车床代替加工中心加工复杂台阶孔工艺
2024-10-25 来源: 中国铁道科学研究院机车车辆研究所 作者:王立超
[摘 要]分析加工中心加工城轨气动控制阀复杂尺寸台阶孔的弊端,对工艺进行改进,使用车床代替加工中心进行加工。设计了专用车床偏心夹具,设计并制造了圆弧成型刀具,从根本上解决了加工中心加工过程中存在的问题,保证了产品质量,提高了生产效率,降低了生产成本。本工艺经过了实际生产的验证,已应用于批量生产中。
[关键词]台阶孔 ;成型刀具 ;复合钻头 ;复合镗刀 ;偏心夹具 ;平衡块
0、引言
台阶孔在机械加工中极为常见且用途广泛。为达到不同的使用目的,如安装阀芯、弹簧卡圈或者做为阀口与其他零件配合等,台阶孔各段的尺寸、精度和粗糙度要求也各不相同。因此,各段的加工方法不尽相同,常见的有车、钻、铣、铰、镗、加工中心插补加工等。文章以一种城轨上使用的气动控制阀体的生产为例,讨论用车床代替加工中心加工多尺寸台阶孔的方法。
1、简介
气动控制阀是通过压缩空气进行控制,因此对阀体气密性的要求很高,对阀体内部和外部零部件之间的配合精度的要求很高。其原理是通过压缩空气压力使阀芯在孔内来回移动,控制与阀芯孔贯通的各管路的开关。阀芯孔是阀体的核心,台阶尺寸比较多,孔口与其他零部件配合,均为圆弧面。阀体的材料为铝(6061-T6),有两个阀芯孔这两个孔最初在加工中心上加工,但是由于问题比较多,加工成本较高,经过技术分析和讨论,将其改到车床上进行加工。
2、加工中心加工的工艺分析
2.1 第一个孔的工艺分析
第一个孔如图1所示,使用加工中心加工时,这个孔的加工有3个有难度的位置,其中Ⅰ位置难度最大,Ⅱ位置、Ⅲ位置依次次之,下面分别讨论。
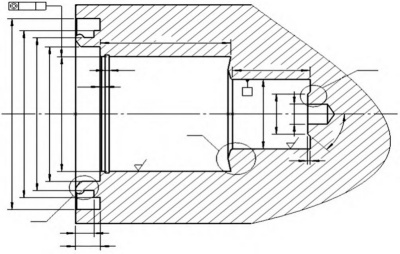
图1 第一个孔示意
(1)Ⅰ位置,放大图如图2所示。其主要难点在于表面粗糙度为 Ra1.6μm、半径为 R1.7mm 的圆弧面的加工。用加工中心加工时,先用 Φ6mm 的立铣刀插补加工,铣出 Φ83 ~ 95mm、宽 6mm 的槽。此时,圆弧面顶点剩余的加工余量为1.8mm,其右侧的 Φ76mm 小圆柱面剩余的加工余量为3.5mm。为了给后续成型刀留出更大的空间,还要插补加工圆弧右侧的 Φ76mm 小圆柱面距离左端面 7.5mm 小台阶的一部分,从外径 Φ83mm 加工到Φ79.6mm。此时,6mm 宽的环槽被加宽到 7.7mm,圆弧面剩余的加工余量为0.1mm,其右侧 Φ76mm 的小圆柱面剩余的加工余量为1.8mm。最后,用定制的成型的铣刀进行插补加工圆弧面以及圆弧右侧直径为 Φ76mm 的小圆柱面到尺寸。
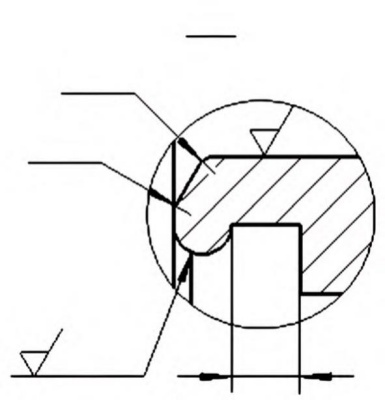
