表面织构化刀具的研究现状与进展
2019-11-14 来源: 南京航空航天大学 机电学院 作者:郝秀清,宋晓路,李亮
摘要:高速切削加工作为难加工材料的主要加工方式,在其切削过程中,刀具的快速磨损、加工表面质量差等问题显著。近些年来,表面织构由于在控制摩擦、减小磨损和改善润滑性能等方面的作用引起了国内外学术界和产业界的广泛兴趣,为刀具减摩降磨技术的研究提供了新方向。
表面织构效应是通过在摩擦副表面加工出具有不同形状几何参数和分布特征的微凹坑、微沟槽等阵列结构时,表面的摩擦磨损和润滑特性随之改变的热动力学效应。针对表面织构技术在刀具方面的应用研究,描述了刀具表面织构的主要制备方法,对比分析了各种制备方法的优缺点,然后分别阐述了微沟槽织构、微凹坑织构、纳米织构/微纳复合结构阵列以及织构化自润滑刀具在减缓刀具磨损、提高加工质量等方面的研究现状与进展,同时分析了表面织构改善刀具系统摩擦学性能的原因和机理,最后指出刀具表面织构技术目前研究存在的问题及其对刀具减摩降磨的重要意义。
关键词:表面织构;刀具;减摩降磨;加工质量;仿生学;润滑
高速切削技术作为先进制造技术中的重要技术之一,广泛应用于航空航天、模具、机械装备、汽车和医学等领域。与传统切削加工相比,高速切削加工能够提高生产效率,但对难加工材料而言,高速切削加工过程中的高切削温度和切削区域的剧烈摩擦会加快刀具磨损,刀-屑界面摩擦系数增大,影响表面加工质量。高切削温度会导致主切削刃处应力及其温度梯度增大,刀具耐用度大为降低,与此同时,刀具的快速磨损严重制约了切削效率的提高。在高速切削加工过程中,刀-屑界面上的材料会紧密结合,外部的润滑液很难进入刀-屑界面,只能通过毛细渗透等方式到达摩擦副界面的边界区域。上述原因共同导致了刀具的快速磨损和工件表面加工质量差的问题,故为了提高刀具耐用度和改善表面加工质量,可从改善切削区的摩擦润滑状况出发,优化刀具结构设计。
表面织构技术作为表面工程技术中的一种,近些年成为表面工程领域中的研究热点。所谓表面织构,是指通过电沉积、电火花、激光加工、光刻加工等方法在表面加工出不同几何参数和分布特征的微凹坑、微沟槽等阵列结构。通过表面织构技术,可以改变刀具表面的拓扑形态,同时设计合理的表面织构来改善切削加工过程中刀-屑界面的摩擦状
况,从而减缓刀具磨损,这对切削加工而言具有极为深远的工程意义。目前,国内外众多学者已开展了表面织构化刀具在不同切削条件下切削性能的研究,研究结果表明,通过在刀具表面加工出微织构,可有效改善刀-屑界面的摩擦学状态,从而减缓刀具磨损,提高表面质量和加工精度。
1 、 织构化刀具的制备方法
在刀具表面加工微织构是一种提高刀-屑界面摩擦学性能的有效手段。刀具表面微织构所具备的储油、储屑、减小刀-屑接触长度和切屑粘结等功能,可有效改善系统摩擦状况和提高刀具切削性能。目前,刀具表面织构加工的主要方法有激光加工、电火花加工、磨削加工、离子束加工等。几种微织构表面加工方法的优缺点如表 1 所示.
