基于ANSYS Workbench的立式车床回转工作台结构优化设计*
2016-9-12 来源:西安理工大学机械与精密仪器工程学院 作者:魏锋涛 宋俐 代媛
摘要:基于ANSYS Wor蚰帅ch平台,以某数控立式车床回转工作台为研究对象。利用拓扑优化和尺寸优化设计方法,对其进行了以减轻质量和提高结构刚度为目标的结构优化设计研究。分析结果表明:与原设计方案相比较,优化改进后的回转工作台质量减少了24.97%,最大变形量减小了39.8%。而且一阶固有频率也由3".9 Hz提高到474.9 Hz。
关键词:回转工作台;ANSYS Workbench;拓扑优化;尺寸优化
目前,在国内外机床结构设计中,依然在广泛采用传统设计方法如经验、类比及简单的有限元分析等方法,这些方法通过与同类结构进行定性的分析和比较,然后取较大的安全系数来保证结构的可靠性。虽然设计过程中也采取了一般的计算与试验,但结构尺寸和重量还是会增大,材料的潜能不能很好发挥,这也使机床总体结构较为笨重,不仅使性能难以提高,同时也增加了制造成本[1-2]。
回转工作台是数控立式车床的重要组成部分之一,工作台带动工件旋转构成了数控立式车床的主运动,它用以装夹并支撑工件,且其静动态特性直接影响机床的加工精度及加工效率。在机床工作台设计中,人们总是希望在满足强度和刚度的条件下尽可能地减轻工作台的质量。因此,对工作台进行静、动态特性分析及结构优化就显得尤为重要。本文以某数控立式车床回转工作台为研究对象,以减轻质量和提高结构刚度为目的,结合拓扑优化以及尺寸优化设计方法,利用ANSYs Workbench平台对其进行结构优化设计。
1、回转工作台结构特性分析
1.1回转工作台结构
数控立式车床回转工作台的主要功能是实现工件的装夹和支撑,并通过绕主轴的旋转构成机床的主运动。常规回转工作台结构如图1所示。回转工作台底部是导轨支撑面;考虑到工件的安装及固定,工作台表面设计成若干个T形槽,以方便安装工装夹具, 并设计中心孔,与主轴连接配合,以实现回转运动;为了增加工作台的支承刚度,在它的内部设计筋板结构。根据数控立式车床整机设计要求,回转工作台部件主要技术参数如表1所示。

图l常规回转工作台结构
表1立式车床回转工作台主要技术参数
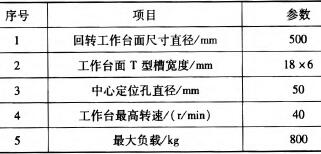
1.2 回转工作台有限元分析
1.2.1 回转工作台静力学分析[3-5]。
(1)创建有限元模型
根据设计要求,选择回转工作台的材料为H他00,添加材料信息时,取弹性模量为1.1×105 MPa,泊松比为0.25,密度为7 200 kg/m3。建立回转工作台三维模型并进行网格划分.其网格划分效果图如图2所示。
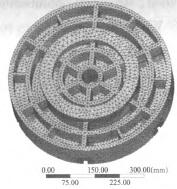
图2回转工作台网格划分效果图
(2)添加约束和载荷并求解
立式车床回转工作台主要实现工件的支撑以及带动工件旋转运动,因此其承受的主要载荷有回转工作台自重、工件重量、切削扭矩以及驱动扭矩。在主轴回转中心孔施加圆柱约束,由于回转工作台工作中可以做旋转运动,故圆柱约束的切向方向自由度不限制。在静压导轨面施加无摩擦约束,用以限制回转工作台的轴向移动,模拟静压导轨对回转工作台的支撑。将上述有限元模型提交运算求解,其静力学分析结果如图3所示。
