数控加工中误差的来源及解决方法探讨
2018-6-8 来源:转载 作者:沈文华,张吉堂,于松章
摘要:文章分析了从图纸到获得成品零件的数控加工过程中误差的主要来源及可采取的改善措施,通过研究这些问题,对提高零件加工质量及提高生产效率有一定的指导作用。
关键词:数控加工;误差来源;定位基准
数控加工技术是现代机械加工技术的重要基础,应用数控加工技术可以实现对各种精密零件的精细加工。但在加工过程中,会由于某些原因而产生不可接受的误差,致使零件精度达不到要求。如何快速准确地辨识数控加工过程中产生的误差已成为一项重要任务。从图纸到成品零件的数控加工过程中,误差的主要来源可概括为主观原因和客观原因。笔者将从不同方面分析产生误差的原因,并指出可以采取哪些措施来减小误差。
1、主观原因产生的误差
在实际加工中,由于主观的人为原因造成的误差一般有以下几种形式:工艺误差、刀具半径补偿应用不当产生的误差、刀具及切削参数选择误差、对刀误差、测量误差等。
1.1 工艺误差
加工工艺也叫加工方法。数控编程者首先应清楚加工零件的各项技术要求,然后根据技术要求及公差大小决定零件的加工方法。工艺误差是由于加工方法不当产生的误差。
1.1.1 定位基准要统一
数控加工中应采用统一的定位基准,防止加工过程出现轮廓位置及尺寸与图纸不符的现象而造成较大的误差。为了减小这样的误差,尽量在编程时选择的编程原点与工艺基准和设计基准点重合。同时,为了避免尺寸换算带来尺寸链误差,设定的编程原点应有利于坐标数值的计算、工件的找正,使对刀方便,编程简便。一般对称零件的编程原点选在零件的对称中心上,对于一些形状不规则的零件,可在其精度要求较高的基准面上选择编程原点,以内孔定位的零件,以内孔中心作为编程的原点。
1.1.2 加工工艺路线要合理
数控加工工艺路线安排要合理,以减少由于加工顺序不同而产生的误差。数控加工工艺路线设计要考虑到具体的加工细节,尤其是在数控镗、铣床上加工形位公差要求较高的零件时,对各个环节更要重视。例如,加工平面与平面有平面度的要求;加工端面与外圆、内孔有垂直度要求;内、外圆柱面有同轴度要求时,均应在一次装夹中完成。
1.2 刀具半径补偿应用不当产生的误差
刀具半径补偿的执行过程一般可分为 3 步:刀补建立、刀补执行、刀补取消。刀补建立或者取消时,必须在 G00 或 G01 指令下进行,不能在 G02或 G03 指令下进行,且在同一个加工方向上 G41或 G42 不能混用,不允许连续使用两句非所选平面的移动指令。一般在刀补建立或者取消过程中容易发生过切或者欠切情况,导致被加工零件的不合格发生 (见图 1)。
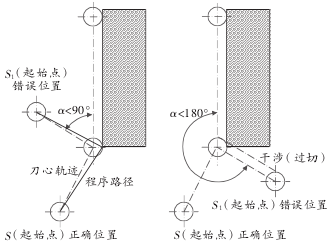
图1 发生过切或者欠切的情况
左图中错误位置导致欠切,右图中错误位置导致过切,所以在建立或者取消刀补时要注意:当刀具中心移动轨迹于前进方向平行时 (α=0°),建立和取消补偿都不过切;当 0°<α<90°时,建立不过切,取消过切;当 α<0°时,建立过切,取消不过切;当 90°≤α≤180°时,建立和取消都不过切;当180°<α<270°时,建立过切,取消不过切;当α=270°时,建立和取消都不过切;当270°<α<360°时,建立和取消全部过切。
