滚珠丝杠的静压结构改造及其流场数值模拟分析
2017-7-21 来源:北京工业大学机械工程与应用电子技术学院 作者:涂承媛 邢欢欢 王新华 李迎超 孙 肖
摘 要: 为了提高废旧机床的加工精度,提出在现有丝杠的基础上利用注塑成型技术实现静压丝杠副的成型方法。基于液体静压向心轴承的设计理论,设计了静压螺母的关键结构参数。运用 Pro/E 三维成型技术建立了静压丝杠副三维模型,并采用 Flo EFD 流体分析软件对静压丝杠螺母的内部流场进行仿真分析,得出了不同负载压力下静压腔、封油边和回油槽内液体压力分布以及丝杠受到的液压作用力。分析表明: 静压腔内液体压力分布均匀; 在负载作用下,液体静压螺母内部上方静压腔内液体压力大于下方静压腔内液体的压力; 丝杠表面受到均匀的液体作用力、丝杠与螺母之间通过均匀的油膜间接接触。因此,应用油膜的均化误差效应可以降低丝杠表面精度的要求。
关键词: 滚珠丝杠; 液体静压丝杠; 改造; CFD; 流场分析
0.引言
随着科技的发展,机床加工精度、自动化及信息化水平的不断提高,机床更新换代速度不断加快,导致机床废弃量不断增加。资料显示,我国役龄 10 年以上的旧机床超过 200 万台,80% 的在役工程机械超过保质[1]; 随着客户对机床加工精度、自动化及信息化水平等性能要求的提高,仅仅将退役机床恢复精度已不能满足客户需求,因而,通过各类高新技术对再制造机床功能及性能进行提升具有重大意义[2]。目前,机床再制造在国外已成为一个新兴产业,例如,MTB 公司将一台普通机床再制造为 5 个轴均由数控系统控制的机床; TMB 公司去掉了原机床用来完成扩程运动的整个机械传动系统,在摇臂轴上安装一个扭矩电机直接控制上/下冲程运动,实现了上下冲程过程中的独立的进给率[3]。从而体现出机床的精化改造与传统改造的本质区别: 充分运用动静压技术、电主轴技术、机床复合化技术、现代传感技术以及先进的制造技术、制造方法提高废旧机床的加工精度,使改造后的机床功能更强、性能指标更优,实现资源循环利用和已有机床跨越式提升。普通废旧机床的进给部件一般采用滑动导轨与滚珠丝杠,然而,滚珠丝杠存在承载能力较低、加工成本高、不能自锁等缺点。与滚珠丝杠相比,液体静压丝杠螺母具有摩擦阻力小; 使用寿命长,能长期保持精度; 传动精度高,丝杠与螺母无空程间隙,重复定位精度高; 传动平稳; 低速传动不爬行等优点[4]。为改善废旧机床的工作特性,提高加工精度,对废旧机床进行再制造与工作特性分析具有重大意义。
1.液体静压丝杠副的结构与工作原理
流体薄膜润滑[5,6]是通过完整的流体薄膜将两运动表面完全隔离,从而起到减少摩擦作用的一种润滑技术。结合流体静压润滑技术与液压气动技术设计的静压轴承、静压导轨等部件在各种精密机械、仪器仪表中得到了广泛的应用。在 Wil-liam W. Pflager[7]的专利中提及了一种改进型流体静压丝杠螺母组件,但是该方法对于以原有丝杠为基础加工制造静压螺母的成本比较高,并且很难实现规模化生产。因此,提出了一种基于现有丝杠利用注塑成型技术实现静压丝杠副的成型方法,该方法具有加工工艺简单等特点,能够加工与任意丝杠配合的静压螺母,简化了在现有丝杠基础上螺母螺纹的加工工艺。
