浅析加工中心主轴和机械手典型故障原因分析及解决
2021-1-8 来源:中国一拖集团有限公司 作者:闫百楼
摘要: 简要分析了加工中心主轴和机械手的几个典型故障,及时有效地排除了故障,提高了主轴的可靠性和机械手的稳定性,缩短了加工中心的停机时间,为后期维修提供了宝贵的经验。
关键词: 编码器; 主轴预紧力; 机械手
1 、加工中心主轴故障
1.1 加工中心主轴编码器输出轴断故障的分析与排除
某公司主要生产 73. 5 k W( 100 马力) 以上轮式拖拉机,NC800 卧式加工中心承担着半轴壳体的加工任务,近段时间,在机床使用过程中频繁出现主轴报警的故障现象,即在主轴定向时发生主轴轮廓监控报警。经过快速检查确认,故障原因是主轴位置编码器与主轴箱连接的输出轴断裂,导致不能检测主轴转速,出现报警。
当时正值高产月,如果不尽快排除故障,将严重影响拖拉机的生产进度。经查阅相关图纸资料,该主轴编码器输出轴结构以及断裂部位如图 1 所示( 图中未注尺寸单位: mm) 。
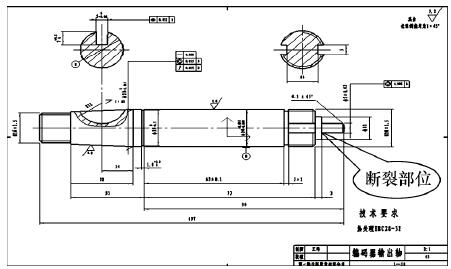
图 1 主轴编码器输出轴结构及断裂部位
针对该故障,正常的维修方法是: 整体拆卸主轴箱,分解传动机构,拆出输出轴,测绘尺寸并加工备件,然后进行更换安装。但此维修方法难度大,拆卸时间长。综合主轴箱的拆卸、解体
、安装,再加上测绘、加工备件等,整体停机时间应该在一周以上,费力费时,且对该公司生产任务的完成造成严重影响,需要想尽一切办法尽快排除设备故障,保证正常生产。
经过研究分析,根据编码器输出轴现场断裂部位,以及现场空间大小,可以利用改进主轴箱位置编码器输出轴锁母来解决该问题。这里存在的主要不确定因素是同轴度问题,因为编码器轴跳动应该小于0.10 mm。决定利用编码器输出轴末端外螺纹 M20×1.5 加工一根内螺纹轴,原编码器采用 2 个结合子,现改为一个结合子。
图2 是新设计的输出轴锁母。加工出来的过渡轴安装后经百分表验证,跳动仅 0.05 mm,完全满足编码器的精度要求。经尺寸测绘、加工、安装,在多部门的快速协助下,该问题迅速得到了解决,仅用时 8 h 即恢复了正常生产。没有拆解主轴箱,大大减少了设备停歇时间,为以后类似故障提供了一个好的解决思路。
1.2 加工中心主轴拉刀机构的故障分析与排除
DMC1035C 立式加工中心担负着壳体类零件的主要加工任务。近段时间以来,设备开始出现主轴松紧刀严重异响的故障现象,导致紧刀信号不到位,换刀过程无法继续进行,严重影响生产任务的顺利进行。
此台机床是德国进口设备,属于电主轴结构,没有图纸可以查阅主轴拉刀机构的工作原理,在咨询厂家服务人员后,他们为了技术保密,直接告诉要更换整套拉刀机构,而且价格昂贵,服务时间不定。在国产发动机更新换代的背景下,为了不影响高产月的生产任务,为了消除主轴拉不紧刀的安全隐患,经设备部门领导批准,决定自己尝试拆卸主轴,修复主轴松紧刀出现的严重异响故障。
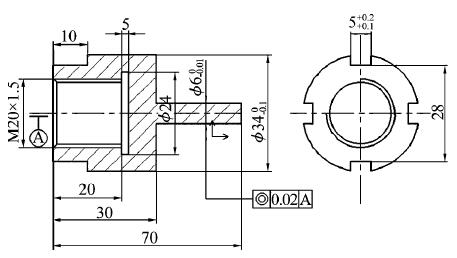
图 2 新设计的输出轴锁母( 图中未注尺寸单位: mm)
1) 拆卸外部防护罩( 见图 3 ) 。手动方式下,多次试验并观察主轴的松紧刀过程,初步确定异响的发生部位。
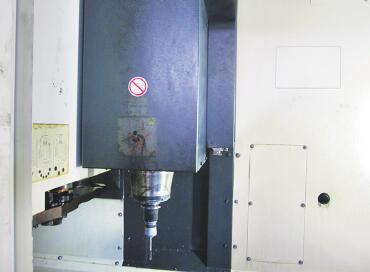