表 1 表面微织构几种制备方法的优缺点

激光加工法是通过激光器发射激光至工件表面,使其表面部分材料发生气化和熔融。该方法具有能量密度高、加工效率高及加工过程污染小等优点,是目前刀具表面织构加工的主要技术。江苏大学符永宏等采用二极管泵浦 Nd:YAG 激光器在YG6X 硬质合金刀具前刀面加工出具有一定尺寸和分布特征的微沟槽,其中微沟槽宽度为 50 μm,深度为 8 μm,微沟槽与实际切屑流向分别成 0°、30°和 60°。宋起飞等采用激光技术在试样表面加工出凹坑等微织构,所加工的凹坑直径分别为0. 4 mm 和 0. 8 mm,间距为 3 mm。胡天昌等则是通过激光技术在 45#钢表面加工出填充有固体润滑剂 Mo S2的微坑,该微坑型织构在材料表面规则排布,其中微坑直径分别为 65、170 和 260 μm,深度在 14~16 μm 之间。
电火花加工则是通过工件电极与工具电极之间产生脉冲火花放电来腐蚀工件,从而获得所需的加工形状。电火花加工法适用于传统加工方式难以加工的材料,同时还能进行复杂结构的加工。Koshy 等通过电火花技术加工在刀具表面加工面型织构和微沟槽阵列,其中微沟槽方向与主切削刃平行,深度和宽度约为 100 μm。山东大学宋文龙等采用微细电火花技术在 YG8 硬质合金刀具表面加工出孔状微织构,其中微孔直径为 0.35 mm,深度为 1 mm。
磨削加工法是通过砂轮尖端在刀具表面加工出微织构。与其他非接触式加工方法相比,磨削加工在微织构形状控制和表面质量方面具有一定优势。华南理工大学谢晋课题组采用磨削技术磨削刀具前刀面,在未涂层刀具表面加工出 V 形的不同方向的微沟槽,其中微沟槽深度在 25~149 μm 之间,方向分别与主切削刃平行、成 45°夹角和垂直。
离子束加工是在真空条件下,将离子束加速聚焦并投射到材料表面,产生溅射效应和注入效应,从而在材料表面加工出微织构。离子束加工具有加工精度高,加工应力和热变形都极小等优点,但其加工成本高、生产效率低,故目前尚无法进行大规模应用。孙华亮等通过聚焦离子束技术在 Ti Al N 涂层刀具前刀面加工微沟槽,其中所采用的离子束能量为 30 ke V,束流为 21 n A,所加工出的微沟槽宽度为 2 μm,深度为 1.2 μm。英国 Chang W L 等采用离子束加工技术在微铣刀前刀面分别加工出与主切削刃平行、成45°夹角和垂直的微沟槽刀具,其中微沟槽宽度为 4.5 μm,深度为 7.5 μm,间距为 4.5 μm。
2 、织构化刀具的几何类型及减摩机理
刀具表面织构的几何类型主要有以下几种:微凹坑、微沟槽和纳米织构/微纳复合结构阵列三大类(图 1)。刀具表面的织构形貌在很大程度上影响着微织构刀具的减摩性能,只有当织构的几何参数在一定范围内,它才能发挥其润滑作用,为刀具减摩降磨提供保障。
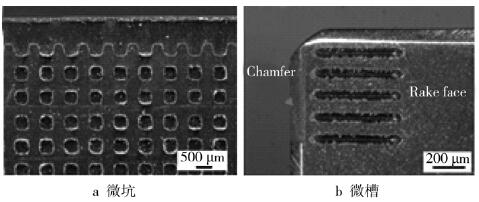
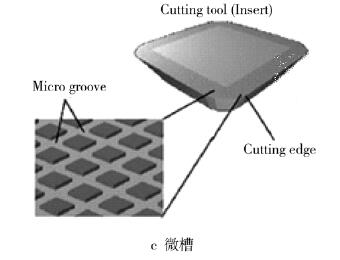
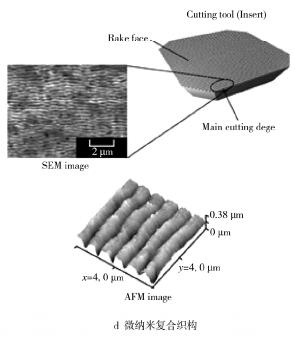
图 1 几种刀具表面织构类型
2.1 微沟槽型织构
刀具表面加工微沟槽示例如图 2 所示,与微坑织构相比,微沟槽方向的不同在一定程度上会影响切屑的排出,进而影响织构化刀具的切削性能,故与微凹坑织构相比,其减摩机理更复杂。