液体静压丝杠副由静压螺母、丝杠、节流器、供油系统、润滑油 5 部分组成[8,9]。静压螺母内含有静压腔、回油槽、封油边、进出油口等结构。静压腔和封油边的尺寸决定了静压丝杠副的承载能力; 封油边和轴径之间的间隙很小,限制静压腔内液压油的外流,起 “憋压” 作用,以保证流入静压腔内液压油的压力平稳; 封油边处螺纹与丝杠螺纹相互啮合实现丝杠与螺母运动的相互传递,螺母螺纹与丝杠螺纹的啮合度决定了静压丝杠的传动精度。运用注塑成型技术加工螺母内腔的螺纹与直接车削螺母内螺纹具有配合误差低、加工误差低、加工工艺简单、成本低等优点。
静压丝杠螺母加工步骤:
1) 按设计要求加工螺母套筒;
2) 以经过简单修复处理的废旧丝杠作为静压丝杠副的型芯,选择高强度自润滑的耐磨涂层材料作为注塑材料,加工注塑出具有与原丝杠完全啮合螺纹的螺母内腔;
3) 按照结构参数加工静压螺母的静压腔、回油槽、封油边、进出油口等结构。静压丝杠副的结构如图 1 所示。
根据已知丝杠的结构参数设计静压螺母的内腔结构,包括静压腔、封油边以及进、出油孔的尺寸等。参考静压向心轴承的设计理论,确定静压丝杠螺母的关键结构参数: 静压腔单元角度 2θ、静压腔深度 r2- r1、螺母宽度 B 等。
油膜厚度不均匀修正系数[4]
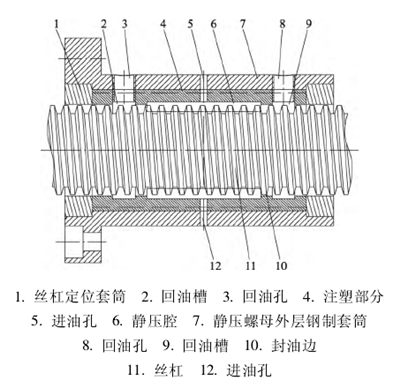
图 1 静压丝杠副结构图
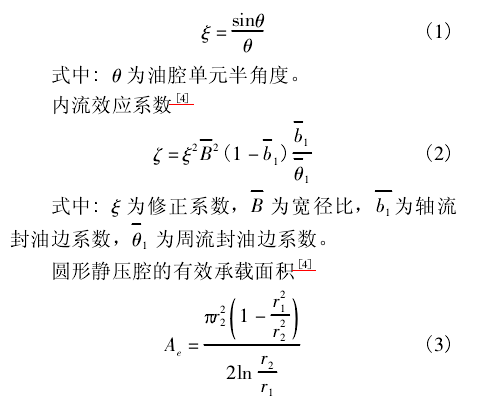
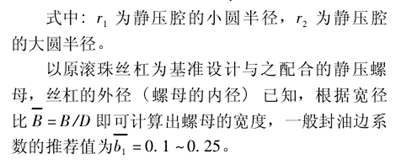
2.计算模型与仿真方法
设计静压螺母的关键在于设计合理的静压腔和封油边,静压腔的作用是扩大有效承载面积并减小摩擦面积,围绕静压腔的凸边称之为封油边。压力油经过节流器产生一定的压力降后流入油腔,再经过油腔四周的封油边之后流到周向回油槽,最后经液压回路回流到油箱。为了分析静压腔、封油边以及回油槽内部流场特性,将静压丝杠副简化为如图 2 所示的模型。
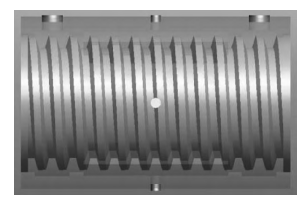
图 2 静压丝杠副模型

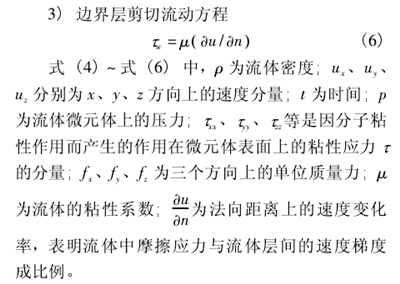
采用 Flo EFD 流体力学分析软件对静压丝杠副进行数值计算,模拟过程的基本设置: 选用 inter-nal 分析类型; 根据所建系统模型的内部封闭流道自动划分网格; 最小流动通道值设置为 0. 8 mm;以油作为工作流体,流体设置为不可压缩流动流体; 不考虑固体内部的导热情况,采用 adiabaticwall 定义壁面为完全绝热; 边界条件定义为质量流入口条件和环境压力出口条件。
3.计算结果与分析
3. 1 静压螺母腔内流场压力分布
以图 2 所示三维结构作为静压丝杠副的流体分析模型,初始化边界条件定义为入口质量流为0. 5 kg / s、出口压力为环境压力 0. 1 MPa,对静压丝杠副的内部流场特性进行分析。图 3 所示为静压丝杠副受到液压油作用时不同方向丝杠表面受到的压力分布云图,可以看出:在进油口处丝杠受到的压力相对较大; 在螺母的静压腔和封油边处受到的压力基本相同,并且比较稳定,没有出现压力急剧变化的现象; 在回油槽处受到的压力相对较小。
