电气化设计在数控机床参数调试与日常维修中的应用
2020-12-21 来源:中国航发贵州黎阳航空发动机有限公司 作者:崔红利,吴玉舫
摘要:使用基于微矩阵参数调试方式,缺少对实际机床精度参数考虑,导致参数调试结果并不精准。为了改善该情况,提出了电气化设计在数控机床参数调试与日常维修中的应用。根据不同的控制要求设定CNC参数,确定主轴转速和程序指令转速之间零偏移和增益偏移误差,通过调整该误差,维护CNC。把数控CNC输入的仿真量转化为用于主轴电机上的的实际转速,以使得主轴的实际输出速度可以保持与数控仿真量相同,维护变频器。观察刀具库和刀架的碰撞,确定角度偏差,调整位置编码器方向停止位置和偏移方向停止位置,使其恢复到原来位置,维护主轴。通过修改No.1850(网格偏重)减速块位置参数,维护机床。描述数控机床典型体及其相邻低序几何,确定坐标系中位置姿态,对于数控机床中参数调试误差研究可以转化为坐标系行为研究,由此修正参数调试误差。由实验结果可知,电气化设计方法在静态工作模式下,参数调试方式主轴工作电流与实际电流一致,实际位置跟踪误差为0A;在动态工作模式下,转速与实际转速一致,实际位置跟踪误差为0转/分,为数控机床稳定运行奠定基础。
关键词:电气化设计;数控机床;参数调试;日常维修
0、引言
人们对机械产品的需求日益增长,要求也日益提高。常规加工设备已不适应这种发展需要,因此,数控机床的出现势在必行。以往使用基于微矩阵参数调试方式,需要计算每一参数的灵敏度,但由于未考虑各种参数,如备用电池出现故障,数控系统操作员误操作,电网瞬间断电,造成部分参数丢失或变化,影响机床正常工作,导致实际机床参数调试结果不准确,影响了数控机床的加工精度。如果用户能够充分了解参数意义,将为故障诊断带来极大便利,通过机器电子控制系统实现对机床作业的模拟,为了使操作人员的工作效率变得更加高效,尽心了数字化技术的结合。
CNC机床是一种结合了电、气、机于一体的一体化机器,其最为重要的组成部分是电控系统,一旦电力系统出现任何的问题,机床的工作都会受到影响,无法正常工作。因此在进行对数控机床的日常调试和维护时,机器电子控制系统模拟机床的工作过程,并结合数字技术来提高操作者的工作效率。电控系统是保证CNC机床自动化运行的核心部分,一旦出现故障,将影响CNC机床的正常工作。因此在数控机床参数调试和日常维护中,电气化设计十分必要。
1 、基于电气化设计数控机床参数调试与维护
数控机床参数调试主要包括主轴相关参数和信号调节结果,这对变频器自身参数调试来说具有重要意义。通过调试,确保数控机床能按要求发出正确的模拟电压信号,驱动主轴经过变频调速后能正常工作。
1.1 CNC参数调试与维护
在整个参数调控过程中,CNC参数是按照所需进行设定的,同时需要在主轴转速上显示控制的结果,保证参数与主轴转速输出结果一一对应。以数控车床主轴电气设计为例,进行了仿真分析,设置转速命令输出限值(模拟量)为10V,主轴档位1~3对应的最高转速分别是1500r/min,3000r/min,4500r/min,在数控机床上设定的主轴参数如表1所示。
