生产线刀具破损监控系统研制
2017-1-13 来源: 大连理工大学机械工程学院 作者:钱峰,董惠敏,董喜望
摘要:研究数控生产线的刀具破损监控问题,对比现有刀具破损监控方法,根据实际工况要求,设计基于机床内置功率传感器的自学习刀具破损监控系统,实现国外进口产品替代。具体实现数控机床联网通讯、接口函数获取机床主轴功率信号、按加工工步分段监控的自学习刀具破损监控功能。并在FANUC 数控系统的数控机床上进行了应用测试,通过实验验证监控系统稳定可靠。
关键词:FUANC 数控系统;主轴功率;分段监控;刀具破损
0.引言
数控机床是数控生产线的核心,也是数控生产线中最容易出问题的环节,对数控机床切削刀具破损在线监控是保证产品质量和提高数控生产线效率的关键技术。刀具破损监控的方法很多,包括直接监控法和间接监控法,直接监控法包括计算机图像处理、光学测量等;间接监控法包括切削力监控、主轴功率监控、振动监控和声发射监控等[1-6] ;直接法虽然监控直观、测量方便,但是一般都是在刀具静态时候测量的,不满足数控生产线对切削刀具在线监控的要求,因此基于数控生产线的刀具破损监控研究的热点还是间接监控法[7]。
国外对刀具破损监控的研究起步较早,也取得了一些成果,已经有不少商用化的刀具状态监控系统。国内在这方面近几年研究的比较多,但是大多数的刀具破损监控成果仅适用于实验室,鲜有稳定可靠商用刀具监控系统。ARTIS 刀具破损监控系统是对机床加工过程中刀具断刀、主轴碰撞等机床状态进行监控的一套监控系统。美国BK Mikro 刀具破损监控系统,该系统主要带有一个机械式的监控测头,能够感知加工过程中刀具的状态变化,并且迅速的反馈刀具状态信息。由于国内没有相应市场化的刀具状态监控产品,而国外的刀具状态监控产品价格昂贵,因此迫切需要开发稳定可靠的产品来替代国外产品的垄断,实现国外进口产品的替代。
现有的刀具破损监控一般都需要外部传感器,传感器要么安装在待加工工件表面,要么安装在刀具上,有的刀具监控系统传感器的安装甚至需要改变机床结构,这种客观的原因严重的阻碍了刀具监控系统的市场化。针对这个问题,本文以数控生产线批量加工的数控机床刀具破损监控为研究对象,提出了利用数控机床内置传感器获取刀具监控信号来实现加工过程中刀具破损监控。
1.刀具破损监控原理
在切削加工过程中,当刀具发生破损时,刀刃状态的改变会引起切削力矩发生变化,从而导致机床主轴功率发生改变,因而通过监控加工过程中机床主轴功率就可以监控刀具的状态。而且机床主轴功率对刀具破损较为敏感,信号获取简单,可避免环境中的切屑、振动等干扰,是生产实际中刀具破损监控较为理想的监测信号[8] 。
数控机床在批量加工过程中,由于加工工艺以及加工参数不发生变化,因此在批量加工中,数控机床主轴的功率信号在时间轴上具有周期性特点[7] 。根据这一特点,可以实时获取数控机床的功率信息并与一组标准加工功率信号进行比较,从而达到对数控机床刀具破损监测的目的。
2.刀具破损监控系统设计
刀具破损监控系统总体分为四个模块,信号采集模块、学习模块、在线监控模块和预警模块。信号采集模块主要是采集监控系统所需要用到的各种信息。学习模块主要存储新刀加工时的主轴功率数据,作为阈值设定的基准。在线监控模块则是实时监测刀具时候超出设定的阈值,如若超出相应的阈值,则传递给预警模块信息。当实时监控时,检测出当前功率超出了设定的阈值则预警模块作用,使机床产生相应的保护动作。
