双主轴车削加工中心高效应用及研究
2017-2-13 来源:陕西国防工业职业技术学院数控工程学院 作者:曹旭妍 李斌
摘 要:双主轴车削加工中心结构复杂、运动形式多样,能够一次装夹下完成零件的所有加工工序,但由于机床结构较复杂,在试件加工时往往会发生碰撞、干涉等危险情况,给机床使用带来风险,同时影响机床的高效应用。基于虚拟仿真技术,以EMCO maxxturn65 双主轴车削中心为研究对象,在VERICUT 中构建机床虚拟仿真加工系统,并进行仿真加工。通过仿真加工,检验NC 程序的正确性,检测加工中可能出现的干涉、碰撞等情况,预知加工结果;根据仿真加工,对错误的NC 进行纠正,保证机床使用中的安全性,进而提高该类机床的应用效率。
关键词:双主轴车削加工中心;虚拟仿真;VERICUT
0.引言
随着机械制造技术的不断发展,零件结构形式越来越复杂,对加工精度的要求也越来越高。加工过程中的多次换装不仅使得零件的加工质量无法得到保障,同时还因多次的工件安装、对刀等过程大大降低了加工效率。双主轴车削加工中心能够使得需要多个加工工序的工件一次装夹下完成所有加工,不仅减少了因多次装夹而导致的加工误差,还提高了加工效率,能很好地满足现代企业生产要求,尤其在航空、航天等领域,双主轴车削加工中心的高效应用具有举足轻重的作用。然而,由于该类机床的结构及运动形式复杂多样,在实际应用中存在数控程序编写及正确性检测困难的问题,这些问题制约着车削中心的高效应用,给企业快速生产带来困难[1] 。利用虚拟仿真技术,以实际机床为原型,在虚拟仿真平台中构建机床的仿真加工系统,使其具有与实际机床完全一致的加工功能,对工件进行虚拟仿真加工。该方式能够在不消耗生产资源的条件下,快速完成工件的虚拟加工,检验数控程序的正确性,同时能够对加工过程中存在的质量问题进行预判,为实际加工过程中机床的安全性及高效性提供可靠保障。
1.虚拟仿真系统构建过程
虚拟仿真系统是将实际机床在计算机中的完全映射,具有与实际机床一致的加工功能。该系统在使用过程中不消耗实际的生产资源,加工过程快,且能够不断反复的进行加工,能很好的解决复杂零件试切过程耗时、耗力等问题,对企业新产品研发生产非常重要。根据机床的结构及尺寸,在VERICUT 中建立虚拟机床模型。其主要过程如图1 所示。
2.构建虚拟仿真系统
2. 1 机床结构分析
EMCO maxxturn65 双主轴车削中心配备一个带有X、Y、Z1 运动轴的刀塔,主轴带有C1 旋转轴功能,副主轴带有Z2、C2 两个运动轴。如图2 所示,床身的工作面为高刚度45°易排屑倾斜结构,其上装有主轴、副主轴和沿床身滑动的床鞍,其中主轴固定于床身,沿床身滑动的副主轴与主轴轴向对置,伺服动力刀架固定于沿床鞍X 轴方向滑动的滑板上。
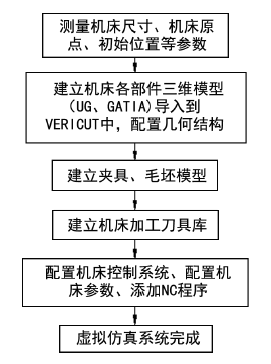
图1 虚拟仿真系统构建过程
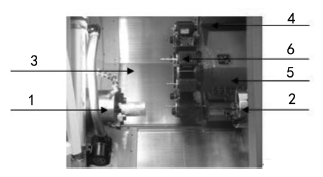
图2 双主轴车削中心结构
1. 主轴 2. 副主轴 3. 床身 4. 床鞍5. 滑板 6. 刀架
2. 2 机床参数测量
双主轴车削中心加工过程中工件换装时机床不停机,因此机床各部件的空间位置精度要求较高[2] 。建立机床的虚拟仿真加工系统时,准确获取机床各运动部件参数是研究的关键之一。EMCO maxxturn65双主轴车削中心的参数获取主要通过测量以及查询手册来实现,通过激光尺、卷尺、板尺等测量工具完成机床主要外形部件及空间尺寸的测量,关键零部件尺寸及机床极限位置等对建模精度有重要影响的尺寸参数通过查询机床手册或者运行机床后在机床控制面板中读取。要完整的建立机床模型,所需要的机床参数主要有:主轴、副主轴、刀塔、刀具等重要部件尺寸;机床初始位置、极限位置;运动轴及部件间的空间位置;外形轮廓等。
2. 3 机床建模
