提高三角形螺纹数控车削质量的方法
2018-6-11 来源: 郑州工业应用技术学院 作者:牛瑞利
摘 要: 三角形螺纹在工程中应用广泛,其加工质量是保障产品质量的一个重要环节。在车削加工中,根据不同材料的工件需要选用不同材料的刀具、设置不同的切削参数和选择不同的切削液等,螺距的不同也需要采用不同的编程方法。本文结合实例从工艺因素、切削方式、程序编制和操作等方面阐述了提高三角形螺纹数控车削质量的方法。
关键词: 三角形螺纹; 刀具; 切削用量; 切削方式; 编程。
0 引 言
螺纹联接在工程应用中经常用到,螺纹车削是数控车床常见的任务。数控车床可以加工多种螺纹而三角形螺纹加工是最为普遍的。用数控车床车削螺纹比用普通车床车削螺
纹操作方便,加工效率高,是目前加工螺纹普遍采用的方法。螺纹的加工质量与参数工艺选择、刀具选择、编程和操作等因素有关。
本文以 GSK980TD 数控系统,加工材料为 45 钢,毛坯为 Φ42mm 棒料,螺距为 1. 5mm 的三角螺纹为例,加工工件如图 1 所示,就如何提高三角形螺纹的车削质量进行探讨。
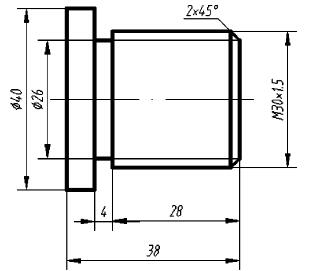
图1 零件图
1 、工艺因素对加工质量的影响
螺纹加工的工艺因素是对螺纹加工质量影响的基本因素,掌握好螺纹加工的工艺因素对提高螺纹加工质量非常重要。
1. 1 刀具材料和刀具几何角度的合理选择
刀具在切削过程中要受高压、高温和较大摩擦力作用,因此刀具要有高硬度、高耐热性、好的耐磨性,也要有足够的强度和韧性。强度和韧性好的材料,其硬度和耐磨性较差,反之亦然。数控车刀常用的材料有高速钢、硬质合金、陶瓷和超硬材料等。
根据工件的材料不同,选用适合的刀具,可以提高零件质量、提高生产效率和降低成本。
对于螺纹刀具,除了选择合适的材料外,合理选择刀具的几何角度和刀尖过渡刃形状对提高加工质量很重要 。车刀的几何角度有主偏角、副偏角、刀尖角、刃倾角、前角、后角和副后角。螺纹车刀的主要角度是刀尖角,其刀尖角的大小直接决定螺纹的牙型,普通三角螺纹车刀,刃倾角一般为 10°,刀尖角为 59°16',刀尖圆弧半径公式计算 r = 0. 144P( 式中 P为螺距)。
副偏角对表面粗糙度影响最大,主偏角和副偏角愈小,刀尖圆角半径愈大的螺纹车刀加工出的螺纹表面质量越低。刀具前角和后角愈大,刀具愈锋利,螺纹表面质量越高,但强度变差。
1. 2 切削用量的合理选用
合理选用切削用量对提高数控车床的加工质量至关重要。切削用量包括背吃刀量、进给量和切削速度,螺纹切削用量的选择应根据工件的材料、螺距大小以及螺纹所处的加工
位置等因素来决定。螺纹的切削用量应逐渐减小,螺纹精车时根据材料有时可选零进给用量。经过总结,列出车削钢类材料的三角形螺纹常用切削用量表,如表 1 所示。
表 1 钢类材料的三角螺纹常用切削用量表
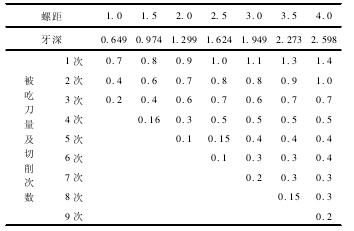
螺纹切削速度应选低些,数控车床车螺纹主要是依靠主轴编码器,当主轴转速选择过高时,通过编码器发出的定位脉冲有可能因“过冲”而导致螺纹烂牙,大多数数控车床的数控
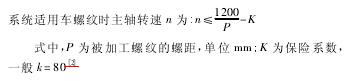
1. 3 切削液的合理选择
合理地使用切削液,能减小由于温度升高引起的加工误差,切削液在刀具和工件表面间形成润滑膜,冲走铁屑减少刀具与工件间的摩擦,减少刀具磨损,提高刀具的使用寿命,防止工件生锈。
数控车削中常用的切削液是乳化液,浓度为5% - 25% ,有些螺纹加工还可以选用油为切削液。在车削铸铁等脆性材料时,不用切削液,因为碎切屑容易与切削液混在一起阻塞机床床鞍的运动,车螺纹时可以刷少量的油; 用高速钢刀具切削钢、铝等塑性金属时,要用切削液; 当切削液的流量能完全冷却硬质合金刀具时,可以提高刀具的使用寿命,所以车削钢等塑性材料以用切削液为好。
1. 4 工件装夹方法的合理选择
工件的装夹一定要牢固和有足够的刚度。轴类零件一般用三爪自定心卡盘直接装夹,在保证加工长度的前提下工件伸出长度越小越好,保证工件的加工刚度,棒料中心线尽量与主轴中心线重合,以防止打刀。工件的装夹方法必须合理,否则对工件的加工质量将带来负面影响,不能发挥数控车床高精度加工的优越性。
2 、螺纹切削的进刀方式
螺纹的切削方式主要是根据螺距大小来确定,受切削机床、工件材料、刀片槽形的影响。直螺纹切削的进刀方式主要有直进式切削、斜进式切削和左右侧面交替进刀三种,如图 2所示,正确选择螺纹切削的进刀方式对螺纹加工的质量也很重要。
