变速箱齿座加工工艺优化
2019-6-20 来源:东风(十堰)发动机部件有限公司 作者:房远奇
摘要: 针对变速箱齿座加工中存在的缺陷,通过改善内孔加工方法、攻克质量风险点及优化加工参数等改进措施,达到了优化工艺、解决问题的目的。
我公司目前加工的零件以铸铁件为主。若根据现有的加工条件来完成相对高精度的钢件加工,无法在有效的成本控制范围内来完成相应的生产。依照现有的刀具、夹具对铸钢材质的齿座进行加工验证后,无论是加工节拍、加工质量,还是工艺流程的繁复程度,都不能满足低成本的要求。
通过对内孔孔径进行改善,对质量风险点进行攻关,对加工参数进行优化等一系列措施,达到了工艺流程的优化,降低了生产成本,提高了产品质量。
1. 产品结构和技术要求
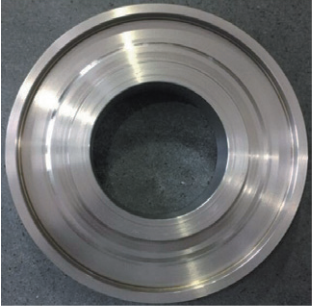
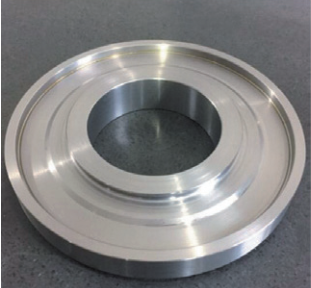
图 1 产品结构
变速箱齿座零件为盘类结构(见图1),材料为铸钢(DFS5218SH2),硬度为150~190HBW。产品技术要求如图2所示。
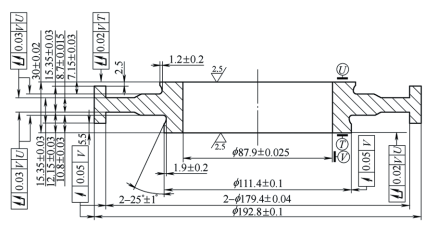
图 2 产品技术要求
2. 加工工艺
考虑到零件尺寸链关系比较复杂,以及尺寸精度大部分都在0.05mm以内,在试加工阶段采用的是粗、精工序分开加工完成,具体流程如表1所示。
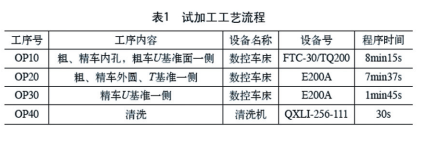
3. 孔径加工变形问题
零件中心孔在OP10序中完成,定位方式是基准T面定位和夹紧外圆夹紧(见图3)。中心孔孔径为φ(87.9±0.025)mm,孔径深度32.7mm。在实际加工过程中发现孔径存在图1产品结构喇叭口的问题。进刀口直径与出刀口直径相差0.01~0.04mm,尺寸不稳定。

图 3 OP10 定位方式
经分析,主要可能存在如下问题:①夹紧变形。卡爪夹紧压力导致孔径存在应力消除后的变化,或者外圆夹紧位置偏低导致零件抬起。②刀具让刀。刀柄直径过小导致零件在切削时让刀。③余量过大。精车余量偏大导致加工时让刀。④应力未消除。钢件零件自身材质偏软,加工后,零件因为应力消失而部分还原。针对这些问题,采取了如下改善措施:
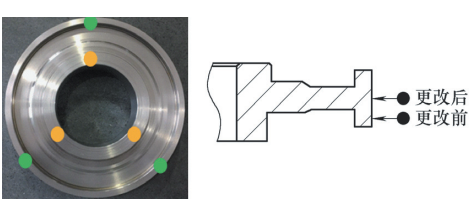
图 4 定位点、压紧点更改位置
(1)更改定位点和夹紧点(见图4)。首先,更改T基准面上的定位点,增加支撑点之间的距离,从而增加支撑的稳定性;其次,更改卡爪夹紧点的位置,将卡爪从外圆的靠边位置更改到中间位置,以便使零件的受力是在零件主体上;最后,对卡爪压力作出适当调整。
(2)将目前使用的φ25mm刀杆更换成φ30mm刀杆,并将刀片换成钢件专用刀片(刀片的后角更大),更有利于切屑的切断和排出。
(3)变更余量试验中,发现铸钢件不同于铸铁件的加工,不是精车余量越小越好。钢件精车余量越小,零件表面外观质量反而越差,存在无规则的花纹。虽然尺寸没有什么影响,但是外观很差。多次验证后发现,将精车余量控制在0.15~0.25mm为最佳。最后以满足质量为前提,将精车余量确定为0.2mm,从而放弃在精车余量上的再次变动。
(4)在上述三点改善措施均完成之后,进行连续性的小批量验证。先采集加工后的数据,然后将零件进行时效处理,之后再复测采集数据。依照前后两次采集的数据进行对比分析,发现以下两点:①喇叭口现象依然存在。②进出口尺寸相对稳定,有一定的规律性,而不再是杂乱无章。
进出口直径相差均值为0.015mm。根据以上分析和试验,在加工稳定的情况下,从程序上进行修改,使出口直径比进口直径大0.015mm。后续试验证明,该方法不仅满足了孔径的要求,而且还通过了CPK大于1.33的验证(见图5)。