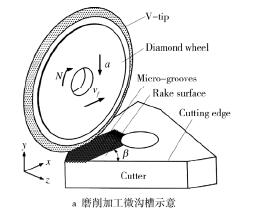
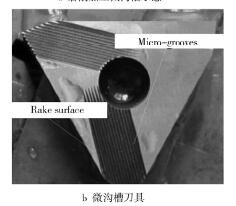
图 2 在刀具表面加工出微沟槽
目前在激光加工刀具表面微织构领域,对硬质合金织构化刀具的研究最深入。长春理工大学于占江等采用激光加工法在 YG8 硬质合金表面加工出微沟槽,然后在车床上进行 AL6061 铝棒切削试验,研究结果表明,微沟槽的置入在一定程度上减小了刀具前刀面磨损并改善了工件的表面质量,通过仿真分析,发现与无织构刀具相比,微沟槽刀具应力分布状况得到改善。与此同时,他们还对比了横向、纵向和斜向微沟槽的切削性能,发现横向微沟槽排屑较困难,切屑粘结现象比较严重,刀具表面有部分基体剥落,纵向和斜向微沟槽有利于切屑排出,切屑粘结程度轻,刀具耐磨性得到提高。华中科技大学吴克忠等设计了具有减摩功能的织构刀具,并用此进行经正火后的 50#钢切削试验,发现微织构刀具能有效降低切削过程中的主切削力,同时还可提高刀具的断屑性能。在传统切削加工中,刀具表面易出现粘结现象,而刀具表面与切屑粘结会加快刀具的磨损,从而降低刀具耐用度。巴西 Davi N 等在 4 mm 水层下或空气中用不同功率的 Nd:YAG 激光器在硬质合金刀具表面加工出微织构,然后采用 PVD 技术在刀具表面沉积一层 Ti Al N 涂层,由此制备出 Ti Al N 涂层微织构刀具并用它们干车削 45#钢,结果表明微织构刀具会减缓刀具表面的磨损,但不会改变其磨损机制;与此同时刀具表面粗糙度相应增大,提高了基体上涂层的粘合性能。激光辐射所产生的热会使刀具表面硬质合金颗粒的化学成分发生改变,其 WC 相会生成新的 WC1-x相,微织构刀具表面抗粘结性能因此增强。
Silva W 等 同样用 Nd:YAG 激光器在硬质合金刀具前刀面加工出阵列微沟槽,通过 CVD 技术在刀具前刀面沉积三层涂层(Ti CN-Al2O3-Ti N),微沟槽方向分别平行和垂直于切屑流向,研究结果表明与无织构刀具相比,微织构刀具可以降低刀具前刀面磨损和后刀面磨损,提高刀具耐用度,如图3 所示,当微沟槽方向垂直于切屑流向时刀具切削性能更好。
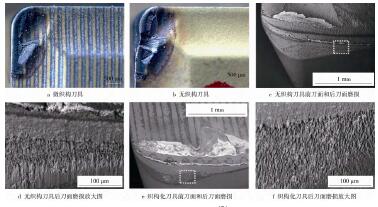
图 3 刀具表面磨损
日本 Kawasegia N 和 Enomoto T 等进行了硬质合金微织构刀具的切削试验及其减摩机理研究,发现与无织构刀具相比,微织构刀具可有效降低切削力并提高刀具耐磨性,与此同时刀具表面的润滑状态得到改善。究其原因可能是因为刀具表面微织构的置入减小了刀-屑接触长度,减缓了刀具磨损,另外由于微沟槽具有储油、储屑等功能,微织构刀具表面的润滑状态得到改善,减小了刀-屑界面的摩擦。日本大阪大学 Sugihara T 等针对刀具表面的严重粘结现象,利用飞秒激光系统在刀具表面加工出微沟槽,在不同润滑条件下切削中碳钢,研究结果表明微沟槽的存在可同时减缓刀具表面的前刀面和后刀面磨损,微织构的尺寸也会影响刀具的耐磨性,沟槽宽度适当增加可进一步减缓刀具磨损,但在干切条件下,过大的沟槽宽度反而起负面作用,此时接触应力增大,会抵消宽度增大所带来的影响。此时织构参数和切削条件对刀具抗磨性的影响如图 4 所示。