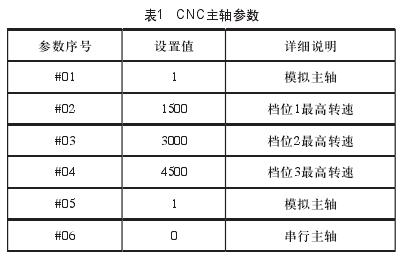
在采用模拟输出主轴的情况下,由于温度和元件特性的变化,实际主轴转速和程序指令转速之间可能存在较大误差。当系统无编程工作时,CNC参数为输出模拟量,此时电压为0V。在完成表1中的参数设置后,可以通过参数#1~#6进行调整。以下是调整的方法和步骤:Step1:测量CNC输出的模拟电压,输入M03S0指令,用万用表测量逆变器两端电压值为-0.20V;Step2:输入M03S4000指令,测得两端电压值为10V,记录数据如表2所示。
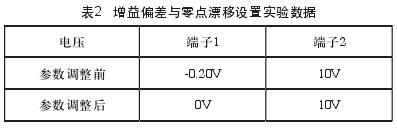
Step3:输入数字#1~#6,使该数字生效,并验证该数字输出的模拟电压;Step4:重复测试1的操作,分别测量速度为0和最高速度的模拟电压,完成参数调整。
1.2 变频器参数调试与维护
在调试变频器参数时,主轴电机的所需要的实际转速是通过对CNC输入的模拟量进行转换得到的,变频器参数调整如表3所示。
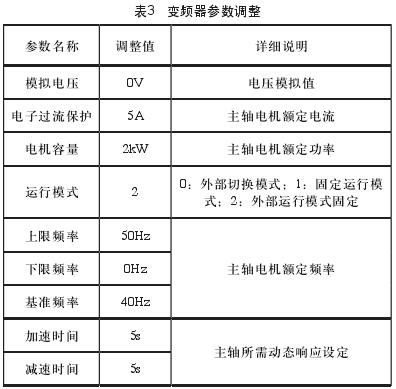
结合表3变频器参数调整结果,需要设定系统运行速度与电流,保证主轴实际输出结果与数控模拟结果一致。
1.3 主轴参数调试与维护
机器刀库为滚筒刀库,不需要机械手来换刀。一般工具更换过程如下:当机床收到工具更换指令后,主轴升至工具更换位置并停止时,“工具更换”程序就会从缸轴向前,并将空鼓的工具位置插入主轴工具箱。在把手凹槽处,用夹紧弹簧夹住滚筒,主轴工具自动夹紧释放机构,松开切削刀,主轴上移,完成切削刀的提取过程;画好切削刀,旋转选择工具[4]。对刀库和刀架进行
了碰撞实验,结果表明,位于刀架上的轴键槽和刀架的关键部分并不在一个位置,而且具有一定的角度偏差,从而引起碰撞。刀架上的键是和主轴的中心在一个水平线上。由此可以推论,刀架的键槽之所以没有匹配刀架的关键位置,是因为主轴的停止位置不在其原本应在的正常位置上,主心轴尚未拆开。因此,对于主轴维护,需要调整主轴的定位位置,使其回到正常的位置。因为方向位置是通过对4031号和4077号两个任何参数进行调整来恢复到之前原本的准确位置,也就是可以排除由于更换机床刀具引起的故障。
1.4 机床参数调整与维护
在CNC数控机床进行减速挡块的调整时,偶尔会有回零的位置不一样的情况。通过观察发现,机床减速在进行参考点返回的时候,出现了一次结果为零的制动过程,但是这往往会导致制动的位置或前或后的出现一个螺距的位移,这也是机床位置编码器发展上的一次改革创新,这可能是因为栅格信号产生的减速信号离开开关太近所造成的。因为传送错误等原因,栅格信号正好漏掉了,必须等待下一个信号到达才能停止,这样就会使停止位置或前或后出现一个丝杠螺距的移动。这样,可通过修改No.1850(网格偏重)减速块的位置或修改信号参数,使网格信号产生时间从减速信号关闭到启动时间,从而避免了这一问题出现。