2. 1 刀具破损监控自学习方法
用自学习方法进行刀具切削状态监控,就是在批量生产时,先用锋利的刀刃加工一个工件,保存这一过程的机床的主轴功率。在以后的加工过程中,实时读取机床主轴功率并与之前锋利刀具切削时保存的功率对比,如果出现超出设定的阈值,就说明刀具出现破损,从而实现监控[9] 。监控过程如图1 所示。
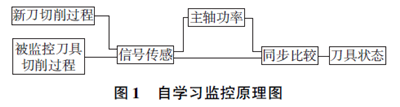
要监控一批零件的加工,只需进行一次自学习过程,以后的监控工作均是重复实时监控过程。用自学习方法的前提就是加工要有一定的批量,如果单件生产就无法应用或从经济角度是不可取的。该方法要求加工过程的重复性包括所加工工件毛坯相同、切削刀具相同、切削用量相同。一般在批量生产中,确定了零件生产工艺,就不会随意更改,因此批量生产过程可保证加工过程严格重复[10] 。自学习方法的根本点就是将实际加工过程的监控数据与自学习过程的标准数据相比较,这就要求必须在相同的条件下进行比较,即数据同步。实现数据的同步对比也是自学习监控方法的关键技术。
2. 2 监控系统功能与结构
本文开发的基于自学习的刀具破损监控系统结构如图2 所示,刀具的切削状态由主轴的功率变化来间接反映,主轴功率信号和加工代码等辅助信息通过数控机床的内置传感器采集,由本文编写的FOCAS2 接口软件实时读取。实时读取的功率信号进入监控模块并依据相应的判定规则做出刀具是否破损的判定,若果判定破损,则给出相应的报警提示。生产线数控机床在加工过程中切削加工的模式为自动状态,此时主轴和进给轴都运动,当监控系统检测到刀具破损信号时,系统发出一个触发信号给机床数控系统,使其修改数控机床的操作模式为手动状态,而机床的手动状态则只是主轴转动,进给停止,这样当监控系统检测到刀具破损信号时,就使得数控机床进给停止,阻止了刀具和工件进一步接触。
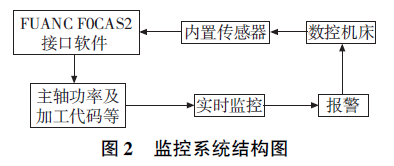
2. 3 监控信号采集模块
数控机床一般都有内置传感器,常用的内置传感器有检测各个轴转速的测速发电机和脉冲编码器,检测位置的直线光栅和光电编码器以及检测各个轴功率的霍尔传感器。使用Microsoft Visual Basic 或者VisualC++ ,配合FANUC 提供的FOCAS2 应用程序接口(API)进行自主编程就可以采集到机床的各个轴的实时转速,各个轴的实时功率以及刀架的位置和当前加工程序等一系列信息。通过FANUC 技术支持提供的信息,实时采集信号的频率可以达到40HZ,对于本文所运用的自学习刀具破损监控原理,能够满足实时监控要求。信号采集过程如图3 所示。
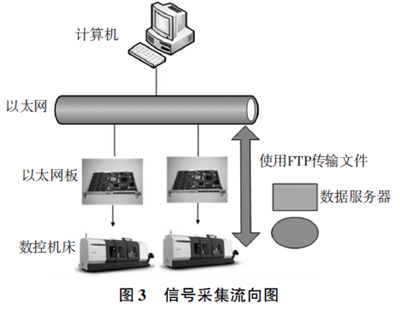
2. 4 系统学习模块和在线监控模块