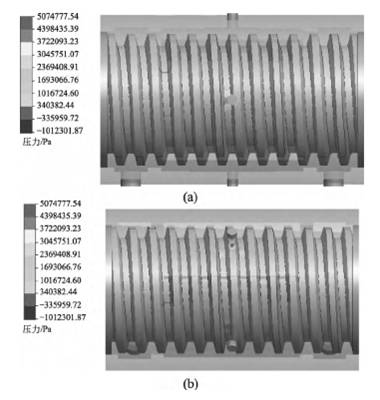
图 3 静压丝杠副内丝杠表面云图
图 4 所示为静压丝杠副不同方向腔内流体与螺母内壁接触处压力分布云图,可以看出: 液压油与螺母内壁接触完整,即没有出现丝杠螺纹与螺母螺纹直接接触而无液压油的现象; 液压油的压力分布均匀,静压腔和封油边处压力高于回油槽处压力,回油孔处压力值最低且压力值基本等于环境压力,这与初始设置是相符合的。
3. 2 不同压力下静压丝杠副的特性分析
丝杠在机床中的作用是将旋转运动转化为直线运动。丝杠以一端固定、另一端支承的方式安装时,固定端轴承同时承受轴向力和径向力,支承端只承受径向力,而且能作微量的轴向浮动,可以避免或减少丝杠因自重而出现的弯曲。因此,
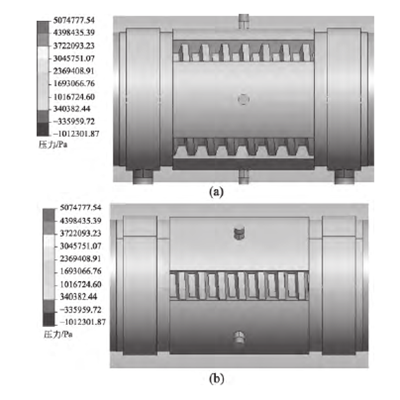
图 4 螺母腔内流体表面云图
不考虑螺母内丝杠的弯曲变形。通过仿真结果比较空载和负载下静压丝杠副的静压腔、封油边内压力分布。
3. 2. 1 静压腔、封油边内压力分布
通过分析对比不同载荷压力下静压丝杠副的仿真结果,从而了解静压丝杠的结构特性。图 5a所示为空载时静压丝杠螺母的静压腔内压力分布云图,图 5b 负载时静压腔内压力分布云图。从图5a 可以看出,上、下静压腔内压力大小相同,在空载时静压腔内压力平衡,丝杠处于稳定状态。从图 5b 可以看出,上、下静压腔内压力大小不相同,上油腔的压力大于下油腔的压力,这是因为螺母受到负载作用时会向下偏移,然而丝杠是固定的,这样使得上静压腔的体积减小,丝杠与螺母之间的液压油的刚度不是无穷大的,因此上静压腔内的液压油会产生微量的压缩,液压油的压力增加用以抵抗增加的负载作用力; 与此同时,下静压腔的体积增大,下静压腔内液压油的压力不变或者有微弱的减小,使静压螺母在新的位置到达受力平衡,此时静压螺母腔内液压油的压力也达到新的平衡,即此时上静压腔内液压油压力大于下静压腔内液压油的压力。
图 5 中压力腔内压力分布均匀,只有在进油孔处出现压力集中现象。在螺纹周围没有出现流体压力集中的现象,验证了液压油膜具有均化误差的作用,可以忽略丝杠的微小误差。静压丝杠的封油边是由螺母与丝杠相互啮合的螺纹间隙形成的,该处螺纹主要有两个作用:一是作为传动介质在丝杠转动时实现螺母的移动;二是作为螺纹啮合处封油边,限制液压油的外流,起到 “憋压”的作用。图 6a 所示为空载时封油边内压力分布云图,图 6b 所示为负载时封油边内压力分布云图。

图 5 静压丝杠的静压腔内压力分布云图
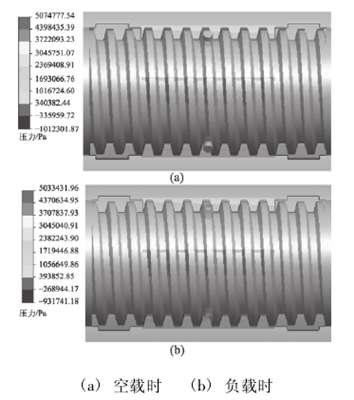
图 6 封油边内压力分布云图
3. 2. 2 静压螺母腔内流体流向分布
图 7a 所示为空载时静压丝杠副内腔流体的迹线图,图 7b 所示为负载下静压丝杠副内腔流体的迹线图。从图中可以看出,进油孔、静压腔内液压油的压力高,回油槽里的液压油的压力低,有利于由进油孔进入的液压油从回油孔流回油路系统。在两个静压腔之间的封油边内有极少部分液压油流过,即在封油边内形成了液压油膜,丝杠螺纹与螺母螺纹之间的油膜支承减小了摩擦力。图 7a、图 7b 不同之处在于: 图 7a 中上下静压腔内流体压力相同; 图 7b 中下方静压腔的流体压力小于上方静压腔内流体的压力,这是因为静压丝杠在承受负载时螺母向下微量偏移使上方静压腔的体积减小、下方静压腔的体积增大,上方静压腔内液压油的压力大于下方静压腔内液压油的压力。