2 、参数调试误差修正
在参数调试方面,除了用户感觉到的是否达到精度要求外,还需通过模拟处理、误差分析了解使用数控机床调试电气设计参数,以及数控机床主轴加工方向,对于参数均优和参数不优两种情况,需对数控机床主轴加工方向展开分析,如图1所示。
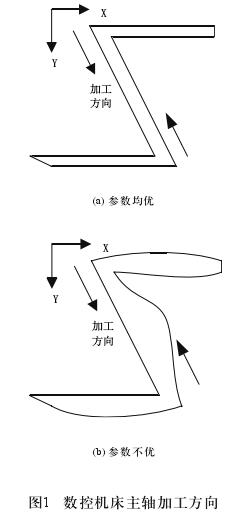
深入研究分析由Z字中选取“\”的笔画,通过加工方向图可发现,X/Y在轴速度为正的时候接收到了同步信号,然而实际模式则是出现在X轴方向的反应比较慢, 而出现在Y轴方向的反应却是正常的,这也就使得开始点与结束点都变成了抛物线形状的斜线。由此可知,确定出口标志的斜线段起点X轴的实际产生的位移值一直比出口标志的斜线段低主要原因,所以需要通过增加X轴的度。
参调主轴参数误差分析时的主要工作是进行确认圆周半径和角度误差的精度是否在所需的范围内,如果半径误差超过了所要求的精度范围时,则需要增加X/Y轴伺服系统的刚度;如果角误差超过精度要求范围的时候,则需要对主刀的升刀延迟时间和刀降的推进时间进行增加,该过程是通过插补控制器完成的,进而使伺服系统位置跟踪精准度得到一定的提升。设数控机床典型体Bk
及其相邻低序Bj,如图2所示

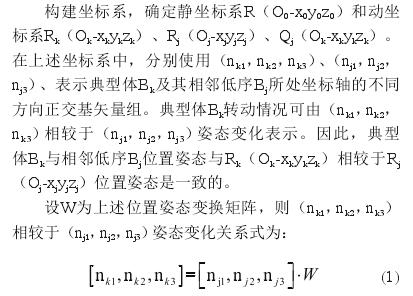
描述了位置姿态变换关系,即为相邻体变换矩阵,对于数控机床中参数调试误差研究可以转化为坐标系行为研究。
在四个象限内分析轴心运动的轮廓误差,如果存在于同一个象限上同一起点的半径误差和半径误差完全一致,而且半径误差在两个不同的象限内,那么X/Y轴的PID参数值保持不变,主轴运动轮廓如图3所示。
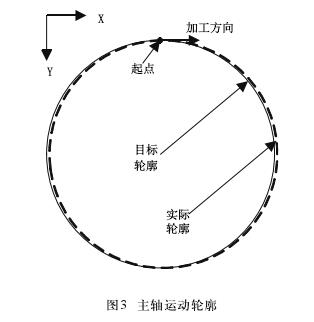
从图3可以得知,当半径误差同时满足在第二象限而且在第一象限的起始点相同时,如果两象限和半径误差大于精度要求,X/Y轴的位置跟踪性能应该进行一定的改善;如果第一象限和半径误差高于精度要求,那么X/Y轴的位置跟踪性能需要进行一定程度上的完善;也可以根据圆口曲线是内、外的圆口曲线还是外的圆口曲线,判断轴伺服系统的软化特性,结合图3中的轮廓轮廓可以看出,X轴的动态性能不良会出现一些偏差,但通过对上述内容进行修正,可以完成参数修正。
3 、实验
针对电气化设计在数控机床参数调试与日常维修中的应用合理性,展开分析。
3.1 模拟主轴系统组成
数控系统模拟主轴控制系统电气化原理图如图4 所示。
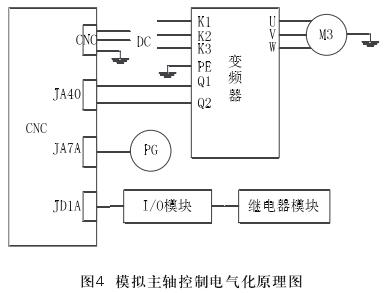
