回转类工件加工误差在机测量系统
2017-12-8 来源: 上海大学 机械自动化及机器人重点 作者:王为东 沈南燕 吴耀赞 喻志响
摘 要 :针对回转类工件轮廓加工误差检测,开发了一套用于数控车铣复合加工中心的在机测量系统。利用接触式测头,读取数控机床各轴坐标值获取测量数据并由以太网上传至上位机,配合误差评定算法及相关软件,实现了回转类工件尺寸、圆度、圆柱度及同轴度的在机检测。介绍了测量系统的硬件组成、软件开发及验证实验结果。在机检测结果可以反馈至数控系统用以补偿加工误差,也可通过车间局域网上传至车间层用于生产管理,因此该系统在大批量、无人化生产中具有良好的应用价值。
关键词 : 回转类工件 接触式测头 圆度 误差评定
机械加工是先进制造技术的基层作业,是先进制造系统中最基本最活跃的环节,其基本目标是在低成本、高生产率的条件下保证产品的质量[1]。但在目前的数控车床加工过程中,零件加工精度的检测主要是采用传统的手工测量和离线检测方法,包括回转轴线法、三点法、投影法等。这些方法都需要将工件转移到专门的夹具里用专门的测量仪或千分表、卡尺进行测量,显然这些测量方式需要二次定位与装夹,不仅效率低,还会产生二次定位误差,越来越不能满足车间快速加工生产的需要[2]。
如果能把车床和合适的检测仪器有机结合起来,这样车床不仅可以用于工件加工,而且可以直接对刚加工完成的工件进行尺寸测量,再利用 CNC 系统的通讯功能,就可以直接通过上位机实现对工件轮廓误差的评定。通过这种方法不仅可以有效避免二次装夹误差,提高测量精度,解决离线零件检测中的费时费力问题,而且可以扩大车床的使用范围,具有很好的应用价值[3]。
因此,针对以上问题,本文围绕回转型零件的轮廓检测,在数控车铣复合加工中心上展开了在机检测系统的研究。通过集成在机测量系统,实现对回转型工件轮廓的方便快捷的测量和评定。
1 、在机测量系统的构建
数控系统本身并不具有测量和误差评定的能力,要实现轮廓的在机测量,必须在数控机床本身能力的基础上,集成具有测量能力的装置,并开发具有误差评定功能的软件。因此,有效的系统集成是实现在机轮廓测量的关键。如图 1 所示,在 HTC50100车铣复合加工中心上集成了 Marposs 接触式在线测量装置,采用以太网经由无线路由器实现上位机和数控系统的连接与通讯。
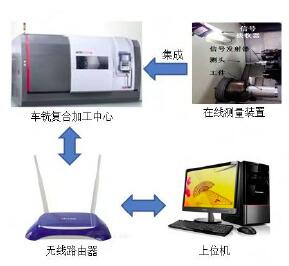
图 1 在线测量系统组成
1.1 在线测量装置与数控系统的集成
本次试验使用的测量装置为 Marposs E83L 加工中心专用触发式测量系统[4],主要由信号发射器、测头和信号接收器组成。其中信号发射器和测头作为刀具装在刀塔上,发射器和接收器之间通过红外传输的方式连接。接收器接收发射器发射的红外信号,并传送给 CNC 系统,同时通过指示灯的变化,显示测量系统当前状态。例如:若程序运行有问题,“Error”指示灯会闪烁;当其接收到触碰号时,“Probe Status”指示灯会闪烁等[5]。可以根据指示灯的状态,判断测量系统的工作情况,并合理的处理异常情况,信号接收器与 CNC 系统具体接线如图 2 所示。
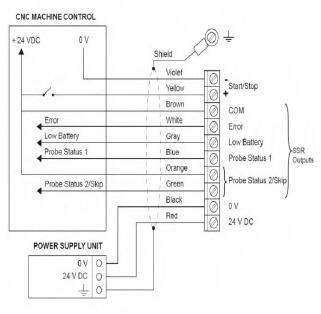
图 2 信号接收器与数控机床的接线图
在实现程序跳转时,利用的是 FANUC 数控系统的高速跳转指令,即 G31 指令。该指令通常只用于测量功能,需要外部输入信号,输入信号地址是X4.7。G31 执行过程中如果没有 SKIP 信号则和G01 完全一样,如果在执行过程中 SKIP 信号置“1”,则在 SKIP 信号置“1”的位置清除剩余运动量,直接执行下一个程序段。在 SKIP 信号置“1”时,进给轴的坐标值会储存在系统变量中,供测量宏程序计算使用。本研究中当测头触碰到工件后,信号接收器就可以将触碰信号传送给 CNC 系统,以实现程序跳转。图 3 所示为跳转功能示意图。
