钛合金螺旋铣孔的切削力和切削温度试验研究
2017-2-21 来源:大连理工大学精密与特种加工教育部重点实验 作者:王欢,董志刚,康仁科,杨国林,谢海龙
摘要:螺旋铣孔技术是航空装备制造领域新出现的制孔技术,因具有加工质量好、效率高等优点被用于加工钛合金、复合材料等难加工材料。采用包括切削速度、切向每齿进给量、轴向每齿进给量和螺旋导程4个基本加工参数描述螺旋铣孔过程,分析了基本参数和螺旋铣孔输入加工参数(自转、公转、进给)之间的关系。在自行研制的螺旋铣孔试验平台上开展了钛合金材料的加工试验,研究了钛合金螺旋铣孔加工中切削温度及切削力的特征,以及基本加工参数对切削温度和切削力的影响规律。试验结果表明,在螺旋导程一定时,切削温度主要由切削速度决定,而与轴向每齿进给量及切向每齿进给量无明显关系;而切削力的影响规律与切削温度相反。切削温度是影响螺旋铣孔过程中刀具磨损及加工孔质量的主要因素。在需同时保证加工效率及加工质量的前提下,应尽量选择大的切向每齿进给量、大的轴向每齿进给量和较低的切削速度。
关键词:钛合金;螺旋铣孔;切削温度;切削力
钛合金具有比强度高、热强度好、耐腐蚀、良好的低温性能,与纤维增强复合材料相容性好及储藏资源丰富等优点,广泛应用于航空航天、国防军工等领域,如飞机的机翼、蒙皮、舱段等。连接孔的加工是钛合金构件上最典型和重要的加工之一卜21。由于钛合金材料的难加工特性,采用传统的麻花钻工艺制孔时,容易形成孔壁热损伤,并存在钻削质量低、孔壁表面质量差等问题。螺旋铣孔技术是航空装备制造领域新兴的高效、高质量制孔技术。螺旋铣孔采用立铣刀,以螺旋轨迹方式进给加工出比刀具直径大的孔。与传统的钻孔技术相比,螺旋铣孔技术具有很多优点:轴向力小;可以实现一种刀具加工不同直径孔,减少刀具种类;切屑不连续,排屑空间大,切屑能更好排出,减少切屑与已加工表面的摩擦,从而提高加工表面质量;断续的加工过程有利于刀具散热,能够降低刀具磨损,延长刀具使用寿命等卜81。国内外在螺旋铣孔末端执行器开发一一01、螺旋铣孔工艺研究。131和专用刀具研制等方面开展了大量工作。
切削力和切削温度是切削加工中重要的过程参数,对钛合金材料制孔精度和加工质量有重要影响,国内外学者对钛合金切削加工的切削力和切削温度进行了大量研究。作为一种重要的制孔方式,螺旋铣孔加工自出现以来也受到了国内外研究人员的关注。从加工几何学角度分析,螺旋铣孔加工过程中铣刀同时做公转、自转和进给运动,加工时同时存在底刃的连续切削及侧刃的断续切削,其未变形切屑的几何形状和尺寸与切削参数之间存在定量的关系。通过研究铣刀侧刃切削与底刃切削去除量之间的关系发现,在铣刀形状固定的条件下,铣刀侧刃切削去除材料和底刃切削去除材料间的比例仅与刀具直径和加工孔径有关,该比例对轴向切削力、加工温度和质量有直接影响。螺旋铣孔加工过程中工件上任一点的温升是铣刀端刃切削生热与侧刃切削生热同时作用的结果,结合螺旋铣动力学分析和传热学理论可建立螺旋铣孑L三维温度预测模型并分析螺旋铣孔切削温度特征。利用上述模型分析螺旋铣孔温度发现,主轴转速与螺旋导程增加时切削温度升高,且热源与测温点越接近时,测量温度越高心。