图 3 主轴外部防护罩的拆除
2) 在多次观察主轴装卸刀的过程中,发现主轴在松刀时会发出“嘭”的异响,而且响声比较大。摘掉主轴上的刀具,检查拉爪并没有发现明显磨损的情况,排除了拉爪与刀柄撞击发出异响的可能( 见图 4) 。
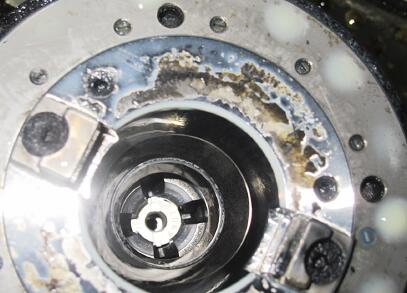
图 4 主轴拉爪并没有发现明显的撞击痕迹
3) 一般主轴的拉刀机构都可以通过调整缸体带动拉刀杆的行程来满足主轴松紧刀的程度,于是想通过调整拉刀行程来尝试消除拉刀的异响故障,但是这样就必须脱开主轴电机,由于此台设备属于电主轴结构,所以需要拆出整个主轴才能观察到内部缸体与拉刀杆的结构原理。
4) 拆出整个主轴后( 见图 5) ,我们发现拉刀机构的行程是由 2 个气缸组成的增压缸( 见图 6) 来控制,而增压缸末端有一个卡簧发生了明显的位移与变形,分析后发现此卡簧正是起到增压缸末端活塞的限位作用。由于卡簧限不住位,所以缸体的活塞在缩回时缩不到位,拢不住气,即导致松刀时出现异响。
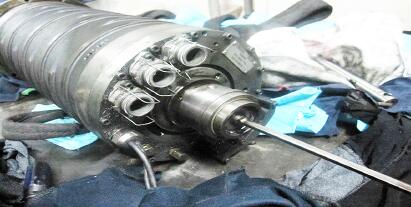
图 5 拆出主轴,脱出拉刀机构
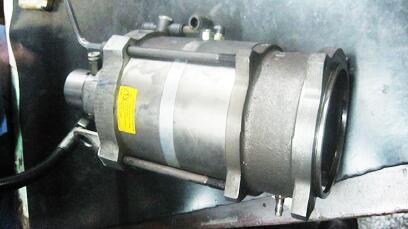
图 6 2 个缸体组成的增压缸
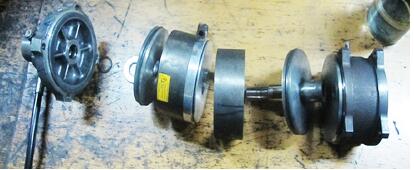
图 7 拆除损坏的卡簧与密封
5) 更换损坏的卡簧和密封( 见图 7) 后,利用压缩空气接两路气管进行了松紧刀的试验,没有出现松刀异响的故障现象,于是重新安装调试,解决了这一疑难故障。
经过 2 个月的修复,完成了从拆卸拉刀机构、清理脏灰,到分析问题、掌握其工作原理、更换备件等一系列维修工作( 见图 8) ,有效地解决了换刀故障频繁发生的问题,提高了设备使用效率,生产效率大大提高。
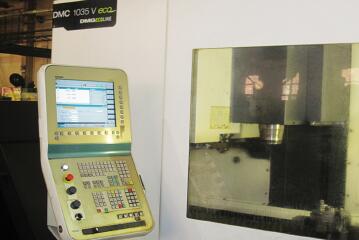
图 8 故障排除后设备运行正常
1.3 加工中心镗孔圆度误差的故障分析与排除
该公司加工中心种类繁多,加工工艺复杂多变。加工中心在加工传动箱壳体类零件的镗孔时圆度误差不稳定,有时超差达到 0. 05 mm 左右,X 轴相对于工作台回转中心机械原点的位置也极不稳定,反映到箱体的加工精度很难保证,严重影响了传动箱壳体类零件的加工精度,直接影响了产品质量的提升。为了提升产品质量,解决镗孔圆度误差及确保 X 轴零点稳定就显得尤为重要。
1) 针对各机床的不同情况,制定合理的解决方案。例如: R1200-U 加工中心在加工过程中出现镗孔椭圆现象,是拉刀不紧导致; Storm1400 加工中心的镗孔椭圆现象是主轴轴承磨损导致; HPC800 加工中心镗孔圆度误差及 X 轴零点不稳是丝杠与轴承之间的传动间隙过大导致。
2) 首先检查各机床的主轴跳动,检查主轴拉刀机构,必要时更换,保证拉刀可靠。例如: R1200-U加工中心更换拉刀杆与碟簧后,有效地降低了圆度误差。
3) 检查主轴轴承是否因磨损导致轴承预紧不够而影响主轴跳动。如果发现轴承磨损,则更换主轴轴承,例如: Storm1400 加工中心在更换主轴轴承后明显改善了加工过程中的镗孔椭圆问题。