铣削非直线轮廓时,例如圆弧 (分内圆和外圆),铣刀铣外圆时避免法线方向切入,要让刀具沿切线方向切入圆弧,加工完成后让刀具沿切线方向走出轮廓线后再取消刀补,以免出现过切现象(见图 2);在铣刀铣削内圆时,也要沿切线方向切入,建立方法是圆弧与圆弧相切 (见图 3)。
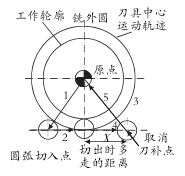
图2 铣外圆弧时铣刀切入切出方法
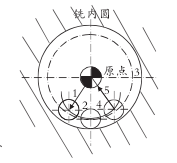
图3 铣内圆弧时铣刀切入切出方法
除了建立或者取消时要注意角度问题,使用时还应注意:切削起始点到轮廓线上目标点的移动距离必须大于刀具半径补偿值,且必须在所补偿的平面内连续移动才能正确切削;D00 ~ D99 为刀补存储器代号,应用刀补时必须选择 D01~D99 中的任意一个代号才能建立起有效的刀补,D00 代表取消刀具补偿,刀具补偿值在加工之前必须输入到补偿存储器中。
1.3 刀具及切削参数选择误差
刀具尺寸是在静态下进行测量的,而加工过程是动态的,刀具不但受到切削力而且还要受到振动外力的影响,这样就会造成零件加工出来的尺寸和图纸尺寸不一致,此项误差的大小主要取决于刀具的质量和动态特性。刀具的性能会直接影响到零件的加工质量及数控机床的生产效率,如加工参数选择不正确,刀具的磨损,刀具的测量误差,都会导致零件的精度异常。
对于数控加工中由于刀具及切削参数选择不当引起的加工误差,可以通过 4 种方法来预防:一是加工精度要求高的零件分粗、精加工,针对不同的切削材料选择不同材质的刀具、不同的转速与进给量。二是减少换刀定位误差,选择一把合适的刀具将零件上能加工的内容全部加工完成以后,再换其他刀具来加工。三是选择恰当的加工余量,分配加工余量时精加工应取 0.3~0.5 mm。加工余量过大会造成拉动过切和偏让欠切,加工余量过少时也会因为切入困难造成欠切,补偿余量后再加工,会引起过切。四是在凹槽的加工要求较高时,先用直径较小的键槽铣刀铣槽的中间部分,再利用刀具半径补偿铣削两侧。
现在各种形状、材质的刀具种类繁多,不同的刀具应用在不同的场合,因此,在铣削过程中,加工人员应根据加工的实际要求,考虑工件形状、刚性、 材料、 切削参数等相关因素选择最恰当的刀具和切削参数进行加工。
1.4 对刀误差
在数控编程时确立了工件坐标系,数控加工中,还要确定刀位点在工件坐标中的位置。常用的对刀方法有:试切法对刀、对刀仪对刀、ATC 对刀等。产生对刀误差的原因主要有:一是用试切法对刀时,对刀误差主要源于操作过程中目测产生的误差和试切工件之后的测量误差。二是在对刀完成后,对于相对编码器的数控设备要执行 “机床回零”操作,在此过程中可能会发生零点漂移而导致回零误差,从而产生对刀误差 。
三是使用对刀仪对刀时,误差主要来源于仪器的制造、安装和测量,另外错误的仪器使用方法也会造成误差。减小对刀误差的主要措施有:一是当用试切法对刀时,操作者在细心对刀后还应参考零件尺寸和编程尺寸之间的差值来修正刀具的补偿值。二是定期检查数控机床的零点漂移情况,及时调整限位开关位置及系统参数。三是使用仪器对刀时,应注意仪器的安装和测量精度,正确掌握专用仪器的使用方法。
1.5 测量误差
不同的加工内容要选择不同的量具进行测量。量具本身精度、加工人员使用量具的熟练程度及所检测项目的测量方法都会对零件的精度产生影响。因此量具要定期送检,并对使用人员要进行专门的测量技术培训。有条件的单位可以利用三坐标测量机及其他专用量仪进行测量,并将测量结果与加工人员的量具测量结果对比,以分析误差原因,这对保证零件精度有一定指导作用。近年来,在线测量设备也逐渐应用到精度较高的零件加工过程中,这样使得加工和测量在同一设备上进行,不仅提高了生产效率,而且不存在重复定位误差,可以随时对加工中的工件进行检测,并能根据在线测量结果调整工艺参数,从而提高加工精度。
