伺服驱动加工定位控制方式
2015-2-23 来源: 福建船政交通职业学院机械系 作者:林祥勇
摘 要:针对某模块化生产加工系统生产制造过程中设备定位问题,设计一种采用伺服电机、PLC和触摸屏为主体,可自动测量并显示绝对坐标位置,并自动定位的控制系统。加工重复定位精度可达0.01mm,减轻了工人工作强度,提高了劳动生产率。
0 、引 言
在亚龙公司的335BMPS模块化自动化生产线的生产制造过程中,生产线各单元模块在组装成功后需要放置在生产线的指定位置,该位置的的定位往往是工人根据生产图纸的尺寸进行定位,采用人力搬运并通过人工校准来进行模块单元安装调整,由于系统安装中存在误差,每台生产线都必须通过生产线的单步试运行功能将物料逐一通过生产线的各个单元模块,并再次通过人工调整对单元模块定位微调,从而保证每条生产线出厂的合格性。这就导致调整时间长、效率低,花费大量的时间,并且通过反复调整以提高定位精度,从而使该生产线的生产周期大大延长。同时,在设计上该MPS模块化生产线将机械手固定在导轨的初始点,从而通过伺服电机带动导轨运行达到机械手在各生产线模块之间的往返的目的。在定位精度上如果机械手与单元模块之间的精度一旦出现2mm 以上的误差,在运行时机械手在摆动气缸的作用下必定在90°旋转时碰撞上单元模块的机械部位从而导致事故,因此,在生产过程中的定位又具有至关重要的作用。为减轻工人劳动强度,加快设备精度定位方式,文中在该MPS模块化生产加工系统硬件的基础上,设计了一种采用伺服电机、PLC和触摸屏为主体,可自动定位并显示绝对坐标的定位测试方法,该方法精确度可达0.01mm,减轻了工人工作强度,同时,在生产任务发生变化时更换不同的加工模块也可以实现快速、精准的定位,提高了生产线的生产效率。
1 、MPS模块化生产加工系统及设计思路
目前,浙江亚龙公司的335BMPS模块化生产加工系统将工作单元分别进行检测、加工、搬运、安装、分类等制作过程,各工作单元分工明确又相互协调。MPS模块化生产线加工系统结构如图1所示。
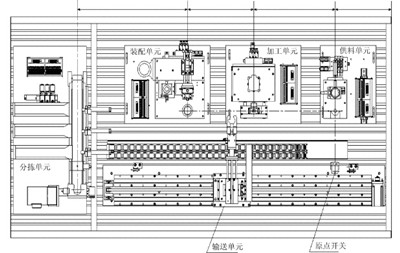
图1 MPS模块化生产加工系统
图中供料、加工、装配等单元分别完成特定生产内容,输送单元负责将原料通过供料单元、加工单元、装配单元进行生产,最后将成品送入分拣单元分拣出合格品。原设计中输送过程系统通过内置程序进行定位目标单元点,利用导轨控制机械手的摆动用机械手抓紧物料将物料放在各模块单元的初始位置,若位置误差略大,则机械手在摆动时必定与模块单元的机械部分之间发生碰撞,造成损伤及事故,因此,各模块单元的初始放置点的定位对精度要求很高。特别在设备的大量生产过程中单纯依靠人工搬运模块单元并进行人动调整,不但对工人熟练度及精细度要求很高,同时也使得劳动强度大大加强。
因此,该自动定位测试方式的思路改变以往让机械手“跟着”单元模块走的定位方式,而改成通过给定机械手位移坐标,根据不同规格的生产线设计要求,当机械手运行到不同单元模块的位置,同时在触摸屏上实时显示机械手的运行位移,再根据机械手的停放位置直接将单元模块进行实时放置,实现一次性定位成功。同时,克服了每台生产线的误差问题可能造成的机械事故,由于机械手的运行通过伺服电机完成,在位置控制上实现定位精度可达0.01mm。
