数控车床梯形螺纹的加工方法及改进研究
2021-5-25 来源: 常州科技经贸技工学校 作者:陈 静
摘要:本文以梯形螺纹 Tr36×6 的加工工艺作为研究对象,针对梯形螺纹的结构参数与直进法、斜进法、左右切削法、直槽法、阶梯槽法、分层切削法等加工方法进行详细分析,并以常规加工方法存在的刀具磨损、排屑困难、生产效率低等工艺缺陷作为切入点,探讨了实现高转速粗车加工与低转速精车加工两道工序间良好衔接的具体方法及程序设计思路。经多次调试与验证后发现,以每分钟 560r 的转速进行粗车加工,再将转速下调至每分钟 25r 进行精车加工,即可实现对梯形螺纹的变速加工,且保障梯形螺纹工件的质量达标,有效提高生产环节的效率,为梯形螺纹副的批量化生产创设有利条件。
关键词:数控车床;梯形螺纹;变速车削
梯形螺纹主要应用于传动机构中作为传导螺纹,梯形外螺纹与内螺纹以成对方式呈现,具有牙型深、螺距较大等特征,在采用数控车床进行加工时易产生较大的切削力与振动问题,加剧刀尖磨损程度、易引发扎刀事故,影响到工件的质量与加工生产进度。基于此,本文拟针对梯形螺纹的常规加工工艺进行改进,并通过程序调试确保工艺具备可行性。
1 、梯形螺纹结构与加工方法
1.1 梯形螺纹
1.1.1 基本结构
选取一对典型梯形螺纹副作为参照,在该梯形螺纹副的左上方、右上方分别设有螺杆和螺套,两类零件的外形、尺寸与螺纹精度将直接决定零件能否正常旋合。以梯形螺纹 Tr36×6 为例(各结构的参数如表 1 所示),其牙型呈等腰梯形、牙型角为 30°,相较于其他螺纹在牙根强度、对中性上占据良好性能优势,其公称直径为 36mm、螺距为6mm。
左旋螺纹需在尺寸规格后加注“LH”,右旋螺纹则不标出。为保障梯形螺纹质量达标,应在加工环节确保牙型的准确度,使螺纹中径与基准轴保持同轴,以中径尺寸定心,在车削加工环节注意控制好中径的尺寸公差与两侧表面粗糙度。
表 1 梯形螺纹的结构及计算公式
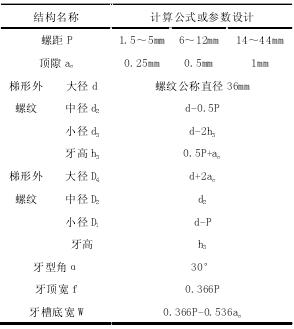
1.1.2 车刀材料
在车刀材料选取上,主要选用硬质合金刀片进行梯形螺纹的高速车削,考虑到数控车床存在较严格的加工标准,因此选用材质为 YT15 硬质合金的可转位机夹刀片,保障刀片在硬度、耐磨性与使用寿命等方面具备良好的性能优势。在车削加工环节,应注重选用标准刀片,在安装刀具时控制主切削刃与工件轴线保持等高且平行,利用样板进行找正与纠偏处理,使刀头角平分线与工件轴线呈垂直关系,并且将车削深度控制在与牙型高度一致的位置,确保中径尺寸达标。
1.2 加工方法
1.2.1 直进法和斜进法
直进法指车刀沿水平方向间歇进给至牙深部位,考虑到在车削梯形螺纹需利用车刀三刃同时切削,由此将产生较大的切削力、加剧刀具的磨损情况,并且无法保障及时排屑,易出现扎刀问题。斜进法指以牙型角方向为基准,将车刀沿斜向间歇进给,能够有效减少切削力及产生的排屑量,但针对螺距较大的梯形螺纹进行加工时,仍面临刀具磨损与牙型角存在偏差等问题,缺乏良好适用价值。
1.2.2左右切削法
该方法指以牙型角反向为基准,将车刀错位进给、实行单刃切削,借此有效规避多刃切削引发的扎刀问题,既有助于提升螺纹的车削精度,同时也可优化梯形螺纹表面质量,但也存在编程复杂的问题,无法保障加工效率
1.2.3 直槽法和阶梯槽法