上述模型为理解螺旋铣孔加工机理提供了有益参考,但由于建模过程中对热源的简化以及求解过程的简化,在描述螺旋铣孔切削温度数值及分布规律准确性方面还需系统的试验验证。在试验研究方面,采用螺旋铣孔及传统钻孔两种方法在铝合金、钛合金、纤维增强复合材料上进行制孔加工,从切削力、孑L壁质量、热损伤和机械损伤等方面进行对比发现,与传统的钻孑L工艺相比,螺旋铣孑L方法在减小切削力、控制切削温度、保证制孔质量等方面均具有明显优势。
目前国内外对钛合金螺旋铣孑L技术的试验研究多集中于一种加工参数下与传统钻孔的对比研究,而对于螺旋铣孑L的重要切削参数如切削速度、轴向及切向每齿进给量等对于切削温度及切削力的影响规律尚不明确。鉴于切削力和切削温度对螺旋铣孔工艺过程和制孔质量的重要影响,尤其是对于易形成热损伤的钛合金材料来说,系统研究螺旋铣削过程的力和温度特征,分析基本切削参数对其影响的规律十分必要。
本文分析螺旋铣孑L加工中铣刀端刃和侧刃切削形成切屑的形状参数及其与加工参数之间的关系,在此基础上设计螺旋铣孔切削力和切削温度在线检测方案,开展钛合金材料螺旋铣孑L加工试验,检测加工过程中的切削力和切削温度,对比研究不同参数下刀具磨损状态及加工孔出口形貌,以期明确影响钛合金螺旋铣孑L加工质量的主要因素和规律,这对理解螺旋铣孔加工机理,确定合理的加工参数具有指导意义。
1.试验设计
1.1加工参数的选择
螺旋铣孔原理如图l所示,刀具中心的轨迹是螺旋线,加工运动由刀具高速自转、刀具绕加工孔中心公转及刀具沿轴向方向直线进给3个运动组合而成喁l。螺旋铣孔的未变形切屑如图2所示,包括底刃切削形成的连续切屑及侧刃切削形成的断续切屑两部分。当刀具确定后,螺旋铣孔未变形切屑的形状及尺寸由切向每
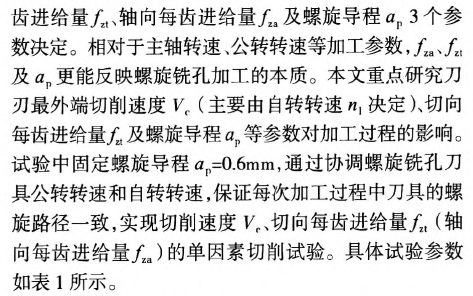
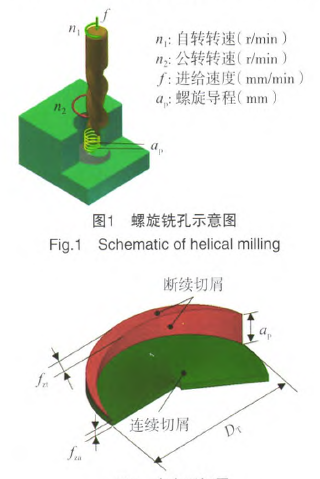
图2未变形切屑
表1 试验参数及切削条件

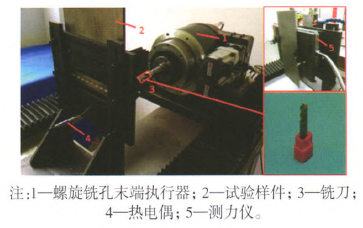
图3螺旋铣子L装置
心量为6mm。螺旋铣孔单元安装于二维工作台上,二维工作台可提供轴向和径向两个方向的最高进给速度均为500mm/min。所用试验材料为厚度7mm的Tc4钛合金板。采用氮化硅纳米涂层的钨钢立铣刀进行螺旋铣孔试验,铣刀参数如表2所示。由于测力仪及热电偶安装方式的限制,测温及测力试验在加工参数、刀具及工件材料相同的情况下分别进行。
