基于A N SYS 的螺纹数控修复车床主轴系统优化设计
2017-2-8 来源:沈阳工业大学机械工程学院 作者:王 可,肖 磊, 孙兴伟
摘要: 主轴动态特性直接影响机床的加工精度和精度稳定性。借助有限元分析软件ANSYS , 对SCK230 螺纹数控修复车床的主轴进行动力学分析,并进一步对主轴的动态特性进行优化计算,最后通过动力学分析获得在合理范围内主轴的最优跨距,为机床主轴的设计改进提供了重要依据。
关键词: 主轴; 优化设计; ANSYS
0.引言
随着科学技术的进步,机床主轴的性能也进一步向高转速、高精度、高刚度方向发展。SCK230 型螺纹数控修复车床是为石油和地质行业管具公司的钻杆、钻铤螺纹修复车削工作而专门设计生产的现代化自动车床,主轴单元是机床的重要部件之一,其动静态特性直接影响工件的加工精度、表面粗糙度和生产效率,对主轴进行动力学分析可以提高整个机床的设计效率,缩短开发周期,降低开发成本,提高机床工作安全和可靠性[1] 。
1.建立分析模型
SCK230 螺纹数控修复车床主轴为简单的阶梯轴,采用双支撑结构,为提高计算效率,在建模时省略主轴上的键槽、倒角和螺纹等细小结构。在ANSYS 中采用从上至下的建模方式建模,首先建立主轴的轴向截面并用Plane42 单元进行手动网格划分,然后用Solid95 单元绕X 轴旋转该截面生成三维实体,得到更加精确的六面体网格划分实体[2 ] ,主轴材料选用45钢。分网后对其进行加载约束,经分析,轴承的弹性和阻尼会对主轴的动态特性产生影响[3 ] ,可将轴承视为在圆周方向等效分布的4 个弹簧,用弹簧阻尼单元Combin14 模拟轴承的支撑[4 ] ,轴承分布如图1 所示。为了限制主轴轴向的移动,在节点T1 、T2 、T3 和T4施加轴向约束,限制其轴向自由度,弹簧的另一端(T5 、T6 、T7 、T8)为固定约束,约束其全部自由度。该车床采用前、后轴承[5 ] ,通过计算前、后轴承的刚度分别为122 .6 × 107 N/m 和577 .5 × 106 N/m ,图2 为带有弹簧约束的主轴有限元模型。
2.模态分析
2 .1 模态分析的基本理论
模态分析实质是一种坐标变换,其原理就是把物理系统中描述的响应向量放到所谓的“模态坐标系统”中来描述,该坐标系统中的每个基向量就是振动系统的一个特征向量。运用力学分析的有限元法,可得该主轴系统的动力学方程如下:
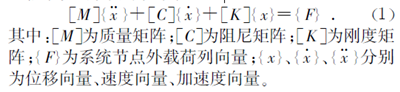
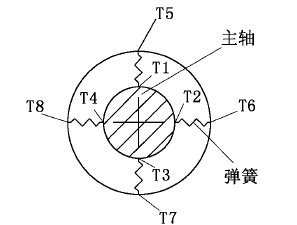
图1 轴承的分布
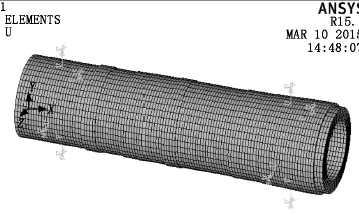
图2 加轴承约束后的主轴有限元模型
机械结构的固有频率和振型是其固有特性,只与刚度和质量相关,故对机械结构进行模态分析时,可忽略阻尼和力对结构的影响,则得到该主轴系统力学模型的自由振动方程为:

求解特征方程的特征值和特征向量,即为所研究机械结构的固有频率和振型。
2 .2 主轴的模态分析
主轴的振动可以表达为各阶固有振型的线性组合,理论上有无数阶固有频率,但加工过程中低阶固有频率对轴的振动影响要比高阶固有频率大,越是低阶影响就越大[6 - 7 ] ,因此低阶频率对轴的动态特性起决定作用。表1 是应用有限元分析软件ANSYS 计算出的主轴的前6 阶固有频率及振型,其中主轴的1 阶、3阶、5 阶和6 阶振型如图3 ~ 图6 所示。
表1 主轴的前6 阶固有频率及最大变形量