在学习和监控模块,为了实现分段监控和数据同步对比本文采用对加工数控程序代码进行解析。一个工序的数控加工程序包含有多行NC 代码,而这些NC 代码一般由多个加工工步的NC 代码组成,包含切削过程和非切削过程指令代码。加工人员根据工艺编写相应的数控程序,在数控程序每个工步前分别定义工序号、工步号、刀号、刃号,并分别在数控程序中每个工步的数控代码行指令前加上一行空代码#29 =1,该工步结束数控代码指令后一行加上空代码#29 =0。这样一段正常加工的NC 程序就按不同的工步被#29 =1 和#29 =0 分为多个片段,其中每对#29 =1 和#29 =0 之间的NC 代码就是刀具切削工件的过程的NC 代码#29 =1 和#29 =0之外的数控程序代码是非切削过程的NC 代码。上述过程就是对数控代码按工步分段解析的过程。解析完后的数控程序代码将切削过程和非切削过程以空代码#29 =1 和#29 =0 明显的区分开了,刀具破损监控时只需要对#29 =1 和#29 =0 之间的加工过程进行监控。数控代码分段解析过程如图4 所示。
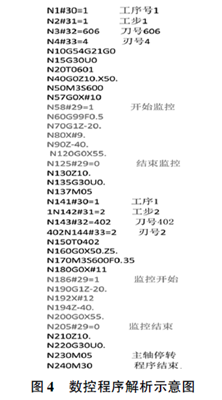
学习数据与实时监控数据同步对比是实现自学习刀具破损监控的关键技术之一。自学习刀具破损监控要求采集的学习功率信号和实时监控功率信号在相同的条件下进行对比,即学习曲线和实时监控曲线对比的时候不能有相位差,数据同步对比如图5 所示,图5a 为非同步对比,图5b 为同步对比。
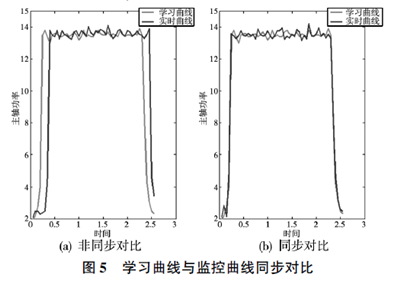
在学习阶段,监控系统读取当前执行数控程序名和当前执行每一行代码的行号,当读取到#29 =1 这一行NC 代码时,系统开始读取并保存主轴功率,直到读取到#29 =0 这一行NC 代码时,停止读取主轴功率,同时保存该工步的工步号、刀号。接下来继续读取当前执行的代码,当读取到下一对#29 =1 和#29 =0 执行上述相同的逻辑,这样一整条数控程序执行完后,在学习阶段就完成了整条数控程序中若干个工步切削过程主轴功率数据的存储。学习过程的算法如图6 所示。
刀具破损自学习监控的阈值设定方式和阈值大小设定直接影响这监控的效果,阈值设定方式有直线阈值和曲线阈值,直线阈值适合于粗加工,曲线阈值适合于半精加工和精加工。根据不同的加工选择不同的阈值设定方式。阈值设置得过小,监控系统反应太灵敏,容易产生误报;阈值设置的过大,可能会漏掉某些破损报警。本文提出一种基于工步分别设置不同阈值的方法,在粗加工和对零件精度要求不严格的工步设置较大的阈值,在精加工和对零件精度要求较高的工步设置较小的阈值。这种基于工步特征设置不同监控阈值的方法相对于对整个加工程序设置一个相同的阈值更加的合理。
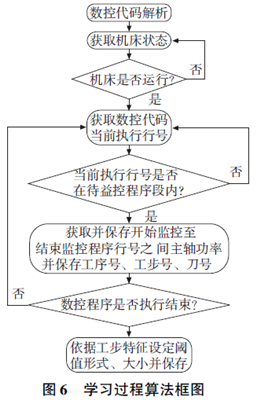
在实时监控阶段,监控系统读取当前执行程序名和当前执行代码,首先判断当前执行程序名和学习阶段执行的程序名是否相同,若相同,则读取当前执行代码,当读取到#29 =1 这一行代码时,系统开始读取执行代码和主轴功率,同时将采集到的工步号、刀号与学习阶段保存工步号、刀号匹配,并将实时采集的主轴功率与匹配上对应学习时的功率逐点对比,判断是否超出设定的阈值,当读取到#29 =0 这一行代码时,结束读取数据,直到整个加工程序结束。学习阶段的算法如图7 所示。

3.刀具破损监控系统软件开发