采用直槽法进行螺纹加工,应确保切槽刀的刀头宽度不超过牙槽底宽,以小径为参考沿横向直进切至指定的直槽深度,并且留足 0.2mm 余量,随后改用梯形螺纹刀沿斜向进行加工。该方法将数控编程进行简化,但同样不适用于大螺距的螺纹加工,影响到排屑效果,加之刀头较长影响到梯形螺纹刀的强度,极易在加工过程中产生刀头折断的问题。
采用阶梯槽法进行加工时,通常需先完成牙槽的分层,控制切槽刀沿左右方向移动切削出阶梯槽,再改用梯形螺纹刀沿斜向进行加工。该方法具有良好的排屑效果,可实现梯形螺纹的批量化加工,但在将切槽刀更换为梯形螺纹刀时无法保障刀体对准螺旋直槽,易引发倒牙问题。
1.2.4 分层切削法
该方法主要将直进法与左右切削法进行整合,先利用切槽刀将牙槽划分为多个梯形槽,再依照直进、左右移动的顺序进行各层梯形槽的车削加工。该方法适用于大螺距的梯形螺纹加工,能够有效提高车削质量与效率,避免产生扎刀问题,并且可采用宏程序进行编程处理,在梯形螺纹任意结构参数发生变化的条件下仍可保障螺纹加工精度。
2 、数控车床变速车削梯形螺纹的加工流程优化设计
2.1 常规加工方法存在的缺陷
过针对四类梯形螺纹车削加工方法进行综合分析,提炼出保障螺纹质量的最优方法的基础上,还应基于生产效率与加工精度层面进行工艺流程的创新。
通常利用数控车床以高转速车削梯形螺纹时,往往面临螺纹表面粗糙度不达标的问题,同时多个刀刃将产生较大的切削力与振动效应,易缩短切槽刀的使用寿命;在以低转速车削梯形螺纹时,往往导致生产效率大幅下降,并且当速度骤然变化时易引发螺纹乱牙问题。
基于此,本文拟采用变速车削这一新型加工模式,首先利用粗车刀以高转速进行工件外形的车削,保障工件的大径、中径和小径数值均符合标准值要求;随后再改用精车刀以低转速进行工件的精车、修光处理,确保牙型角、牙顶宽与牙槽底宽等指标均符合要求。
在此过程中,需注意控制好高转速、低转速与粗车、精车间的衔接过渡,保障梯形螺纹的加质量。
2.2 变速车削加工方法的应用
2.2.1 加工方案分析
基于GSK980TD 数控车床进行梯形螺纹 Tr36×6 的变速车削加工方案设计,考虑到该梯形螺纹的螺距为 6mm、保持中等水平,因此可选用斜进法与左右切削法配合加工,基于 G76 指令进行切削加工,依次完成粗车、精车环节的编程设计,注意留足余量。
2.2.2变速车削加工程序设计
在粗车前,首先以 X 方向为基准留出精车余量 X0.5,将车床转速设为每分钟 560r 的高转速水平,待完成粗车后倘若直接将转速调低进行精车,极易产生牙槽乱牙问题,并且易引发撞刀、刀片折断等问题,因此需重点做好粗车后的速度调节与工序控制。
粗车程序设计如下:
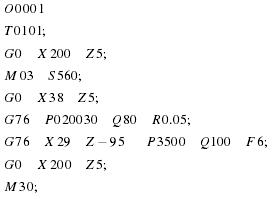
在粗车完成后,首先将粗车刀停放的位置设为 X200 Z5,随后进入对刀界面在磨耗栏中输入 U8 刀补,使坐标系上的原点朝 X 轴右侧移动 4mm 的距离,此时刀尖较先前提高约一个 h3的距离;随即将数控车床的转速降低至每分钟 25r,再次运行粗车程序,在此环节精车刀将位于靠近梯形螺纹表面的平面移动,确保不会接触到梯形螺纹表面。
此时观察梯形螺纹车刀可发现,车刀所处位置较牙槽存在一定的偏移,应通过调试使车刀重新回到牙槽内,在此可将粗车程序中的起始点 Z0 调整为- 1,再次运行粗车程序,并同时校对车刀与梯形螺纹槽间的偏差值,调整至二者保持完全对正为止。
