钛合金铣削加工刀具磨损有限元预测分析
2016-12-12 来源:山东大学机械工程学院 作者:孙玉晶 孙杰 李剑峰
摘要:钛合金Ti6Al4V因其优良的综合性能在航空航天领域有着广泛的应用。然而,在钛合金切削过程中,极易出现刀具磨损现象。目前尚缺乏钛合金加工用刀具寿命预测的有效手段和方法。针对这一问题,基于刀具在铣削工作过程中受到的热力耦合作用,利用Fick扩散定律揭示了刀具扩散磨损机理,构建刀具磨损模型;利用有限元仿真软件AdvantEdge的二次开发技术,将刀具磨损模型嵌入到有限元模型中,进行刀具磨损的预测;进而借助刀具寿命试验,验证了刀具磨损模型的可靠性。
关键词:铣削;Ti6Al4V;刀具磨损;磨损模型;有限元
0.前言
钛合金因密度小、比强度高、耐高温、耐腐蚀等一系列优点,广泛应用在航空制造业中[1-2]。由于钛合金具有变形系数小、冷硬现象严重、切削温度高、单位面积上切削力大、刀具易磨损等特点,使其成了典型的难加工材料[3]。硬质合金因其硬度高、耐磨性好、机械强度高、耐腐蚀性和抗氧化性好等优良的性能而广泛应用于钛合金材料的加工。然而,在钛合金加工过程中,硬质合金刀具易出现磨损,严重的刀具磨损不仅对加工效率和质量有较大影响,而且也关系到加工成本,且目前缺乏钛合金加工用刀具寿命预测的有效手段和方法。因此,研究钛合金加工用刀具的磨损模型,预测刀具磨损量,监测刀具磨损状态,已成为钛合金加工研究领域值得关注的课题。
刀具磨损模型的建立是刀具磨损预测的基础。为了能够定量地表示磨损量,国内外学者对刀具磨损机理及其磨损模型进行了大量的研究,并提出了许多著名的刀具磨损预测模型, 其中包括RABINOWICZ 等[4]提出的磨粒磨损模型,USUI等[5]提出的黏结磨损模型,HARTUNG 等[6]提出的扩散磨损模型等。TAKEYAMA 等[7]提出的刀具磨损模型在考虑了黏结磨损的同时,也考虑了磨粒磨损。KITAGAWA 等[8-9]研究发现,USUI 提出的黏结磨损模型可预测前、后刀面的磨损,并与试验结果吻合较好。
切削钛合金过程中,硬质合金刀具的磨损是由磨粒磨损、黏结磨损及扩散磨损等综合的磨损机理导致而成[10]。许多学者研究证明,在高速条件下,对于硬质合金刀具来讲,其磨损过程是一个热敏扩散过程。MATHEW 等[11]通过利用硬质合金刀具加工碳钢,验证了TAKEYAMA 和MURATA 学者所提出模型的正确性,研究发现当切削温度超过800 ℃时,磨粒磨损是可以忽略的。USUI 等[8-12]的研究发现当切削温度超过877 ℃时,就会出现刀具的脆化现象的产生。MOLINARI 等[13]在近期的研究中提出了新的刀具扩散模型,此扩散模型考虑到温度是控制扩散速率的主要因素[12, 14]。李友生等研究发现600 ℃时硬质合金刀具和Ti6Al4V在结合边界上发生了元素之间的扩散。
