轧机AGC伺服液压缸结构优化探讨
2018-4-2 来源:武汉科技大学 作者:朱兵,傅连东,黄科夫,湛从昌,高雨
摘要:针对我国某一钢厂的轧机AGC伺服液压缸出现的故障进行了分析,对出现伺服液压缸缸体底部裂损进行了详细的研究,并且用ANSYS对其进行了有限元分析,突破了常用的增大伺服液压缸底部圆弧半径等思维,提出了一种新的改进方案,即将缸体底部的圆弧变为倒角,适"-3调整倒角的尺寸,使得工作状态变得更加安全和可靠,分析了各个参数对最大应力的影响状况,并选择了最佳参数,使AGC液压缸处于较好的工作状况结构,优化后的结构应力明显减小,满足工作要求。
关键词:AGC伺服液压缸;有限元分析;最佳参数;结构优化
引言
随着机械自动化的快速发展,我国机械方向所需轧制板材精度的要求越来越高,提高轧机系统的性能是前提保障。轧机AGC伺服液压缸是轧机AGC伺服液压系统中的关键部件,它的性能直接影响了轧机AGC伺服系统的加工的钢材的质量。根据统计表明轧机AGC伺服液压缸缸底在油口部位最容易发生裂损。传统的加厚液压缸缸体缸筒、液压缸缸体底部和液压缸缸体底部倒圆角仅减小部分集中应力并没有从根本上解决液压缸缸体油口处的断裂的问题。例如,某钢厂使用的轧机AGC伺服液压缸缸体底部油口处发生断裂后,适当加厚液压缸缸体缸筒厚度和调整圆角后,在使用中仍会发生液压缸缸体底部油口处断裂。
针对上述现象本研究对轧机AGC液压缸缸体底部的油口部位进行倒直角并进行了ANSYS有限元分析优化,静态分析结果发现适当的调整倒角的高度和角度可以尽可能的减小油口处的集中应力,为改进轧机AGC伺服液压缸结构奠定了基础。
1、 AGC液压缸的工作原理
在大型钢厂中,轧制高精度的钢材需要由高精度的轧机AGC伺服液压系统对加工板材的动态特性和静态特性进行处理和监控。在轧机AGC伺服液压系统中主要工作元件是轧机AGC伺服液压缸,该缸由活塞、活塞杆、端盖、缸体、位移传感、密封圈和防尘圈等组成。图1为轧机AGC伺服液压缸结构示意图。当轧机AGC伺服液压系统对轧制厚度的控制时,为防止活塞的快速运动而撞击缸体,液压缸端盖设有缓冲结构。
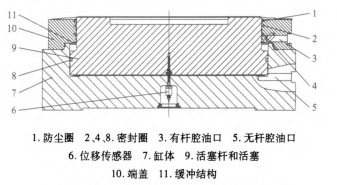
图1 轧机AGC伺候液压缸出现的故障分析
2、 轧机AGC伺服液压缸出现的故障分析
某钢厂轧机AGC伺服液压缸如图1所示。该液压缸结构为活塞式,液压缸活塞直径为西=1450 mm,液压缸缸底外直径D=1850 mm,液压缸缸底厚度s=215 mm,液压缸缸底与液压缸缸筒之间圆弧半径R=15 mm,设计工作压力23 MPa,测试压力30 MPa,设计寿命4年,液压缸缸底由900 mm宽的平面支撑。该液压缸在使用过程中,沿缸底与缸筒交界处上,以及在进出油口附近区域m现了大段裂纹.如图2所示
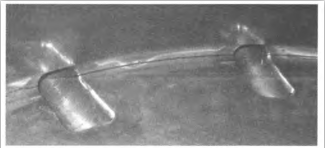
图2轧机AGC伺服液压缸缸底的无杆腔油口的裂损
针对这一现象对出原始方案进行了有ANSYS限元分析如图3,并分析了故障原因:当轧机工作时,轧机AGC伺服液压缸在控制厚度的过程中起主要执行作用。当轧机AGC伺服液压缸正常工作时,工作中产生的最大应力超过了缸体使用材料的疲劳强度;当工作中出现咬钢时,系统轧制力瞬间增加,使得轧机AGC伺服液压缸里面的油液压力瞬间升高,对液压缸缸底进行强烈的冲击;当工作中出现抛钢时,系统轧制力瞬间减小,轧机AGC伺服液压缸里面的油液压力瞬间下降,油口的压力瞬间减小,也会对液压缸缸底带来很大的冲击。在这样无数往复次的工作循环下,油压不断的对液压缸缸底进行冲击,油液的压力频繁冲击液压缸缸底油口处和缸底的连接处,在长时间的冲击将油口处的缸底部位直接损坏。
