基于五轴联动加工技术的叶轮加工方法分析
2021-5-24 来源:桂林航天工业学院 广西桂林 作者:钟国成
摘要: 叶轮是动力机械中不可缺少的重要部件,已经被广泛应用于汽车制造、航空航天等多个领域。由于叶轮本身的结构复杂性较强,应用传统加工技术困难性大,性价比不高。五轴联动加工技术可有效避免刀具干涉,提升表面质量,增强加工精度,性价比高,目前已经逐渐取代传统加工技术。本文主要讨论了基于五轴联动加工技术的叶轮加工思路与具体加工方法,以供参考。
关键词: 五轴联动加工技术; 叶轮加工; 方法
所谓五轴联动加工技术,简单来说就是一种在 CNC 控制下五个坐标轴协调运动加工零件的加工技术,它以计算机网络技术作为主要的技术支撑。随着加工技术的持续发展,虚拟仿真技术逐渐被应用于五轴联动加工中,给后者加工质量与精度的提升产生了重大的积极影响。基于五轴联动加工技术加工叶轮,为避免刀具干涉、碰撞,先在仿真环境中构建叶轮模型,经多次试验后确定切削参数,并对其进行验证,再将参数录入五轴联动数控机床,叶轮一次成型。
这不仅能提升叶轮加工质量与精度,也能减少加工叶轮的必要时间,同时做到资源的有效节约。那么,基于五轴联动加工技术的叶轮加工具体方法是什么样的呢? 以下就是笔者对此的分析与论述。
一、基于五轴联动加工技术的叶轮加工思路
( 一) 工艺流程叶轮加工主要是加工叶片与流道,由于叶片通常为扭曲状,而流道则很狭窄,所以加工中常有干涉、过切、碰刀现象。为了实现对这些现象的有效规避,并保证加工精度,选择分阶段济钢。第一阶段,叶片、流道粗加工,主要采用五轴曲线加工法,对于流道,先进行结构分割后再加工; 第二阶段,叶片精加工与清根处理,主要采用五轴侧铣方式; 第三阶段,流道精加工,主要采用五轴限制面加工法。
( 二) 五轴加工刀具路径规划
( 1) 粗加工刀具。
第一阶段粗加工从流道深度延伸的方向进行分层加工,合理连接每层的刀具路径,使之构成整体加工路径。由于流道普遍为梯形,入口窄出口宽,所以选择倒“Y”型路径,这不仅可缩小切削路径长度,也能有效提升加工效率。在此过程中,先根据刀具轨迹点确定开槽刀位,再以刀具直径
、开槽刀位至偏置面弧长等确定扩槽走刀行数,基于此确定行距,从而构建刀轴矢量图。
( 2) 精加工刀具。
对于选择五轴侧铣方式的叶片曲面,确定以叶片上下曲线为导向线,从而保证切削刃与被加工曲面相切。由于流道面对加工精度及表面顺滑度有极高要求,所以通过等参数线法进行刀具路径的规划。先沿一定方向将流道曲面离散成点,再根据流道走向连接这些点,构成刀具路径。以同等方法生成的等参数刀具路径,就是刀轴矢量控制线。
( 三) 刀具选择
刀具的选择应充分考虑加工目的、加工工艺要求、毛坯材料、允许切削面、刀具特性等多方面的因素。粗加工的主要目的在于切削可能多的材料,为达到这一目的,就要选择直径较大的刀具,而流道的加工需要刀具直径小于两叶片间最小距离。那么,粗加工选择球头铣刀,精加工选择球头刀,两种刀皆为硬质合金涂层。
二、基于五轴联动加工技术的叶轮加工方法
( 一) 数控编程规划( 附工程图)选择支持复杂五轴加工、具有轨迹批处理功能、携带后置处理模块的软件进行数控编程,如 CAXA 制造工程师、北京精雕软件等。
附工程图:
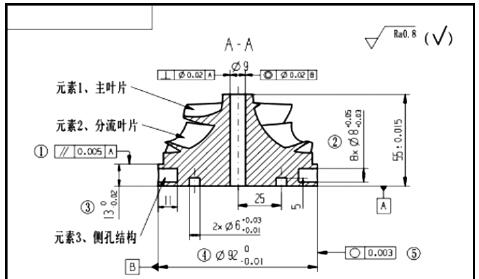
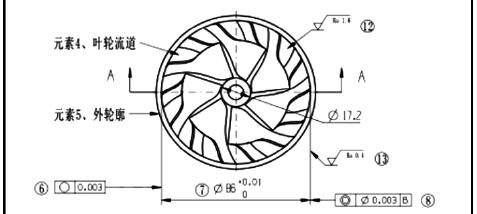
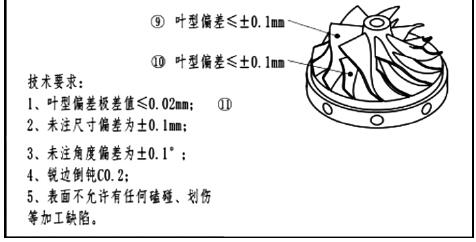
叶片流道粗加工阶段,根据倒“Y”型刀具路径,以叶片上缘高度为建构分成面的基准,对流道面进行等距划分,从而形成流道代替面。基于此,确定最大层深,先定位加工辅助面母线,再通过旋转面方面建构加工辅助面。在明确开槽到位的情况下,以刀具精度、开槽刀位至偏执面出气口弧长确定走刀行数,并设定相应的速度参数。为了防止撞刀、干涉等现象的发生,以工件大小及其原点位置确定相应的高度参数。叶片精加工阶段,CAXA 环境中侧铣导线是以刀位点为定位点的,那么刀具就极大可能出现刀尖过切,因而要手动设置相应的偏置参数。建构好等距面后,将其与叶片曲面交线确定为叶根线加工导线。