综上所述,现有研究已经基本上对钛合金切削中刀具磨损机理达成共识,但是尚缺乏受温度影响的扩散磨损机理的解析阐述。因此,基于前人研究成果,本文揭示了基于Fick 扩散定律的刀具扩散磨损机理,构建了刀具磨损模型;并且利用有限元仿真软件AdvantEdge 的二次开发技术,将刀具磨损模型嵌入有限元模型中,进行刀具磨损的预测;并将模拟仿真结果与刀具寿命试验结果进行对比分析,验证了刀具磨损模型的可靠性。
1.硬质合金与钛合金扩散理论分析
1.1 Fick 扩散定律
德国学者阿道夫-菲克(Adolf Fick)基于试验总结出了各向同性介质在扩散过程所遵循的规律:在单位时间内通过垂直于扩散方向单位截面积的物质流量(称为扩散通量)与该截面处的浓度梯度成正比,即为Fick 扩散定律,可表示为如下。
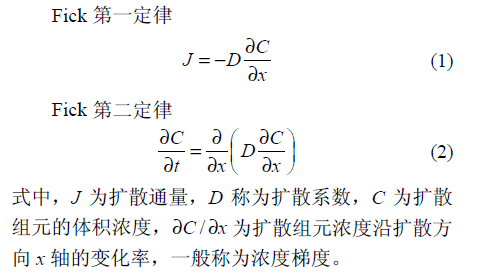
对于硬质合金与钛合金之间的元素扩散,假设此扩散体系各向同性,可将其简化为一维扩散,则扩散的数学方程如式(2)所示。采用分离变数法可以求得Fick 扩散第二定律的一种误差函数解
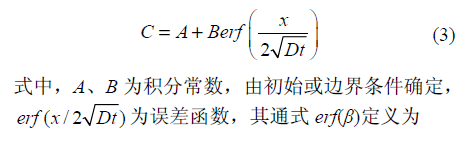
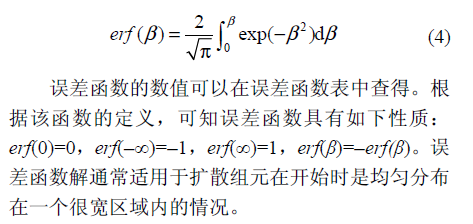
1.2 硬质合金刀具与钛合金扩散理论分析
通过解析扩散方程,可求出扩散时间为t 时沿x 方向溶质浓度分布的解析表达式C=C(x,t),以进行硬质合金刀具材料与钛合金的扩散理论分析。假设有两个截面积相同、成分均匀的合金块S1和S2,如图1 所示。合金块S1 中组元i 的初始浓度为C1,S2 中组元i 的初始浓度为C2,且C2>C1。将S1、S2 两合金块紧密接触在一起,来模拟切削过程中硬质合金刀具与钛合金接触扩散偶。将此接触扩散偶加热至足够高的温度并保温,组元i 在浓度梯度的作用下将由合金块S2 向合金块S1 中扩散。
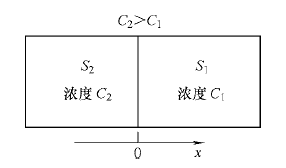
图1 合金块S1、S2 扩散偶示意图
合金块中的扩散组元在开始时是均匀分布在一个很宽区域内,符合Fick 扩散第二定律误差函数解的情况。因合金块足够长,固态下原子扩散很慢,则认为两端浓度恒定。因此可以确定其初始条件和边界条件如下所示。
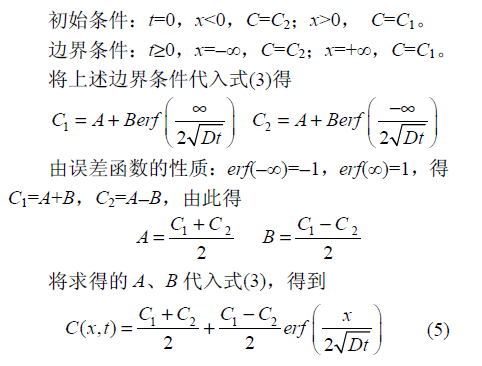