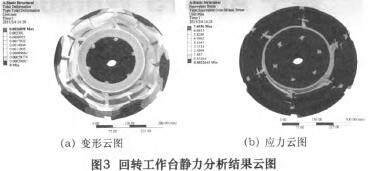
1.2.2回转工作台模态分析
在ANSYS workbench中直接利用静力学分析中的有限元网格模型,对原型回转工作台进行模态分析。提取原型回转工作台的前六阶模态,其模态振型如图4所示,并提取回转工作台前六阶频率如表2所示。
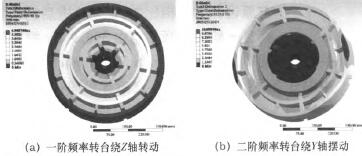
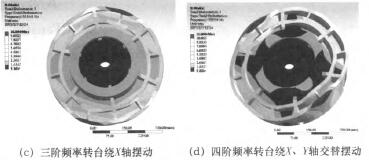
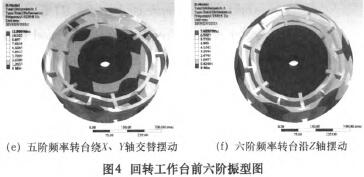
表2 回转工作台前六阶频率

通过以上静力学及模态分析,获得了原型回转工作台的最大变形、振型以及各阶频率值,可以确定该回转工作台的静力学和模态分析结果均满足设计要求,说明其本身设计是合理的。但由图3可看出,变形和应力云图中转台的小变形区和小应力区过多,变形和应力较大的区域少,且最大应力值远小于原材料的屈服强度。又由图4可看出,回转工作台固有频率和引起机床共振的频率相差很多,可知该回转工作台原结构设计过于保守造成材料浪费,其结构有待进一步改进,故可利用拓扑优化和尺寸优化设计方法,对其进行以提高结构刚度、减轻质量为目标的结构优化设计。
2、回转工作台拓扑优化设计
拓扑优化的思想是将寻求结构的最优拓扑问题转化为在给定的设计区域内寻求材料的最优分布问题,即可以通过优化材料分布,体现结构的载荷传递路径。因此,结合常规型回转工作台结构,通过拓扑优化依据力学准则提取体现回转工作台载荷传递路径的“支撑骨架”结构,在不改变工作台外形结构及尺寸的前提下,对其内部的加强筋板进行拓扑优化,确定其数量及最佳位置,达到优化回转工作台的结构形式,达到提高转台支撑刚度并减轻其质量的目的[6-9]。
2.1拓扑优化模型前处理
(1)三维模型的建立
建立回转工作台进行拓扑优化设计所需的三维模型,首先需要根据设计要求,得出设计最大包络空间,其次设定设计区域与非设计区域,最后对三维模型进行网格划分。由于回转工作台为旋转体,故选取一个扇形区域进行优化设计,这样不但可以正常得到概念模型,还可以大大节省时间。回转工作台初始设计区域模型如图5所示。设定好设计区域和非设计区域后。在ANSYs中对回转工作台进行网格划分。
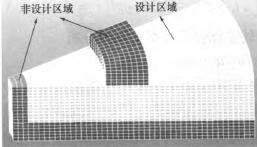
图5回转工作台初始设计区域模型图
(2)回转工作台载荷与边界条件的确定
拓扑优化中载荷的传递路径取决于载荷、约束的类型以及材料去除体积百分比,与载荷的大小并无直接关系。为更好地得到“支撑骨架”结构,需对载荷进行简化。在拓扑优化时对回转工作台台面施加轴向载荷,这也是回转工作台所承受最主要的载荷,并对整个体添加重力加速的载荷。同时,在静压导轨面限制z轴移动,主轴部分限制除绕z轴回转的其他五个自由度。
2.2 回转工作台拓扑优化及结果分析
基于ANsYS Workbench平台,采用密度拓扑优化方法,以应变能最小为目标,以体积分数、位移为响应建立结构拓扑优化模型,运用该模型完成回转工作台的拓扑优化设计。故将上面完成的前处理模型在To一pological Opt中进行运算,提交计算后显示可去除材料分布云图,如图6所示。
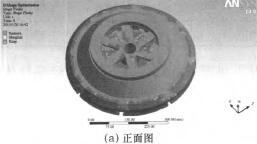
