用3D打印技术增强轨道交通车辆零件的可用性
2019-7-3 来源:埃马克 作者:
毋庸置疑,机车、轨道车辆和列车是否可用,对轨道交通的可靠性至关重要。德国联邦铁路公司(Deutsche Bahn,以下简称德铁))有 7,000 多名员工从事着车辆养护工作,为由数千车辆组成的车队保驾护航。其中,备件的库存和采购是一项巨大的挑战。对于那些难于采购的零件,采用 3D 打印的方式制造零件,则能够显著提升备件的可用性。目前,德铁在一个试点项目中首次使用了 GEFERTEC 的 3DMP® 工艺。
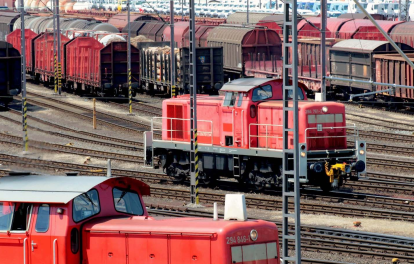
1966 至 1974 年, 294 系列机车在德国联邦铁路公司营运
“可用性对我们公司来说是一个非常重要的课题”, Tina Schlingmann 博士说道,她从去年开始为德铁研究增材制造的潜在应用。这位材料学专家认为,除原型制造和工具领域,备件业务尤其大有可为。 德铁所购买的数千辆列车和机车的养护都由自己进行,这就存在着一个很大的问题:对于老旧的机车,经常面临原厂备件停产的情况。
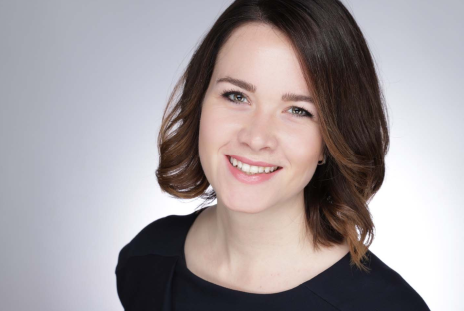
Tina Schlingmann 博士在德国联邦铁路公司致力于增材制造方法的应用
9 个月的轮对轴箱盖交货期
在过去的几年里, 德铁总共在 100 多个使用案例中进行了有关增材制造的可行性研究。“事实证明,增材制造在与可用性相关的备件业务领域尤其大有可为”, Schlingmann 博士强调道。最近的一个案例是在 20 世纪 60 和 70 年代投入营运的一辆 BR 294 型机车的轮对轴箱盖 ——这一配件的损坏和缺失,极有可能造成润滑剂从轴承中逸出,导致轴承损坏,最糟糕的情况下,机车甚至可能因此脱轨。然而,这一备件的交货期长达九个月,在此期间导致的机车停运,给公司带来了巨大的经济损失。轮对轴箱盖的原始铸件重达 11.5 千克,直径 为 374 毫米,高 78毫米。在可行性研究中, 德铁选择与增材制造领域专家 Rolf Lenk GmbH 共同合作,以寻找替代解决方案。
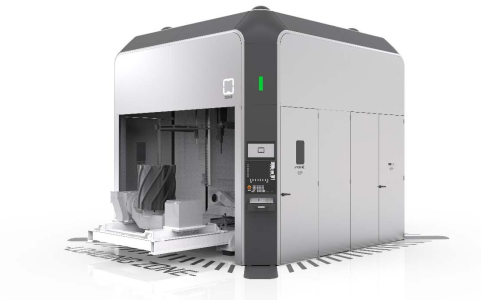
重 11.5 千克的轮对轴箱盖在 GEFERTEC 的 arc605 上打印生产
去年, Rolf Lenk 有一台 GEFERTEC GmbH 的 arc605 机床投产,该机床所使用 3DMP® 工艺(见文本框),是能够进行大型配件高速增材制造的理想选择。
由于老旧车辆的备件通常没有数字形式的 3D 数据,因此首先需要进行完整的逆向工程,在完成该步骤后,还必须为线切割机床整理 3D 数据。在这个项目中所使用的 3DMP®CAM 软件可从配件的数字模型生成特殊的 CNC 数据,然后使用软件由线切割机床逐个焊道进行工件构造。“包括设置在内,在 GEFERTEC 机床上的实际生产时间只有大约 8 小时”, Rolf Lenk 公司项目专员 Matthias Otte 说道。在机床上完成基础加工后,还需对近净成形的配件进行切削加工。从构想、逆向工程到最终生产,整个项目共计用时两个月。“这只是在初次生产工件时需要花费的时间”, M. Otte 强调说:“将来,根据机床的情况,我们可以将这一配件的生产时间缩短至 2 到 3 周。”
