大口径光学元件的精密磨抛与检测装备开发及应用
2020-3-4 来源: 厦门大学微纳米加工与检测联合实验室 作者:郭隐彪,彭云峰,王振忠,毕果等
摘要:大口径光学元件超精密加工是一个复杂的系统性工程,涉及精密机床、数控、加工技术与工艺、精密检测和补偿控制等机电控各领域的专业知识,其发展与一个国家的高端制造技术及装备发展能力息息相关,也是一个国家综合国力的集中体现。主要介绍了厦门大学微纳米加工与检测联合实验室在大口径光学元件超精密加工技术及装备方面取得的研究进展,针对大口径光学元件磨削和抛光两个加工流程及其配套的精密检测技术,详细阐述了磨削装备及单元技术、可控气囊抛光机床及相关单元技术、精密检测装备及相关单元技术等的研究应用情况。这些技术研究从超精密加工的需求出发,借鉴国内外的研究经验和成果,通过对装备、工艺、检测等各方面整合,形成了具有自主知识产权的集磨削、抛光和检测装备及工艺技术的大口径光学元件超精密加工体系,这些技术与装备确保了大口径光学元件的高质量超精密加工。
关键词:大口径光学元件;超精密加工;磨削加工装备;气囊抛光;精密检测;磨床
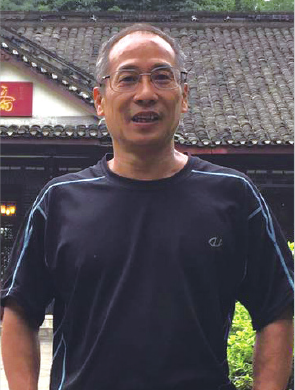
郭隐彪博士、教授、闽江学者特聘教授
主要研究方向为光学超精密加工、先进装备开发与研制。
光学自由曲面如非球面等具备优越的光学性能,在同等功能要求条件下,可获得成像质量更优、结构更简单、成本更低和重量更轻的仪器,是航空航天和军事国防领域不可或缺的关键基础元器件,广泛应用于大型天文望远镜、激光核聚变装置、红外热成像、医疗影像设备等民用和国防尖端技术领域。在国家大光学工程任务以及光电子消费产品需求日益增长的牵引和推动下,其加工技术日益要求向高效、高精度、高质量方向发展。大口径光学元件超精密加工技术不仅取决于机床、刀具和工艺方法,还取决于测量和控制技术,即含机、光、电、传感技术和计算机技术等,它是多种学科新技术成果的综合应用,但也对许多高新科技的发展与进步起着推动的作用。大口径光学元件的加工是衡量一个国家先进制造技术水平和综合国力的重要标志,西方国家在该领域一直对我国实行技术禁运。因此,开展光学元件超精密加工技术的研究有助于确保我国重要技术安全,我国“十二五”发展规划中尤其做出了相关的指示,即《国家中长期科学和技术发展规划纲要》中关于“关键基础件制造和批量生产的关键技术为制造业的第一优先主题”的精神。
大口径光学元件超精密加工,一般需要经过粗磨、精磨、抛光和镀膜等工序,以提高工件面形精度,降低粗糙度和亚表面缺陷。这些工序中,大口径光学元件的精磨与抛光加工尤其重要,在很大程度上决定了大口径光学元件的加工质量水平,其中,精密磨削基本确定了大口径光学元件的面形精度,同时为降低后续的抛光工作量,精密磨削过程中需尽量减少在光学元件表面形成过多的缺陷与破坏,而抛光加工是获取超光滑低缺陷损伤光学表面的必要保证,因此,从保证大口径光学元件加工质量的角度,精密磨削与高精度抛光手段是相辅相成,必不可少的,而高精度的机床装备则是实现精密磨削与抛光的前提保证。受技术瓶颈限制,当前的硬件设计和开发很难开发出绝对高精度的机床装备,且代价太高,导致精密磨削与抛光加工大口径光学元件的同时不可避免地形成较大的加工误差。
