插床导杆机构的优化设计与运动仿真
2018-8-24 来源:转载 作者:周 琦,张惜君
摘要: 对插床导杆机构的工作原理和运动过程进行了分析,运用动力学仿真软件 ADAMS 对导杆机构进行了参数优化设计,优化了导杆机构的几何参数,改善了其综合运动性能。利用 Pro /E 和ADAMS 软件建立优化后机构的虚拟样机,对优化结果进行了仿真验证。
关键词: 插床; 导杆机构; 优化设计; 运动仿真
插床是一种具有急回特性的金属切削机床,广泛用于加工键槽、花键槽、异形槽和各种异型表面。在对插床进行设计、制造时,要使插刀在进给过程中尽可能地平稳,以保证加工零件的表面质量; 插刀快退时尽可能减少空行程时间,提高插床工作效率。要实现插刀的平稳运行,了解执行机构结构参数对其运动特性的影响,仅凭理论计算和经验往往难以实现。ADAMS 软件是美国 MDI 公司开发的机械系统动力学仿真分析软件。设计人员可在该软件的交互式图形环境下建立或导入机械产品的虚拟样机,再对虚拟样机进行静力学、运动学和动力学仿真分析,输出位移、速度、加 速 度 和 反 作 用力 曲线。ADAMS 软件的仿真可用于预测机械产品的性能、运动特性等,目前已广泛应用于工业领域的机械产品研发中。本文对插床中导杆机构的设计进行了研究,分析其工作原理,设计计算导杆机构的几何参数,对导杆机构进行了运动学分析。利用 ADAMS 软件对导杆机构的关键点坐标进行以加速度为优化目标的参数化设计研究和优化设计,实现了导杆机构结构尺寸的最优化设计。
在此基础上返回 Pro /E环境中修改相关零件的结构尺寸,使之与优化后的参数对应起来,再导入 ADAMS 软件中进行仿真,验证了优化设计改善机构性能的可行性。虚拟样机技术在插床设计中所显示出的优越性,为进一步提高插床的工作质量提供了新的设计思路和方法.
1 、导杆机构原理及运动分析
1. 1 导杆机构工作原理
导杆机构是插床实现插削运动的一个关键机构。导杆机构由机架 1,齿轮 2 和 3,滑块 4 和 7,导杆 5,连杆 6 组成,机构运动简图如图 1 所示。图中齿轮 3 为原动件,当齿轮 3 旋转时,通过滑块 4带动导杆 5 围绕 C 点作往复摆动,导杆 5 通过连杆6 带动滑块 7 上下来回移动,从而完成切削过程。
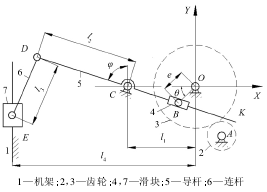
图 1 插床导杆运动机构简图
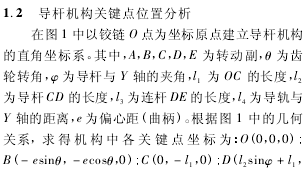
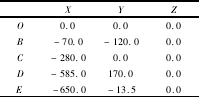
表 1 各关键点的坐标
表 1 中机构的各关键点坐标已知,且 Z 轴坐标均为 0,故该机构为平面运动机构,由此各构件的相互位置及尺寸基本确定,为后续在 Pro /E 环境中进行导杆机构的虚拟样机设计打下了基础。工程实践证明,在传统设计过程中理论设计计算的结果与实际值或多或少都会存在一些误差,虽然这些误差可以通过物理样机的调试试验进行消除,但也使得产品的研发周期变长,成本增加。
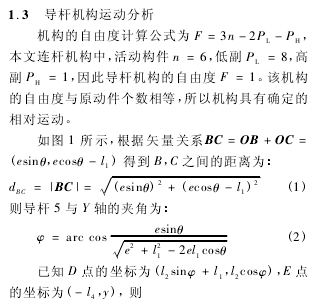
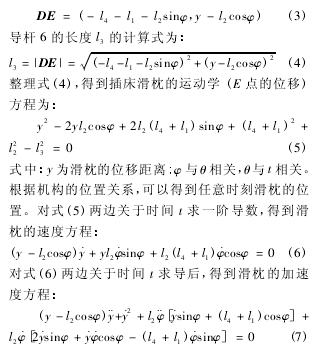
2 、导杆机构优化设计
基于 ADAMS 软件的导杆机构设计,首先建立机构的简化三维模型,然后通过仿真验证研发前所提出的各种设计要求,最后对该机构进行优化设计,得到最优的设计方案和优化结果。相比常规的解析法设计,机构设计的尺寸精度得到了提高,同时解决了经验设计中复杂机械无法兼顾各种设计要求的弊病。依据表 1 中的数据,在 ADAMS 软件中建立插床导杆机构的简化模型,如图 2 所示。
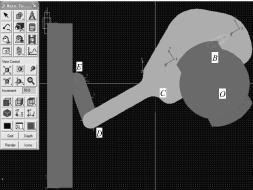
图 2 插床导杆机构简化模型
插床执行机构中滑枕的工作特点决定了切削运动为循环往复运动,安装在滑枕上的插刀速度波动越小,切削加工件的表面质量越好。而加速度是检验速度大小变化的最好依据,所以在插床运动机构的设计中,通过减小加速度的变化幅值进而控制速度变化是可行的。以加速度为优化目标的插床导杆机构参数化设计,首先对机构中决定构件尺寸的关键位置点进行参数化,即将关键点的 X,Y 方向坐标全部设置为变量,然后对这些变量进行参数化的设计研究,最后依据设计研究的结果找出对机构性能影响最大的关键点变量,并再次进行分析。本文对导杆机构中的 O,C,B,D,E 等关键点设置了 10 个变量,分别对应此 5 点的 X,Y 坐标值,进行以加速度为优化目标的导杆机构参数化设计研究,其结果见表 2。
