叶轮加工中心床身动态特性分析与优化
2018-1-18 来源: 北京信息科技大学 机电工程学院 作者:王 能,钟建琳
摘要: 叶轮是航空发动机的重要组成部分,需要具有高的加工精度和质量。以某工厂生产的航空发动机叶轮专用加工中心床身为研究对象,采用有限元方法分析其动态特性。根据床身的固有频率和模态振型找出其薄弱环节,针对床身的薄弱环节提出相对的优化改进意见,以改善床身的动态特性,并通过模态试验验证优化的合理性和可行性,为以后的设计提供了一定的参考。
关键词: 固有频率; 加工中心; 动态性能; 模态试验
0 、引言
随着科学技术的发展,航空制造业的先进性成为了影响国家国际地位的重要标志之一。
针对航空发动机叶轮的特点,某单位自主研发了航空发动机叶轮专用生产设备。根据叶轮的加工工艺特点,要求机床具有高加速度、高精度、高刚度、大扭矩的五轴五联动的特性。
提高制造设备的性能,保证叶轮的加工质量的主要手段之一就是机床的动态特性研究[1-3]。
目前,国内、外对叶轮制造进行了大量的研究,主要包括以下三个方面:
①运用计算机辅助手段对叶轮进行多学科优化设计;
②优化叶轮生产过程中的加工工艺,选取适当的加工参数和方法;
③提高叶轮制造设备的性能,保证其加工质量。
其中,提高制造装备研究的主要手段之一就是机床动态特性研究。
本文即从改善制造装备入手,通过应用 ANSYS Workbench 软件对某工厂自主研发的航空发动机叶轮专用生产设备的主要结构进行分析和优化来提高机床的动态特性,改善
叶轮的加工质量。
最后通过模态试验验证合理的优化设计,不但提高了本台机床的性能,为今后机床结构的设计尤其是主要受力部位设计也提供了一定的参考。床身是高速、高精五轴联动铣削加工中心的关键部件,其动态性能直接影响到整个加工中心的加工精度、抗振性和稳定性,同时,机床的床身承载了机床的所有运动部件,也是决定机床刚度的重要环节。
因此运用计算机辅助软件对床身结构进行分析,观察床身结构在各阶模态下的振型和固有频率,找出其薄弱环节并进行合理的优化对改善机床整体的动态性能具有很大的意义[4-5]。
1 、床身结构特点
叶轮是由多个薄且为自由曲面的叶片构成,其技术要求为: 叶片型面轮廓度为 0. 1,直径范围 200 ~500,叶片前后缘尺寸最小为 R0. 1 ~ R0. 15mm,粗糙
度 Ra0. 8。采用钛合金 TC4、高温镍基合金 GH4169 材料,如图 1 所示。
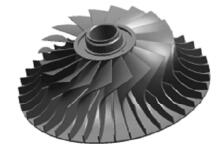
图 1 叶轮
叶轮加工中心由床身、Y 轴滑座、X 轴滑座、主轴箱、摆转台等关键部件组成,其模型如图 2 所示。与床身直接接触的结构为 X 轴滑座和摆转台左、右两箱体。其中,X 轴滑座通过滑块-导轨结构与床身接触;摆转台的左、右两箱体则通过螺栓直接固定在床身上。
床身的材料是 QT500,查阅文献[6]可知,该材料泊松比为 0. 275,弹性模量为 169GPa,密度为 7100kg /m3。
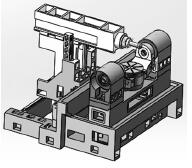
图 2 叶轮加工中心模型
2 、床身有限元分析
2. 1 床身优化前模态分析
利用三维建模软件去除对分析无影响的倒角、小孔( 包括地脚螺栓安装孔、导轨安装孔等) ,以减少计算量,缩短计算时间。由于实际试验状况下,床身是 6个橡胶垫块着地,故在橡胶垫块的底面添加固定约束,图 3 中的蓝色区域为橡胶垫块与地面接触位置,查阅文献[6]可知,橡胶垫块材料的泊松比为 0. 49,弹性模量为 6. 1MPa,密度为
1000kg /m3。
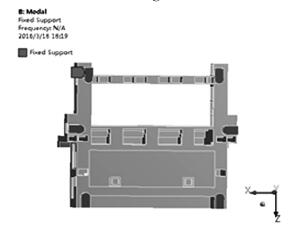
图 3 床身施加约束
提取床身的前 3 阶模态,其固有频率如表 1 所示,振型如图 4 所示。
表 1 床身优化前模态分析结果
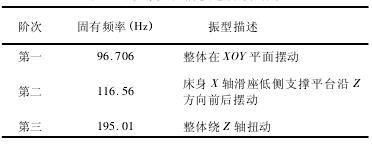
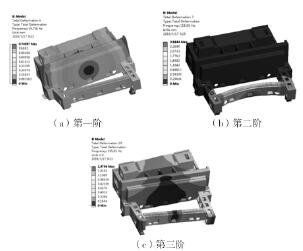
图 4 床身前 3 阶振型图
从前 3 阶振型图可以看出,床身的 X 轴滑座低侧支撑平台的刚度较弱,最大的振幅发生在第二阶模态,达到了 2. 6644mm,由于床身的最大变形处支撑 X 轴滑座,因此床身的振动会直接传递到 X 轴滑座上,进一步传递到 Y 轴滑座与主轴箱上,从而引起刀具的振动,直接影响工件的加工精度和表面质量。