为获得更高精度和质量的光学元件,必须进一步补偿加工以提高光学元件的加工质量。而目前国内的光学测量与检测装备适应范围有限,一般口径较小且成本高昂。同时,作为获取光学元件的加工尺寸与质量信息的必要手段,大口径光学元件测量装备与评价技术的开发也同样重要。可以说,精密磨削与抛光装备是获得高精度大口径光学元件的制造手段,而其精密检测装备与评价技术则是整个加工过程顺利进行的保障,三者缺一不可,都构成了大口径光学元件精密制造的必然环节。因此,加强大口径光学原件精密制造的研究,必须三管齐下,唯有攻克并掌握三者的技术瓶颈,才可真正实现并确保大口径光学元件的精密制造加工。
在激光核聚变和空天望远镜等大型光学工程项目的驱动下,西方发达国家,如美、日等国在大口径光学元件的超精密制造技术已取得了重大进展。装备方面,美国 Livermore 国家实验室开发了 LODTM 单点金刚石切削机床,可加工 Φ1400mm 的光学元件,面形精度可达 PV ≤ 0.025μm,表面粗糙度 Ra≤ 5nm。英国 Cranfield精密工程研究所研制的 OAGM2500超精密磨床,可加工 Φ2000mm 的非球面光学元件,面形精度 PV ≤ 1μm。日本丰田工机研制的 AHN60-3D 复合机床,磨削加工的非轴对称光学元件 PV 为 0.35μm,表面粗糙度 Ra为0.016μm。加工方法与工艺技术方面,为获得高质量的光学元件表面形貌,日本理化所的 Ohmori 等提出了 ELID在线电解磨削方法,可实现光学元件的镜面加工。
在光学表面完整性控制方面,基于小工具加工的数控抛光技术(CCOS)、应力盘抛光技术、气囊抛光技术、磁流变抛光技术和等离子体法等技术均可有效去除亚表面损伤层,并能有针对性地改善工件表面质量和面形精度。这些先进的超精密加工技术,基本上解决了大口径光学元件加工问题,但是国外发达国家对我国进行严格技术和设备禁运,造成我国大口径光学元件超精密加工技术发展落后。
同时,国内也充分意识到了大口径光学元件在民用和国防军事等领域应用的重要性,明确了加强大口径光学元件精密制造研究的必要性,并在相关项目的驱动下加紧了相关加工技术及装备开发等各方面研究。装备方面,中航精密机械研究所研制了 Nanosys-300 超精密复合加工机床,哈尔滨工业大学研制了大型曲面超精密复合加工机床,均可实现光学非球面的加工。国防科技大学研制的光学数控加工机床(AOCMT),最大加工能力为 650mm,对直径 116mm 的碳化硅零件,铣磨成型的精度为 8.9μm,研抛后工件面形精度 PV 为(1/20~1/30)λ,表面粗糙度 2~5nm。厦门大学研制了大尺寸矩形光学平面精密磨床。加工工艺方面,厦门大学开发了光学非球面的计算机辅助制造工艺软件。
光学完整性控制方面,国防科技大学开展了计算机数控抛光技术(CCOS)的研究,哈尔滨工业大学、国防科技大学和中物院等单位均开发了磁流变抛光机床,哈尔滨工业大学、浙江工业大学和厦门大学等研究了气囊抛光技术并试制样机。此外,厦门大学还开展了光学精密加工环境控制方面的研究,拟通过非硬件途径弥补硬件缺陷以提高光学元件的加工精度。
目前,在先进军事及空间光学系统、激光核聚变、大型天文望远镜工程等国家重大光学工程任务的需求牵引下,我国大口径光学元件制造和检测技术得到了快速发展。就其关键工艺路线的装备保证方面而言,实现大口径光学元件超精密加工的前提基础是要具备高精度磨削与抛光加工设备,而大尺寸的高精度磨床与抛光装备开发技术一直被公认为是要持续发展的技术、不可公开的技术和不可复制的技术,因此,高精度的磨削与抛光及其配套的检测设备仍是制约我国超精密加工技术发展的瓶颈。而且,实现大口径光学元件的超精密加工,除了高精度磨抛装备之外,还需要一系列关键的配套单元技术,这些配套技术包括:超精密磨抛加工工艺与技术、机床精度整合技术、超精密环境监控技术、工具修整和动静平衡技术、计算机辅助制造和检测软件 , 以及检测路径规划和对应的补偿加工策略。