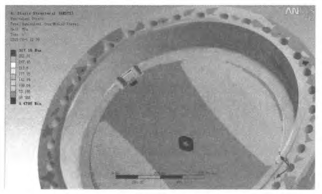
图3 最原始方案的等效应力图
在23 MPa工作压力下,由有限元分析结果图3可知油口最大应力为317.16 MPa,已超过该材料疲劳极限285.78 MPa。轧机AGC伺服液压缸是通过精加工而成,缸底与缸筒交界处及油口附近的应力集中及工作过程中频繁的冲击导致了此处出现大段裂纹。为了解决这种故障,设计者提出了一种改进方案:轧机AGC伺服液压缸缸体壁厚加50 mm、缸底厚度加50 mm。
此次改进是设计者根据经验得出的,但是没能解决问题。设计者又将底部圆弧半径改为20 mm,虽然减小了部分集中应力,但是没有将轧机AGC伺服液压缸改进到最佳状态。为了减小油口处的集中应力,本研究作者认为不一定需要把底部过度部分改为圆弧,可以改为倒角形式,调整一定的倒角高度和角度,可以使底部油口处的集中应力更进一步的减小,并且可以适当的减少液压缸的壁厚和缸底的厚度,从而节约成本和延长液压缸的使用寿命。
3、AGC伺服液压缸缸体的优化。
将轧机AGC伺服液压缸采用的材料是42 CrMo。从文献得42CrMo的屈服极限为939 MPa,抗拉强度1080 MPa,密度为7850 kg/m3,体积模量为175 GPa,剪切模量为80.769 GPa,尺寸因子为0.567,经计算得出该材料的疲劳极限为285.78 MPa。在20℃时其弹性模量为210 GPa,泊松比为0.3。在ANsYs/wORKBENCH中,对第一次的改进在23MPa的工作压力下进行了分析得到等效应力如图4,由结果可知轧机AGC伺服液压缸油口处的最大应力为258.13 MPa。
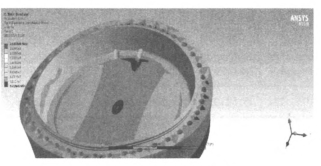
图4 第一次优化的等效应力图
在ANSYs/WORKBENCH中对该设计的最终改进方案:将轧机AGC伺服液压缸的缸筒增加50 mm、缸底的厚度增加50 mm和将缸底的圆弧部位改为20mm,对轧机AGC伺服液压缸的改进结构在液压压力为23 MPa下,工作分析得到等效应力分布如图5,由结果可知轧机AGC伺服液压缸油口处的最大应力为183.2 MPa。
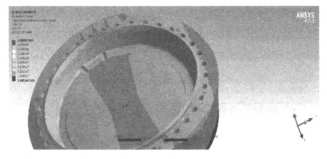
图5 设计者改进最终方案的等效应力
在ANSYS/WORKBENCH中对于轧机AGC伺服液压缸缸体底部倒圆角的模型进行优化,设置轧机AGC伺服液压缸的3个参数:
(1)液压缸缸筒加厚范围25 mm到150 mm;
(2)底部厚度增加20 mm到60 ITlln;
(3)圆弧半径10 mm到30 mm。
以下分别为液压缸缸体缸筒加厚大小、液压缸缸体底部增加的厚度、液压缸缸体底部圆弧半径对油口处最大集中应力的影响,分别如图6一图8所示。
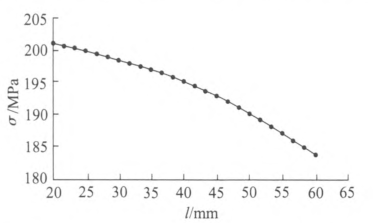
图6 红筒加厚d对油口最大集中应力的影响
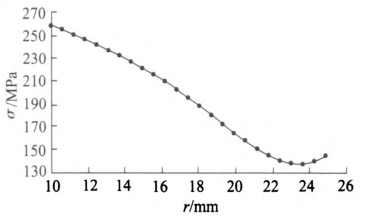
图7 底部增加厚度L对油口集中应力的影响
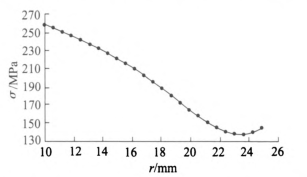
图8 圆弧半径r对油口最大集中应力口的影响
经过分析和筛选得出了以下优解如表1。
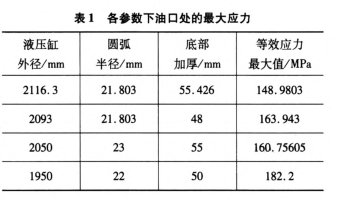
在ANsYS/wORKBENCH中对该轧机AGC伺服液压缸的结构尺寸进行了优化,设置AGC液压缸的4个参数:
(1)液压缸缸体缸筒加厚范围25 mm到150 mm;
(2)液压缸缸体底部厚度增加20 mm到60 mm;
(3)液压缸缸体底部倒角的高度15 inln到25 mm;
(4)液压缸缸体底部倒角的度数30。到60。
以下分别为液压缸缸体缸筒加厚大小、液压缸缸体底部增加的厚度、液压缸缸体底部倒角的高度、液压缸缸体底部倒角的度数对油口处最大集中应力的影响,分别如图9~图12所示。
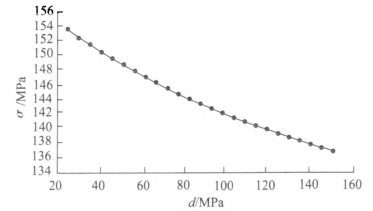
图9 缸筒加厚d对油口最大集中应力的影响
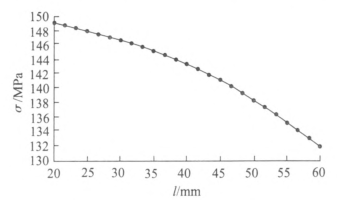
图10 底部增加厚度l对有口最大集中力的影响
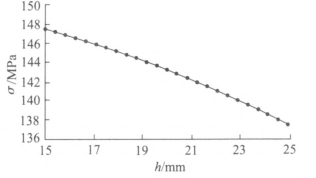
图11 倾角高度h对油口最大集中应力的影响
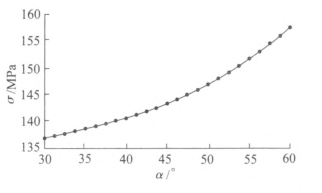
图12 角度数d对油口最大集中应力的影响
根据以上数据所得最优解,故将轧机AGC伺服液压缸缸体尺寸圆整后取值:液压缸外径1950 mm,底部加厚50 mm,倒角高度25 mm,倒角高度35 o,将此优解ANSYS/w0RKBENCH软件中在工作压力为23 MPa下进行分析,得到等效应力为,如图13,由结果可知轧机AGC伺服液压缸油口处的最大应力为132.03 MPa.
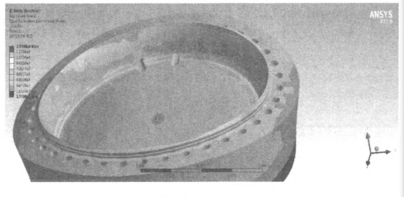
图13 分析和筛选的最佳尺寸有限元分析
将上述设计师改进的结果进行对比,如表3所示。
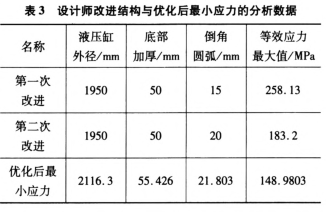
本次最佳优化结果,如表4所示。
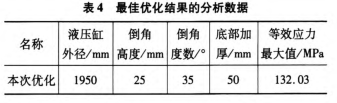
通过此次优化的结果和设计师的改进对比可以看出:此次优化并木有增加材料而增加成本,仅仅只是突破了传统的倒圆弧的方式,将圆弧的方式改为倒角的方式,并适当的调整倒角的倒角高度和倒角角度,大大的降低了油口处的集中应力,从而可以大大的了提升液压缸的使用寿命。
此次优化的结果和液压缸缸体底部为圆弧的优化结果对比:液压缸缸体底部倒角为圆弧的优化,液压缸缸体缸筒加厚133.15 mm,液压缸缸体底部加厚55.426 mm,液压缸缸体圆弧倒角为21.8030时,液压缸缸体的最大应力值达到了148.9803 MPa,而此次优化方案,只需将液压缸缸体缸筒加厚50 mm,液压缸缸体底部加厚50mm,液压缸缸体倒角高度25 mm,液压缸缸体倒角角度35。,即可将最大应力降低!91]132.03 MPa,不仅节约了材料,而且还降低了液压缸缸体的最大应力。
4、结论
以某钢厂使用的轧机AGC伺服液压缸为研究对象,综合分析了液压缸缸壁厚度、液压缸缸体底部厚度、液压缸缸体底部倒角高度和液压缸缸体底部倒角角度对液压缸缸体集中应力的影响。并通过选择合理的参数确定了液压缸最终优化方案。为了检验优化后液压缸工作状况,对改进后的液压缸进行23 MPa液压油工作的仿真计算,并与前面的优化方案进行了对比,结果证明改进后的轧机AGC伺服液压缸的工作性能得到了明显的改善,改进后的液压缸缸体油口出的集中应力的问题大大消除,达到了优化的目的。
投稿箱:
如果您有机床行业、企业相关新闻稿件发表,或进行资讯合作,欢迎联系本网编辑部, 邮箱:skjcsc@vip.sina.com
如果您有机床行业、企业相关新闻稿件发表,或进行资讯合作,欢迎联系本网编辑部, 邮箱:skjcsc@vip.sina.com
更多相关信息