因此,对床身进行结构优化改进,提高床身的刚度,改善床身的动态特性,进而提高整机的加工精度和抗振性。
2. 2 床身优化后模态分析
结合床身的仿真结果和整机装配关系可知,床身变形主要集中在 X 轴滑座作用位置。考虑到床身质量对动态特性的影响,在床身与 X 轴滑座接触位置设计成回型筋板结的同时,通过填充两侧支撑板来提高床身刚度,以及平衡床身质量,优化结果如图 5 所示。
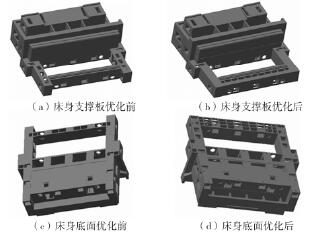
图 5 模型优化前后对比
对优化后的床身结构进行模态分析,其处理方式与优化前保持完全一致,提取床身的前 3 阶模态,其固频率如表 2 所示,振型如图 6 所示。
表 2 床身优化后模态分析结果
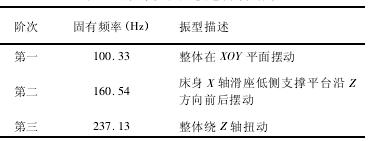
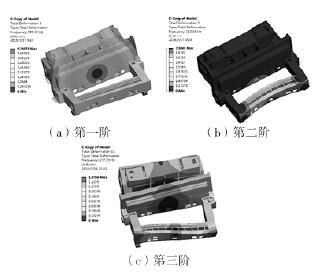
图 6 床身前 3 阶振型图
由频率和振型图可知,优化后的床身模型最大变形仍出现在 X 轴滑座低侧支撑平台处,但各阶最大变形量与优化之前相比之下均减少了,其优化前后的结果对比如表
3 所示。
表 3 床身优化前、后的结果对比
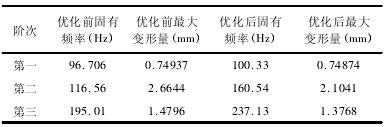
由表 3 可知,床身前 3 阶固有频率均有明显提高,近似频率下相对变形量有所减小,对于提高机床整机的加工精度至关重要,因此,针对床身的优化是合理的。
3 、试验模态分析
3. 1 试验模态测试系统
工厂对优化后的床身结构进行了生产,我们对生产后的床身进行模态试验,本实验采用 SIMO 锤击法测试方式,试验测量系统共由三个部分组成: 激振系统,响应采集系统,模态分析和处理系统,图 7 所示为测试系统原理简图。
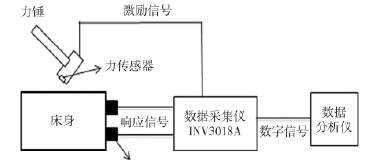
图 7 测试系统原理简图
3. 2 试验方案设计
3. 2. 1 支承方式
为尽量使床身的各阶模态更好地显示出来,在床身底面加上 6 个橡胶垫块用来支撑床身部件。
3. 2. 2 激励点和响应测点的布置
一般来说激励点的布置原则是根据结构的特点和试验目的,以不遗漏模态为前提而又尽可能简化,此外激励点还应避免在各阶模态的节点位置,节点位置可由试验前的有限元分析获得。
响应测点位置以能反映零件的动态特性、振动明显、能得到较好信噪比信号为原则[7],试验响应测点布置如图 8 所示。
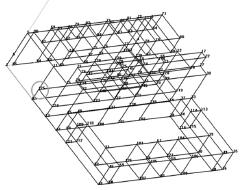
图 8 激励点和响应测点的布置
3. 3 模态试验分析结果
采用东方振动噪声研究所模态试验测试分析设备Coinv DASP V10 中集总平均法进行模态定阶识别,试验后的床身模态频率如表 4 所示,振型如图 9 所示。
表 4 试验模态分析结果
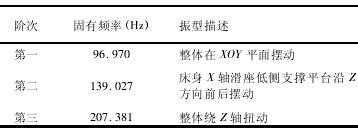
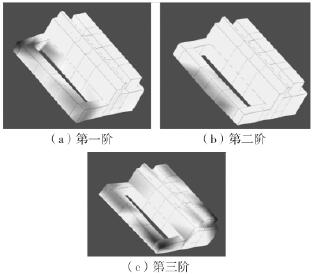
图 9 试验模态振型图
3. 4 理论与试验对比
通过试验分析得到床身的前 3 阶固有频率并与其优化后的理论分析结果进行对比,如表 5 所示,各阶振型相同,同阶固有频率最大误差为 13. 4% ,说明试验结果与理论分析结果相一致。
表 5 理论与试验分析结果对比
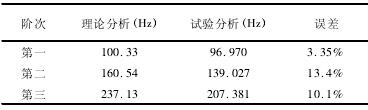
4 、结束语
本文以某工厂研制的叶轮专用加工中心为例,通过理论分析找出该加工中心床身结构的薄弱环节,有针对性地提出优化改进意见。
通过对比,优化后的床身结构固有频率有明显提高,近似频率下相对变形量有所减小。最后通过试验验证了该方案的合理性和可行性。本文所得的结论为改善整机的动态特性奠定了一定的基础。
投稿箱:
如果您有机床行业、企业相关新闻稿件发表,或进行资讯合作,欢迎联系本网编辑部, 邮箱:skjcsc@vip.sina.com
如果您有机床行业、企业相关新闻稿件发表,或进行资讯合作,欢迎联系本网编辑部, 邮箱:skjcsc@vip.sina.com
更多相关信息