基于大口径光学元件的发展需求,厦门大学微纳加工与检测联合实验室课题组长时间以来深入地开展了大口径光学元件的精密磨抛装备、加工工艺技术及计算机辅助制造软件、配套的精密检测装备与工艺等方面的研究,并取得了较突出的科研成果。本文以大口径光学元件加工的关键磨抛工序为主要论述对象,介绍了厦门大学课题组在实现大口径光学元件高精度、高效率与高度自动化精密加工的装备开发及相关单元技术方面的研究情况。大口径光学元件精密磨削机床及单元技术大口径光学元件一般采用脆性材料,且具备较大口径和复杂面形等特点,这为其精密加工带来了较大的困难和挑战。
目前,硬脆性材料大口径光学元件的精密加工步骤和程序一般为先毛坯铣磨加工去除多余的材料,然后粗磨到一定面型精度,再通过精磨加工得到满足其设计面型精度的半成品,最后再抛光去除表面 / 亚表面损伤层获得超光滑的光学表面,整个加工过程较为复杂,需通过精密的工艺控制和检测及补偿加工实现。因此,为满足大口径光学元件的精密加工,具备高刚度和高精度及稳定性等性能特点的机床不可或缺,其中大口径精密磨床则首当其冲。目前,在精密磨床制造方面,美国、日本、英国和德国等工业发达国家在国际上享有极高声誉,代表产品如:英国 Granfield 大学精密工程研究所研制的 OAGM2500 六轴数控超精密磨床,可用于超精密车削、磨削和坐标测量;日本 Nagasei 公司拥有 SGC/SGE/N2C/NIC/RG 等系列的超精密磨床,可用于各种尺寸的非球面(自由曲面)、平面超精密镜面加工;除此之外,Moore 公司的 Nanotech、Precitech 公司的 Freeform 系列、德国 Satisloh公司开发的 GII 系列、保宁机床公司的 ProfimatMT 系列和瑞士美盖勒机床公司的 MFP 系列也达到了很高的加工精度。国内方面则稍显落后,厦门大学微纳米加工与检测联合实验室以国外先进的制造技术为借鉴,从我国大口径光学元件超精密加工需求出发,研制了多台大口径高精度卧轴矩台平面磨床,本文将以开发的一台 2MK7160 平面磨床及其单元技术为例进行说明。
1 、大口径精密磨床的方案设计与样机研制
为确保开发的大口径平面磨床具备结构简单、总体刚性好、磨削效率高等性能特点,研发首先通过综合分析,将机床的整个开发工作分解为关键部件、关键技术、辅助配套与电气及数控系统等部位进行模块化研究。机床整机确定为立柱移动式数控卧轴矩台平面磨床结构,外围加钣金全防护罩防护。改变传统平面磨床导轨结构形式,床身底座采用 T 形布局和分体铸件形式,提高工艺合理性。采用人工时效与自然时效相结合的办法来保证基础大件的长期稳定性。采用数字化设计和工程分析对设计方案进行充分论证,进行整机方案的结构静力学和动力学设计和分析,保证样机整机性能。为提高工艺系统刚性,采用液体动静压轴承支撑的砂轮主轴,实现高回转精度和运动平稳性,各轴传动系统由伺服电机带动高精度滚珠丝杠,XY 方向采用液体静压导轨,并通过纳米级分辨率的线性光栅构成全闭环控制回路,导轨采用拼块结构,工艺性更加合理、刚性足,能实现高加工精度,从而保持高直线运动精度和高刚性。数控系统选用PANUC 31i 高端系统,基于 windows操作平台,操作简单、灵活,易掌握。