图2 Ⅰ位置放大图
(2)理论上,上述加工方法能留给圆弧成型刀的最大工作宽度为7.7mm。经过计算,圆弧刀最细处的最大理论直径为4.3mm。考虑到机床重复定位精度、刀具加工精度、对刀误差等各种误差的积累,以及进出刀方便和排屑等问题,实际加工中,采用成型刀具最细处直径为3.5mm。成型刀具直径太细是用加工中心加工的致命缺点,给后续加工带来了很多问题,有些甚至无法克服。
2.2 第二个孔的工艺分析
第二个孔如图3所示,其情况与第一个孔类似,主要是圆弧面有些差别。但是由于Ⅰ、Ⅱ和Ⅲ位置都是成型面,需要定制多把成型刀具,下面以第二个孔的Ⅲ位置(图4)为例加以说明。
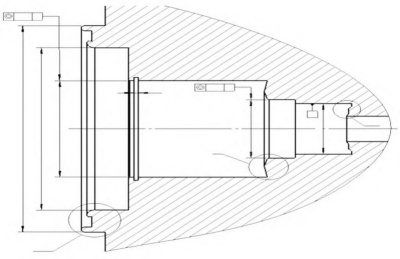
图3 第二个孔示意图
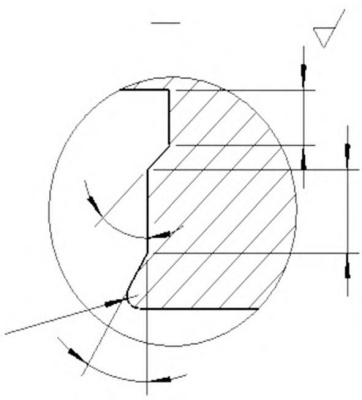
图4 Ⅲ位置放大图
为了减少刀具数量,同时避免更换刀具和插补铣削浪费时间,提高孔的同轴度等加工精度。在加工Ⅲ位置时,先用钻头钻孔,再用定制复合钻头(图5)一次性钻削到位。钻削后,留有精加工余量,再用复合镗刀一次镗削到尺寸。
由于Ⅲ位置成型面的尺寸较宽,约为10mm,复合镗刀加工时,如果采用一个刀片进行加工,由于切削刃过宽容易引起刀具振动而产生振纹,影响表面粗糙度。为了减少振动,提高表面粗糙度和刀具使用寿命,设计成型刀时,可以考虑用两个或两个以上的刀片组合切削来完成一个成型面的加工。文章采用一把复合镗刀上的两个片刀来加工Ⅲ位置,如图6和图7所示。

图5 定制复合钻头
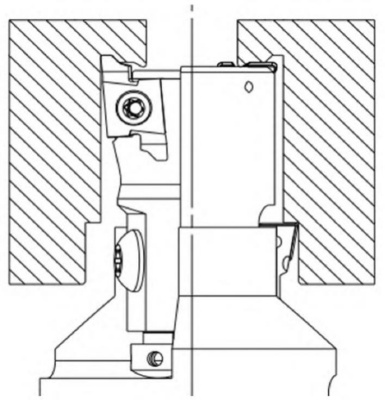
图6 复合镗刀上的片刀1
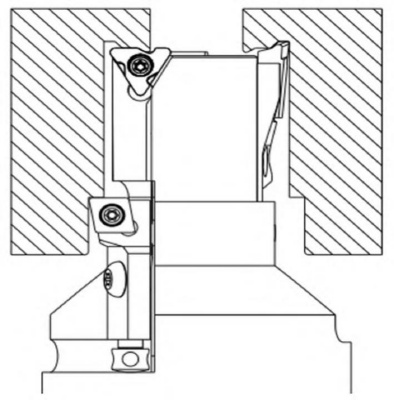
图7 复合镗刀上的片刀2
3、改进后的加工方法及其优缺点
文章对这两个孔的加工方法进行了改进,将其改到车床上进行加工,从根本上解决了加工中心加工存在的的问题。下面主要讨论这两个孔的车床加工工艺的优缺点。
3.1 优点
(1)工件表面粗糙度很好保证。
(2)加工时间大幅减少,加工效率提高。①车刀刀杆直径远大于加工中心成型刀具的刀杆直径,具有更高的刚性,车削进给量和吃刀量显著提升。②从工艺角度上来看,孔的车削加工工艺也远比加工中心插补工艺节省时间。加工中心插补时,工件不动,刀具旋转并以给定的进给速度走一个整圆的轨迹。而车削时,工件旋转,刀具进给轨迹很短,因此大大减少加工时间。③刀具数量减少,相应的减少了对刀、调刀、停车换刀的时间。
