基于ANSYS的移动机器人底盘结构稳定性分析
2017-3-24 来源:上海大学 作者:高慧慧, 鲍晟,洪银芳
摘要:以移动机器人自动打铆系统为例,运用 UG 软件对麦克纳姆轮式移动机器人底盘结构实体建模。 利用 ANSYS Workbench 软件分析底盘结构在四轮同时着地、单轮悬空和机械手臂末端反冲力 3 种工况下的静态特性,得出不同工况下载荷分布对底盘结构稳定性的影响,为后续优化设计提供重要依据。
关键词:移动机器人 底盘结构 有限元分析 稳定性
随着工业化的快速发展, 对于机器人技术的应用研究越来越受到人们的重视和关注。 全方位移动机器人是机器人家族中灵活性更好、自主性更强、智能化更高的一员,在加工制造领域获得越来越多关注[1]。 麦克纳姆轮式全方位移动机器人具有平面内的全部自由度, 能够实现横向、 纵向的平移和绕任意中心点的旋转,可以在狭小空间灵活运动到达目标位置[2]。 与其它全方位移动机器人相比, 麦克纳姆轮式全方位移动机器人在移动精度和承载能力等方面具有明显的优势,适用于工业应用需求。通过在麦克纳姆轮式全方位移动机器人平台上添加相应的操作臂[3],增加了系统的柔性和适应性 ,可以进行搬运、打铆、装配等工作,同时也对机器人的承载力、移动稳定性和精确定位方面提出了更高要求。
底盘结构是移动机器人最重要的承载部件, 承受着复杂的空间力和力矩作用[4]。 为确保移动机器人的移动精度和运行性能, 有必要采用有限元法对该底盘结构进行静态稳定性分析[5],以验证其可靠性 ,并为结构优化设计提供参考。
笔者基于 ANSYS Workbench 软件,分析底盘结构的静态特性[6],通过分析底盘结构在四轮同时着地 、单轮悬空、机械手臂末端反冲力 3 种工况下的稳定性,得出不同工况下载荷分布对其稳定性的影响, 并加以校核与优化改进, 使其满足麦克纳姆轮式全方位移动机器人的精度和稳定性要求。
1.移动机器人及底盘结构
麦克纳姆轮式全方位移动机器人由动力机构、底盘结构、升降系统、底盘、三点支撑等组成。电机驱动克纳姆轮, 减速电机调节速度, 底盘结构支撑整个车体,升降系统由螺旋升降组件提供动力,实现平台的升降,底盘辅助支撑起到加工时稳定车体作用。
移动机器人底盘作为麦克纳姆轮式全方位移动机器人的支撑机构,主要由两组对称主梁、两对侧梁以及上部结构安装板组成,如图 1 和图 2 所示,其结构强度直接影响全方位移动机器人的移动精度和运行性能。
2.移动机器人底盘结构模型建立
采用有限元软件建立底盘结构三维模型[7], 底 盘材料选取 Q235A。在 ANSYS Workbench 中对底盘模型进行自动划分网格,单元格平均质量为 83,满足有限元分析的要求,划分结果如图 3 所示。
3.移动机器人底盘结构稳定性分析
对底盘结构的稳定性分析分为 3 种情况[8]:4 个轮子同时着地、单轮悬空、机械手臂末端反冲力的影响。
3.1 4 个麦克纳姆轮同时着地工况分析