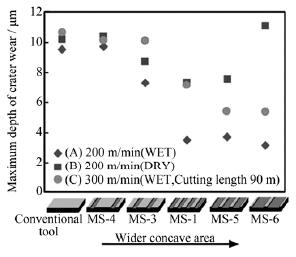
图 4 不同条件下刀具前刀面磨损最大深度
山东大学张克栋等采用激光加工技术在刀具表面加工微沟槽,然后再沉积一层 Ti Al N 薄膜,如图 5 所示。在润滑条件和干切削条件下分别比较无织构涂层刀具与织构化涂层刀具的切削性能,发现在润滑条件下切削液会进入微沟槽,微沟槽收集切屑并为润滑膜提供切削液,故织构化涂层刀具可减缓刀具前刀面磨损,降低切削力和切削温度。在干切削条件下,织构化涂层刀具和无织构涂层刀具的切削力基本相等,由此可推测微沟槽具有储存润滑液的功能。
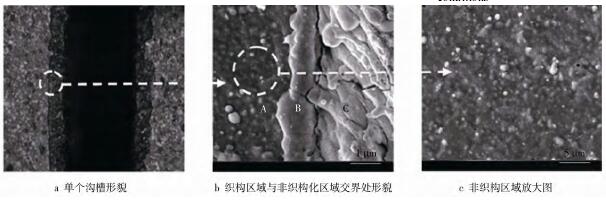
图 5 织构化涂层刀具沟槽形貌、织构区域与非织构化区域交界处形貌
此外,也有学者将微沟槽织构应用至钻头表面。美国西北大 Ling T 等通过激光加工技术在钻头表面加工出微沟槽阵列,利用该微织构钻头在钛合金板上进行钻孔试验,结果表明在钻孔过程中无织构钻头和织构化钻头表面均有切屑脱落,但织构化钻头切屑脱落更多,相同钻削条件下微织构钻头耐用度更高。他们同时还加工了微沟槽密度分别为 10%和 20%的织构化钻头,发现沟槽密度为 10%的织构化钻头耐用度最高,由此可见微沟槽密度并非越大越好,而是应处于一定范围内。
2.2 微凹坑型织构
合肥工业大学杨超等采用激光加工技术在硬质合金刀具前刀面加工出微凹坑型织构并进行切削试验,该微织构三维形貌如图 6 所示。通过改变微坑的直径、深度、面积占有率等参数,来比较不同几何参数的微坑型织构对刀具切削性能的影响,研究结果表明,切削过程中切削液可迅速进入微凹坑,改善刀-屑界面润滑状态,但只有当微织构几何参数合适时,该微织构刀具才能有效改善刀具的切削性能,在此基础上得到了微织构几何参数的最优组合,当微坑直径为 110 μm 和 200 μm,深度为 7 μm,面积占有率为 20%及微坑直径为 170 μm,深度为 10 μm,面积占有率为 10%时,微织构刀具切削性能最好。Obikawa T 等在硬质合金刀具前刀面制备了微方坑阵列织构,通过正交切削试验,研究了微凹坑织构对刀-屑界面润滑状态的影响。德国 Johannes K 等同样在硬质合金刀具表面加工出微凹坑织构,如图 7 所示。之后由此进行碳素钢切削试验,研究结果表明与无织构刀具相比,微凹坑型织构在切削过程中积屑瘤更稳定,这在一定程度上减缓了刀具磨损,提高了刀具耐用度。美国 Lei S 等采用飞秒激光技术在硬质合金刀具前刀面加工出直径在几十到几百微米的微坑织构,微坑织构中还填有固体或液体润滑剂,由此进行低碳钢切削试验。研究结果表明:与无织构刀具相比,微坑型织构刀具降低了切削力,其刀-屑接触长度降低约 30%。
Ma J F 等则对微坑织构参数在切削过程中的作用进行了仿真分析,结果表明微坑的存在降低了切削过程中的能量消耗,并减小了切削力。
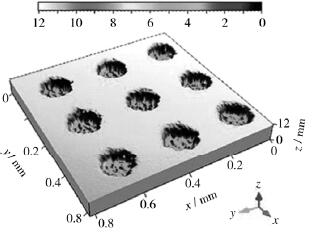
图 6 微凹坑型织构三维形貌
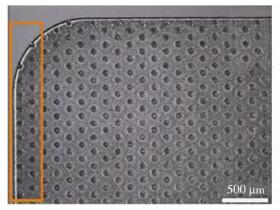
图 7 微凹坑型织构化刀具前刀面形貌
