基于开放式数控系统的CKJ6136A车床改造
2017-1-3 来源:广州番禺职业技术学院机电学院 作者:窦凯 朱洪雷 钟飞龙 廖传辉曹甜学侯文峰
摘要:在分析数控车床改造要求的基础上,描述了伺服电机的选择、参考点的设定与调整、进给传动链误差补偿的方法以及变频调速器、数控系统参数的设置,改造后车床的加工精度满足生产要求。
关键词:车床;开放式数控系统;数控装置参数
1. CKJ6136A简介及改造要求
CKJ6136A数控车床是一台简易型数控车床,配置某公司早期的GSK928数控系统,X 轴、Z 轴采用步进电机驱动,主传动采用异步电机、齿轮变速。由于机床原数控系统频出故障且为已淘汰产品,无法维修,但该机床导轨、丝杠、主轴等精度保持较好,因此具有改造价值。为适应加工时能选择更加合理的切削用量,从而获得最佳的生产率、加工精度和表面质量的加工要求,主传动要能实现无级变速且具有较宽的调速范围。为保证加工精度和增加伺服驱动能力,X 轴、Z 轴采用交流伺服电机驱动,数控系统选用HNC-21TD开放式数控系统。
2.电机的选择与安装
2.1 主轴电机
主电机的选择采取类比法,经过与同类型数控车床的床身上最大回转直径、主轴转速范围、主电机功率等技术参数比较,结合主传动系统的基本要求,选择GM710三相交流伺服变频电机为主轴电机。GM710电机功率为5.5 kW,额定转速为2500 r/min。该电机结构紧凑,体积小,重量轻,功率密度高;电磁振动小,旋转精度高,恒转矩及恒功率调速范围宽;转子惯性小,响应速度快;气隙均匀,平衡精度高,转矩脉动小;性价比高.
2.2 进给伺服电机
X 轴与Z 轴进给电机的选择采用类比和校核计算相结合的方法,即经过与同类型数控车床的X 轴、Z 轴快速进给速度、最小输入单位、重复定位精度、快速空载转矩、切削力矩、快速进给力矩、转动惯量等技术参数比较,初步确定交流伺服电机型号,而后进行转矩校核计算和转动惯量匹配性校核计算,满足要求即可。
下述为X 轴电机选择流程,用类比法参照同类型数控车床初步选用GK6061交流伺服电机作为X 轴驱动电机(同理,Z 轴选用GK6062交流永磁伺服电机)。
2.2.1 切削力及丝杠的进给牵引力计算
依据主传动功率计算法,主切削力为[2]:
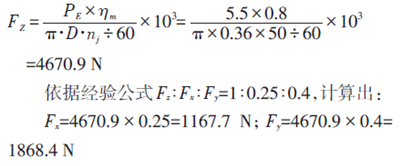
车刀受到的车削抗力由拖板传递到导轨上,与进给丝杠的牵引力相平衡。对于综合型导轨,丝杠的进给牵引力为:
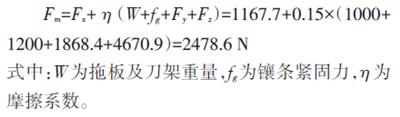
2.2.2 转动惯量匹配校核
拖板及丝杠等折算到电机轴的等效转动惯量为:
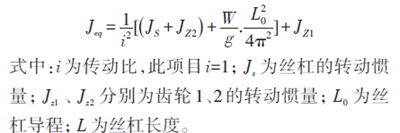
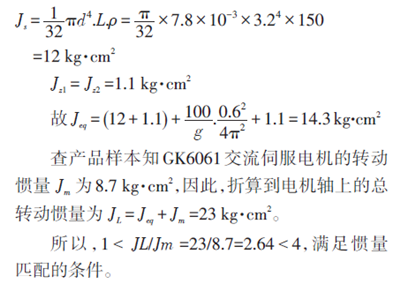
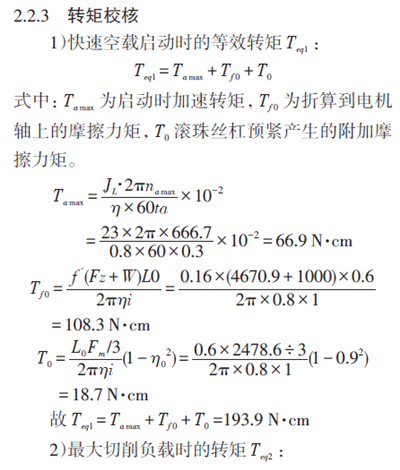
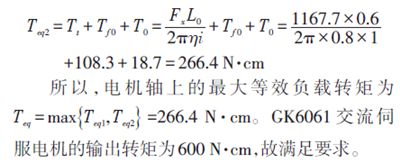
2.2.4 电机的安装
更换主轴电机与进给伺服电机后,新电机与机床原有电机的安装尺寸不同,因此均采用过渡连接板的方式来实现电机的固定。
2.3 主轴脉冲发生器的安装
脉冲发生器安装在床头箱的后端,并通过一对传动比为1∶1的齿轮与主轴相联,工作时,脉冲发生器与主轴同步旋转,数控装置控制进给伺服电机准确地配合主轴的旋转而产生进给运动。从而保证主轴每转1转,螺纹车刀移动1个导程,同时还保证每次走刀都在工件的同一点切入,使螺纹不乱扣。