在 ANSYS Workbench 中对底盘结构施加载荷,可将底盘受力看作恒等静态载荷, 对其支撑面施加力约束,主要包括机器人自重(约280 kg)、电池自重(约150kg)、控制箱自重 (约 150 kg)、螺旋升降机构和其它辅助机构质量( 约 60 kg,对底盘应变影 响 微 小 ,分析时可忽略其大小)。施加载荷的相应位置分别如图 4 中的 B、C、D 所示。
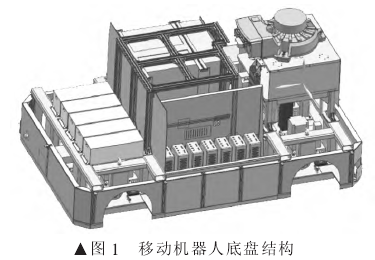
在相应平面和轴上施加约束条件[9]:对 4 个麦克纳姆轮支撑平面进行固定约束和无摩擦约束, 施加位置如图 4 中 A;在 ANSYS Workbench 中进行计算,得到该工况下的等效应力和位移云图, 得出底盘结构的最大应力、最大位移变形和位置,如图 5 所示。
由 图 5 可 见 ,底盘结构等效最大应力为 216.8MPa, 发生在底盘中间横梁处 ; 底盘最大应力变形为2.575 mm,发生在底盘中间横梁位置靠近前轮处 ;可以得出该工况下最大应力小于材料屈服强度 235 MPa,符合设计和使用要求。
3.2 单轮悬空工况分析
在路面不平时车轮会出现单轮悬空状况, 难以保证底盘结构的强度、精度和运行性能,因此有必要对该工况进行分析[10]。 底盘结构呈左右对称布置,分别以底盘右后轮、右前轮悬空两种工况为例分析。
(1) 右后轮悬空工况。 底盘右后轮悬空时,在右后轮处不加任何约束, 对其余 3 个麦克纳姆轮施加固定约束和无摩擦约束; 在 ANSYS Workbench 中分析计算,得到此工况下的底盘结构等效应力和总变形云图,如图 6 所示。 底盘等效最大应力为 260 MPa,发生在底盘 中 间 和 前 两 轮横梁处,大于材料的 屈 服 强 度 235MPa,所以该工况比较危险 ,需要添加加强筋和横梁减小应力分布。 底盘最大变形为 2.88 mm,发生在不受约束的右后轮处。在底盘结构后续的优化时,需要添加横梁或者改变尺寸减小变形。
(2) 右前轮悬空工况分析。 底盘右前轮悬空时,在右前轮处不加任何约束, 对其余 3 个麦克纳姆轮施加固定约束和无摩擦约束;在 ANSYS Workbench 中分析计算, 得到该工况下的底盘结构等效应力和总变形云图,如图 7 所示。 底盘等效最大应力为 255.03 MPa,发生在底盘中间和左前轮横梁处, 大于材料的屈服强度235 MPa,因此该工况会 引起底盘的破坏 ,需要添加加强筋来减小应力分布。 底盘最大变形为 4.35 mm,发生在底盘中间横梁处和不受约束的右前轮处。 对底盘结构后续的优化,应该改变尺寸或者添加横梁减小变形。
综上所述,得出不同工况下的分析结果:从图 8 可知, 全方位移动机器人在路面状况良好时能够正常工作,查阅设计手册可知,结构强度满足使用要求;在单轮悬空时受力不理想, 底盘结构出现较严重的扭转变形,应尽量避免这种情况。
4.机械手臂末端反冲力对底盘稳定性的影响
以机器人钻铆加工应用为例,在钻铆过程中,机械臂末端反冲力引起的力和力矩对底盘结构的稳定性会造成影响,因此,分析机械手臂反冲力的影响也是至关重要的[11-12]。
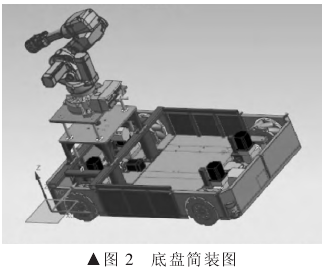