式(5)反映了合金块S1 中组元i 的浓度在不同时刻t,沿x 方向的变化规律。假设图1 中的S2 为硬质合金刀具材料,S1 为钛合金Ti6Al4V。对于硬质合金刀具的元素扩散现象主要是刀具中Co 元素向工件中扩散。刀具材料中W、C 以及工件材料中Ti 元素也有相互扩散现象,但扩散程度较Co 元素低。因此,为了简化研究,假设硬质合金刀具与钛合金工件之间的元素扩散磨损只考虑Co 元素的扩散,则对刀具材料中Co 元素的扩散浓度表达式进行求解。因在元素扩散前,钛合金中没有Co 元素,即C1=0,式(5)可简化为
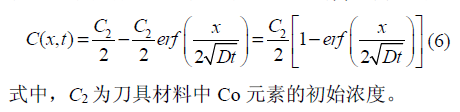
1.3 硬质合金刀具扩散磨损率模型研究
前刀面与切屑以及后刀面与已加工工件的接触区域是刀具扩散磨损现象的集中区域,如图2 所示。
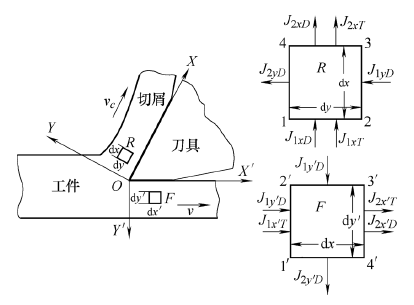
图2 切削过程中的扩散与移动单元示意图
图 2 中,考虑刀具Co 元素向工件扩散的同时,也考虑了由于切屑与工件相对于刀具的不断移动而导致的Co 元素的流失。根据Fick 扩散定律及其解的分析可得刀具前刀面扩散磨损率模型为
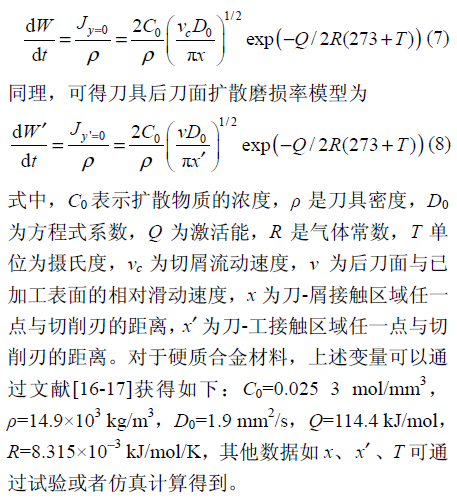
2.硬质合金刀具磨损模型构建
硬质合金刀具在切削钛合金过程中,在切削力、切削热等耦合作用下,磨损过程复杂且磨损机理相互作用。当温度较低时,刀具前、后刀面主要磨损机理是磨粒磨损和黏结磨损;当温度上升到一定程度时,扩散磨损和黏结磨损同时发生,极易形成前刀面月牙洼以及后刀面的磨损带。因此,阐明刀具在不同的温度阶段下主要的磨损机理,可为监测刀具磨损状态、预测刀具寿命、优化刀具结构参数及其工艺参数提供科学合理的技术支持。基于李友生等[15]试验研究发现当切削温度超过600 ℃时,硬质合金刀具和钛合金Ti6Al4V 在结合界面上发生了元素扩散。综合考虑热力耦合作用对刀具磨损影响,在修正TAKEYAMA[7]以及USUI[5]刀具磨损模型的基础上,构建了以切削温度600 ℃为温度阈值的刀具磨损模型,如式(9)所示
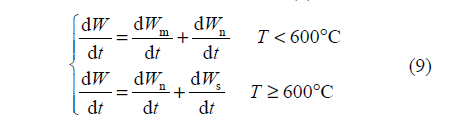
2.1 磨粒磨损率的计算
磨粒磨损率的计算采用RAINOWICZ[18]磨粒磨损模型。当切屑流动速度为vc 时,磨粒磨损率表达式如下
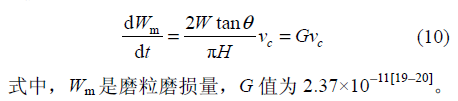
2.2 黏结磨损率的计算
黏结磨损率采用USUI 等[5]黏结磨损模型
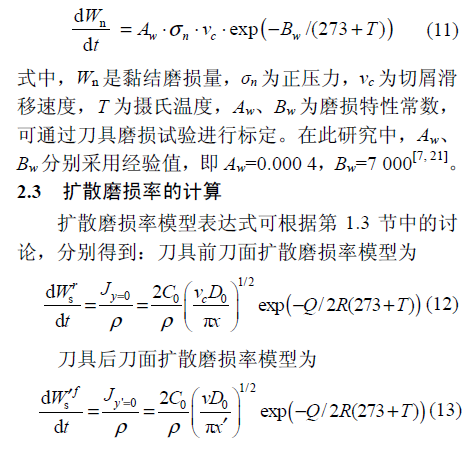