表2刀具参数

采用YDCB—III三向测力仪检测切削力,测得的信号经过电荷放大器LN586lA处理后,利用数据采集卡PCI9118DG进行数据采集。采用标准K型铠装热电偶检测切削温度,热电偶直径0.5mm,热响应时间0.2s,允差等级0.4。热电偶检测的信号通过NI uSB一9213测温模块放大后,由cDAQ一9174 UsB机箱通过usB数据线传输给计算机,该测温模块具有内置冷端温度补偿功能及标准热电偶的电势一温度标定程序。热电偶安装在螺旋铣孔的出口侧直径0.6mm、深2mm的小孔中,小孔中心与待加工孔中心距6mm,如图4所示。热电偶及小孔孔壁的空隙填充导热胶以提高导热性。采用如图5所示的方法标定测量点与加工孔孔壁之间温度差。首先在钛合金板上加工一个直径lomm的通孔,在孑L内通过过盈配合插入一个紫铜棒,距紫铜棒外缘0.1mm处加工一个直径0.6mm、深度2mm的小孔。在如图5(a)所示与之相对的钛合金孑L壁边缘位置同样加工一个直径0.6mm、深度2mm的小孔。将热电偶I、热电偶Ⅱ分别插入紫铜棒及钛合金的小孑L中,而非绝对值,因此标定误差可以忽略。
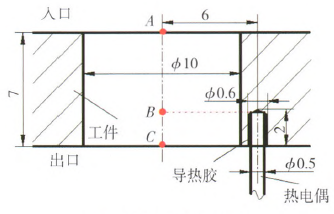
图4热电偶安装示意图
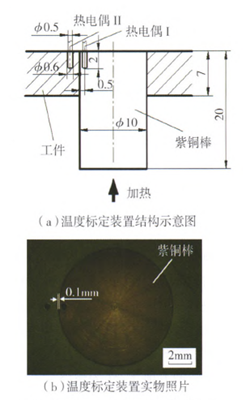
图5螺旋铣孔切削温度标定装置
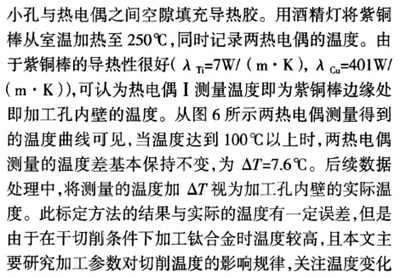
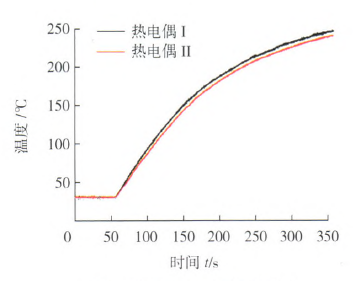
图6热电偶I和II测量温度对比
2.试验结果
2.1 典型切削温度曲线
图7所示为一条典型的切削温度随时间变化的曲线,螺旋铣孔参数Vc=40lTl/min,.fzt=40μm,ap=o.6mm。在4点以前,切削尚未开始,采集室温。A曰段曲线对应刀具开始切人工件直至切到与热电偶距离最近的过程。在这一阶段,刀具在轴线方向上逐渐接近热电偶的测温点,传人测温点的热量不断增加,使测量温度逐渐升高直至达到温度最高值。BC段曲线对应刀具切过测温点直至切出工件的阶段,随着刀具与测温点在轴向方向的远离,由于材料不断被去除,散热面积增加,散出的热量大于传人测温点的热量,测量点温度下降。c点以后的曲线对应刀具切出工件后的阶段,切削加工停止,工件在空气中快速冷却,直至接近室温。4c段温度曲线呈现波浪式变化,起伏的幅度随着切削温度的增加而增加,波动周期保持恒定为f,。在后续的数据处理中,选取每次采集到的最大值咒作为最终切削温度。
2.2典型切削力曲线
图8所示为加工参数Vc=40m/min,fzt=40μm,
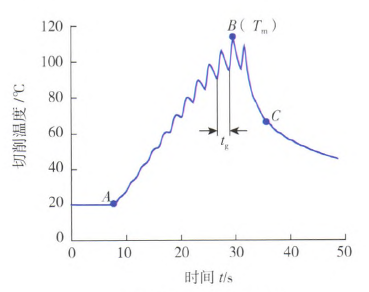
图7典型切削温度曲线