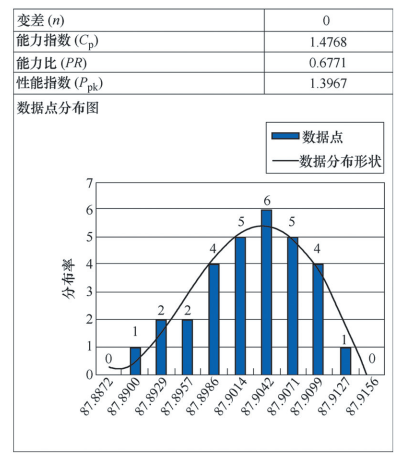
图 5 数据点分布及过程能力值
4. 清根问题
根据图样要求,零件有4处需要清根,而且相关尺寸控制也比较严格。
四处清根部分,最大加工余量1.9mm,最小加工余量0.5mm。根据图样要求以及机床刀位的控制,A、B两处只能选用主偏角>90°、副偏角>25°的车刀,C、D两处只能选用主偏角>112°、副偏角>0°的车刀。
在实际加工中,只有C、D两处刀具能够走轨迹一次加工成形。而A、B两处主偏角过大,理论上一次切削量不能太大,否则会存在崩刃的风险。实际加工验证存在崩刃、缠屑、“噎刀”和外观不良等诸多问题,只能采取分量多次加工(见图6)。后续加工验证,虽然轨迹走刀加工出了轮廓,但在轨迹接口的位置仍然存在一个目测可视的台阶(见图6左侧黑点处),无法步判定台阶与切屑排除不及时有关。经过多次试验验证和改良, 将等量切削的余量改为由大变小地进行切削, 使刀具在切削轨迹将近完成时, 切屑量减少而使切屑崩断。 最终完美地解决了问题。
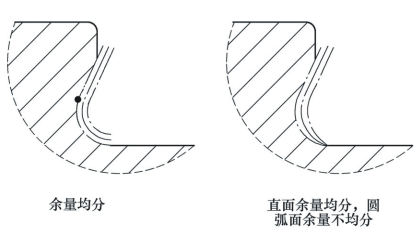
图 6 走刀轨迹变更对比
5. 加工参数优化
在样件试制阶段, 虽然已经参考现有的刀具和刀具加工参数经验, 也采用了一部分钢件专用刀具, 但是在实际生产中, 仍然存在切屑缠绕严重(见图 7b) 、 换刀频次偏低以及零件表面外观差(见图 7a) 等诸多问题。 而且加工时间(见表 1)始终无法再次提升。
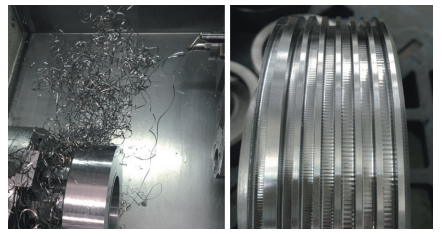
图7 b 图7a
在无法满足厂家指定成本和产能输出的情况下, 对刀具进行了更换, 对加工参数进行了修改。加工参数和程序优化后, 零件表面和断屑得到了很好的改善。 同时换刀周期也有明显的改善。对参数进行更改(见表 2) 后, 缠绕切屑变成了 3~5mm 的卷状切屑且自然断裂, 零件表面不规则光亮带也消失了。
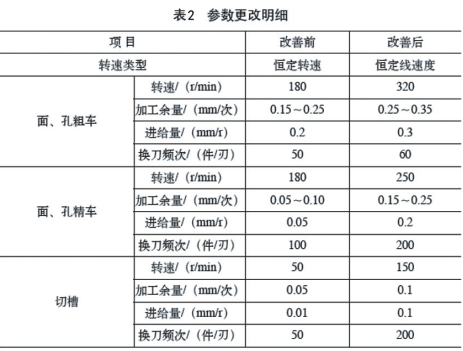
6. 工艺流程优化
通过以上改进措施, 提高了产品质量, 且产品质量稳定, 加工效率得到了提升, 最终根据改图 6 走刀轨迹变更对比善后的实际情况, 对工艺流程重新进行了布置和规划, 避免了部分零件多次定位造成的磕碰以及工序不必要的加长。 具体的工序变更情况如表 3所示。
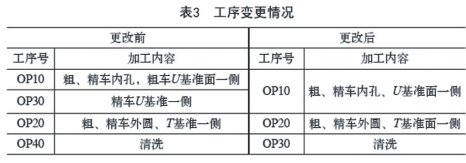
7. 工艺优化效果
在完成孔径变形、 清根缠屑外观不良、 刀具及参数提速不明显、 工艺优化等几个问题的整改和改善之后, 对齿座的质量、 工艺节拍和成本等有了一定的控制和优化, 减少了该零件的制造成本, 从而以更优的质量和市场价格来面对市场的需求和变化。
8. 结语
从开始调试到中期各种问题点的解决, 到后期的工艺流程优化, 一环扣一环。 初期问题的及时发现, 中期问题的及时改善, 后期工艺的及时优化、 固化, 都为齿座加工质量的成功改善提供了动力。
工艺的优化都是在市场需求情况下一步步地发现、 改善、 提升、 优化、 再发现……, 处于不断循环之中。 只有不停地改善提升, 才能更好地适应市场的需求和冲击, 才能在未来的市场中站稳脚跟。
投稿箱:
如果您有机床行业、企业相关新闻稿件发表,或进行资讯合作,欢迎联系本网编辑部, 邮箱:skjcsc@vip.sina.com
如果您有机床行业、企业相关新闻稿件发表,或进行资讯合作,欢迎联系本网编辑部, 邮箱:skjcsc@vip.sina.com