范围为[0.02,0.046] 。
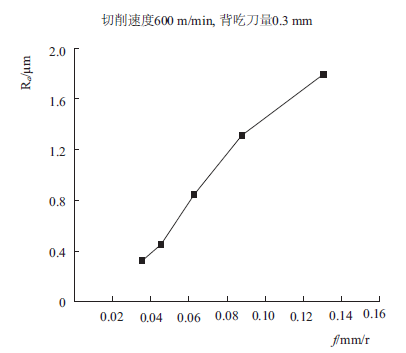
图2 进给量对表面粗糙度的影响
2) 利用黄金分割法确定切削速度的水平范围
选取切削速度实验范围[500,1 000]、背吃刀量0.3 mm、进给量0.1 mm/ r。按黄金分割法实验点的提取步骤,在[500,1000]的0.618 处取值,选取第1 实验点为:
P1 =500+0.618(1 000-500)= 809
第2 实验点为:
P2 =500+0.382(1 000-500)= 691
实验测得P1的表面粗糙度值Ra1.241 μm 优于P2 的表面粗糙度值Ra1.375 μm,则舍弃不包括P2 点的以外部分,在留下部分再找出P1的对称点P3。
第3 实验点为:
P3 =691+0.618(1 000-691)= 882
实验测得P3的表面粗糙度值Ra1.233 μm 好于P1 的表面粗糙度值Ra1.241 μm,则舍弃不包括P1 点的以外部分。
切削速度对表面粗糙度的影响,如图3 所示。随着切削速度的增大,工件表面粗糙度值逐渐减小,在切削速度达到800 m/ min 以上值后,对表面粗糙度的影响降低,表面粗糙度值趋于稳定。因此,实验结束,优选范围为[809,1 000] 。
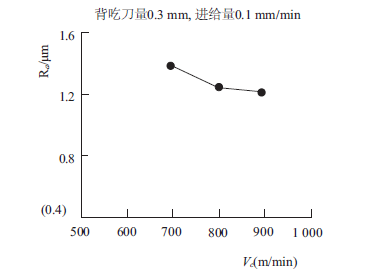
图3 切削速度对表面粗糙度的影响
3) 利用黄金分割法确定背吃刀量的水平范围
选取背吃刀量实验范围[0.05,1.0]、进给量0.1 mm/ r、切削速度600 m/ min。按黄金分割法实验点的提取步骤,在[0.05,1.0]的0.618 处取值,选取第1 实验点为:
P1 =0.05+0.618(1.0-0.05)= 0.637 1
第2 实验点为:
P2 =0.05+0.382(1.0-0.05)= 0.412 9
实验测得P2的表面粗糙度值Ra1.415 μm 优于P1 的表面粗糙度值Ra1.554 μm,则舍弃不包括P1 点的以外部分,在留下部分再找出P2的对称点P3。
第3 实验点为:
P3 =0.05+0.382(0.637 1-0.05)= 0.274 3
实验测得P3的表面粗糙度值Ra1.293 μm 好于P2 的表面粗糙度值Ra1.415 μm,则舍弃不包括P2 点的以外部分,在留下的部分中找到P3的对称点。
第4 实验点为:
P4 =0.05+0.382(0.412 9-0.05)= 0.188 6
实验测得的P4的表面粗糙度值Ra1.271 μm 好于P3的表面粗糙度值Ra1.293 μm,则舍弃不包括P3 的以外部分,在留下的部分中找到P4的对称点。
P5 =0.05+0.382(0.274 3-0.05)= 0.135 7
实验测得的P4的表面粗糙度值Ra1.271 μm 好于P5的表面粗糙度值Ra1.280 μm,则舍弃不包括P5 的以外部分。
背吃刀量对表面粗糙度的影响,如图4 所示。随着切削深度的增大,工件表面粗糙度值逐渐增大,增大趋势不明显;但在切削深度小于0.1 mm 时,测得工件表面粗糙度又趋于反方向细微增大。实验结束, 优选范围为[0.135 7,0.274 3] 。
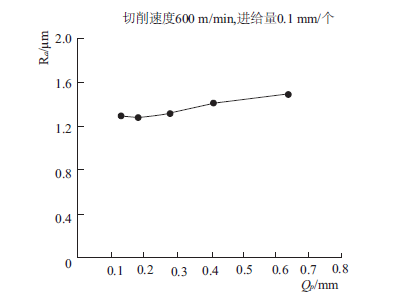