接下来需针对偏移后的坐标系进行调整,在对刀界面磨耗栏内输入 U- 8 并执行程序,即可使坐标系重新恢复至粗车加工模式下的坐标系,随后再次运行粗车程序,倘若发现精车刀在车削加工过程中触碰到牙槽,则需重新进行梯形螺纹的粗车加工,直至精车刀与牙型保持一致、无表面接触为止。
最后需针对梯形螺纹的小径尺寸进行调节,选用左右切削法进行切削调试,确保精车螺纹两侧面的偏移量符合标准件设计要求;通过进入对刀界面调整磨耗栏中的 U 值,即可实现对中径、小径等尺寸的精确调整,并配合三针测量法进行测量,计算得出梯形螺纹左右两侧面的偏移值均为 0.26mm,确保最终加工出的梯形螺纹工件尺寸与精度达标。
2.2.3 调试结果
通过针对变速车削加工的程序与具体参数进行多次验证,最终确定标准化加工方案,即先以每分钟 560r 的高转速运行粗车程序、完成粗车加工,再将转速调整至每分钟 25r的低转速水平,将定位坐标调整为 G0 X38 Z- 1.8,运行精车程序、利用精车刀进行工件左右两侧面的精修处理,最后针对中径、牙顶宽、牙槽底宽等指标进行测量,以此判断加工精度是否符合质量要求,提升梯形螺纹加工效率。精车程序设计如下:
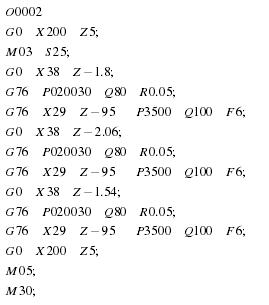
2.3 工艺优化的注意事项
在采用数控车床变速车削工艺时,还应注意以下问题:首先是在切削过程中需补充足量切削液,在刀头处增设顶尖,用于防止切削刀具在车削工件环节产生大幅振动,保障梯形螺纹副表面具备良好的粗糙度,并且在数控车床执行车削作业过程中做好操作人员的安全教育工作,禁止采用棉纱擦拭工件表面,避免引发安全事故或设备损坏问题。
其次应注意在精车前做好中心孔的修正工作,针对螺纹同轴精度进行严格校正,并且做好精车刀质量的检查,确保两侧刃磨平直且锋利,保障后续加工环节的精车质量。
再次是在车削加工梯形螺纹的过程中,应尽量调低切削用量,防止在后续切削环节因疏于管控造成工件变形问题;在装夹工件环节,应注意控制好尾座套筒的伸长量,避免因套筒过短导致车刀退刀环节尾座碰撞床鞍。
最后还应加强对梯形螺纹技术参数的把控,例如检查梯形螺纹的中径是否与基准轴位于相同轴线上,中径尺寸公差是否符合设计标准,大径尺寸是否控制在标准尺寸以内,梯形螺纹牙型角是否为 30°,梯形螺纹左右两侧的表面粗糙度数值是否达标等。在利用数控机床加工梯形螺纹时,还应注意做好机床设备刚度、工件与刀具材料等指标的调节,并针对编程进行精细化设计,实现工艺优化目标。
3 、结论
当前在采用数控车床进行梯形螺纹加工环节,常面临粗加工吃刀深、切削余量大、生产效率低、表面粗糙度大以及编程复杂程度高等问题。对此需针对一般加工方法做出改进,引入变速车削工艺进行加工方法的优化,做好粗车与精车加工衔接环节转速的调节、实现平稳过渡,避免刀具触碰工件表面影响到加工质量,并完善程序设计与调试工作,保障提升梯形螺纹加工精度与效率,实现零部件批量化生产目标
投稿箱:
如果您有机床行业、企业相关新闻稿件发表,或进行资讯合作,欢迎联系本网编辑部, 邮箱:skjcsc@vip.sina.com
如果您有机床行业、企业相关新闻稿件发表,或进行资讯合作,欢迎联系本网编辑部, 邮箱:skjcsc@vip.sina.com