2 、系统组成
系统上采用三菱触摸屏F940GOT-LWD及三菱FX1N-40MTPLC为主控制器 ,并利用触摸屏进行模块单元的位移运行控制,其中三菱PLC为系统核心,完成模拟量输入、开关量输入状态检测、开关量输出控制以及整个系统的过程控制。触摸屏实现人机界面,完成相关数据、信息、状态显示和参数设置,与PLC通信进行数据交换和相关控制。
系统控制电源接通后,首先初始化PLC和触摸屏;然后PLC自动检测系统的启动条件,气压是否达到有效设定值,输送单元是否处于原点,非原点则执行原点返回程序;与伺服通信是否正常,触摸屏通信有无故障,若条件不满足,系统等待并发出报警信号;若启动条件满足,PLC根据位置量要求控制伺服系统运行并将运行位置及运行速度反馈在触摸屏上,通过触摸屏输入不同位置的设定值控制其自动定位。
3、 伺服控制系统
伺服控制系统由伺服驱动器、伺服电机和齿轮传动机构构成,实现对各工作单元及检测装置进行精确定位,是该方法的关键部分。通过伺服驱动器控制伺服电机运行,运行到位后通过PLC实时监测得到的运行距离,即实际测量值与自动计算后得到的脉冲量同时显示在触摸屏上,操作人员根据得到的实际测量值进行模块单元的一次性安装,调整完毕后再进行下一个定位点的自动测试,即使生产任务发生变化,不同的单元模块进行更换,只要将存储器内位移量直接改变即可,方便可靠。同时,伺服系统将定位精度控制在0.01mm。控制模式如图2所示。
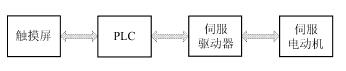
图2 控制模式
在伺服控制中通过原先生产线自带的松下MHMD022P1U 永磁同步的交流伺服电机及MADDT1207003全数字交流永磁同步伺服驱动装置作为运动控制装置。该交流永磁同步伺服驱动器主要有伺服控制单元、功率驱动单元、通讯接口单元、伺服电动机及相应的反馈检测器件组成,其中,伺服控制单元包括位置控制器、速度控制器、转矩和电流控制器等,如图3所示。
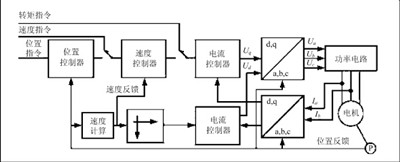
图3 伺服控制单元
根据该伺服控制单元,将机械手需要的位移运行量换算成伺服驱动器接收的脉冲频率,同时,由于对位置和速度的精度要求控制在0.01mm,故使用伺服驱动器位置控制模式,位置控制模式采用位置环、速度环、电流环三环控制结构,PLC给定高速脉冲信号n1送到位置控制器,控制伺服电机运行,即进行直线位移,与通过位置反馈得到的电机实际转动脉冲数n2比较,误差信号Δn=n1-n2,经过位置调节器PID调节后,输出转子转速给定信号m1,实际转子转速反馈信号m2,速度误差信号Δm=m1-m2送到速度控制器,再经过PID调节后输出伺服电机交轴电流信号i1,与实际交轴电流i2比较,得出交轴电流的误差信号Δi=i1-i2,电流控制器输出PWM 控制信号,使伺服电机按给定脉冲数运行,并控制运行精度。位置控制模式下,电子齿轮等效的单闭环系统方框图如图4所示。
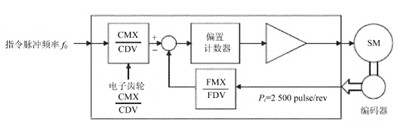
图4 等效的单闭环位置控制系统方框图