4) 最后检查 X 轴丝杠及轴承间隙。如果间隙调整未果时就要更换轴承及丝杠,从而彻底消除传动间隙。例如: HPC800 加工中心镗孔圆度误差及 X轴零点不稳就是丝杠与轴承的传动间隙过大导致的。在更换 X 轴轴承与丝杠之后,调整 X 轴平衡,检验 X 轴零点,有效地控制了镗孔圆度误差及 X 轴零点不稳这一现象的发生。
2 、加工中心机械手故障的分析与排除
HP1250 铱镏数控镗铣床担负着箱体类零件主要的加工任务。2019 年 3 月以来,该设备开始频繁出现机械手换刀故障,导致换刀过程无法继续进行,严重影响生产任务的顺利进行。此机床最初只是普通数控镗铣床,后来为满足加工需求,配套了刀库系统,使之成为同加工中心一样的数控设备。由于长期使用,并且机床本体在与刀库系统的配合上存在不足,此台机床在机械手换刀时,经常会出现机械手旋转、伸缩和归刀时的一系列故障问题,而且故障频发,严重影响生产任务。
1) 观察机械手换刀过程,分析机械手在换刀过程中的伸缩、旋转、滑移和归刀等换刀分段动作,初步确定造成换刀故障的原因。
2) 在多次换刀观察后发现机械手在旋转时总会出现旋转无力的现象,旋转过程中有死点存在,轻敲才会进行接下来的换刀动作,排除了液压马达的问题。在紧固连接处的油管接头、改良密封、拆掉机械手、清理缸套内壁、更换掉旋转的两套轴承( RST010)后,这一现象得到了明显好转。图 9 为机械手旋转马达,图 10 为清理机械手内壁并更换轴承。
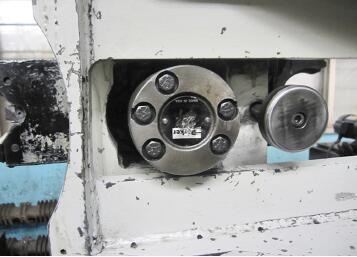
图 9 机械手旋转马达
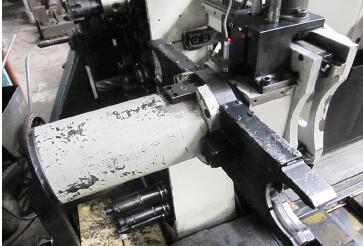
图 10 清理机械手内壁并更换轴承
3) 此外,该设备的机械手在归刀过程中,总会出现归不进刀的情况,容易造成掉刀。在多次观察后发现归刀位置存在偏差。由于该机床刀库系统属于改造后的系统,无法通过参数调整刀库机械手换刀位置的高低,所以只能通过机械调整。
4) 该机械手的换刀位置高低可以通过调整机械手转轴两端的锁母( 见图 11) 来控制。经检查发现机床原有的锁母无锁紧功能,长时间使用会造成轴向的轻微移动,故过段时间就出现归刀故障。
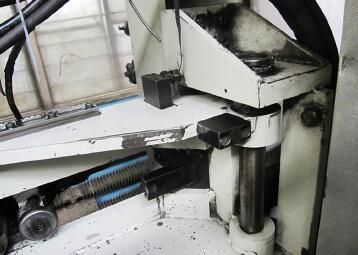
图 11 旋转轴锁母
5) 为了彻底解决归刀故障,决定改进原有锁母,更换为本身带有自锁功能的锁母,以达到限位要求。经过2 个月左右的彻底修复,完成了从机械手旋转油缸螺钉的紧固、油管接头的密封及紧固,到机械手伸缩轴承的更换及其缸套内壁的清理等一系列工作,有效地解决了机械手故障频繁发生的问题。
3 、结束语
加工中心主轴是加工中心的核心部件,机械手在加工中心是执行部位。通过日常检查及时发现并处理加工中心常见的机械故障,减少加工中心的故障停机次数和维修时间,保证加工中心的日常运转,延长加工中心的使用寿命,为企业生产节省成本。
结合日常维修中的典型实例对加工中心主轴和机械手的故障进行分析与总结,及时有效地排除故障,提高了主轴的可靠性和机械手的稳定性,缩短了加工中心停机时间,为拖拉机生产保驾护航! 同时也为后期维修提供了宝贵的经验。
投稿箱:
如果您有机床行业、企业相关新闻稿件发表,或进行资讯合作,欢迎联系本网编辑部, 邮箱:skjcsc@vip.sina.com
如果您有机床行业、企业相关新闻稿件发表,或进行资讯合作,欢迎联系本网编辑部, 邮箱:skjcsc@vip.sina.com
更多相关信息