磨床的辅助系统包括冷却系统、过滤装置、润滑系统,油水雾净化装置等。其中关键配套技术均为自主开发,砂轮修整采用绿碳杯形砂轮修整方法并开发专用修整器,工件检测以机床运动带动高精度接触式 /非接触式传感器实现,加工控制与工艺技术融合进计算机辅助制造软件开发中,采用工作流设计方法,实现人与机床活动的自动化处理,采用视图 / 文档的设计模式,实现数据处理和用户界面的分离。基于工控机的软件开发模块包括工件检测、砂轮修整、加工监控,动平衡等系统。砂轮修整采用两轴精密杯形修整技术可保证金刚石砂轮形状精度和平面、圆弧砂轮修整,实时现场动平衡检测,减少主轴系统引入误差,从而提高工件加工精度。加工监控消除机床振动影响,最大限度地消除加工表面 / 亚表面损伤。采用高压冷却水带走磨削过程中的磨削热量和切屑,提高加工表面性能,并采用油雾净化器消除雾化的磨削液以净化机床加工空间。同时独立于高精度设备、技术人员及技术水平之外的外部环境的加工环境控制技术,保证高精度加工不受环境限制,最终实现了精密温控系统、多层次消振技术、超精密净化相关技术。设计后的磨床参数为:工作台加工范围 800mm×600mm,各轴分辨率0.1μm,主轴采用动静压支承技术,最高转速 3000r/min,X 轴移动速度最大 20m/min,Y、Z 两轴移动速度最大 5m/min,数控系统采用 FANUC 31i 系列,砂轮修整器采用 GC 杯形砂轮修整器。图 1 为设计开发的2MK7160 大口径卧轴矩台平面磨床。
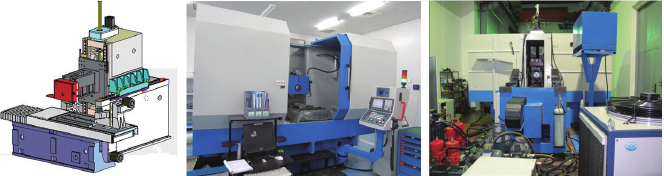
图1 大口径卧轴矩台精密磨床2MK7160及其辅助配套系统
2 、液体静压支承技术
液体静压具备动静摩擦系数相差级小、运动平滑、高刚度、可吸收振动、承受大负载和动态响应快等特点,为保证工艺系统的刚度和运动精度,磨床采用了闭式的液体静压支承技术,并开发了拼块式静压导轨结构,该结构简单且刚性好,极大地降低了常用闭式静压导轨的加工和装配调试难度,且拆装更为方便。开发的拼块式导轨技术首先应用于第一台开发的 MK7160 大口径平面磨床的水平 X 轴上,并在成功后将其首次应用于 2MK7160 大口径磨床的垂直Z 轴上,研究发现应用于垂直 Z 轴上的拼块式导轨支承性能良好,优于传统的接触式导轨结构。图 2 是开发的拼块式液体静压导轨结构及应用实例。
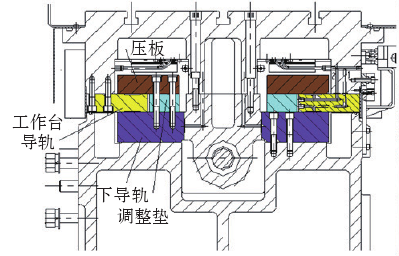
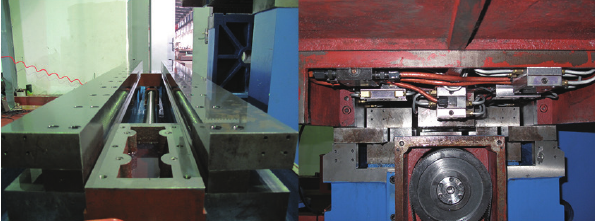
图2 拼块式液体静压导轨
3 、砂轮修整技术及装置
光学元件一般为硬脆性材料,加工难度大,砂轮极易磨损而丧失加工能力。为保证金刚石砂轮磨粒尖锐性和面型精度,必须开发适应用于圆弧金刚石砂轮的修整技术,从而实现圆弧金刚石砂轮的修形和修锐以保证其加工能力。课题组提出了如图 3 所示的圆弧金刚石砂轮的杯形圆弧包络修整方法,通过杯形砂轮的包络运动实现圆弧金刚石砂轮的修形和修锐。技术的实施上,机床提供修整运动所需的横向往复运动和金刚石砂轮主轴的回转运动,修整装置提供杯形砂轮的摆动、修整进给和杯形砂轮回转运动。修整过程中,杯形砂轮上脱落的磨粒将对金刚石砂轮磨粒与结合剂产生冲击和研磨作用,从而完成对圆弧金刚石砂轮的修整。辅助工艺与系统方面,开发集砂轮面形精度测量、误差建模、半径补偿、修整工艺等关键单元技术在内的杯形砂轮包络修整计算机辅助加工软件,并可实现圆弧金刚石砂轮修整装置与机床的多轴联动控制。圆弧金刚石砂轮的杯形砂轮包络修正方法及装置的开发,极大地保证了圆弧砂轮的加工性能并提高了其加工效率。该修整技术的最大特点是其修整的对象不局限于金属结合剂圆弧金刚石砂轮,也适合于树脂结合剂砂轮和陶瓷结合剂砂轮的修整。
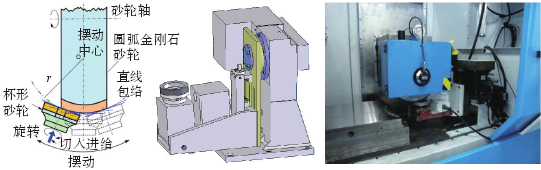