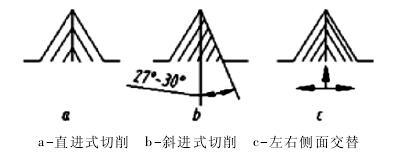
图 2 螺纹车削进刀方式
直进式切削就是指螺纹刀具径向直接进刀,又叫径向切削。螺纹刀的两侧刃都参加了切削,所以刀具在轴向的切削分力会相互抵消,刀具磨损均匀,减小螺纹车削时因轴向切削分力导致车刀偏歪的现象,加工的螺纹牙形清晰,质量较好。但由于直进式切削螺纹时受力集中,排屑不畅,散热不好等因素,特别是车削大于 3mm 以上的螺距时,由于切削深度大,刀刃磨损较快,容易造成螺纹中径产生误差,所以直进式切削法适用于 3mm 以下的螺纹车削。斜进式切削是指刀具以和径向成 27°-30°的角度进刀车削。
在螺纹车削中,由于其为单侧刃切削,刀具受力较小,排屑流畅,散热效果好,所以加工出的螺纹表面粗糙度稍低。但是刀刃较易损伤和磨损,造成加工出的螺纹表面不直,刀尖角容易因磨损发生变化,加工出的螺纹牙形精度较差。因此,斜进式切削适合加工螺距在 3mm 以上的螺纹。
左右侧面交替进刀是指刀具每次径向进给时,刀具横向向左或向右移运动一定的距离,使车刀每次进刀只有一侧刃参加切削,左右交替进行。由于此方法编程较复杂,操作不如上面两种方便,一般用于通用车床和螺距在 3mm 以上的螺纹加工。
3 、三角形螺纹数控车削的编程
以 GSK980TD 为例,该系统螺纹加工指令有等螺距螺纹切削指令 G32、变螺距螺纹切削指令 G34、Z 轴攻丝循环指令G33、螺 纹 切 削 循 环 指 令 G92 和 多 重 螺 纹 切 削 循 环 指 令G76]。G32 和 G92 指令可以加工等螺距的直螺纹、锥螺纹、端面螺纹,切削方式属于直进式切削和左右侧面交替切削,G32 指令属于单程序段,多次走刀切削时编程较长,一般不常用,G92 指令的切削方式属于直进式切削和左右侧面交替切削,由于该指令加工螺纹中径误差较大,但牙形精度较高,一般多用于小螺距高精度螺纹的加工。
G76 指令可以加工带螺纹退尾的直螺纹和锥螺纹,可实现单侧刀刃螺纹切削,吃刀量逐渐减小,有利于保护刀具、提高螺纹精度,但不能加工端面螺纹,由于该指令工艺性比较合理且编程效率较高所以应用较为广泛。根据以上分析,图 1 所示的螺纹加工用 G92 指令,G92 指令的螺纹走刀路径如图 3 所示,A 点为螺纹起刀点( 终点) ,B点为螺纹切削起点,L1 为螺纹空刀切入量( L1≥2P) ,L0 为螺纹有效切削量,L2 为螺纹空刀退出量( L2≥0. 5P) ,L3 为螺纹退尾宽度( 当螺纹没有退刀槽时根据螺距设置,有退刀槽时可以为 0) ,C 点为切削终点,D 点为螺纹径向退刀终点。
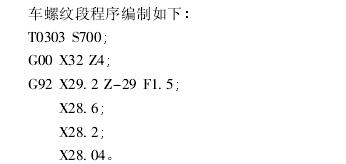
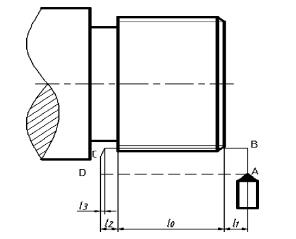
图 3 G92 指令的走刀路径
4 、螺纹加工的操作技巧
螺纹刀的对刀技巧,螺纹刀具不像外圆车刀能精确地对出其位置。螺纹轴向对刀一般是靠操作者的目测刀尖与工件原点是否重合。
在螺纹轴向要求较高时,由于操作者的目测误差,易出现对刀不准确,造成过切的现象。解决此问题,操作者可在对刀时,在轴向和径向方向都预留对刀余量( 螺纹长轴一般多留
0. 5mm - 1mm,螺纹短轴一般多留 0. 2mm -0. 5mm) 。
通过首件试切,测量后精确调整刀补进行修正( 轴向用±W,径向用±U) ,确保不出现过切现象。螺纹刀多次使用后,特别是在加工不锈钢、镍合金等硬度高的材料时,刀具磨损较快,要多测量,工件在测量合格后方可卸下,掌握刀具磨损规律,可在程序运行前修改刀补,提高螺纹加工质量和生产效率。
5 、结语
在实际加工生产中,除了根据工件材料、螺距等选择适合的刀具,还要根据螺纹的螺距及加工特点来选择适宜的编程方式,灵活地运用螺纹加工指令,有时还可以采用两次加工,循环指令( G76) 和单段指令( G32) 相结合的方法,发挥各指令的特长,保证螺纹的加工质量。合理运用以上知识,可有效地提高螺纹加工的合格率,保证三角形螺纹的加工质量
。
投稿箱:
如果您有机床行业、企业相关新闻稿件发表,或进行资讯合作,欢迎联系本网编辑部, 邮箱:skjcsc@vip.sina.com
如果您有机床行业、企业相关新闻稿件发表,或进行资讯合作,欢迎联系本网编辑部, 邮箱:skjcsc@vip.sina.com
更多相关信息