陶瓷刀具具有耐磨性好、硬度高及高温力学性能优良等优点,故其多用于加工难加工材料 ,通过将表面织构技术与陶瓷刀具相结合,可进一步提高其对难加工材料的切削性能。广东工业大学刘泽宇等通过激光技术在陶瓷刀具表面加工出微坑并进行摩擦磨损试验,研究结果表明与无织构陶瓷刀具相比,微织构陶瓷刀具可降低系统摩擦副表面的摩擦系数,微坑的存在可扩大刀具的散热面积,降低切削温度,同时微坑还能容纳一部分切屑,提高刀具的抗粘结性和抗磨损性,通过有限元分析发现无织构陶瓷刀具应力集中现象十分明显,而微织构陶瓷刀具的应力分布状况得到了改善,应力场分布较均匀。
2.3 纳米织构微纳复合织构阵列
单一型微织构刀具具有尺寸相对较大,减摩降磨性能好,在润滑条件下能有效降低切削温度等优点,但研究发现单一型微织构刀具在切削过程中极易出现二次切削现象,切屑很容易堵塞微织构。单一型纳米织构刀具尺寸较小,故其织构深度较小,刀具抗磨性能提高有限,减摩降磨作用时间也将有所减小。微纳复合织构阵列则综合了二者特点,其切削性能与二者相比有了一定程度的提高。
日本 Kawasegi N 等采用飞秒激光技术在硬质合金刀具表面加工出微米和纳米沟槽,在微量润滑条件下对铝合金进行切削试验,研究结果表明微纳米织构的存在能提高刀具耐磨性,降低切削过程中的切削力,与此同时,沟槽相对于切屑流出方向的不同会影响微织构刀具的切削性能,其中垂直于切 屑 流 出 方 向 的 微 织 构 刀 具 切 削 性 能 最 好 。Sugihara T 等针对铝合金深孔加工过程中切屑严重粘结等问题,同样采用飞秒激光加工技术在硬质合金刀具表面加工出微纳复合织构,在切削铝合金过程中发现微纳复合织构改善了刀-屑界面的润滑状态,减轻了刀具表面的切屑粘结现象。这为刀具减摩降磨研究提供了新的指导方向,在此基础上,他们设计了一种新型微纳复合阵列织构化刀
具,以降低刀具磨损和提高刀具耐用度。
山东大学邢佑强等采用飞秒激光技术在 Al2O3/Ti C 陶瓷刀具表面分别制备了平行于切削刃、垂直于切削刃及波浪状这些几何特征不同的微纳织构,其中波浪状微纳复合织构如图 8 所示,在干切条件下进行切削淬火钢试验,发现与普通刀具相比,微纳织构刀具不仅能减少刀具磨损,还能减小切削过程中的机械振动,从而得到更均匀的表面质量。由此推断在干切条件下微织构的存在仍有一定的积极作用,它仍可以收集切屑,减轻切削过程中刀具表面的“犁沟”现象,同时减小了刀-屑接触长度,这样可减小切屑在刀具表面的粘结。冯秀亭等结合纳米织构和微米织构的特点,采用 Nd:YAG 激光器分别加工了纳米织构和微/纳复合织构陶瓷刀具,并与微米织构刀具相对比,发现微/纳复合织构刀具减摩降磨效果最好,并用有限元分析方法进行了验证。在前期的切削过程中,纳米织构居于主导地位,经一段时间后,微米织构起主要作用,整个切削过程刀具抗磨性都得到加强。
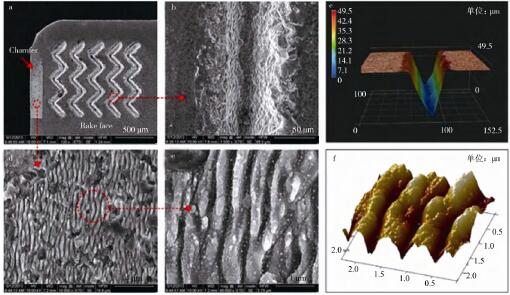
图 8 微纳复合织构刀具. (a)Al2O3/Ti C 陶瓷刀具表面 SEM 图; (b)微米织构 SEM 图; (c)微沟槽三维光学显微镜图; (d)和(e)纳米织构 SEM 图; (f)纳米沟槽 AFM 图
2.4 不同类型织构的减摩机理