图3 2轴杯形砂轮修整装置
4 、计算机辅助制造(CAM)软件
大口径非球面属于典型的面型复杂工件,加工难度较大,磨床各运动轴需协同控制运动才可完成。此外,机床机械系统特性均存在一定极限,在其性能不能进一步改善时,则需通过工艺的优化。为保证磨削的加工精度同时保证充分发挥数控磨床精度特性,需根据不同类型工件和具体磨床结构方式,选择合理有效的加工工艺和加工规划,优化磨削加工参数以提高面形精度和减小磨削亚表面损伤。其中加工补偿控制方法是关键。为此,课题组提出了一系列的非球面面型插补方案和控制策略,并对其进行优化,建立了基于误差检测评价数据的建模补偿技术;同时为延缓砂轮磨损,保证砂轮的加工能力,深入分析了圆弧砂轮的磨损机制,针对性地提出了砂轮均匀磨损与速度控制技术,有效提高砂轮寿命;针对非球面加工中的圆弧半径误差,提出分离检测误差成分并进行补偿加工以提高加工精度;为提高砂轮修整效率,提出砂轮修整参数优化技术。基于上述的工艺优化方案,合理制定了加工工艺,配合计算机技术,特别是利用计算机辅助制造和测量,实现对加工过程信息自动处理及控制,提高加工过程自动化和加工效率;并研究数控伺服系统及微位移控制,进行不同工件加工方法分析、轨迹规划及编程优化,确保加工中对机床的正确使用、数控加工特点的发挥和工件的加工精度。
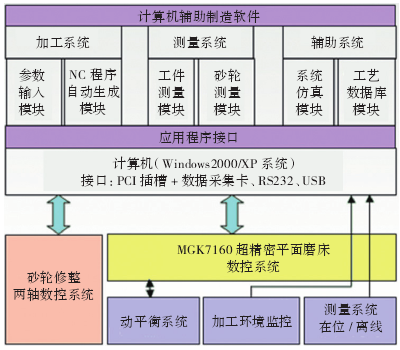
图4 大口径非球面精密磨削加工计算机辅助制造软件
如图 4 所示是课题组开发的用于实现超精密磨削的计算机辅助制造(CAM)系统软件,其功能模块包括磨削加工、面形测量、磨削补偿、面形拟合和环境监控等,辅助制造系统软件的应用可使整个磨削过程更加高效、便捷。CAM 软件的开发可使大口径光学非球面的精密磨削加工数控编程自动化,同时集成了磨削加工过程关键技术,包括工艺分析设计、参数输入、加工轨迹数学处理、程序编制、工件测量、砂轮修整、加工监控、机床通信等功能模块,各功能模块的联系和功能如图5 所示。

图5 计算机辅助制造软件功能模块关系图
光学元件可控气囊抛光机床及单元技术
硬脆性材料在去除过程中,极易发生脆性断裂破坏从而使加工表面较为粗糙。常规而言,大口径光学元件在精密、超精密磨削成形加工后常需进行抛光等光整加工,目的是去除前道工序形成的表面变质层和损伤,并使工件表面超光滑化。但抛光加工易破坏工件的面型精度,因此常需采用后续的修正抛光加工以获得高面型精度的大口径光学元件。传统的光学元件面形修正方法由于加工周期长、面形收敛慢等缺点很难适应现代光学系统的发展需求,故出现不少先进的现代抛光方法,例如小磨头数控研抛、应力盘抛光、离子束抛光、磁流变抛光和可控气囊抛光等确定性抛光技术。
在新出现的几种确定性抛光技术中,小磨头数控抛光是采用最广泛的一种。该技术具备可抛光修正复杂自由曲面工件面型的优点。为降低抛光盘与工件表面间干涉对工件精度的影响,小磨头数控抛光的工具尺寸一般较小,导致其在采用规律性的加工路径时易在元件表面形成中高频误差。美国亚力桑那大学提出的应力盘抛光技术能克服这个问题,但其修形能力较弱,控制复杂,且小磨头和应力盘均属于接触式加工方法,加工中盘面和元件的接触易导致元件发生弹性形变使元件面形难以加工到较高精度。离子束抛光技术虽可实现局部修正抛光加工,但是其抛光效率极低,且对加工环境要求极高,成本高昂。相比之下,磁流变抛光和可控气囊抛光技术属于柔性抛光技术,能够实现很高的加工精度,但磁流变抛光成本很高,导致其很难应用于凹曲面以及大口径高陡度工件的加工。基于上述分析,课题组有针对性地开发了可控气囊抛光技术及其机床。