针对上文介绍的自学习刀具破损监控原理和算法,运用Visual C++ 和SQL SERVER 开发工具开发了刀具破损监控软件,实现了自动生产线批量生产刀具破损实时在线监控功能。软件主要实现批量加工时刀具破损。
学习时,按照解析之后的数控加工代码加工一个标准零件,存储加工过程中的主轴功率数据,在整个数控代码的所有工步执行完之后完成学习过程。阈值设定时首先选择阈值的形式,有直线阈值和曲线阈值两种可供选择。阈值的大小是相对于学习曲线来计算的,曲线形式的阈值上限是学习样本中最大功率值的设定百分比加上当前每个时刻功率,阈值下限是学习样本中每个时刻的功率值减去最小功率的设定百分比。直线形式的阈值上限是学习样本中最大值加上最大功率值的设定百分比,阈值下限是学习样本中最小值减去最小功率的设定百分比。在所有工步学习完后可以给每个工步分别设定不同的阈值大小。实时监控时,系统实时读取当前主轴功率,并与学习样本同步对比,判断当前主轴功率是否超出设定的阈值上下限,若超出,则监控系统报警,数控机床进给停止。刀具破损监控系统的界面图8、图9 所示。
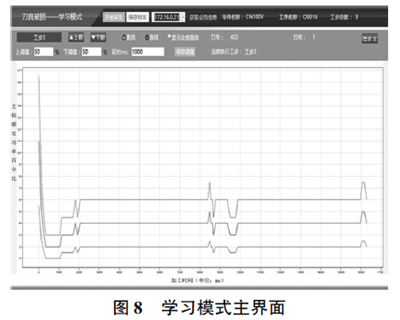
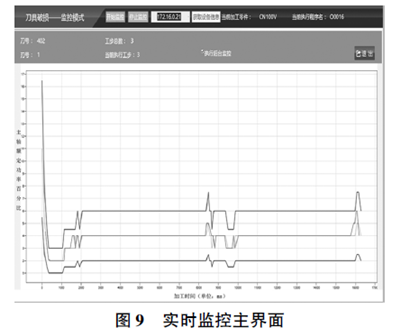
4.应用测试
为了验证监控系统的效果,做了如下的实验:实验机床使用的是沈阳机床A5-T2 单机自动化数控机床,数控操作系统为FANUC-0i-mate,实验试件为Cr40 阶梯轴,刀具采用的是SANDVIK 外圆粗加工车刀和外圆精加工车刀,刀具材料为硬质合金。加工工序含有两个工步,用粗加工刀具加工阶梯轴外圆,切削用量为切削速度V = 200m/ min,进给量f = 0. 5mm/ r,背吃刀量ap =3. 5mm,上下阈值均设定为40%。精加工切削用量为切削速度V = 500 m/ min,进给量f =0. 2mm/ r,背吃刀量ap = 1. 0mm,上下阈值均设定为25%。刀具破损是随机发生的,为了使加工过程中刀具发生破损,在工件中嵌入硬质点,这样当刀尖碰到硬质点时,刀具必将破损。实验中一共切削了50 个工件,其中25 个工件在粗加工工步嵌入硬质点,25 个工件在精加工工步嵌入硬质点。粗加工工步中当切屑到工件含有硬质点部位时,全部监控到,准确率100%,精加工工步当切削到工件含有硬质点部位时,监控到了24 个,有两个没有报警,报警准确率98%。
5.结论
本文论述了基于FANUC 提供的FOCAS2 应用程序接口(API)进行自主编程获刀具破损取监控信号,为数控机床状态监控信号获取方式的进一步研究提供了借鉴意义。采用数控机床内置传感器获取监控信号,很好的解决了传统刀具破损监控传感器的安装难题。结合NC 代码解析来甄别切削过程和非切削过程解决了以往刀具破损监控对整个加工过程监控的盲目性,为后续研究刀具破损监控拓展了研究思路。开发的刀具破损监控系统已经应用在企业中,实践证明本系统监控效果良好运行可靠.
投稿箱:
如果您有机床行业、企业相关新闻稿件发表,或进行资讯合作,欢迎联系本网编辑部, 邮箱:skjcsc@vip.sina.com
如果您有机床行业、企业相关新闻稿件发表,或进行资讯合作,欢迎联系本网编辑部, 邮箱:skjcsc@vip.sina.com
更多相关信息