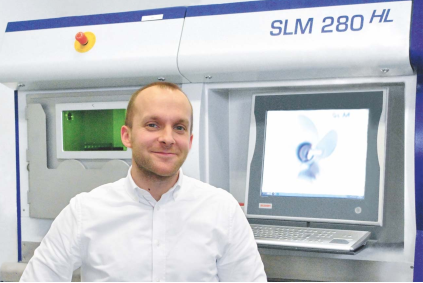
Matthias Otte 是 Rolf Lenk 公司的项目专员,他说:“包括设置在内,轮对轴箱盖在
GEFERTEC 机床上的实际生产时间只有大约 8 个小时。”
德铁和联邦铁路局的材料实验室对成品配件进行过全面彻底的检测。“除通常的材料学检测之外,甚至还进行了计算机断层扫描”, Schlingmann 博士讲道。无一例外都是肯定结果,确证了 3DMP® 工艺进行轮对轴箱盖生产的高品质。现在,只需完成德铁组件的批准认证流程,该备件就能被顺利安装了。
数字化备件仓库列入未来愿景
有关轮对轴箱盖增材制造的可行性研究只是一个开始——未来,德铁在该领域还有多项计划:将备件仓库数字化,以解决仓库运营成本高昂、费用巨大的难题。所有配件将在其中以数字文件的形式提供使用,需要时,可以在合适的机床上进行增材制造。这一方案在提高备件可用性的同时,也将同步节约成本。因为除了生产成本外,公司还担负着运输和库存成本。此外,关键配件还必须在其使用寿命结束后报废。 Schlingmann 博士还特别指出这种解决方案的环境影响:“通过增材制造,可显著减小零部件的碳足迹。”因此,备件增材制造加工也非常贴合德铁“That's Green”的环保主张。
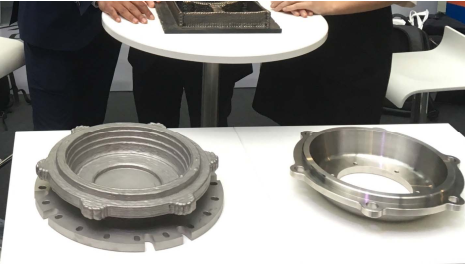
轮对轴箱盖采用 3DMP® 工艺打印(左)然后再进行切削加工(右)
文本框
增材制造机床采用 3DMP® 工艺
GEFERTEC GmbH 的线切割机床使用了 3DMP® 工艺,该工艺已晋升为新的行业标准。这些机床使近净成形的金属坯件生产高效快速且成本低廉。工件的最终质量也完全符合使用标准加工方法生产的工件质量。 3DMP® 工艺使用线材作为原材料,利用它逐个焊道进行工件打印。与使用粉末作为原材料的 3D 打印方法相比,这一制造方法具备诸多优势:无需进行成本高昂的粉末处理,生产更具经济性,且已经适用于大多数标准材料。但最大的优点还是累积率非常高,根据所用材料的不同,每小时可多达 600 cm3。这使得线切割机床更适用于快速和经济的生产,包括以钢、镍基、钛或铝为材质的大尺寸工件生产。线切割机床有适用于约 3 m3 以下工件尺寸的 3 轴版、适用于 0.8 m3 以下工件尺寸的 5 轴版,以及适用于 0.06 m3 以下工件尺寸、更加紧凑的 5 轴版可供选择。专门开发的 CAM 软件可根据工件的 CAD 数据生成数据, CNC 控制系统利用这些数据可对焊接机头进行精确定位。然后,机床会自动完成近净成形工件的生产,并可采用传统的 CNC 铣削技术进行最后加工。与其他制造工艺相比, 3DMP® 工艺优化了材料利用率,从而带来了巨大的成本优势,特别是对于钛等贵金属材料的生产:根据实际应用情况显示,生产成本最多可降低 60 %。
投稿箱:
如果您有机床行业、企业相关新闻稿件发表,或进行资讯合作,欢迎联系本网编辑部, 邮箱:skjcsc@vip.sina.com
如果您有机床行业、企业相关新闻稿件发表,或进行资讯合作,欢迎联系本网编辑部, 邮箱:skjcsc@vip.sina.com