1 、可控柔性气囊抛光机床的开发
柔性气囊抛光技术首先由英国伦敦光学实验室的 Walker 教授提出,后由英国 ZEEKO 公司开发成系列的产品。课题组在消化吸收其产品的基础上,开发了国内首台可控柔性气囊抛光机床及单元技术。如图 6 所示,气囊抛光机床整体采用龙门结构,分别由工作台底座、立柱横梁、中溜板与主轴箱结构组成。两气囊抛光机床的核心部件,在结构设计中不仅要保证整个机构的运动精度还要为满足附加功能而预留足够的位置空间。气囊抛光采用进动式的加工方式,即抛光加工过程中气囊主轴始终与工件局部法线成固定的进动角。为了方便控制气囊自转轴的空间位姿,两轴气囊抛光工具由两个旋转轴 Z1和Z3来控制气囊主轴 Z2在空间位姿的变化,同时两轴气囊抛光工具的 Z1、Z3和 Z2轴相交于气囊头的球心。通过对运动空间的理论分析计算当 Z1轴和 Z3轴在空间成 45°时,即整个机构的空间角度为 45°,整个气囊抛光工具的空间运动范围与刚度最合适。
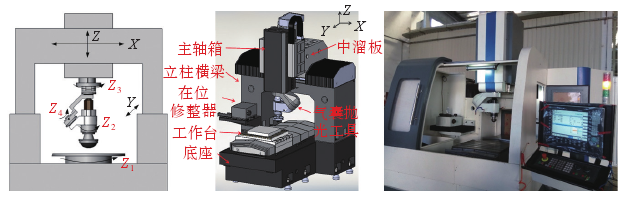
图6 可控气囊抛光样机模型和实物图
2 、柔性可控气囊设计及其修整技术
为避免刚性抛光头损伤自由曲面面型,气囊抛光机床采用具有一定充气压力的球冠形气囊作为抛光工具,这样不仅可以保证抛光头与被抛光工件表面吻合性好,而且可以通过调节气囊内部压力控制抛光效率和被抛光工件的表面质量。为此,柔性气囊抛光方法是一种极具发展潜力的抛光方法,尤其适用于非球面和自由曲面的抛光。柔性气囊抛光加工采用一种独特的进动运动方式,即抛光过程中,气囊自转轴始终与工件局部法线呈固定角度 ( 称进动角 ) 进行抛光,通过特定的加工轨迹与路径控制,可以在接触区形成杂乱的加工痕迹,生成接近高斯分布的去除函数,这种加工方式有助于降低抛光表面中频误差的形成,正是基于这个特点,气囊抛光加工技术具备广泛应用于大口径自由曲面元件的去中频误差修正加工。
为确保气囊加工可适用于不同的加工对象,课题组研究了不同结构形式的气囊抛光头,以获得不同变形模式和刚度的抛光头,包括纯橡胶气囊头、内置钢网橡胶气囊头和内置薄钢板气囊头等多种形式,并有针对性地研究了各种气囊头的变形特性和去除函数。图 7 所示是其中开发的内置钢网的柔性气囊抛光头。
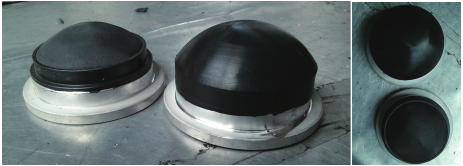
图7 设计的柔性气囊及其结构
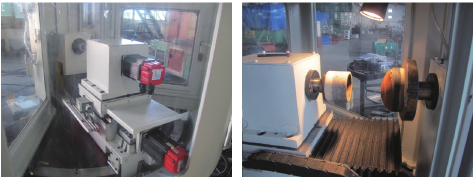
图8 离线气囊修整装置
为了进一步提高加工效率,减少气囊抛光头修整耗时,课题组将气囊头修整工序分离,设计并增加了离线气囊修整装置,开发了如图 8 所示的离线气囊修整装置,该装置由底座、摆动电机、摆动底座、摆动导轨、进给电机、导轨、砂轮底座、砂轮主轴电机、修整砂轮、抛光头电机、防护装置等部分组成。摆动电机固定在底座的底部,通过减速机与摆动底座相连,导轨固定在摆动底座上,进给电机与进给主轴通过导轨带动砂轮底座完成进给运动,砂轮主轴电机通过联轴器带动修整砂轮旋转,完成修整砂轮的运动。抛光头部分底座通过螺钉固定在底座的一端,气囊抛光头由皮带轮与抛光头电机带动旋转。
在气囊头离线修整加工中,气囊头的修整由橡胶气囊头的旋转、砂轮主轴的旋转、进给轴进给运动和摆动轴的摆动运动共同完成。同时,在防护罩的顶部安装有气囊头动平衡装置,检测气囊头在旋转过程中的振动与转速,方便对气囊头的平衡调整,提高修整精度。
3 、气囊抛光仿真与运动控制软件