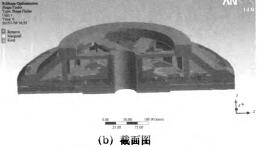
图6可去除材料应力分布云图
结合常规回转工作台结构及拓扑优化结果,对回转工作台结构形态进行修改,最终改进后的拓扑优化型回转工作台结构如图7所示。
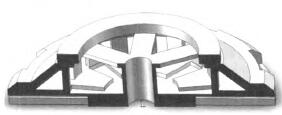
图7拓扑优化型回转工作台结构
为了验证拓扑优化的效果,对拓扑优化型回转工作台进行静力分析和模态分析,其静力学分析变形云图如图8所示,并从质量、变形和前六阶频率值三方面对原型、拓扑优化型回转工作台进行对比,其结果对比如表3和表4所示。
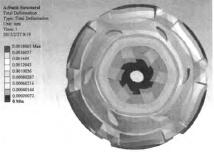
图8拓扑优化型回转工作台变形云图
表3拓扑优化型回转工作台性能分析对比表
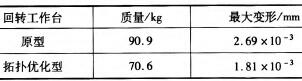
表4拓扑优化型回转工作台前六阶频率对比表

由表3和表4可知,回转工作台经拓扑优化后,与原型回转工作台相比,其质量减少了22.33%,最大变形量也减小了32.71%,基频也提高了16.3%。因此,经过拓扑优化确定了回转工作台合理的结构形态分布,并达到了提高结构支撑刚度、减小结构质量的目的。
3、回转工作台尺寸优化设计
通过拓扑优化设计的回转工作台还属于较为概念化模型,需通过尺寸优化确定合理的实际结构尺寸。本节在ANsYS workbench目标驱动优化模块中进行基于多目标遗传算法的回转工作台尺寸优化设计㈨01。
3.1 回转工作台尺寸优化设计数学模型
(1)选择设计变量
在拓扑优化型回转工作台的基础上,不改变其结构形态,建立参数化模型,进行尺寸优化设计。由于回转工作台的质量主要分布在下半部分桁架结构的支撑肋板上,并且回转工作台的支撑刚度也主要由这些支撑肋板决定,同时为了简化参数化建模过程,故选取支撑架结构中支撑肋板的7个参数做为尺寸优化参数,即设计变量,其中参数的选取如图9所示。
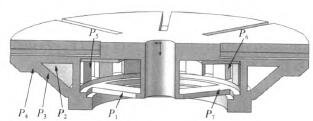
图9回转工作台参数分布图
因此,尺寸优化设计变量选择为:
x=[xl,x2,x3,x4,x5,x6,x7】T=【Pl,P2,P3,P4,P5,P6,P7】T式中:P1、P7分别为内圈肋板的厚度和宽度;P,、P6分别为中间肋板的厚度和宽度;P3、P4分别为外圈肋板底板的厚度和宽度;P2为外圈肋板与工作台面的夹角。P1、P3、P7的单位为mm,P2的单位为(。)。
(2)确定约束条件
根据回转工作台设计要求,给出相应的约束条件:

式中:Li和ui分别是设计变量xi的下限和上限,下限L设定为[8,38,10,14,lo,20,30]T,上限u设定为[10,50,20,18,14,35,50]T。其中设计变量的初始尺寸值:Xo=【8,40,15,16,12,30,40】T。
(3)建立目标函数
回转工作台尺寸优化设计的目的是进一步减小回转工作台质量,同时使其最大变形极小化,故两个目标函数分别定义为:

式中:M(Xi)表示回转工作台的质量;Defmax(Xi)表示回转工作台的最大变形量。
(4)数学模型
综上所述,回转工作台尺寸优化设计的数学模型为:
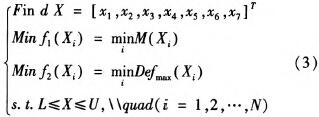
3.2 回转工作台尺寸优化结果分析