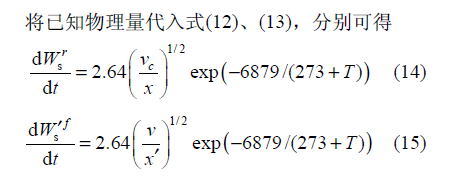
3.铣削钛合金Ti6Al4V 有限元仿真
3.1 钛合金Ti6Al4V 材料本构模型的确定
本研究采用钛合金Ti6Al4V 基于Power-Law 的材料本构模型。Power-Law 模型的基本表达式为[23
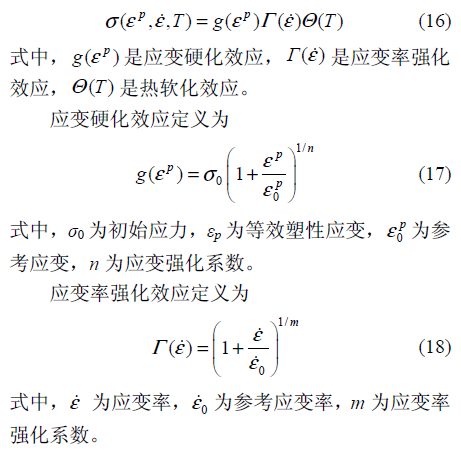
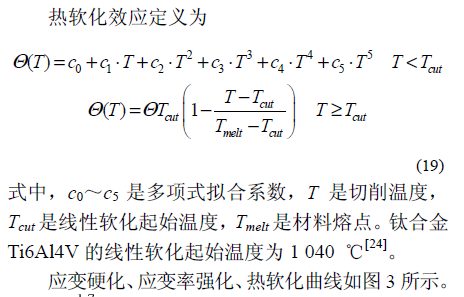
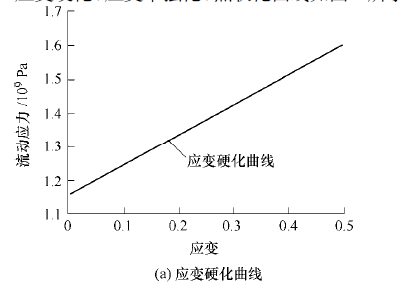
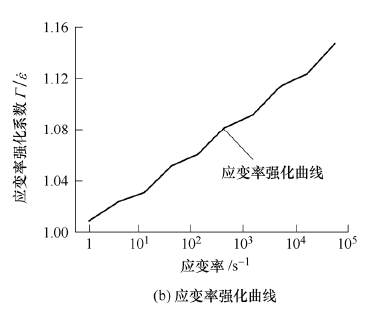
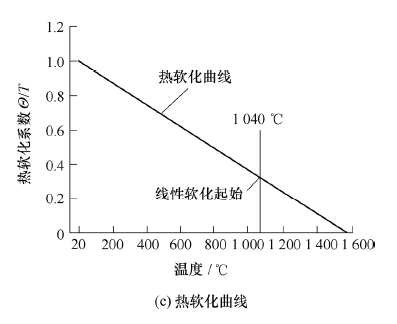
图3 Ti6Al4V 的材料本构模型
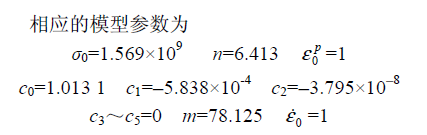
3.2 钛合金Ti6Al4V 材料失效模型的确定
判断材料失效的原则是根据单元积分点处的

3.3 摩擦模型的确定
在切削过程中,刀具前刀面与切屑之间以及后刀面与已加工表面之间存在摩擦。摩擦的大小以及分布特征影响切屑形貌、刀具磨损以及工件表面质量完整性等。本研究采用目前应用最为广泛的库仑摩擦模型描述了切削过程的摩擦关系。
3.4 二维简化铣削模型的建立
鉴于三维切削仿真较复杂,对三维切削合理简化成二维切削进行分析计算。图4 所示为研究采用的铣削简化模型。此模型将刀具进给速度等效成一个垂直于切削方向的速度,以保证在开始切入时未变形切屑厚度最大,而到切出时未变形切屑厚度变为零。此模型体现了在铣削加工中切削厚度随切削时间变化而改变的特点。
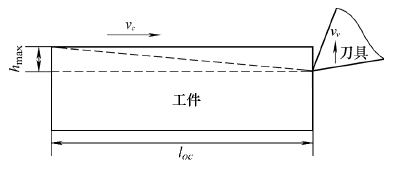
图4 刀具斜向切削模型
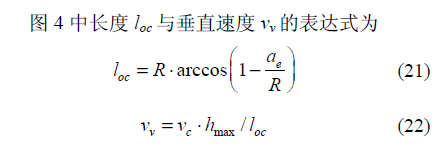
3.5 工件和刀具的建模及其位移边界条件的确定
对工件和刀具结构进行精确建模,并采用四面体单元对模型进行网格划分,如图5 所示。切削过程中,工件在X、Y 方向上的自由度受约束;刀具沿X 轴负方向以恒定的速度对工件进行切削。在仿真过程中,网格在刀具与工件接触区域不断细化,以克服材料大变形引起的网格畸变问题,形成较好的切屑。工件材料为钛合金Ti6Al4V,刀具材料为硬质合金。
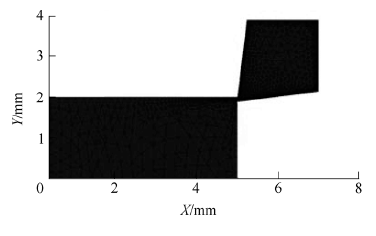
图5 刀具-工件建模及其网格划分
3.6 刀具磨损过程分析子程序的编制