基于对加工精度及撞刀、干涉现象的充分考虑,设置刀具运转中的拓展余量参数及切削速度参数。流道精加工阶段,确定限制面与加工面,根据精度要求设置切削参数。根据单个刀具轨迹生成全部叶轮刀具轨迹,确定仿真效果。
( 二) 后置处理
在生成刀具轨迹的过程中,CAXA 软件自动形成相应的文件,这些文件需要通过后置处理才能被虚拟数控机床读取。后置处理中,结合虚拟数控机床特性与功能,确定最适宜的后置处理器,该工具可直接进行从文件向机床可读取代码的转换。后置处理器的开发,遵循“数控系统选择———机床类型选择( 运动学设置与机床组件配置) ———机床参数设置( 运动轴行程等) ———其他控制程序设置( 起止刀具进退等) ———子程序调用( 钻孔、循环控制等) ———宏程序编制”,同时确保刀位点数值和机床运动的一致性。
( 三) 设计仿真加工流程
选择可仿真五轴联动加工过程、有真实三维实体展示效果与 CAD/CAM 接口、能实现与其他工程软件的嵌套运行、可验证与优化 NC 程序的数控加工方针软件进行仿真加工,如 VER-ICUT 等。基于 VERICUT 的叶轮仿真加工流程如下: 设置仿真机床 环 境———设 置 控 制 程 序———添 加 刀 具、毛 坯、加 工 程序———基础参数设置———仿真———比较检查结果———合格后进入数控现场加工( 不合格修改加工程序) 。
仿真机床环境设置中,先构建五个轴间的逻辑关系,以此作为参照设置结构树,再根据结构树导入不同部件的几何模型,从而完成机床环境设置。至于几何模型的建立,可选择应用 UG、CAD 等软件建模后将文件导入 VERICUT,也可选择直接在 VERICUT 建模。处于对仿真机床模仿真实机床运作的考虑,还应设置对刀点、碰撞检查等机床参数。
控制程序设置中,需要对控制程序进行二次开发,这主要是为了保证加工代码与机床实际需求相符。对于换刀及五轴开关功能的实现,以 WFL M65 机床为例,这一机床的“换刀”是以“TLPREP1”与“TLCH1”代码实现的,前者用于刀具准备,后者用于更换刀具以及调节刀轴角度,那么在仿真加工中需要加入这两种代码。
另外,五轴加工时,由于两个旋转轴共同运作,为防止刀具中心偏移,通常该机床要打开“RTCP”功能。那么在仿真加工中就要加入相应的指令代码。
( 四) 加工
( 1) 加工程序。
先确定加工坐标系,并结合叶轮加工要求以及刀具相关数据定义刀具,再根据叶轮结构特性确定具体加工流程,基于此,选择切削参数进行模拟加工,经多次实验排除干涉、撞刀等问题,在 NC 程序验证后确定实物切削参数,最后在实体的五轴联动数控机床的计算机上录入切削参数,并将毛坯、NC程序载入机床,通过实物加工获得叶轮零件。
( 2) 结果检测。
仿真加工完成后,对加工效果图进行分析检测,看有无过切、欠切、残留量较多的情况,基于此,优化加工工艺,从而满足叶轮加工要求。
( 3) NC 程序优化。
仿真完成后,通过 VERICUT 相应模块进行 NC 程序的优化与验证。优化过程中,设置刀具参数、工件材料、机床类型等,并对比前后程序变化。
三、结语
综上所述,基于五轴联动技术的叶轮加工,将虚拟仿真技术融入其中,先通过仿真获得经验证后的 NC 程序及最优切削参数,再将其录入实体机床进行实物加工,可有效避免实际加工中的干涉、撞刀问题,并提升加工精度与质量。值得注意的是,仿真所获得的叶轮模型是在理想的环境下获得的,实际加工还得考虑机床的维护管理问题,保证机床在最接近理想环境的情况下运行。
投稿箱:
如果您有机床行业、企业相关新闻稿件发表,或进行资讯合作,欢迎联系本网编辑部, 邮箱:skjcsc@vip.sina.com
如果您有机床行业、企业相关新闻稿件发表,或进行资讯合作,欢迎联系本网编辑部, 邮箱:skjcsc@vip.sina.com
更多相关信息