提高汽车模具零件加工精度与效率的方法
2017-11-27 来源: 四川宜宾普什模具有限公司 作者:尧军
摘要:通过对加工工艺流程和装配工艺流程的分析,找出影响汽车模具零件制作精度的因素,通过改善模具零件的装夹方式、加工顺序、加工条件和优化装配淬火流程,在保证单件加工尺寸精度的同时强调过程检验,以达到提高模具零件制作精度的目的。
关键词:等高垫铁;淬火流程;过程检验;模具零件
l 、引言
随着汽车工业的飞速发展,对于汽车模具零件的加工精度要求越来越高,周期要求越来越短。为满足模具零件加工的要求,越来越多的企业采用购买高精机床进行模具零件加工,但是从实际加工生产来看,加工的模具零件精度仍不能得到很好的保证,因此如何优化模具零件的加工工艺流程显得尤为重要。
2、合理的加工工艺
模具零件加工受机床、切削力、温度的影响,导致模具零件的加工质量及尺寸精度也受到影响,因此需要通过优化加工流程来提高零件的加工精度。
2.1零件装夹优化
模具零件装夹的一般流程为:采用垫铁安装模具零件,保证垫铁等高(同时平磨),将垫铁分布到零件的四周,如图1、图2所示,然后按操作流程进行模具零件的装夹。
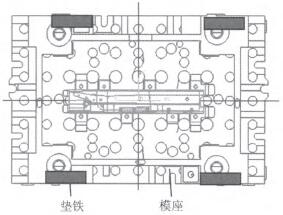
图1模具零件尺寸<2m
加工时通常只关注垫铁是否等高,而忽略当垫铁摆到机床工作台上时是否等高,由于机床工作台长期使用,有可能导致垫铁放到点后而高度不一致,导致模具零件装夹不平。每次零件装夹前应确认垫铁摆到机床工作台上后是否等高。
模具零件加工后由于切削应力和热变形,将会导致模具零件加工完后有变形,零件底面与垫铁接触面越多,越能反映加工后零件的平面真实情况。试验表明,4块垫铁和6块垫铁导致的模具零件精度差在O.05 mm左右,模具零件越大精度差越明显。
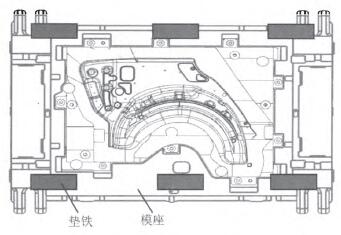
图2模具零件尺寸>2 m
对于薄板类模具零件(如落料模模座)加工前其自身就会产生变形,即使对零件进行多次加工仍可能无法保证底面平整,装好后始终会有一个角与接触面有间隙,对于这种情况,再用机床加工来解决变形只会增加制造成本。由于模具零件最终是在机床上进行作业,上机床后工作状态为直接将模具装夹到工作台上,只要保证模具的装夹状态与机床的装夹状态一致,就能保证其加工精度。为此对于此类模具零件无法加工平整的,加工时保证其平面度在0.3 mm以内,对于模具零件的装夹,条件允许的情况下直接放在工作台上更能保证其加工精度。
垫铁安装好后就需要对模具零件进行校平找正,为了能够快速校平找正,可利用模具零件底平面的十字键槽进行定位,制作定位键,定位键的上端与模具零件的键槽配合,下端与机床工作台上的键槽或者T型槽配合,如图3、图4所示。
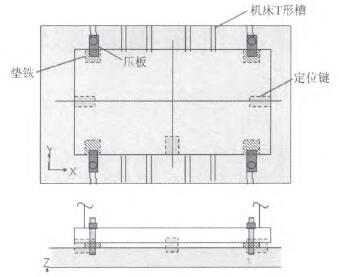
图3 模具零件定位安装样图
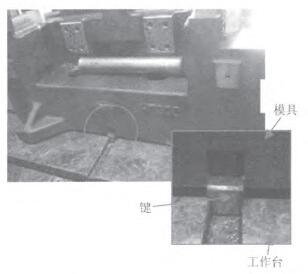
图4模具零件定位安装
相对传统的手工校平方式,用定位键自动校平可提高约50%的装夹效率。同时模具零件紧固从以往靠压板与零件及工作台之间的摩擦来限制模具零件的水平自由度,改为直接刚性限制其水平自由度,这样能获得更好的安装效果。
2.2制作工序的合理安排
对于零件加工,最重要的是基准(即瓜,,、z基准),基准的准确与否直接影响模具零件的最终加工精度。Z基准即模具零件的底面,考虑如何装夹来应对模具零件的变形,首先要考虑尽量减小或者消除零件自身的变形。一般模具零件底面的制作流程为:①底面粗加工;②底面压夹槽、键槽等粗精加工;③底面精加工,然后进行正面的一次加工,组装后的二次加工。这样的制作流程消除了模具零件底面由于大余量切削产生的加工变形,但是加工应力和热应力不能得到充分释放,也就是后期模具零件还会有变形,同样会使得后期进行二次加工时Z基准平面不平,经验证,其变形量约O.2 mrrd2 m。一般模具零件一次加工完成后进入钳工组装镶件,然后再进行加工需要2~3天,在这过程中模具零件也在进行自然时效,而模具零件的二次加工量很少,对模座加工产生的应力很小。因此只要在二次加工时先将底面重新精光加工一次,就能很好消除底面变形产生的影响,保证模具零件z基准精度。
Z基准重新精光后,原来的从】,基准也会有相应的变化。在一次加工时,基准孔做小一号(同样按H7制作),二次加工时将其精加工到位,这样能保证其精确。同时将精度要求高的导向面、导向孔也安排在二次加工时精加工,以保证导向精度。
2.3 加工机床的合理使用