用户子程序将成为有限元模拟程序的一部分。该子程序是在有限元模拟程序中用于计算刀具磨损量等单元变量,它在有限元模拟程序中的位置如图6 所示。
在有限元软件AdvantEdge 中,首先获得刀具与工件接触区的稳定温度场;然后调用刀具磨损子程序计算并提取刀具节点的相关参数,包括应力、温度等,将这些数据代到磨损子程序中计算出节点的磨损,进而根据磨损量更新刀具的几何形貌,如此循环直至达到设定循环时间。其中,刀具与工件接触区稳定温度场的获取是实现有限元仿真的关键问题。在有限元软件AdvantEdge 中,稳定温度场是通过设置“Avg. Length of cut”来获取,即通过设置切削路程到达总路程的百分比来获取切削稳定状态,基于经验值一般取10%。
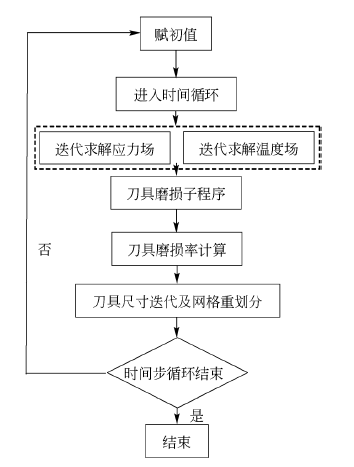
图6 子程序在有限元计算中的位置
4.刀具磨损模型试验验证
4.1 试验设计
试验刀具:整体硬质合金立铣刀。相关参数如表1 所示。
表 1 刀具几何参数
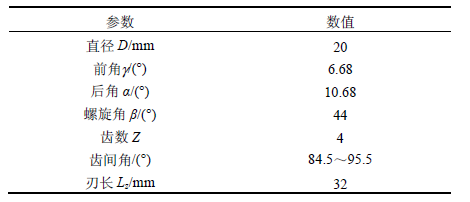
工艺参数:结合大量生产实践与科学试验中钛合金高速铣削较为常用的参数,确定本试验的四个主要工艺参数如表2 所示。
表2 铣削工艺参数

试验工件材料为航空用钛合金Ti6Al4V。试验机床为DAVEWOO ACE-V500 数控加工中心,采用顺铣加工方式。利用VHX-600E 大景深三维显微系统以及Veeco NT9300 光学轮廓仪对刀具的磨损形态进行记录分析。现场加工照片如图7 所示。
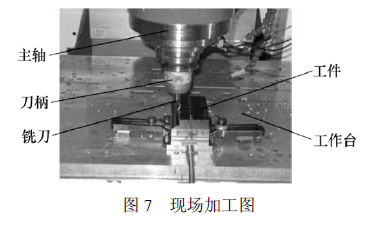
4.2 刀具磨损数值模拟结果与试验结果对比分析
图 8 为仿真获得的刀具磨损结果。由图8 可知,前、后刀面上靠近刀尖处的磨损最严重,并随着切削时间的累加磨损范围扩大,总磨损深度增加;刀具前刀面磨损最深处发生在与切削刃有一定距离处,这与实际加工结果相符。
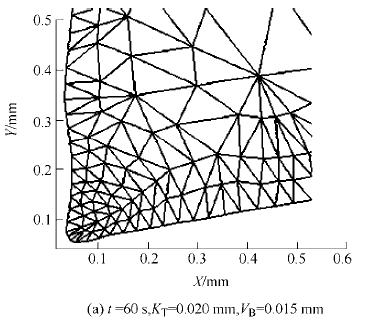
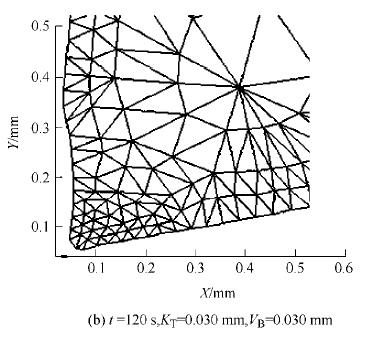
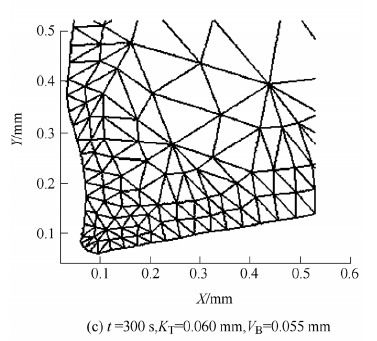
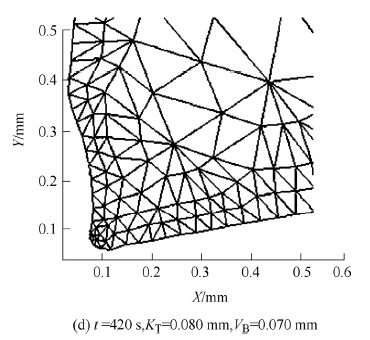
图8 刀具磨损模型切削仿真结果