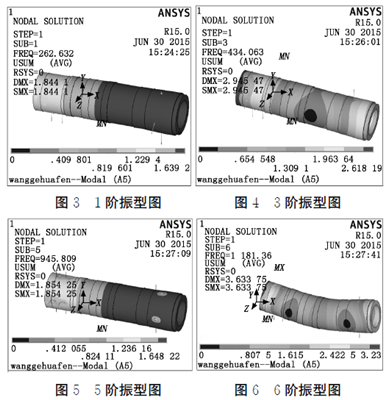
临界转速是指主轴旋转时使主轴出现挠度急剧增大、转动失稳现象的旋转速度。主轴的工作转速应当远离其临界转速,否则主轴将有可能处在共振区域而产生剧烈振动。通过比较临界转速与主轴工作转速,可以判断主轴系统是否发生共振[8] ,转速和频率的关系为:

表2 主轴前6 阶固有频率的临界转速

从表1 中可以得出,主轴的1 阶、2 阶固有频率相近,3 阶、4 阶固有频率相近,并且其振型表现为正交,因此可将其视为复根。主轴的第1 阶模态表现为主轴的垂直方向上的一阶弯曲振动,第2 阶模态表现为主轴横向水平方向(Z 向)的一阶弯曲振动,且最大弯曲变形发生在主轴的中部。第3 阶模态表现为主轴垂直方向的二阶摆动弯曲振动,第4 阶模态表现为主轴横向水平方向(Z 向)的二阶摆动弯曲振动,且最大弯曲变形发生在主轴后端。根据该车床的实际工况可知,本主轴的工作转速约为250 r/min ,小于其1 阶临界转速,故不会产生振动,保证了主轴的加工精度。主轴系统的动态分析有很多影响因素,单一条件的约束不足证明系统达到最佳工作状态[9 ] ,因此应该对主轴系统进行进一步设计改造。
3.主轴优化设计
3 .1 优化设计的理论方法
主轴系统优化设计的目的在于增强系统的动态特性,在优化设计前,需依据原结构的有限元分析结果及机床工作需求明确优化目标、优化变量、约束条件[10 ] ,轴承支撑刚度、跨距、主轴的径向尺寸等对主轴系统动态特性都有直接影响,可将其作为变量因素,约束条件为变量的设计区间。本文对主轴的跨距进行讨论分析,根据该主轴的工作情况,可采用如下公式计算最佳跨距:

3 .2 优化设计的有限元分析
由计算得到了主轴的合理跨距范围,该主轴系统的跨距为840 mm ,可以知道其跨距处于合理范围之内。为进一步分析该主轴系统的最佳跨距,利用ANSYS软件进行不同跨距下的主轴有限元模态分析,考察其固有频率如何变化。该车床主轴的跨距为840 mm ,据此设置跨距改变量为- 40 mm 、- 20 mm 、+ 20 mm 和+ 40 mm ,取各自1 阶固有频率进行分析,分析结果见表3 。
表3 不同跨距下的主轴1 阶固有频率

根据表3 可以看出,跨距在800 mm 时主轴的1阶固有频率最大,跨距在880 mm 时1 阶固有频率最小,主轴的1 阶固有频率在800 mm ~ 880 mm 范围内随着跨距的增加逐渐减小。根据主轴在主轴箱体的整体布局的实际情况,综合考虑主轴的跨距为820 mm 更佳。
4.结论
通过对SCK230 螺纹数控修复车床的主轴进行实体建模和有限元仿真计算,得到了主轴前6 阶固有频率、形变程度及各阶的临界转速,在此基础上利用优化设计的理论计算该主轴的合理跨距,并利用有限元分析软件分析主轴在不同跨距下其固有频率的变化,得出了以下结论:
(1) 对主轴系统进行有限元分析,得出了该主轴在现有的轴承支撑刚度条件下的前6 阶固有频率和各阶临界转速,发现1 阶临界转速大于其工作转速(250r/min) ,说明该主轴能够避开共振区域。
(2) 通过对主轴最佳跨距的计算及分析,得到了主轴在实际条件下的最佳跨距,减小了主轴的跨距,缩小了主轴箱体的空间距离,减轻了系统重量,为主轴箱体的整体设计改进提供了依据,有利于主轴系统的整体优化。
投稿箱:
如果您有机床行业、企业相关新闻稿件发表,或进行资讯合作,欢迎联系本网编辑部, 邮箱:skjcsc@vip.sina.com
如果您有机床行业、企业相关新闻稿件发表,或进行资讯合作,欢迎联系本网编辑部, 邮箱:skjcsc@vip.sina.com