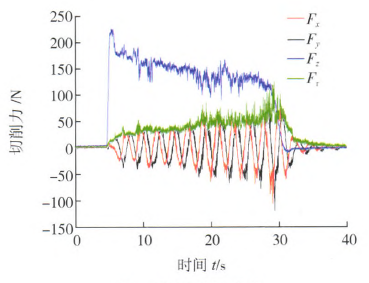
图8典型切削力曲线
ap=0.6mm时采集到的3向切削力曲线。定义z向为刀具轴线方向,工件表面为xoy平面。由图8可见,轴向力F:大于径向力F。及F。。在切削开始时,由于刀具和工件突然接触,轴向切削力疋由零跳跃至226N,并在接下来的2s左右的时间内下降至185N。随后的稳定切削段内,,,逐渐下降,下降速度约为2.94N,s,直至切出工件。在切削刃切透工件的最后约2s时间内,轴向切削力快速降低直至为零。在后续讨论中,将图8中从切削力稳定至切削结束的阶段作为有效切削力段,并去除开始2s及结束前2s中的不稳定数据,分别取该阶段的平均值、最大值和最小值作为轴向切削力凡的均值及上下误差范围进行对比讨论。切向力只、F。在切削开始前为零,在切削周期内出现周期性波动,其波动幅值逐渐增加,波动周期为定值,与切削温度波动周期相同。在整个切削阶段,以及每个波动周期内,B、R大小及变化趋势一致,但存在0.56s的时间差。测力仪采集到的x方向及y方向切削力在x缈平面内互呈90。,将其按式(1)合成得到合力F,,由图8可见,径向合力f随着时间逐渐增加。

在后续讨论中,同样将切削阶段去除不稳定阶段数据作为有效数据,取该段内F的平均值、最大值和最小值作为切向力的均值及上下误差范围进行对比讨论。
2.3切削参数对切削温度及切削力的影响
图9所示为切削速度及切削温度对切削力的影响,
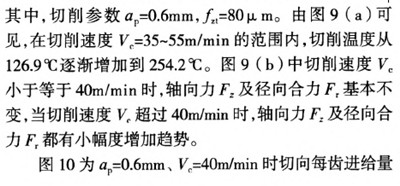
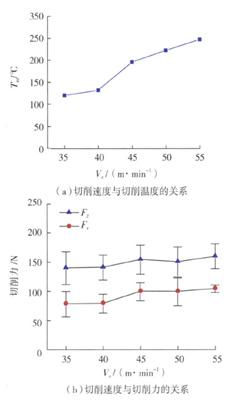
图9切削速度对切削温度和切削力的影晌
与切削温度及切削力的关系。随着切向每齿进给量fzt从40μm增加到120μm,切削温度虽有小的波动,但是基本稳定在(125±3)℃,无明显变化。而轴向力fz及径向合力f都随着切向每齿进给量厶的增加而增加,轴向力E变化范围为128.3~214.9N,径向合力fr变化范围52.5~106.2N。
2.4加工孔出口质量
切削力及切削温度直接影响加工孔的质量,为探究切削温度及切削力对加工孔显微形貌的影响,分别选取最大切削温度咒两组参数及最大轴向力t两组参数加工孔出口形貌进行检测。图ll为不同加工参数下孔出口形貌,图11(a)及图11(b)加工孔的出口较平整,无明显缺陷,两组参数下的切削温度丁。分别为120.9cC及131.7℃,轴向力疋分别为164.8N及214.9N;而图11(c)及图11(d)出口的表面形貌较差,有明显的飞边、毛刺现象,切削温度r。分别为229.2cc及254.2℃,轴向力F:分别为150.8N及160.5N。对比可知,加工孔的出口质量对切削温度比较敏感,而切削力对其影响较小,切削温度越高,加工孔的出口质量越差。
2.5刀具形貌