零件加工时常会将粗加工机床和精加工机床分开,可以更好地保护机床。由于各种因素的影响,精/JnY-.机床的精度一般≤0.01 mm/1 m,重复精度一般≤0.006 mm/1 m,但是对于不同的机床,有些机床精度可能是0.01 mm/1 m,有些是一O.01 mm/1m,这样同样用于精加工的不同机床,其误差就在0.02 mm/1 m。模具零件的精度要求:型面+--0.05mm,导向孔±0.01 mm,导向面±0.05 mm,也就是不同机床不能满足导向孔的精度要求。因此对于模具零件的二次精加工,采用上、下模同一台机床加工更能保证其配合精度。
3、运用合理的装配流程
装配流程的优劣直接影响模具零件的制作质量和生产成本,因此在模具零件制作环节起着关键性的作用。模具零件的装配包括下模与凸模的组装、上模与镶件的组装、上模与压料器的组装、斜楔与模座的组装等,这里主要是淬火工序和组装基准对模具零件精度的影响。
3.1淬火工序的合理安排
随着模具零件制作技术的不断进步,淬火工序也在进行不断优化,以镶件淬火为例,以往的淬火流程如表1所示。
上述流程的优点:能够很好地保证镶件之间拼接,精加工时余量均匀。缺点:组装粗加工会增加加工难度,整体型面粗加工容易出现加工盲区,球刀粗加工时加工量大,对机床损伤严重,同时也增加了模具零件在机床的占机时间,加工周期长。优化后的淬火流程如表2所示。
优化后的加工流程优点:机床的加工时间得到有效降低(只有8 h),对加工效率提高具有很大的作用,节约了加工成本,后期钳工装配时间也大大缩短,进一步缩短模具零件生产周期。缺点:由于采用单件加工只有单件基准,也就是会出现基准误差,再加上钳工的研配,会出现组装后镶件之间型面轮廓结合不好的情况,严重时没有加工余量,增
加了返修次数。要解决这一问题,首先要保证镶件的一次加工质量,同时加工工艺充分考虑镶件淬火前的加工余量。
表1淬火流程
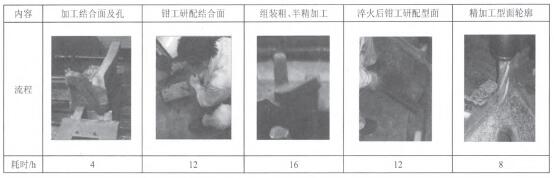

综上所述,采用优化后的淬火流程能够很好地在保证零件加工质量的前提下提高生产效率,这是目前广泛采用的加工方式。也并非所有的镶件都适合先淬火后加工,图5所示的镶件内圆角R1 mm,由于CNC加工很难达到R1 mm的加工(一般到R2mm),导致加工完成后内圆角尺加工不到位,只能留给钳工修配,如果先淬火,势必会增加钳工的修配难度,还会由于工具限制无法实现修配,此类镶件适宜钳工研配好后进行淬火。
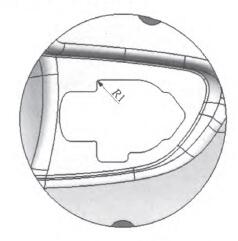
图5车门板锁口位置
3.2组装工序的合理选择
各零件组装加工有利于保证整体模具的制作精度,但影响模具的制作周期,如何保证零件加工精度需从工艺流程上对其进行优化。
一般在凸模基准侧的压料器和斜楔、整形压料器都需要组装加工,这样能更好地保证基准精度。而对于其他压料器和斜楔采用单件加工,能缩短加工周期。单件加工会产生基准累积误差,导致模具零件精度下降。压料器、斜楔与模座一般都是采用导板或导柱导向进行组合,以保证其组合精度。压料器、斜楔其导向一般都是在背面加工,而型面在
正面加工,因此就存在背面和正面的相对误差,而且导向尺寸公差的不一样,会产生直线误差,这样就使得加工完成后组装到模座里面型面不吻合。对于不组装的压料器、斜楔,在做正面加工时需以背面导向尺寸类来确定基准,首先保证导向类尺寸公差一致,然后将其转换到正面,保证相对基准。
4、进行有效的过程检验
检验可以第一时间发现制作过程中加工零件的质量问题,但是一般检验都是在模具零件加工完成下机后或者是钳工装配完成后进行,这样虽然发现了问题,但是没能在第一时间解决加工尺寸问题,会造成模具零件的返工返修。因此在模具零件制作过程中引入过程检验,在加工过程中,对零件关键尺寸进行实时检查确认,对没有加工到位或者装配不合理的及时予以修正,保证其加工下机前零件合格,如图6所示。

图6过程检验流程图
通过在加工制作的同时确认加工零件尺寸精度,避免了重复上机床翻修,可大大降低返修时间(装夹、转运、二次加工找正等工时消耗)。
5、结束语
影响模具零件加工精度的因素有很多,如操作技能等。随着自动化加工的不断深入,模具零件的制作采用机床全程序加工,同时将装配工序细分,保证每一部位零件的装配质量;并且重视模具零件存放时的摆放状态,减小模具零件变形对其精度的影响,更有利于模具精度的提高。
投稿箱:
如果您有机床行业、企业相关新闻稿件发表,或进行资讯合作,欢迎联系本网编辑部, 邮箱:skjcsc@vip.sina.com
如果您有机床行业、企业相关新闻稿件发表,或进行资讯合作,欢迎联系本网编辑部, 邮箱:skjcsc@vip.sina.com