图4 背吃刀量对表面粗糙度的影响
3.2 等距法确定因素水平值
依据等距法,切削速度范围[809,1 000] ,因素水平值为809、905、1 000;进给量范围[0.02,0.046] ,因素水平值为0.02、0.033、0.046;背吃刀量范围[0.13,0.27] ,因素水平值为0.13、0.20、0.27。
3.3 正交实验
采用三因素三水平L9(33)组合切削参数,3 个因素分别是:切削速度νc 、进给量f 和背吃刀量ap ,以工件表面粗糙度作为质量特征,评价切削参数的优劣。正交实验的因素水平表见表1。
表1 正交实验因素水平表
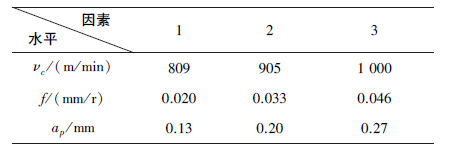
t 正交实验方案与结果见表2。
表2 正交实验方案及结果
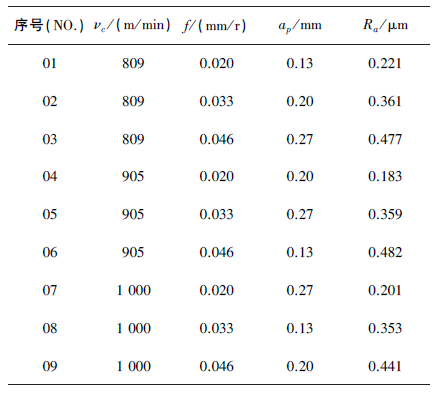
由实验数据分析,对工件表面粗糙度影响最大的因素是进给量,次之是切削深度,切削速度的影响最小。如图5 所示,切削参数对表面粗糙度的影响验证,随着切削速度的增大,工件表面粗糙度值逐渐减小;随着切削深度的增大,工件表面粗糙度值逐渐增大;随着进给量的增大,工件表面粗糙度值显著增大。工件表面二次元成像微观机理显示,随进给量的增大,走刀间距变大,工件表面上纹路清晰,是造成工件表面粗糙度值变大的主要因素。
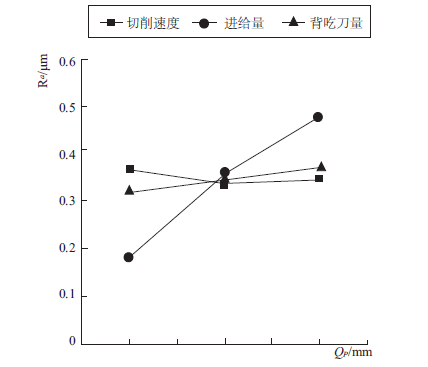
图5 切削参数对表面粗糙度的影响
正交实验验证:在稳定的高速车削环境下,切削速度与切削深度对表面粗糙度值影响较小,进给量是造成工件表面粗糙度值变大的主要因素。提取进给量的含优区间为[0.033,0.046]。
3.4 黄金分割法单因素实验
选取进给量实验范围[0. 033,0. 046]、背吃刀量0.2 mm、切削速度900 m/ min。按黄金分割法实验点的提取步骤,在[0.033,0.046]的0.618 处取值,选取第1 实验点为:
P1 =0.033+0.618(0.046-0.033)= 0.041
第2 实验点为:
P2 =0.033+0.382(0.046-0.033)= 0.038
实验P1 的表面粗糙度值Ra0.391 μm,P2 的表面粗糙度值Ra0.387 μm,则P1 测得的是最优实验值。实验结束,进给量取值为0.041 mm/ r。
4. 结语
在稳定的高速车削环境下,切削速度与切削深度对表面粗糙度值影响较小,进给量是影响工件表面粗糙度值变化的主要因素。PCD 刀具车削5052 铝合金表面粗糙度达到Ra0. 4 技术要求的最佳工艺参数是: 进给量0.041 mm/ r、背吃刀量0.2 mm、切削速度900 m/ min。黄金分割法应用于铝合金车削表面质量的实验研究,拓宽了实验方法,有效地减少了实验次数,提高了实验精度。所获得的实验数据为这类材料高精度、高效率车削加工提供了可靠的理论依据。
投稿箱:
如果您有机床行业、企业相关新闻稿件发表,或进行资讯合作,欢迎联系本网编辑部, 邮箱:skjcsc@vip.sina.com
如果您有机床行业、企业相关新闻稿件发表,或进行资讯合作,欢迎联系本网编辑部, 邮箱:skjcsc@vip.sina.com
更多相关信息