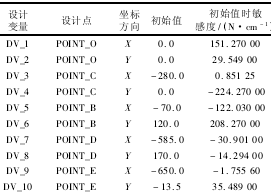
表 2 设计变量分析结果
表中设计变量 DV_1、DV_4、DV_5 和 DV_6 的初始敏感度的绝对值远大于其余变量,说明它们对机构加速度的影响较大。其中设计变量 DV_4 的敏感度绝对值最大,说明机构中 A 点的 Y 坐标值大小对加速度的影响最大; 设计变量 DV_4、DV_5 的敏感度为负,即这些设计变量的位置值越小,执行构件的加速度越小; 设计变量 DV_1、DV_6 的敏感度为正,即这些设计变量的位置值越大,执行构件水平方向的加速度越小。根据以上结果,可以对这 4 个设计变量进一步优化,获得以加速度为优化目标的最佳设计结果。优化设计的过程与设计研究基本一致,这里不再叙述。对 DV_1、DV_4、DV_5 和 DV_6 进行优化设计,得到插床导杆机构以滑块 E 的加速度为优化目标的最佳设计尺寸,优化设计结果见表 3。
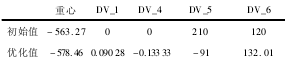
表 3 优化设计结果
至此,本次插床导杆机构等效简化模型的优化设计全部完成。机构关键位置的最新坐标为: O( 280,- 0. 133 33,0) ,B( - 91,132. 01,0) ,C( 0. 090 28,0,0) ,D( - 585,170,0) ,E( - 650,- 13. 5,0) 。
3 、优化结果仿真与验证
3. 1 优化结果仿真
根据导杆机构在插床中所处的位置及作用,设定安装插刀的滑枕为仿真对象,正常工作时每分钟往复运动 80 次。机构仿真时的驱动速度由插床主电动机提供的转速计算得出,机构中斜齿轮的转速为 35. 46rad /s。参数设定完成后即开始进行运动学仿真。软件运算完成后,使用 ADAMS /Postprocessor模块中的仿真结果曲线绘制功能,分别绘制出机构中滑枕的位移 y、速度 v 和加速度 a 与时间 t 的运动特性关系曲线。将优化前后的运动特性曲线合并,如图 3 ~ 图 5 所示。图中实线为优化前的曲线,虚线为优化后的曲线。
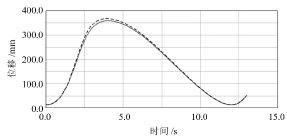
图 3 优化前后滑枕 E 的位移曲线对比
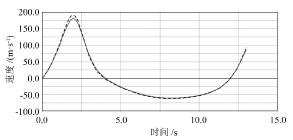
图 4 优化前后滑枕 E 的速度曲线对比
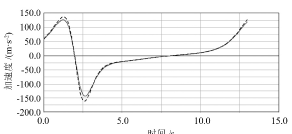
图 5 优化前后滑枕 E 的加速度曲线对比
从图中可以看出,优化后滑枕的行程 H =353. 290 7mm,滑枕的行程有了一定的增加; 最大速度 vmax= 191. 137 0mm / s,最 小 速 度 vmin=- 61. 856 2mm / s; 最 大 加 速 度 amax=136.014 7mm / s2, 最 小 加 速 度 amin=- 160. 900 9mm / s2。在插刀进给阶段滑枕的速度和加速度的突变值减小,工作更加平稳; 急回阶段的速度和加速度的突变值增大,因此急回阶段所花费的时间也相应地减少。
3. 2 优化结果验证
按照优化后的尺寸,在三维 CAD 软件中重新建模,然后导入 ADAMS 软件中,建立插床导杆机构的虚拟样机模型,再次进行仿真,结果如图6 所示。与简化模型的运动特性曲线( 图 3 ~ 图 5)相比,两者的位移、速度和加速度曲线形状基本一致,从而验证了优化设计的效果。
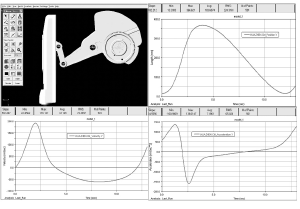
图 6 虚拟样机模型与仿真运动曲线
4 、结束语
本文从工程实际出发,通过分析插床导杆机构的工作原理,在 ADAMS 软件中对该机构进行了优化设计,得到了机构的最佳参数,使得插床滑枕在急回阶段的加速度变化幅值有所增加,提高了滑枕切削完成后的返回速度,从而提高了切削加工效率。运用虚拟样机技术,在 CAD 软件中建立虚拟模型,导入 ADAMS 中对优化设计结果进行仿真验证,依据得到的最佳性能参数返回 CAD 软件中修改原模型的尺寸,间接实现了外部导入模型的优化设计,为相关机械产品的优化设计提供了一条思路。
来源:(1. 江阴职业技术学院机电工程系,江苏 江阴 214405)( 2. 江苏省江阴中等专业学校机电工程系,江苏 江阴 214400)
投稿箱:
如果您有机床行业、企业相关新闻稿件发表,或进行资讯合作,欢迎联系本网编辑部, 邮箱:skjcsc@vip.sina.com
如果您有机床行业、企业相关新闻稿件发表,或进行资讯合作,欢迎联系本网编辑部, 邮箱:skjcsc@vip.sina.com
更多相关信息