图中指令脉冲信号和电机编码器反馈脉冲信号进入驱动器后,均通过电子齿轮变换进行偏差计算。电子齿轮可以用来任意设置每单位指令脉冲对应的电机速度和脉冲当量,由于FX1N-40MT 作为上位控制器最高脉冲输出频率为100kHz,受其限制,使用电子齿轮功能,以减小给伺服驱动器发送脉冲的频率。
对应脉冲计算公式为
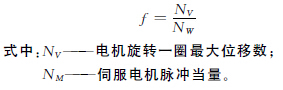
设伺服电机旋转一周移动60mm,松下MINASA4系列AC伺服电机驱动器,电机编码器反馈脉冲为2 500pulse/rev。由于伺服电机脉冲当量为0.01mm,减速比为1,则电机运行一圈所需的脉冲数为:
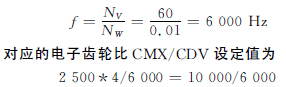
伺服驱动器与PLC及伺服电机的接线图如图5所示。
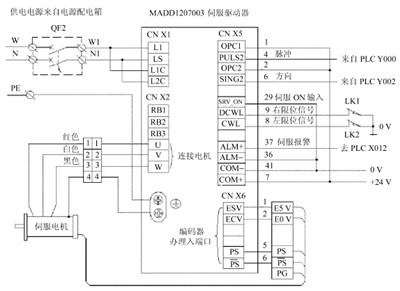
图5 伺服驱动器接线图
4、 系统软件
通过原位行程开关作为原始点定位,通过PLC相关复位程序进行上电初始位置检测,PLC在复位后等待PLC相关检测程序对各输入单元及故障报警进行诊断,并配置报警指示灯。PLC的I/O端口资源分配表见表1。
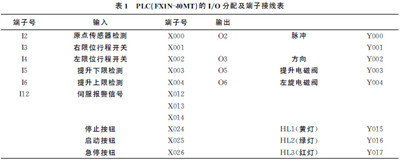
在系统正常运行后,等待触摸屏发出控制指令,通过触摸屏上由调试人员输入运行距离,启动运行按钮,使伺服电机自动移动到目的地。同时,在触摸屏上设置绝对位置位移显示框可以实时得到电机运行的实际距离,从而确定绝对位置的精度,还可以根据需要改变伺服电机的运行速度。所设计的软件流程如图6所示。
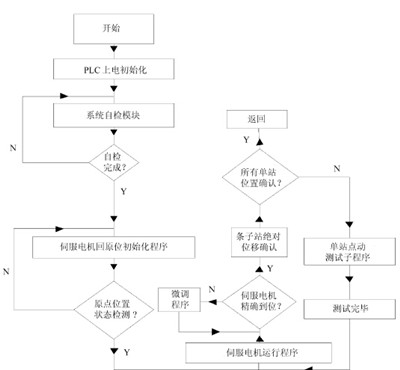
图6 软件流程图
在控制过程中,核心为触摸屏组态程序和PLC控制程序,其中,触摸屏组态程序主要负责实时监控机械手的运行速度、运行距离,并可实时微调。PLC控制程序主要是输出脉冲当量进而通过伺服驱动器来控制伺服电机运行,从而起到精确定位的作用。相关控制程序如图7所示。
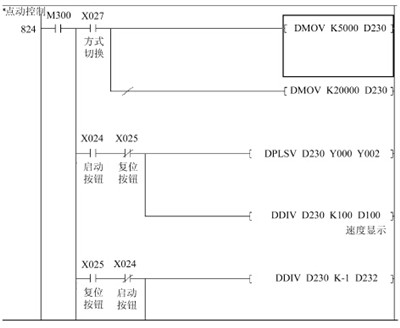
图7 相关控制程序
通过三菱触摸屏设置启动及暂停按钮进行测试控制,并同时在线可看到机械手当前运行位置,使安装人员直接根据系统反馈的位置量进行单元模块的精确定位,避免了系统误差。控制界面如图8所示。
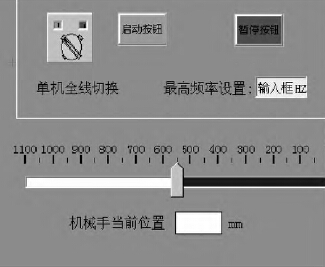
图8 控制界面
5 、结 语
采用伺服电机、PLC和触摸屏为主体,通过系统给定值自动测量并显示绝对坐标值,同时自动定位,并且将定位精度控制在0.01mm;在实际生产过程中,替代原有的人工测量、定位,减轻了设备安装过程中工人反复安装的工作强度,节省安装时间,提高了劳动生产率。实践证明,该方法定位可一次性定位、速度快、精度高,杜绝了机械碰撞损坏等问题,保证系统运行可靠。同时,在类似系列的生产线上都可以通用,且具有易修改、易实现的特点。
投稿箱:
如果您有机床行业、企业相关新闻稿件发表,或进行资讯合作,欢迎联系本网编辑部, 邮箱:skjcsc@vip.sina.com
如果您有机床行业、企业相关新闻稿件发表,或进行资讯合作,欢迎联系本网编辑部, 邮箱:skjcsc@vip.sina.com