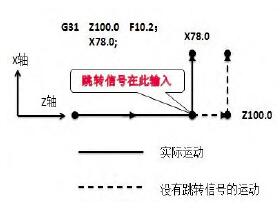
图 3 G31 跳转功能示意图
1.2 上位机与数控系统的集成
随着科技的发展,数控系统也得到了进一步的完善。现在数控系统不仅具有通信功能,能够通过以太网实现与上位机连接,而且为用户提供了许多工具包和函数库,供用户更好的开发和使用。
本次试验通过以太网实现上位机与数控系统的集成,然后利用 FANUC 系统提供的 focas 函数库cnc_download3(unsigned short Flib Hndl, long *length, char *data)以及 cnc_rdmacro(unsigned short Flib Hndl, short number, short length, ODBM *macro)函数,实现对数控系统内存中宏变量的读写,进而通过上位机软件对工件轮廓作出评价。
2 、轮廓检测的实现
要实现回转型零件的轮廓检测,不仅仅需要硬件的投入,也要软件的支撑。本次试验所使用的软件主要是基于 VC 平台开发的,其中评定算法是利用 Matlab 语言编写并编译成 COM 组件,发布后供上位机软件调用。软件功能组成如图 4 所示。检测软件主要分为三个模块,即数控程序生成模块、数据采集模块以及轮廓误差评定模块。
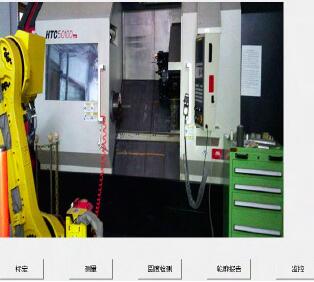
图 4 轮廓在机检测软件界面
2.1 测量程序生成模块
数控程序生成模块主要用于生成实现在机测量的数控程序,并通过以太网下载到数控系统。这里采用灵活方便、易于操作的数控宏程序编程,实现轮廓测量中的简单算术运算、逻辑控制功能[6]。例如,圆度循环测量的宏程序:

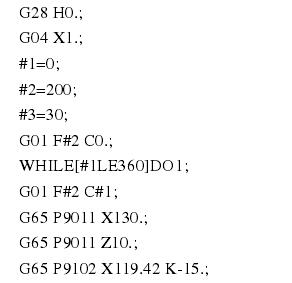
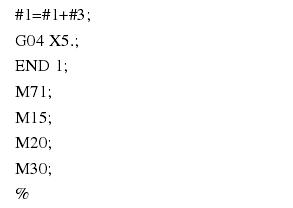
其中 M71/M70 为测头系统的开关指令,M70为开;M21 为由车铣床状态转换,这是因为圆度评定需要在工件圆周上均匀选取 12 个点,C 轴必须可以精确转到指定角度,故应在铣床状态下进行;然后是循环测量,其中 P9011 为安全移动宏程序,P9102 为 X 轴方向单一测量宏程序,我们只需输入必要参数,即可实现我们理想的运动轨迹和要求。测量程序在上位机中生成界面如图 5 所示。
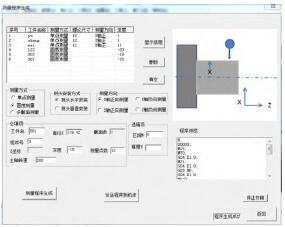
图 5 测量程序生成模块
2.2 数据采集模块
数据采集模块负责对数控系统宏变量的读取和设置,采集并保存测头触碰工件时工件尺寸。为此我们利用 FANUC 系统提供的 focas 函数库,在上位机中基于 VC 平台开发了一个数据采集模块,利用focas 函 数 库 中 cnc_download3(unsigned short Flib Hndl, long *length, char *data) 以 及cnc_rdmacro(unsigned short Flib Hndl, short number, short length, ODBM *macro)函数实现对数控系统内存中宏变量的读写访问,最后保存在数据库中,以便进行处理。具体界面如图 6 所示
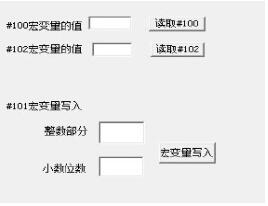