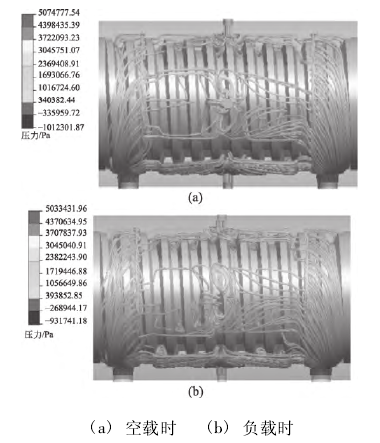
图 7 静压丝杠内腔流体的迹线图
3. 2. 3 不同负载下静压螺母腔内压力
在给定进出口压力边界条件下,静压丝杠副腔内的液压油压力分布与负载大小有关,负载越大,上方静压腔与下方静压腔内液体压力值的差越大。图 8 所示为静压丝杠的剖视图,线 1、2 均是在丝杠左侧密封处至右侧密封处的连线且不与丝杠和螺母接触,用 Flo EFD 软件计算这两条线上各点处的液压油压力,得出图 9 所示的压力分布曲线。从图 9 中可以看出,静压螺母内液体压力值以进油孔为中心对称分布,液压油压力以进油孔为中心向两端逐级递减; 液体压力值最低点出现在回油槽内,回油槽内液体压力波动较大,液体压力值在封油边迅速减小,静压腔内压力值基本处于平稳状态。空载时,线 1、线 2 处液压油的压力曲线基本重合,线 1、线 2 处液压油的压力基本相同,静压腔的液体压力值稳定在 1. 8 MPa 左右,回油槽液体压力最小值在 1 MPa 左右; 有负载时,线 1 处液压油的压力大于线 2 处液压油压力,并且线 1 处液压油压力大于无负载下相对应位置的液体压力值; 线 1 与线 2 处液体压力曲线趋势略有不同,在回油槽内线 1 处液体压力稳定在1. 6 MPa 左右,而线 2 处波动较大,因为线 1 处距离回油孔较远,上方静压腔内液压油经周向封油边进入回油槽,刚进入回油槽的液压油因距离回油孔较远,液压油压力降低得较慢,并且回油槽内存在压力差有利于液压油的回流。
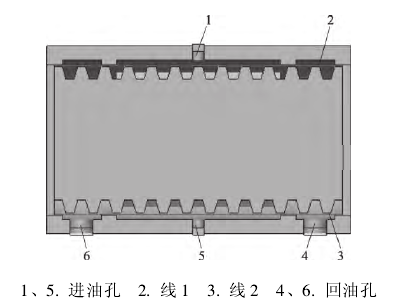
图 8 静压丝杠剖视图
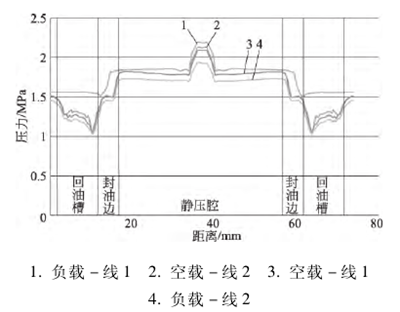
图 9 不同负载下静压螺母腔内液体压力分布曲线
4.结论
1) 基于废旧机床的再制造理论提出了一种将滚珠丝杠副改造成液体静压丝杠螺母副的方法,并运用静压向心轴承的计算公式,建立了静压丝杠螺母副的三维模型。以丝杠为型芯注塑螺母内螺纹,然后车削加工静压腔等内部结构的方法加工螺母,该成型方法简单,资源利用率高。、
2) 静压螺母的静压腔内液压油压力分布均匀; 在封油边内,液压油压力由静压腔至回油槽方向递减; 静压螺母腔内液压油压力以进油孔为中心左右对称分布; 静压螺母与丝杠之间通过液压油膜间接接触,因此,可以利用油膜的误差均化效应降低丝杠的表面粗糙度要求。
3) 在负载作用下,静压丝杠螺母内液体压力特性良好,油膜完整,并没有出现螺母螺纹与丝杠螺纹直接接触的情况,螺母偏移量小; 运用螺母微小的偏移量调整上、下静压腔内液体压力,使其处于新的稳定状态。
投稿箱:
如果您有机床行业、企业相关新闻稿件发表,或进行资讯合作,欢迎联系本网编辑部, 邮箱:skjcsc@vip.sina.com
如果您有机床行业、企业相关新闻稿件发表,或进行资讯合作,欢迎联系本网编辑部, 邮箱:skjcsc@vip.sina.com
更多相关信息