2、 客观原因产生的误差
客观原因产生的误差主要分为数控操作系统误差、机械误差及工装误差 3 个部分。
1)数控系统误差。数控系统按照伺服系统的控制方式可以分为开环控制系统、闭环控制系统和半闭环控制系统。其中闭环控制系统能够实时检测刀具的实际位置,并将结果反馈给数控系统,进行反馈值与系统中指令值的比较,直到差值消除时才会停止移动,因而控制精度很高。但是,闭环位置检测反馈中各种不稳定因素较多,因此调试工作困难,若各种参数不匹配,会引起系统振荡,造成机床工作不稳定。闭环控制系统误差的主要是反馈系统在安装过程中产生的安装误差。减小上述误差的主要方法是提高反馈系统的安装精度,尽量选用精度较高的反馈系统。半闭环控制系统中存在不反馈环节,刀具的位置精度仍然会受到不反馈环节影响。传动链误差是指传动链中首末传动元件之间相对运动的误差,其是影响加工精度的主要因素,可以通过修改数控系统参数的方法进行补偿。开环控制系统不带有位置检测装置,也没有反馈电路。由于进给系统中没有反馈检测装置,其进给线路产生的误差就无法通过反馈信息进行补偿,从而导致了实际位置误差。例如,采用步进电机的主要误差有步距误差、动态误差和起停误差。针对以上各种误差,可以选择能够满足步距角要求的电机或细分电路驱动电机来改善。
2)机械误差。数控机床机械部分包含减速齿轮、支承轴承、滚珠丝杠副及联轴节等。传动丝杠存在反向间隙,当工作台反向运动时,这种间隙会造成电动机空转而工作台不运动,从而产生误差。针对传动反向间隙,消除滚珠丝杠与螺母间隙的方法是施加预紧力;在开环系统中引入切入与切出方向延长量,防止欠切削或过切削而影响零件的加工质量;测出闭环和半闭环系统中的间隙值,可作为反向螺距误差补偿参数进行设定。对于由机械传动链受力变形和热变形而引起的误差,可通过提高机床零部件质量 (加工精度、刚度与热特性等)、降低内部热源发热量及严格控制加工环境和使用条件等来解决。
3)工装夹具误差。工装夹具的定位误差会直接影响工件的尺寸精度和位置精度,因此要求工装夹具要有良好的定位精度、刚性及结构工艺性。合理选择夹具的支点、定位点和夹紧点,保证零件夹紧时的变形量在合理范围内,否则过大的变形量将影响零件的加工精度。若采用相应的措施仍不能控制零件的变形,应当考虑必要的工艺措施,例如对零件进行热处理,以消除应力,减小变形;对不能用热处理方法解决的变形问题,可以采用粗、精铣分开的方法,粗、精铣加工采用不同的夹紧力。
3 、结束语
综上所述,在数控机床上加工零件是整个工艺系统及加工环境综合作用的结果,误差来源非常复杂,零件的加工精度取决于系统的各种因素。因此,必须综合考虑各个环节,分析并找出影响零件精度的误差来源,以便采取相应措施。
来源:太原工业学院工程训练中心, 中北大学机械工程与自动化学院
投稿箱:
如果您有机床行业、企业相关新闻稿件发表,或进行资讯合作,欢迎联系本网编辑部, 邮箱:skjcsc@vip.sina.com
如果您有机床行业、企业相关新闻稿件发表,或进行资讯合作,欢迎联系本网编辑部, 邮箱:skjcsc@vip.sina.com