(3)减少成型刀具的定制,刀具的购买和维护成本也大大降低。①第一个孔的圆弧位置还是采用非标车刀进行加工,其余的复合钻头、复合镗刀等非标刀具全部取消。②成型车刀的刀杆很粗且刚性很好,选好加工参数,刀具的寿命很高,基本不用更换。③成型槽刀更换通用车刀刀片的成本也要比更换整个整形刀具低。
3.2 缺点
(1)需要设计专用夹具,进行偏心装夹,普通夹具无法满足工艺要求。
(2)工件经过多次装夹,导致孔的位置精度不好保证。
4、车床偏心夹具设计、成型刀具设计
4.1 车床偏心夹具设计
文章设计了两套专用偏心夹具工装以确保两个孔的加工精度。这两套工装的定位和夹紧方式类似,仅存在尺寸和公差上的区别,故文章仅以第一孔为例来讨论工装的设计过程。
夹具采用前序加工中心工序中已加工完毕的 Φ57mm孔进行中心定位,同时使用阀体的外表面做角向定位限制,然后用压板来压紧,车床偏心夹具装配图如图8所示,通过计算,偏心距为70±0.1mm。为了进一步提高定位精度,中心孔定位销可采用胀套设计,夹具的磨损不会影响定位精度。也可以对定位销结构进行改进,改成中心销和套环两部分组成,根据公差范围将套环按0.01mm 分级做成多个。在实际加工中,根据孔的实际尺寸配用套环,以确保中心定位销和孔的间隙不超过0.01mm,来提高定位精度。
由于工件是偏心装夹,如果夹具的总体结构不平衡,夹具随着车床的主轴旋转时会产生的离心力。工件在离心力的作用下将产生振动,影响工件的加工精度和表面粗糙度,同时也加剧机床主轴和轴承的磨损,存在安全隐患。因此,为了提高工件的加工质量和机床的使用寿命,需要对夹具进行平衡。
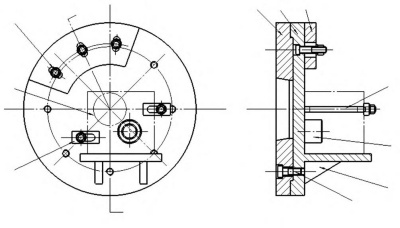
1.压板;2.工件;3.螺母;4.过渡盘;5.夹具;6.平衡块;7.双头螺柱;8.中心孔定位销;9.支撑板;10.螺钉
图8 车床偏心夹具装配图
平衡的方法有两种 :设置平衡块或加工减重孔。文章采用设置平衡块的方法来进行夹具的平衡。计算平衡块重量时,采用隔离法做近似估算。即把工件及夹具上的各个元件,隔离成几个部分,相平衡的各个部分忽略不计,对于不平衡的部分,按力矩平衡原理确定平衡块的重量。经过估算,配重块的重量约为 3.5kg。为了弥补估算法的不准确性,平衡块上开有径向槽,以便在加工中进行调整,以达到更好的平衡效果。
4.2 刀具设计及加工
由于批量不大,为了降低刀具购买成本,文章设计并制造了一把单体式车刀,下面进行说明。
4.2.1 刀片及刀杆的材料选择
由于被加工材料为铝合金6061-T6,其切削性能较好,且加工过程中有切削液散热,所以刀片的工作条件相对较好。成型刀片的材料选用常用的钨系高速钢 W18Cr4V,其具有高硬度、红硬性级高温硬度。切削温度为540℃时,硬度可以保持在 HRC66 ;切削温度为600℃时,硬度可保持在 HRC63。材料具有热处理范围较宽,淬火过程中不易过热,热处理过程不易氧化脱碳,磨削加工性能较好,容易磨出锋利的切削刃,加工工艺成熟等优点。完全满足文章的铝合金加工要求,且具有较长的使用寿命。该钢属于常用的刀具钢,价格低廉,有利于降低成本。