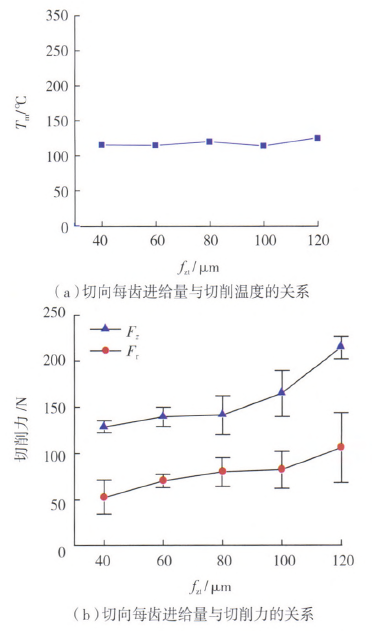
图10切向每齿进给量对切削温度和切削力的影响
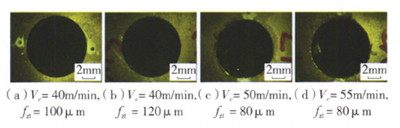
图1 1 不同加工参数下孔出口形貌
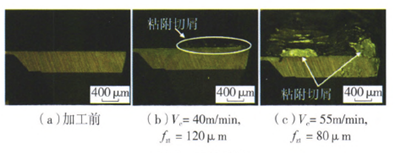
图12刀具形貌
不同参数下切削后的刀具形貌如图12所示。图12(a)为加工前刀具形貌图,切削刃完好无破损。采用Vc=40μm,fzt=120μm加工后的刀具形貌如图12(b)所示,此时的切削温度为131.7℃,轴向力为214.9N。
刀刃最外侧粘附有微量切屑,切削刃没有大的破损及堵塞现象,仍有很好的切削能力,孔出口处的材料很容易被切断,出口质量较好。图12(c)为加工参数为y,=55m/min,正。=80斗m时刀具形貌图,此时的切削温度为254.2℃,可以看出整个刀刃粘附有大量切屑.此时刀具已失去切削能力。
3.讨论
从图7和图8所示的切削温度和切削力可见,两者都存在波动,且波动周期一致,与螺旋铣孔加工中公转周期相同。螺旋铣孔加工中测温点温度变化取决于从切削点传来的热量,以及向外散出的热量。刀具的螺旋公转运动使得切削点距离测温点的位置周期性变化,使得切削温度出现波动。这也证明螺旋铣孔相对于传统钻孔的优势,螺旋铣孑L的偏心加工方式可以使工件在每个公转周期内散热,降低工件温度,这在加工导热性差的钛合金及导热情况复杂的复合材料时避免了热损伤,具有很大的优势。
由图8可见,随着螺旋铣削加工的进行,径向切削力Fx、Fy的峰值逐渐变大,这是因为所用铣刀侧刃部分高度为10mm,大于工件厚度,因此在整个螺旋铣孑L加工过程中,随着刀具的轴向进给,与孑L壁直接作用的侧刃长度一直在增加,侧刃与孔壁之间的切削力和摩擦力逐渐增加。在此阶段内,只、F.大小及变化趋势一致,存在0.56s的时间差,与公转转速对比可知,上述时间内刀具相对孔中心转过90。角,即两径向力只、F。之间存在90。的相位差。在切削过程中铣刀端刃的切削厚度和速度均保持相同,但可见轴向切削力由最大值逐渐降低,与文献[21]中的切削力信号一致。结合切削温度检测结果分析,随着切削的进行,切削区域温度逐渐升高,这可能导致钛合金材料软化,使铣刀底端横刃的切削变得轻快,导致轴向切削力降低。
从图9可知,切削速度l,,对切削温度丁。的影响较大而对切削力的影响较小。由文献[4】知,当切削速度y,增加时螺旋导程口。、轴向每齿进给量.正。、切向每齿进给量.丘。不变,整个未变形切屑的形状及尺寸都保持不变,但是单位时间内刀具与切屑及已加工表面的摩擦次数增加,做功增加,摩擦产热大幅度增加,热量来不及扩散,流人工件内的热量增加,使得测量温度丁。升高。同时,增加切削速度y。.时,切削温度n增加,材料软化,切削阻力减小,切削力减小。但是在干切削条件下,加工条件比较恶劣,当切削温度增加到一定值时,切屑流动性变差,造成排屑槽堵塞,如图12(c)所示刀刃的切削能力降低,部分材料靠刀具挤压去除,使得轴向力t及径向合力f都增加。