建立机床的虚拟模型,不仅需要完成各运动部件的三维几何模型,还要赋予其与实际机床相一致的运动关系。VERICUT 软件中提供了许多运动轴组件,根据实际机床的运动结构,建立其运动树,将各运动部件的三维模型加载到相应的运动组件下即可完成机床模型的建立[3] 。要正确建立机床的运动树,首先要明确机床的运动连。EMCO maxxturn65 双主轴车削中心包含两条运动链:基座-工件;基座-刀具。根据确定好的运动链,在VERICUT 中依次添加相应的运动组件,完成机床运动组件树的创建,如图3 所示。创建组件树仅是完成了机床各运动部件间运动关系的建立,还需添加相应的几何模型。由于机床机构较复杂,各运动部件几何模型在VERICUT 中创建较困难,因此,在三维模型在UG 中建立各部件几何模型,然后将模型保存为STL 格式文件导入到相应的运动组件下即可。
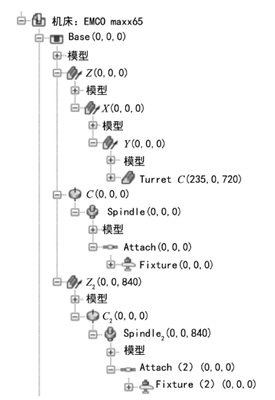
图3 机床运动树
2. 4 建立刀具库
VERICUT 中提供了丰富的刀具设计样本,根据刀具的具体特征及参数,选择所需结构及尺寸即可生成刀柄、刀片。刀具生成后,为保证加工的顺利进行,还需根据实际使用中将要用到的刀具特点及参数,设置刀具的驱动点(对刀点)、安装点等参数,如图4。
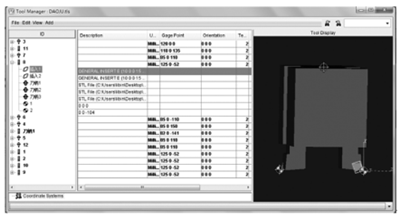
图4 双刃刀具建立
2. 5 控制系统配置
为了满足用户需求,VERICUT 系统库中提供了多种不同类型的控制系统,根据实际机床,选择SIEMEND840D系统。VERICUT 系统库中所提供的为通用控制系统,而为满足双主轴车削中心的加工功能,生产厂家对其定制了一些特殊的加工代码,因此需要对所选控制系统进行二次开发,以保证虚拟加工系统与实际机床具有相同的加工功能。
2. 6 机床参数设置
构建完机床的几何模型及相关部件后还需对机床参数进行设置。机床参数设置的主要目的就是告知机床当加工中出现错误、碰撞等问题时能够及时的进行报警,便于技术人员查找问题所在,并进行修正。虚拟系统中机床参数主要包括了:机床行程设置、机床各运动轴的初始位置设置、刀具换刀点的设置、碰撞检测距离设置等,正确设置机床参数,对保证仿真加工过程与实际加工的一致性至关重要。
3.仿真加工
3. 1 NC 程序生成
双主轴车削中心加工功能强大,工件结构通常比较复杂,采用手工编程的方式很难实现复杂工件的NC 编写。在UG 等三维软件中建立零件的几何模型,并利用UG 中先进的数控加工功能对工件进行艺处理,生成正确的刀位轨迹文件,但该文件不能直接被数控机床所识别,因此需对其进行后置处理。UG 中自带的后置处理模块能够对三轴及以下刀位轨迹文件进行后置处理,生成机床能够直接识别的NC 程序,而对于三轴以上的复杂文件则无能为力[4] 。针对双主轴车削中心的结构特点,利用UG 后置处理模块开发专门的后置处理器MAXX-POST,该后置处理器能够专门对适合双主轴车削中心的工件前置刀位轨迹文件进行处理,生产机床能直接识别的NC 程序,满足加工需要。
3. 2 虚拟仿真加工及验证
将UG 中生成的NC 程序添加到虚拟仿真系统中,添加毛坯、工件的模型到系统中,进行G 代码偏置设置(即加工对刀)后,进行仿真加工,如图5所示。仿真加工中不仅要观察刀具及工件的状态是否合理,还要根据警告内容分析存在的问题并进行处理,确保前置工艺过程、NC 程序的正确性。
4.实际验证
经过虚拟仿真加工,验证NC 程序的正确性后,对加工工件进行实例验证。将经过虚拟仿真验证过的NC 程序载入实际加工机床中,对工件进行实际加工。加工中刀具的走刀路径与仿真加工一致,没有干涉、碰撞等问题出现,其加工结果如图6 所示。
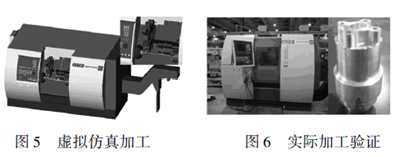
5.总 结
介绍了在VERICUT 中建立机床虚拟仿真加工系统的一般方法,并以EMCO maxxturn65 双主轴车削中心为对象,建立其虚拟仿真加工系统。以一回转体零件为加工样件,对其进行虚拟仿真加工,检验了NC程序的正确性,并对该样件进行实际加工。结果表明,该虚拟仿真加工系统能够准确验证NC 程序的正确性,并正确预知加工中可能出现的干涉、碰撞等危险情况,能有效保证机床使用中的安全性及高效性。
投稿箱:
如果您有机床行业、企业相关新闻稿件发表,或进行资讯合作,欢迎联系本网编辑部, 邮箱:skjcsc@vip.sina.com
如果您有机床行业、企业相关新闻稿件发表,或进行资讯合作,欢迎联系本网编辑部, 邮箱:skjcsc@vip.sina.com
更多相关信息