在表面织构对刀具减摩机理的认识方面,目前研究认为刀具表面加工微织构后,将形成具有高强度、高硬度的晶层和残余压力层,这在一定程度上可提高刀具耐用度。另一方面,微织构刀具能减小刀-屑接触长度,同时其磨粒磨损现象减轻,从而减缓刀具磨损。不仅如此,在润滑条件下进行刀具切削试验时,刀-屑界面往往处于边界润滑状态,微织构此时其储存润滑液的功能,为刀-屑界面提供二次润滑,进一步减缓刀具磨损。
实际上,织构类型不同,刀-屑界面润滑膜状态也将有所差异,从而造成刀具的减摩降磨功能不同。不同类型织构对润滑状态的影响如图 9 所示。
通常来讲,切屑的切削力和剪切力促使润滑膜在刀-屑界面运动,此时润滑膜速度在垂直于切屑运动方向将形成速度梯度,平行于切屑运动方向的同一平面内润滑膜速度恒定。对单一织构类型而言,润滑膜运动基本稳定,由于刀-屑界面通常处于边界润滑状态,故刀具与切屑之间的润滑膜可能处于断续接触状态(如图 9a 和 9b)。对微凹坑织构而言,由于其润滑膜扁平且相对密闭,故在微凹坑周围可获得较高的润滑膜压力。而对微沟槽织构而言,微沟槽还将连通外界空气,此时在微沟槽内的主要承载区域润滑膜厚度最大,而微沟槽向有效承载区切削液的不断补充则会提高整体润滑膜压力。从接触面积来讲,当微凹坑与微沟槽的占空比(织构特征宽度与间距的比值)相同时,在相同切削条件下微凹坑织构化刀具的刀-屑接触长度要大于横向(与切屑运动方向垂直的方向)微沟槽织构化刀具,此时微凹坑织构化刀具摩擦副表面接触面积更大,故微凹坑织构化刀具的刀-屑粘结和刀具磨损现象仍较为严重。
从热传导方面来讲,微沟槽织构比微凹坑织构更有利于刀具的热传导,促进刀具表面与空气的对流,因此可更有效地降低切削温度。综上,与微凹坑织构化刀具相比,横向微沟槽织构化刀具在提高切削性能和刀具耐用度方面具有更佳的结果。
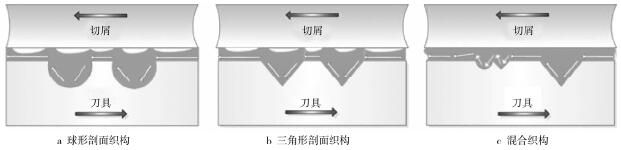
图 9 不同类型织构的润滑状态示意
对于混合织构而言,由于刀具表面织构类型的变化将降低润滑膜的稳定性,故此时沿垂直于切屑运动方向润滑膜速度将有所提高,而此方向润滑膜的速度将对边界润滑状态下润滑膜分布不均的状态起到改善作用。此外,微织构的作用相当于流体动压润滑轴承,流体润滑状态的改变将增大其径向力。结合圆弧织构与三角剖面织构的混合织构将改善界面的压力分布,从而起到提高润滑膜径向力的作用。润滑膜径向力的提高,可使刀-屑界面之间的接触区域减小,降低界面摩擦力,从而降低切削力、平均摩擦系数和刀具磨损。
3 、织构化自润滑刀具
在金属切削加工过程中,刀具表面摩擦剧烈,切削温度很高,到达一定程度后刀具会因磨损剧烈而失效。故为减轻切削过程中刀具磨损现象,目前普遍在切削加工过程中使用切削液。然而自润滑材料的出现为刀具减摩降磨提供了新的途径 。自润滑刀具在干切削条件下仍然能够实现自润滑加工,它主要是依靠刀具在高切削温度的条件下发生摩擦化学反应,此时刀具表面有润滑膜产生,从而实现其自润滑功能,除此之外,也可向刀具材料中添加固体润滑剂或表面离子注入等实现刀具自润滑功能,这样可以避免在切削过程中使用切削液,减少环境污染。
山东大学邓建新等将表面织构技术与自润滑刀具技术相结合,制备出微织构自润滑刀具,微织构内填充固体润滑剂,如图 10 所示。他们采用激光加工技术在硬质合金刀具前刀面加工出微织构,微织构内填有 Mo S2固体润滑剂,然后用此在干切削条件下进行淬火 45#钢的切削试验,试验结果表明与传统刀具相比,微织构自润滑刀具能够提高系统摩擦学性能,有效降低切削力,同时微织构的几何参数和分布区域也会影响刀具表面的摩擦学状况,微织构设计得当方能提高刀具的切削性能,减缓刀具磨损。