为确保气囊抛光加工可实现预期功能,课题组充分研究了可控气囊抛光的加工机理,将试验与仿真相结合,确定不同工艺条件对抛光接触区的影响,以及不同条件下气囊抛光的静态和动态去除函数,并研究了基于去除函数的抛光驻留时间算法。在研究基于运动学理论的气囊抛光过程中进动控制方法的基础上,得出最高效的进动控制算法。研究特别对连续进动抛光模式下的气囊加工进行了深入的研究,尤其在压力控制和位姿控制的基础上分别研究了如图9 所示最优效率算法、刚度可控算法和四轴联动控制算法等,并在此基础上编制了柔性气囊可控抛光的仿真与运动控制软件,该软件具备手动和自动控制两种模式,如图 10 所示为开发的软件界面。该仿真与运动控制软件极大地方便了气囊抛光的运动规划和运动控制,有效地促进了气囊抛光加工的高度自动化。
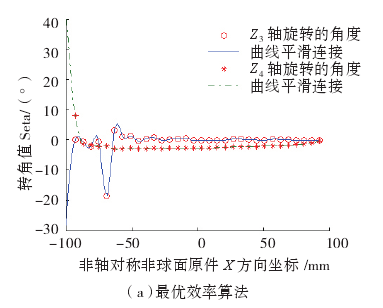
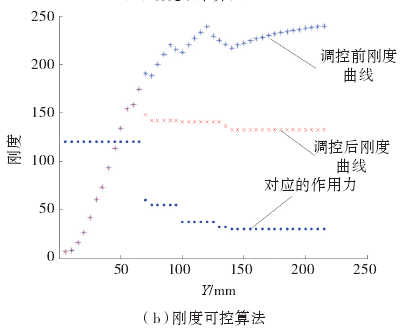
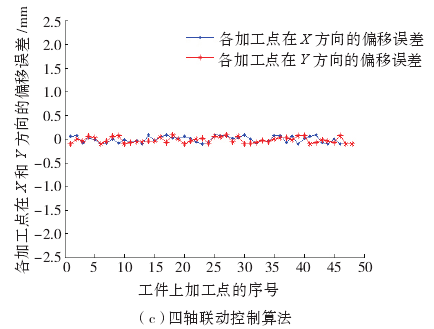
图9 开发的几种气囊抛光控制算法
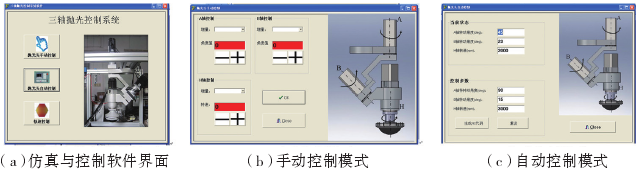
图10 气囊抛光的仿真与运动控制软件界面
大口径光学元件精密检测装备及单元技术
大口径光学元件的加工一般经历铣磨、磨削、抛光 3 个阶段,为保证每道工序的加工余量和精度,每个加工阶段都需要匹配对应的精度测量检测技术。大口径光学元件的加工过程中,磨削加工阶段主要是为了获得较为接近设计要求的形状精度,该阶段获得的面型精度将在很大程度上决定后续面型收敛加工的工作量,因此其面型精度的检测至关重要。一般而言,大口径光学非球面磨削加工阶段面型误差检测装置的精度要求介于数十微米到亚微米之间。基于此,课题组有针对性地开发了大口径光学元件面型误差的检测技术。图 11 所示是课题组开发的在位检测系统,该检测系统将激光位移传感器放置于磨削主轴上,利用磨床各轴的运动完成大口径非球面元件的面型检测,可实现大口径光学元件的全口径测量。该种检测方式属于在位式的,其特点是可以避免工件离线测量引入装夹、定位等误差,实现对工件加工表面精度进行测量,并可为补偿加工提供加工误差数据。图 12 所示为利用在位检测系统检测大口径非球面光学元件初始加工和补偿加工后的面形精度图,经过 3 次补偿加工后面形精度 PV 值由 7.77μm 下降到4.67μm。
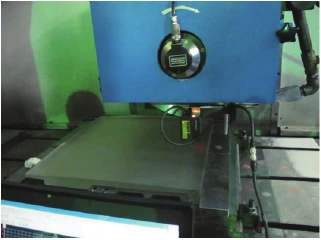
图11 在位检测系统
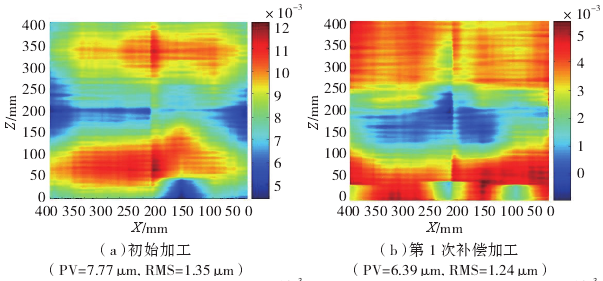
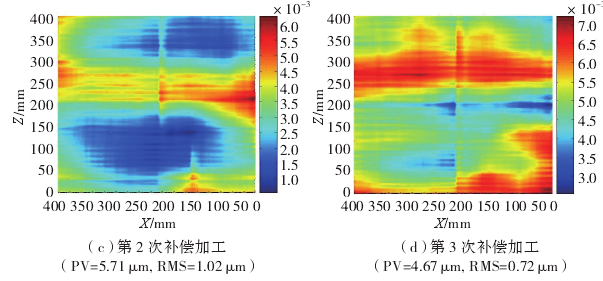
图12 初始加工的补偿加工面形精度
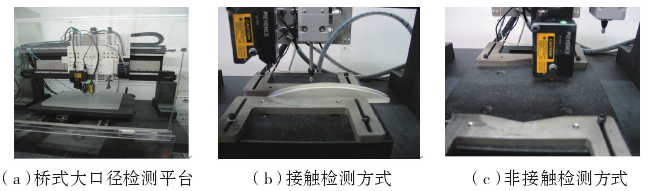
图13 大口径光学元件检测装置
此外,课题组还分别开发了中大口径(200mm×200mm)和大口(400mm×400mm)光学元件的三维轮廓测量离线精密检测平台。图 13为其中的大口径离线精密检测平台,该平台采用固定桥式结构,XYZ 轴行程分别为 400mm×400mm×150mm,各轴定位精度为 ±1μm,整体设计测量精度目标为 ±3μm。检测平台采用一种上下位机的多 CPU 结构,上位机实现系统管理、数据处理及人机界面等功能。下位机由运动控制和数据采集两个模块组成,实现实时的运动控制和数据采样、分析及处理功能。平台采用接触式和非接触式双探测系统,可针对不同工件需求实现工件面形数据的实时采集,采集后的面形原始数据通过相关数据拟合算法和误差分析,可拟合出实际加工后的工件面形,将拟合后的工件面形与理想的非球面面形比较,从而求出非球面面形误差和各种像差等参数,为后续加工提供加工补偿数据。
