基于 HNC-8 数控系统的机床热误差补偿方法
2018-8-8 来源:转载 作者: 陈国华,闫茂松,向华,李强,张少博,童
摘要: 热误差在机床总误差源中占了极大比重,研究热误差补偿方法对于提高机床加工精度具有十分重要的意义。基于 HNC-8 ( 华中 8 型) 数控系统的开放性特性,根据机床热误差的补偿原理,分析热误差补偿值的计算方法,并据此算法开发了集成于 HNC-8 数控系统的热误差补偿模块,最后结合实例,验证了补偿方法的有效性。
关键词: HNC-8 系统; 机床; 热误差; 补偿方法
数控机床随着机床定位精度和刀具性能的不断提高,几何误差和切削力误差在一定程度上已经得到了较好的解决,而温度变化引起的热误差在总误差源中占了极大比重,成为了影响机床精度、精度保持性的最重要和最难以解决的因素。
减小热误差的方法主要有 3 种: 温度控制、热稳定性设计和热误差补偿。温度控制不易实现,因为温控总是滞后于温升,只有发生了温度变化后,控制机构才会发生作用。热稳定性设计通常称为误差防止法或硬技术,因为它在机床设计制造阶段就进行热误差机制分析,包括机床温度场和变形位移场,进而采取结构优化和材料改进等来提高机床的热稳定性。而热误差补偿则不需要改变机床结构设计,采用补偿控制器加上软件编程来消除机床自身产生的热误差,所以又称为控制热误差的软技术,被认为是最有效、最经济的方法。
从目前来看,补偿运动控制的实现方法有: (1)通过修改 G 代码来实施补偿,很明显,该方法实时性差,应用极不方便; ( 2) 开放式数控系统补偿法,但国外数控系统完全不开放; ( 3) 数控系统内部参数调整补偿法,如螺距补偿、齿隙补偿、刀补等,但仅静态补偿; ( 4) 原点偏移补偿法,但受限于数控系统。
由于以上原因,特别是受限于国外数控系统功能接口的不开放,使得误差补偿技术应用不到位,因此,作者基于 HNC-8 数控系统的开放性特征,根据机床热误差补偿原理与方法,将热误差补偿模块集成于数控系统,以提高机床的加工精度为目的,从而实现扩大国产数控系统的功能。
1 、机床热误差补偿方法
1. 1 补偿原理
机床热误差不仅仅与温度相关,而且与机床的位置有关。为了实现机床热误差补偿,必须测量指定温度条件 T 下机床各运动轴在行程范围内的误差值序列,并根据误差值序列运用回归拟合的方法绘制热误差曲线。热误差曲线如图 1 所示。
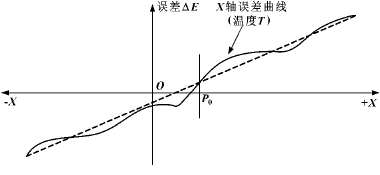
图 1 X 轴热误差曲线拟合图
从图 1 可以看出: 在满足一定精度要求的前提下热误差曲线可以用一条直线 ( 虚线) 代替,该直线可以通过斜率与补偿参考点 P0唯一确定,这为热误差在数控系统中的补偿提供了极大方便。只要确定不同温度下的热误差与机床位置的函数斜率及参考点截距,就可以在数控系统中实施动态补偿。
1. 2 补偿值的计算
对机床热误差的补偿其实就是对拟合直线的斜率和拟合直线的偏置值进行补偿,使补偿后的拟合直线斜率为 0,拟合直线偏置值为 0。图 2 形象表达了补偿值的计算方法。以 X 轴补偿为例,补偿值 Cx由当前指令坐标值Px以及温度传感器测量得到的温度值 T 确定,计算公式如下:

各参数含义如图 2 所示,具体如下: Cx为 X 轴在 Px位置的温度补偿值; ΔEx为 X 轴在温度 T 时的热误差值; K0为 X 轴位置无关式热误差补偿值; Px为 X 轴指令位置; P0为 X 轴补偿参考点; tanβ 为 X轴位置相关式热误差补偿系数 ( 即 X 轴热误差拟合直线的斜率) 。
1. 3 热误差补偿插补方法
热误差曲线仅描述了针对某一特定温度的瞬时状态,所以当温度变化时补偿参数必须根据新的热误差曲线重新生成,并传送给数控系统。热误差补偿在插补周期内进行,即所谓的插补后补偿。为防止机床过载,在按照公式 ( 1) 计算得到热误差补偿值后,必须先通过监控程序与补偿值平滑处理限制补偿值的大小,再将其与插补输出指令位置进行叠加。热误差补偿插补方法如图 3 所示。
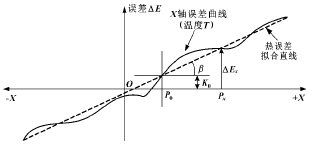
图 2 误差补偿值的计算原理
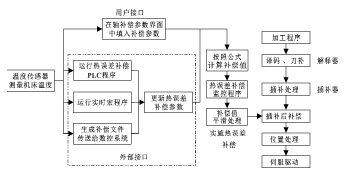
图 3 热误差补偿插补方法
1. 4 热误差补偿模块开发
基于 HNC-8 数控系统的开放性特性,根据机床热误差补偿方法,开发了一套集成在华中 8 型数控系统中的热误差补偿模块,有效地扩展了国产数控系统的功能以及适用范围。热误差补偿模块如图 4 所示,主要补偿参数有: 补偿轴轴号,热误差补偿类型,热误差补偿参考点坐标,偏置表起始温度,偏置表温度点数,偏置表温度间隔,偏置表传感器编号,偏置表起始参数号,斜率表起始温度,斜率表温度点数,斜率表温度间隔,斜率表传感器编号,斜率表起始参数号,补偿率。