图 6 数据采集模块
2.3 轮廓误差评定模块
轮廓误差评定模块负责对采集的数据分析处理并做出评定,实现对回转型零件轮廓的在机检测。为此我们基于 VC 和 Maltab 平台开发了一个轮廓误差评定模块,用于评定零件的轮廓误差[7]。具体过程是首先利用 Matlab 完成圆度、圆柱度、圆锥度等评估算法程序的编写并编译成 COM 组件,然后利用 VC 调用编译好的 COM 组件完成计算和评估。图 7 为零件轮廓误差评定界面。
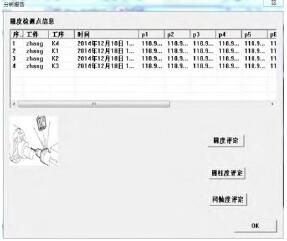
图 7 轮廓误差评定模块
3 、在机轮廓检测的误差分析
在机轮廓检测系统虽然有效的避免了二次装夹带来的误差,但也不可避免的引入了机床、测量装置等硬件的系统误差,因此,采取有效的方式减少这些误差才是保证在线轮廓检测准确性的有效途径[8]。
影响在机测量精度的主要包括机床几何误差、测头安装误差、测头系统误差[9]。首先,对于机床几何误差是由制造、安装不善产生的机床导轨误差、运动部件误差、导轨间位置误差等因素综合影响的,它直接影响着机床坐标系统的精度,是影响在机测量精度的一个重要因素,这部分误差主要由机床本身决定;对于测头安装误差,这是影响测量精度最大的可控因素,因为测头是人为地装夹在刀塔上的,所以为了最大限度的减小测头安装误差的影响,一方面,我们在对刀后,会用千分表校正测头位置,使测头和测杆尽量和 Z 轴重合,另一方面,在执行测量程序前,我们会先运行标定程序,这是由于千分表校正后仍会有误差存在,通过标定程序可以把这些微小误差测量出来,并保存在固定的宏变量里,当执行测量程序时,再通过调用这些宏变量将误差消除掉;对于测头系统误差,这是由其测量原理决定的,由于本测量装置是触发式的,当测头触碰工件后会有一定的预行程,因此,必须保证使每次测量时预行程是相等的,所以标定和测量程序中当测头触碰工件时必须具有相同的速度,以减小测头系统误差的影响。
4 、实例分析
为了验证在机轮廓测量的可行性,我们基于以上设施,设计了如下的车削加工及在线测量实验:首先在车床状态下对工件进行外圆切削,然后在工件圆柱表面上等间距地取四个截面,并在铣床状态下进行轮廓测量。通过使用上位机中的测量程序生成模块生成测量宏程序,并由以太网下载到数控系统内。工件每转 30°测量 1 次,通过上位机软件采集和保存测量结果。程序运行完毕,所得的测量结果表 1 所示。
表 1 测量结果
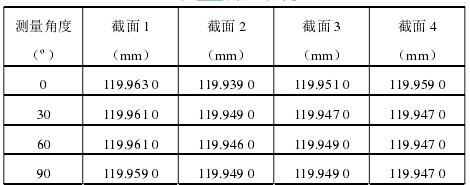
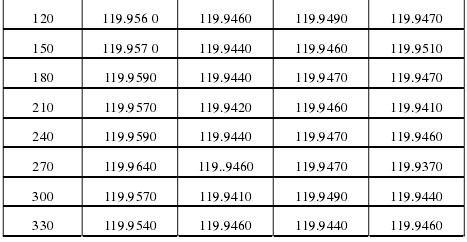
对于以上保存的数据,直接调用轮廓误差评定模块进行处理,结果如下:
表 2 圆度误差评定结果

表 3 圆柱度误差评定结果

表 4 同轴度误差评定结果

5 、 结语
通过在车铣复合加工中心上集成在线测量技术,实现了对回转型工件轮廓的在机测量。虽然文中只是针对圆柱型工件进行的轮廓形状误差评定,但相似的测量过程,配合不同的轮廓误差评定方法,还可以推广应用在凸轮等具有非圆曲线工件的轮廓检测中。相比于离线测量,在机轮廓测量不仅能够避免二次装夹带来的误差,提高测量效率,检测结果还可以快速反馈至数控系统用以补偿加工误差,或者上传至车间层用于生产管理,有利于构建无人化、自动化生产车间。
投稿箱:
如果您有机床行业、企业相关新闻稿件发表,或进行资讯合作,欢迎联系本网编辑部, 邮箱:skjcsc@vip.sina.com
如果您有机床行业、企业相关新闻稿件发表,或进行资讯合作,欢迎联系本网编辑部, 邮箱:skjcsc@vip.sina.com
更多相关信息