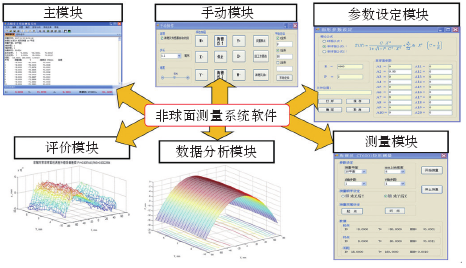
图14 非球面检测软件及功能模块
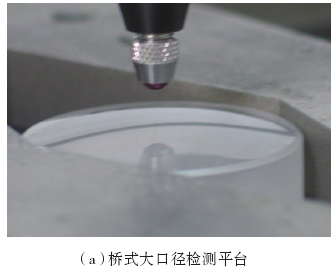
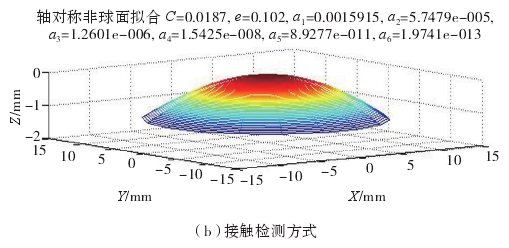
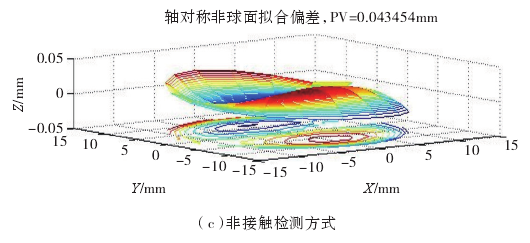
图15 非球面光学元件的检测结果
为使检测平台在大口径非球面元件检测中更为便利,课题组还开发了适应于大口径非球面元件检测的非球面测量系统软件,该软件包含如图 14 所示的参数设定模块、测量模块、数据分析模块和评价模块,具备非球面顶点查找、定位误差补偿、直线度与垂直度和平面度误差补偿、测杆变形误差补偿等功能,该软件设有手动和自动两种工作模式。图 15 是利用开发的大口径光学检测平台和软件测量得到的非球面光学元件面型及拟合偏差。该检测装置和配套软件的开发成功地为大口径光学元件的精密加工提供了强有力的精度测量和补偿加工保证。
结论
大口径光学元件的精密制造加工属于一个复杂的综合性系统工程,其精密加工涉及难加工材料的去除机理与控制、精密超精密机床开发、数控技术、精密检测、加工工具及修整、材料、加工状态及环境控制、误差评价及补偿和加工技术与工艺等方面,其中的每一项均是一个重要的研究方向,对其深入系统的研究任重而道远。在相关大光学工程项目的资助下,厦门大学微纳米加工与检测联合实验室在大口径光学原件的精密制造与检测装备方面进行了较多的探索,取得了一些实用的科研成果,主要体现在:
(1)开发了“T 型”布局的大口径四轴精密磨床,该机床采用液体静压支承导轨、动静压主轴及动平衡技术,配置针对圆弧金刚石砂轮修整的杯形砂轮修整器,针对大口径非球面光学元件的精密加工需求,开发了与该磨床配合使用并包含多个关键单元功能模块的计算机辅助制造(CAM)系统。
(2)开发了大口径柔性气囊抛光机床,抛光机床采用 AB 摆五轴构,“T”型龙门布局,抛光头采用柔性气囊结构,具备压力和姿态控制两种加工模式。研究设计了多种抛光加工路径与驻留时间算法,并开发了精密抛光机床的计算机辅助抛光(CAM)系统。
(3)研制了中大口径光学非球面检测平台,测量平台具备接触式与非接触式两种测量工具与手段,并开发了大口径非球面的测量与评价软件,该软件具备自动测量、数据分析、评价和补偿等功能,可实现较高精度大口径非球面的精密测量与评价。综合分析当前的技术发展现状可见,虽然我国已经能加工出较高精度的大口径光学元件,但相比国外先进水平仍然存在较大的提升空间,未来需要相关部门与研究机构及高校创新性的探索研究相关新加工技术与方法、新的工艺、新的检测技术,以期在此基础上实现大口径光学元件的高精度与高质量加工,确保我国相关大工程项目和国防军事等领域的建设与实施。在相关高端装备及数控领域方面的攻关工作,也将帮助我国最终突破国外技术封锁,全面提升我国的精密制造技术及其装备水平,确保我国的技术安全。
投稿箱:
如果您有机床行业、企业相关新闻稿件发表,或进行资讯合作,欢迎联系本网编辑部, 邮箱:skjcsc@vip.sina.com
如果您有机床行业、企业相关新闻稿件发表,或进行资讯合作,欢迎联系本网编辑部, 邮箱:skjcsc@vip.sina.com
更多相关信息