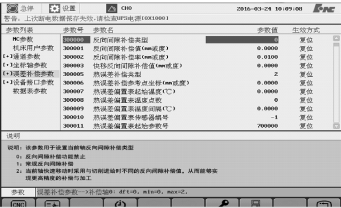
图 4 机床热误差补偿模块界面
2、 实例应用
2. 1 研究对象
以立式加工中心 XHK715 为研究对象,如图 5 所示。XHK715 配有华中 8 型数控系统 HNC-818B,并集成了机床温度数据采集系统,该温度采集系统是基于华中 8 型数控系统设计的对机床温度信息进行实时采集并实时显示的温度检测系统。通过埋在机床热关键点的温度传感器采集温度信息,并将温度信息经过HIO 传输到数控系统,并在时域示波器界面进行实时显示。几何精度测量仪器采用美国 API 公司研发的6D 激光干涉仪。机床的热变形规律和机床上许多重要部件的温度变化有关。因此,必须在机床上布置一些温度测量点来检定机床的整体温度,通过对温度数据进行分析和计算,在机床上筛选出能够与机床热变形有较高相关度的温度测量点,并采集这些温度测量点处的温度数据用于机床热误差的模型建立。综合考虑,此次应用验证以丝杠温度传感器的布置点选择在近电机端的轴承座上为热误差建模。
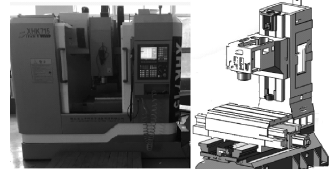
图 5 研究对象 XHK715
2. 2 热实验方案
实验的目的是对 XHK715 机床热误差进行测量与补偿,探讨温度对机床 21 项误差的影响规律,研究华中 8 型数控系统热误差补偿技术在机床 X 轴丝杠热误差补偿上的实际适用性。机床空载运行,X 轴以一定进给速度做往复运动,使机床温度不断升高,每到温度间隔点采集一次误差数据。机 床 误 差 测 量 与 补 偿 实 验 的 具 体 步 骤如下:
(1) 安装激光干涉仪。在移动轴运动升温前安装激光干涉仪,达到一定温度时可以直接测量移动轴误差,机床温度下降影响测量结果。
(2) 采集机床热误差。机床空载运行,X 轴以最大的进给速度 6 000 mm/min 做往复运动,使机床温度不断升高,每隔 1 ℃ 测量一次机床误差。
(3) 热误差补偿前后对比分析。通过对热误差补偿前后的对比分析,验证热误差补偿方法的效果。
2. 3 补偿效果对比分析
由于季节性的原因,车间环境温度在 18 ℃ 左右,故选取机床误差测量的温度区间为 18 ~ 28 ℃ ,温度间隔取 1 ℃ 。在不同温度点对机床 X 轴定位误差进行多次采样,采样过程中,由于测量时间长,机床温度会有 0. 1 ℃ 左右的下降,在处理测量数据时忽略微小温降。最后对所有误差数据进行汇总分析,分析结果如图 6 所示。
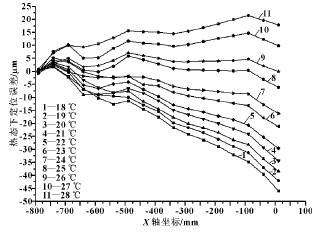
图 6 X 轴补偿前热误差曲线
根据 X 轴热态下的定位误差统计数据,可以计算出机床热误差补偿参考点坐标为-800 mm,根据各温度下的误差曲线求出各自的热误差拟合直线的斜率和在参考点处的偏置值,并以此在 HNC-8 数控系统中设置热误差补偿参数值,进行热误差补偿后得到误差曲线如图 7 所示。
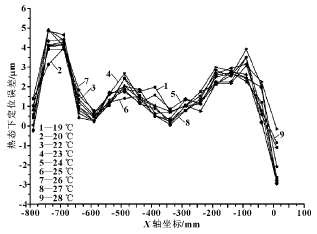
图 7 X 轴补偿后热误差曲线
可以看出: 补偿前,在 18 ℃ 时,定位误差最大值为-47 μm,在 28 ℃ 时,定位误差最大值为 23 μm。温度相差 10 ℃ ,定位误差相差了 80 μm,可见温度对机床的定位误差有很大的影响。补偿后,不同温度条件下的误差曲线基本重合,误差在 - 3 ~ 5 μm之间。采取同样的方法,对 X 轴水平方向直线度和垂直度方向直线度进行了热误差实验与补偿效果验证。水平方向直线度,补偿前: 18 ℃ 最大值为-15 μm,28 ℃ 最大值达到 25 μm,补偿后: 误差在 - 4 ~ 4 μm之间; 垂直方向直线度,补偿前: 18 ℃ 最大值为 17μm,28 ℃ 最大值达到 41 μm,补偿后: 误差在 - 3 ~4 μm之间,热误差补偿效果显著。
3、 结论
基于 HNC-8 数控系统的开放性平台,根据机床热误差补偿原理,分析了误差补偿值的计算方法,开发了集成于数控系统的机床热误差补偿模块,并以一机床 X 轴热误差补偿为例,进行了应用验证,补偿效果显著,证明了补偿方法的有效性。
来源:湖北文理学院机械与汽车工程学院,襄阳华中科技大学先进制造工程研究院,中铁十一局集团第一工程有限公司
投稿箱:
如果您有机床行业、企业相关新闻稿件发表,或进行资讯合作,欢迎联系本网编辑部, 邮箱:skjcsc@vip.sina.com
如果您有机床行业、企业相关新闻稿件发表,或进行资讯合作,欢迎联系本网编辑部, 邮箱:skjcsc@vip.sina.com
更多相关信息