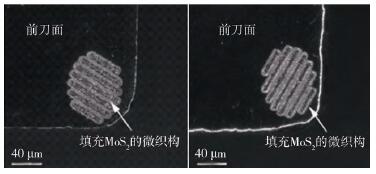
图 10 微织构自润滑刀具表面形貌
吴泽等同样通过激光技术在硬质合金刀具表面加工出椭圆形微沟槽刀具,其中微沟槽深度为 50 μm,宽度为 150 μm,微沟槽内还填充有固体润滑剂,由此进行 TC4 钛合金切削试验,发现与无织构刀具相比,微织构自润滑刀具能够改善刀-屑界面的润滑状态,还能显著地降低切削过程中的切削力和切削温度,从而提高刀具耐用度。连云崧等通过飞秒激光微细加工技术在硬质合金刀具前刀面加工出纳米织构自润滑刀具,并向织构内填充 WS2固体润滑剂,用传统刀具、纳米织构刀具、纳米织构自润滑刀具进行对比切削试验,研究结果表明与传统刀具相比,纳米织构刀具和纳米织构自润滑刀具可有效减小刀-屑界面的摩擦系数,减轻刀具的粘结现象并降低切削力和切削温度,而在二者之中纳米织构自润滑刀具切削性能要优于纳 米 织 构 刀 具 。 湘 潭 大 学 龙 远 强 等鉴 于0Cr18Ni9 奥氏体不锈钢的难切削特性,在硬质合金刀具前刀面加工出填有固体润滑剂的微织构,从而制备得到微织构自润滑刀具,并用此刀具进行0Cr18Ni9 奥氏体不锈钢切削试验,发现与无织构刀具相比,微织构自润滑刀具能显著降低主切削力和切削温度,其中主切削力降低了 8%~16%,切削温度降低了 15%~24%,切屑粘结现象也得到了一定程度的减轻。
表面织构技术与自润滑刀具技术相结合在刀具应用领域具有广阔的前景,但目前尚未明确在织构化自润滑刀具中微织构与刀具自润滑的减摩作用的主次性,有待进一步探讨研究,由此可为织构化自润滑刀具减摩机理提供指导理论方向。
4 、存在的问题
目前对微织构刀具的研究尚无系统的理论和试验论证,对微织构刀具织构参数设计和位置分布尚处于起步阶段,还需进一步的优化设计理论和模型,并用仿真分析和试验进行验证,进而优化刀具表面微织构的尺寸、分布位置和方式。其次目前对刀具表面织构的研究多为利用织构来减小刀-屑接触长度,实现织构的储油、储屑等功能,缺乏对切削介质运动状态的控制,而且因实际切削过程中刀-屑界面工况恶劣,现有微织构刀具的减摩功能会逐渐失效。
5 、结语
织构化刀具利用表面技术在刀具表面加工出织构,由此提高刀具的切削性能。国内外专家学者由此进行了大量的试验和分析,研究结果表明:织构化刀具可减小刀-屑接触长度,提高系统摩擦学性能,减缓刀具磨损并减轻切屑粘结现象,降低切削力和切削温度。鉴于高速加工在我国制造业中的基础地位和重要性及高速加工中刀具磨损现象极为严重,亟需开发新型刀具技术,提高刀具耐用度和工件加工质量,从而降低生产成本并提高生产效率。故织构化刀具成为如今刀具制造业的研究热点,在润滑条件下,织构化刀具表现了良好的切削性能,可有效提高刀具耐用度,对新型刀具技术的发展具有极为深远的意义。
投稿箱:
如果您有机床行业、企业相关新闻稿件发表,或进行资讯合作,欢迎联系本网编辑部, 邮箱:skjcsc@vip.sina.com
如果您有机床行业、企业相关新闻稿件发表,或进行资讯合作,欢迎联系本网编辑部, 邮箱:skjcsc@vip.sina.com
更多相关信息