4.2.2 刀具设计
(1)成型刀具设计原理。单体成型刀的轮廓形状是切削刃在垂直于其后刀面的平面上的投影的形状。
(2)刀具轮廓设计。根据刀具设计原理,垂直于后刀面的刀具轮廓与被加工零件轮廓完全一致。
(3)刀具参数设计。为了得到较准确的圆弧轮廓,刀具的前角选为0°。综合考虑刀具强度和表面粗糙度,后角选为10°。为了在有限的刀具工作空间内,尽可能提高刀具的强度,刀头背面选择10°,如图9所示。
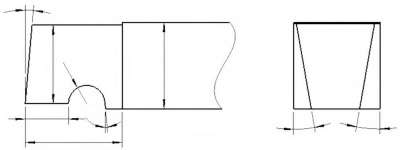
图9 刀具二维图
4.2.3 刀具加工
刀具的加工思路是完全模拟刀具切削时的工作状态,在线切割机床上加工刀具轮廓,以保证成型刀具轮廓的准确性。加工刀具时,根据刀具后角的度数10°,使用工装将刀具垫高 10°,再利用线切割按照圆弧的轮廓来切割成型刀具。这种加工方法加工出的刀具的实际后角是变化的,只有与线切割机床走刀方向相垂直的那段轮廓的后角是10°,其他不垂直位置的刀具实际后角都大于10°。但是这不影响刀具的轮廓和加工精度。
5、提高孔加工质量的工艺改进
(1)由于阀体内有很多孔,其中一些与阀芯孔相贯通。为了解决孔相交处的毛刺问题,在工艺安排上,其他表面粗糙度要求不高的通气孔先加工,重要的阀芯孔均是最后加工,以防止毛刺方向朝向阀芯孔内侧。
(2)每完成一道工序,均采用压缩空气吹去所有残留、铝屑等杂质。待所有加工工序完成后,用40MPa 的高压水枪进行清洗,确保毛刺、残屑全部清洗干净,以防在产品使用时产生不良影响。
(3)所有孔都进行人工去毛刺,特别在两个阀芯孔去毛刺时,在用力以及工具延伸方面,均朝向阀芯孔外侧,再次防止去毛刺边角外翻到阀芯孔,影响其使用性能。
6、结论
(1)通过改进两个阀芯孔的工艺,整个阀体加工时间节省了近50min,大大缩短了加工时间,提高了生产效率。
(2)从根本上解决了加工中心圆弧成型刀具太细而导致刀具折断等各种问题,保证了产品的加工质量。
(3)自行设计并制造了高效且易于维护成型车刀,这种加工方法加工的刀具轮廓形状的准确性很高,简单、实用、成本低廉。
(4)减少了多把复合钻头、复合镗刀的使用,大大节省了刀具费用。
投稿箱:
如果您有机床行业、企业相关新闻稿件发表,或进行资讯合作,欢迎联系本网编辑部, 邮箱:skjcsc@vip.sina.com
如果您有机床行业、企业相关新闻稿件发表,或进行资讯合作,欢迎联系本网编辑部, 邮箱:skjcsc@vip.sina.com
更多相关信息