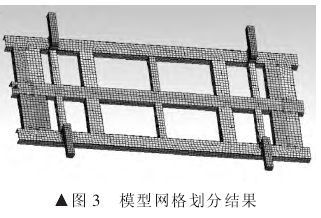
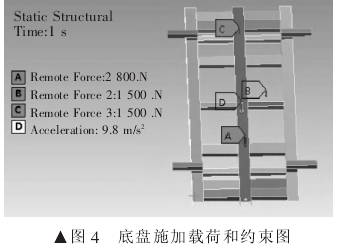
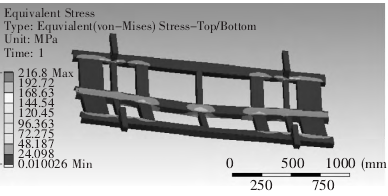
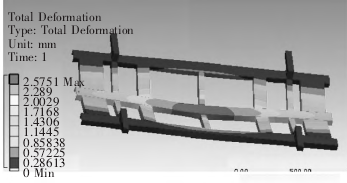
图 5 底盘结构等效应力和总变形云图
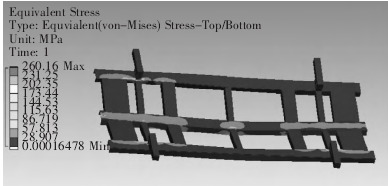
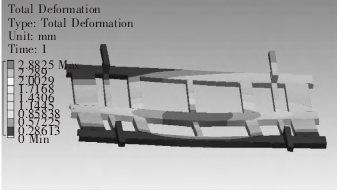
图 6 底盘结构等效应力和总变形
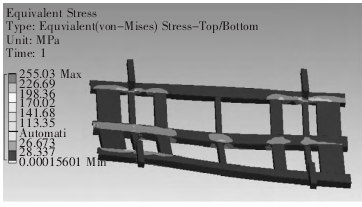
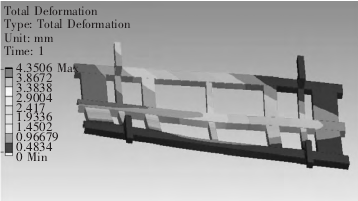
图 7 底盘结构等效应力和总变形云图
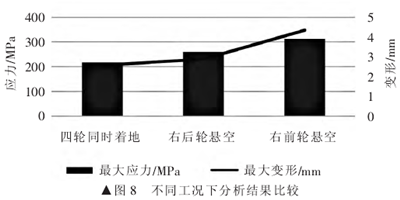
以移动工业机器人自动打铆系统为例, 根据机械臂型号和铆枪型号,由实验估计机械手臂反冲力在30~5 000 N 范围内变化,机器人手臂末端距离底座高度约为 1 300 mm, 可以计算出反冲力引起的附加力矩在39~6 500 N·m 范围内变化。
分析最大反冲力 F=5 000 N 对移动机械手臂底盘结构稳定性的影响。 经 ANSYS Workbench 分析计算,得到底盘结构的等效应力和总变形云图,如图 9 所示。危险位置发生在底盘中间横梁处, 底盘等效最大应力为 243.63 MPa,大于材料的屈服强度极限 235 MPa,底盘结构严重扭转变形。 底盘最大变形为 0.866 mm,发生在底盘中间横梁并靠近后轮位置。
由实验数据得出结论: 当机械手臂末端的反冲力小于 5 000 N 时, 底盘结构的应力和位移变形满足强度要求;当反冲力大于 5 000 N 时,底盘结构出现严重扭转变形,稳定性受到严重影响,全方位移动机器人不能正常工作,需要对底盘结构进行后续的优化与改进。
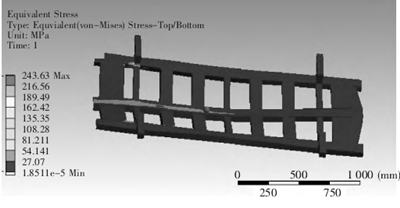
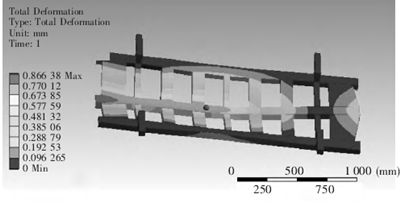
图 9 底盘结构等效应力云图和结构总变形图(F=5 000 N)
5.总结
分析了底盘结构在四轮同时着地、 单轮悬空和机械手臂末端反冲力 3 种工况下的稳定性, 得出最大应力和最大变形的位置,理论分析结果与实际情况相符,验证了有限元分析的正确性。实验证明,该底盘结构的强度和变形完全符合实际要求, 单轮悬空工况由于会导致较大扭转形变,应尽量避免;根据本文分析的数据以及最大应力及变形的位置, 为后续底盘结构的优化设计与完善提供了重要依据; 对后续的移动机械臂系统的关键结构的优化分析提供了借鉴和保障。
投稿箱:
如果您有机床行业、企业相关新闻稿件发表,或进行资讯合作,欢迎联系本网编辑部, 邮箱:skjcsc@vip.sina.com
如果您有机床行业、企业相关新闻稿件发表,或进行资讯合作,欢迎联系本网编辑部, 邮箱:skjcsc@vip.sina.com
更多相关信息