3. 控制系统的参数设置
3.1 主轴变频装置
选用日立SJ300 变频器,多数参数保留默认值,部分参数根据需求进行设置。主要参数设置如表1所示。
表1 变频器参数设置表
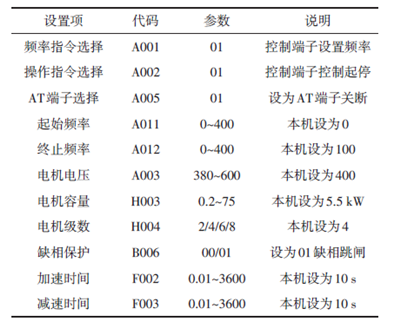
3.2 数控装置
HNC-21TD数控装置通电后经自检进入主控界面,为保证改造后的数控机床能正常运行,必须进行参数优化。进入系统参数设置菜单,对照硬件检查系统参数是否正确,同时按表2所示数据核查设置参数[1]。
表2 HNC-21TD参数设置表
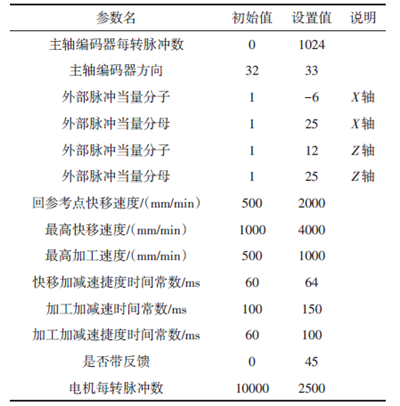
3.3 PLC参数
在PLC 程序中机床输入的开关量信号定义为X,即各接口中的I 信号;输出到机床的开关量信号定义为Y,即各接口中的O 信号。将各个接口HNC-21 本地远程I/O 端子板中的I/O(输入/输出)开关量分别定义为系统程序中的X 、Y 变量,需要通过设置硬件配置参数和PMC 系统参数来实现,主要参数如表3所示。
表3 PLC参数设置表
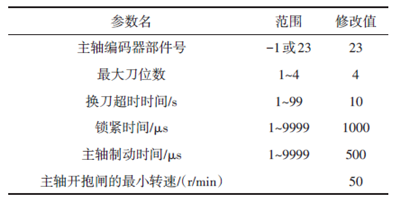
4. 机电联调
4.1 参考点的设定与调整
随滑板一起运动的减速挡块释放参考点开关触头使其由通转为断,机床滑板减速并以设定的速度继续移动,减速可使参考点停留位置准确。采用脉冲编码器上的格栅信号来确定参考点,当减速挡块释放参考点开关触头使其触点状态由断再转为通后,数控系统将等待码盘上的第1个格栅信号,该信号一出现,滑板立刻停止运动,此时的位置是电气原点。数控装置会记忆该点,调整时一般难于做到电气原点与机床参考点位置完全一致,会存有一定误差,实际调整中是通过测量这一误差值,采取对参考点补偿的方法进行校正。
即滑板到达电气原点后会再移动一个补偿量,从而准确到达机械参考点。数控系统启动后进入主界面,按主菜单F1(参数索引)键→选择F3(坐标轴参数)→选择轴2(Z 轴)→选择“参考点开关偏差”,输入参考点补偿量即可。
4.2 进给传动误差补偿
机床长期使用后,进给传动链运动部件会磨损并存在一定间隙,为恢复其加工精度,需进行间隙补偿,即对数控装置内的补偿参数(Z 向参数地址、X 向参数地址)进行重新设定。补偿量的具体测量方法是:使刀架从停留位置向-Z 方向快速移动50 mm,将百分表触头对准滑板的+Z侧,适当压紧触头并调整表针对零;让刀架从当前停留位置再向-Z方向快速移动50 mm,刀架停稳后使其从停留位置向+Z 方向快速移动50 mm,读出此时百分表的数值并记录下来,重复进行5~10次,取算术平均值作为间隙补偿量。X方向间隙补偿量的测定参照进行。
5. 结束语
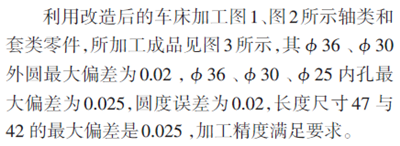
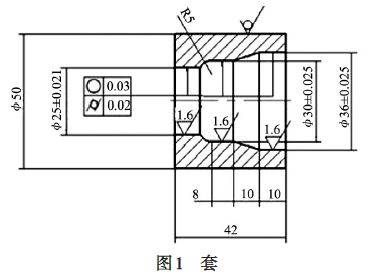
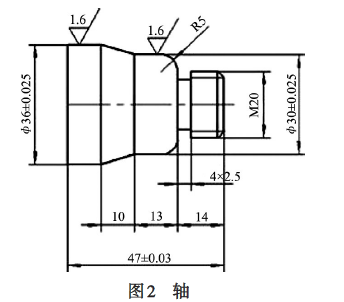
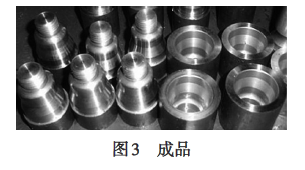
投稿箱:
如果您有机床行业、企业相关新闻稿件发表,或进行资讯合作,欢迎联系本网编辑部, 邮箱:skjcsc@vip.sina.com
如果您有机床行业、企业相关新闻稿件发表,或进行资讯合作,欢迎联系本网编辑部, 邮箱:skjcsc@vip.sina.com
更多相关信息