由图4可以得出,CNC数控系统的JA40接口输出电压为0~15V的模拟电压,E700变频器上的两个Q1、Q2子端接收模拟电压信号,该模拟信号是通过JA40接口输出的,由JD1A接口输出的转向信号则由子端接收,JA7A接入由主轴编码器反馈得到的信号。
3.2 数控机床性能调试
对于数控机床性能调试,分别从静态工作模式和动态工作模式两个方面展开。
3.2.1 静态工作模式
当数控机床在静态工作模式下,主轴工作电流和位置跟踪误差如图5所示。
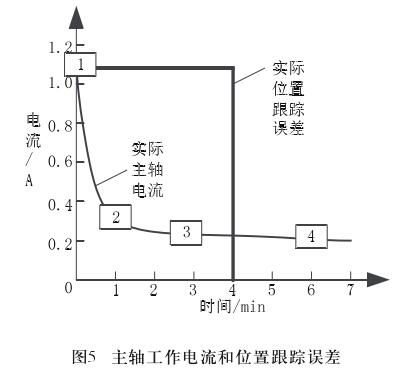
由图5可知,4个特征点下主轴工作电流分别为1.1A、0.3A、0.25A、0.2A,针对这4个特征点的位置跟踪误差电流分别为0A、0.8 A、0.85 A、0.2A。基于该内容,分别使用基于微矩阵参数调试方式和电气化设计参数调试方式对该工作模式下的实际主轴工作电流和位置跟踪误差展开分析,结果如表4所示。
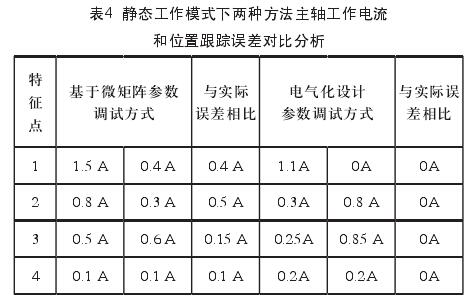
由表4可知,使用基于微矩阵参数调试方式主轴工作电流与实际电流相差较大,其中实际位置跟踪误差最大为0.5A,而使用电气化设计参数调试方式主轴工作电流与实际电流一致,实际位置跟踪误差为0A,由此说明,当数控机床在静态工作模式下,电气化设计参数调试方式合理。
3.2.2 动态工作模式
当数控机床在静态工作模式下,实际转速和位置跟踪误差如图6所示。
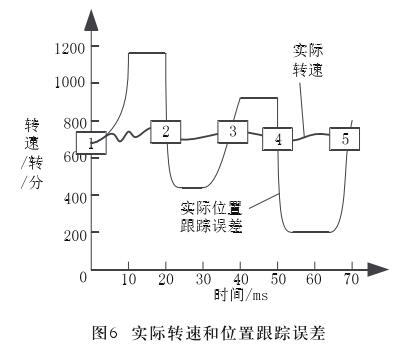
由图6可知,5个特征点下实际转速分别为700转/分、750转/分、740转/分、680转/分、680转/分,针对这5个特征点的位置跟踪误差转速均为0转/分。基于该内容,分别使用基于微矩阵参数调试方式和电气化设计参数调试方式对该工作模式下的实际转速和位置跟踪误差展开分析,结果如表5所示。
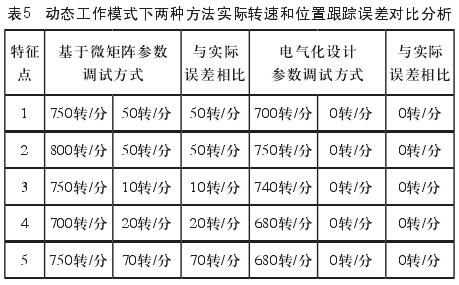
由表5可知,使用基于微矩阵参数调试方式转速与实际转速存在一定偏差,其中实际位置跟踪误差最大为70转/分,而使用电气化设计参数调试方式转速与实际转速一致,实际位置跟踪误差为
0转/分,由此说明,当数控机床在动态工作模式下,电气化设计参数调试方式合理。
4 、结语
主轴控制系统的调试是数控机床调试的重点,若输入的指令和主轴的实际转速不符,且在进行零件加的时候误差较大,就需要对主轴进行调试。因为电气化设计在进行参数调试的时候主要侧重于对主轴主轴控制系统的硬件组成进行模拟和调试,缺乏分析了解数控机床软件的功能部分,所以今后可以在调试过程中总结和积累更加丰富的经验,进而完善和提高在调试和维修方面的技能。
投稿箱:
如果您有机床行业、企业相关新闻稿件发表,或进行资讯合作,欢迎联系本网编辑部, 邮箱:skjcsc@vip.sina.com
如果您有机床行业、企业相关新闻稿件发表,或进行资讯合作,欢迎联系本网编辑部, 邮箱:skjcsc@vip.sina.com
更多相关信息