从图 8、10 可以看出,当切削时间为60 s 时,仿真所得的后刀面磨损宽度VB 为15 μm,试验平均测量值为13 μm;当切削时间为120 s 时,仿真中后刀面磨损宽度与试验测量值基本吻合,大约为30μm;当切削时间为300 s 时,仿真中后刀面磨损宽度VB 为55 μm,试验平均测量值为48 μm;当切削时间为420 s 时,仿真中后刀面磨损宽度VB 为70μm,试验平均测量值为65 μm。通过对仿真与试验获得的刀具前、后刀面磨损形貌数据对比分析,可以发现刀具磨损模型能够较好地反映切削过程中刀具磨损变化规律,并且具有较高的预测精度。但是仿真与试验获得的刀具前、后刀面磨损形貌数据并不完全相同,出现偏差的原因主要有以下几点。
(1) 刀具材料与工件材料的组合差异。由于刀具的磨损模型的构建基于不同学者的研究,而不同的研究学者所研究刀具和工作材料的化学成分和结构是存在差异的,因此经验数据的选取与确定存在一定误差,这种误差将直接影响仿真模型的精确性。
(2) 摩擦模型的简化模型和摩擦因数的选取。在利用有限元软件预测刀具磨损过程中,所采用的是库仑摩擦模型,这样尽管可以简化刀具-切屑接触界面的相互作用,但是会引起界面所产生的温度及接触压力等物理量的变化。因为在实际的切削过程中,刀具-切屑界面之间的相互作用是复杂变化的,特别是在高温作用下,其界面作用变化很大。因此,摩擦模型的简化模型和摩擦因数的选取对仿真模型的精确性的影响很大。
(3) 材料本构关系模型。在此研究中,钛合金Ti6Al4V 的本构关系的建立是基于试验研究,根据数据拟合所得,本构关系模型拟合精度的高低也将直接影响仿真模型的精确性。
(4) 网格细化程度。网格精度也对仿真结果的精度有很大影响。虽然仿真值与试验值有一些偏差,但是它们的整体趋势还是相同的。所以建立的基于温度效应的硬质合金刀具磨损模型基本上是符合实际的,具有一定的工程应用指导意义。
5.结论
(1) 基于Fick 扩散定律,讨论了硬质合金刀具的扩散磨损机理,构建了考虑温度效应的硬质合金刀具磨损模型。
(2) 利用有限元仿真软件AdvantEdge 的二次开发技术,将刀具磨损模型嵌入有限元模型中,确定了基于Power-Law 的钛合金Ti6Al4V 材料本构关系,分析了材料失效模型及摩擦模型。
(3) 进行了刀具寿命试验,并将仿真结果与试验测量结果之间进行对比分析,结果发现刀具磨损模型可以较好地反映切削过程中刀具磨损变化规律,并且具有较高的预测精度。
(4) 具有较高预测精度的刀具磨损模型可为监测刀具磨损状态、预测刀具寿命、优化刀具结构参数及其工艺参数提供了科学合理的技术支持。
投稿箱:
如果您有机床行业、企业相关新闻稿件发表,或进行资讯合作,欢迎联系本网编辑部, 邮箱:skjcsc@vip.sina.com
如果您有机床行业、企业相关新闻稿件发表,或进行资讯合作,欢迎联系本网编辑部, 邮箱:skjcsc@vip.sina.com
更多相关信息