(1)Pareto前沿
提交多目标遗传算法尺寸优化设置并计算,可得到一组Pareto最优解集。同时得到转台质量Mass和最大变形量T0tal一Def的权衡(Tradeoff)图,如图10所示。由图10可看出,获得的Pareto前沿已经非常清晰。每一个离散点都代表其中的一个设计点对应的两个目标函数值,由于目标函数都是取最小值,因此,Pa.reto前沿都集中靠近在两个坐标轴的附近。
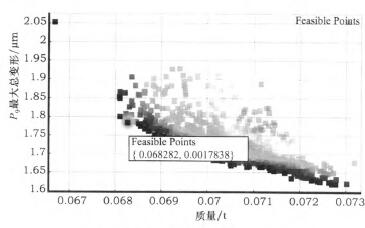
图10质量和最大变形量的Pareto Front
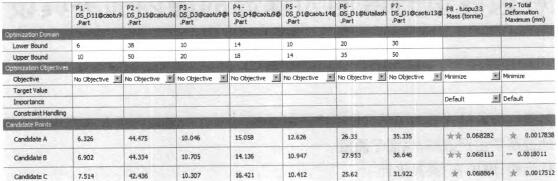
图11优化候选解
2)回转工作台尺寸优化结果
尺寸优化分析计算之后,在Pareto最优前沿中选取3个候选设计点(candidate points),如图11所示。结合尺寸优化计算结果,从回转工作台的结构、最大变形量及质量3个方面考虑,在保证回转工作台达到使用要求的前提下,确定候选设计点A为最优方案计点,并将参数圆整,整理后的回转工作台尺寸优化前后的参数见表5。
表5回转工作台尺寸优化前后参数对比表
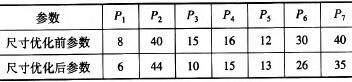
(3)尺寸优化型与原型及拓扑型回转工作台特性对比分析
为了验证尺寸优化效果,根据表5中优化后的尺寸参数修改回转工作台三维模型,对其进行静力学和模态分析,其静力学分析变形云图如图12所示,并从质量、变形和前六阶频率值三方面对原型、拓扑优化型及尺寸优化型回转工作台进行对比,其对比结果如表6和表7所示。
表6尺寸优化型回转工作台性能分析对比表
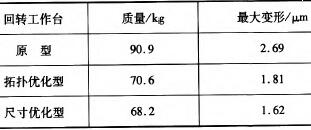
表7尺寸优化型回转工作台的前六阶固有频率对比表
单位:Hz

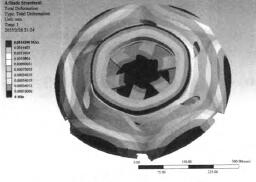
图12尺寸优化型回转工作台变形云图
由表6和表7可知,回转工作台经过尺寸优化后,与原型回转工作台相比,其质量减少了24.97%,最大变形量也减小了39.8%,一阶固有频率也提高了18.75%;与拓扑型回转工作台相比,其质量减少了3.4%,最大变形量也减小了10.49%,一阶固有频率也提高了2.1%;因此,通过回转工作台尺寸优化设计,在减轻结构质量的同时,也达到了提高回转工作台支撑刚度的目的。
4、结语
本文在数控立式车床回转工作台部件常规设计的基础上,以减轻结构质量、提高结构刚度为目标,进行了拓扑优化和尺寸优化设计以及静动态特性分析,确定了回转工作台合理的结构形态布局以及关键尺寸。由优化结果分析可知,通过对回转工作台优化改进,原工作台质量由90.9 kg减小到68.2 kg,减轻了22.7kg;最大变形量由2.69×10~mm减小到1.62斗m;一阶固有频率也由399.9 Hz提高到474.9 Hz;达到了减小结构质量、提高结构支撑刚度的综合优化效果,也为其他机床工作台结构设计提供了有益参考。
投稿箱:
如果您有机床行业、企业相关新闻稿件发表,或进行资讯合作,欢迎联系本网编辑部, 邮箱:skjcsc@vip.sina.com
如果您有机床行业、企业相关新闻稿件发表,或进行资讯合作,欢迎联系本网编辑部, 邮箱:skjcsc@vip.sina.com
更多相关信息