从图10(a)及图lo(b)可知,切向每齿进给量fz1对于切削力的影响较大而对切削温度几乎没有影响。这是因为切削速度y,不变时,单位时间内摩擦产热基本不变。当切向每齿进给量.厶及轴向每齿进给量.正。增加,底刃及侧刃的切削厚度增加,未变形切屑变厚,切屑变形脱离工件所做的功增加,导致总切削产热增加;但另一方面,由L0ewen和MC Shaw于1954年提出切削温度解析方法口21可知,当切削厚度增加时,切屑剪切变形产热流入切屑的比例月。增大,流人工件的比例1一月。减小,切削热绝大部分由切屑带走,以上两方面的影响使得传人工件的热量基本不变,测量温度基本不变。
由图9(b)及图10(b)可见,轴向力F大于径向合力F,这是因为在螺旋铣孑L过程中,同时存在底刃的连续钻削及侧刃的断续铣削两种加工形式,以铣削和钻削方式去除材料的体积之比(R)可由式(2)计算。计算可知本试验中铣削作用和钻削作用的比例为4,9,钻削比铣削的贡献大,从而使轴向力E大于径向合力F。

切削温度对刀具状态和钛合金孑L出口质量有重要影响。温度过高时使钛合金切屑软化,容易滞留在排屑槽中,甚至粘附于前刀面,导致切削刃的切削能力减弱,孔出口处的一部分材料靠刀具的挤压去除,所以在出口处出现飞边及毛刺现象。较高的切削温度不仅降低加工孔的质量,同时也影响刀具的使用寿命。
4.结论
开展了钛合金螺旋铣孔试验研究,分析了加工参数对切削力、切削温度及制孑L质量的影响,得出以下主要结论。
(1)在螺旋铣孑L加工过程中,测量点的温度由于传热与散热相互影响而先上升后下降,局部温度曲线呈周期性波动,波动周期即为刀具公转周期。
(2)螺旋铣孔加工中F。、E随刀具的公转呈周期性波动,在每个周期内,只、F。大小及变化趋势一致,但存在900的相位差。
(3)切削速度增加时,切削温度明显上升,切削力基本保持不变;轴向每齿进给量及切向每齿进给量增加,切削温度无明显变化,切削力上升。切削温度是影响钛合金加工孔表面质量的主要因素。切削温度高,切屑流动性变差,容易粘附在排屑槽中堵塞刀具,降低刀具的切削能力,导致在工件表面出口处有大量毛刺存在,降低加工孔的质量。
(4)在需同时保证加工效率及加工质量的前提下,应尽量选择大的切向每齿进给量、大的轴向每齿进给量和较低的切削速度。
投稿箱:
如果您有机床行业、企业相关新闻稿件发表,或进行资讯合作,欢迎联系本网编辑部, 邮箱:skjcsc@vip.sina.com
如果您有机床行业、企业相关新闻稿件发表,或进行资讯合作,欢迎联系本网编辑部, 邮箱:skjcsc@vip.sina.com
更多相关信息