一种变速箱加工的数控系统设计与实验研究
2020-7-6 来源: 陕西工业职业技术学院 作者:邓丰曼
摘要:针对传统的多轴数控机床较难满足变 速箱加工过程中精度要求,提 出了一种基 于 “ARM+DSP”硬件结构的参数可重构嵌入式数控系统的设计。所设计的数控系统通过参数化自动编程模块,实现了根据变速箱齿轮的参数、加工刀具参数和加工过程参数自动生成数控加工程序,还能够通过专家数据库优化数控程序中周期性参数的设置,同时在所设计的数控系统中应用了一套新型的软件电子变速器,以达到提高多轴同步运动控制精度的目的。实验结果表明,将所设计的嵌入式数控系统应用于六轴滚齿机,能够有效提高变速箱齿轮的加工精度。
关键词:变速箱;嵌入式数控机床;参数自动编程;专家数据库;电子齿轮箱
0引言
变速箱是机械设备的重要基础部件,广泛用于船舶,汽车,飞机,农业设备,工程机械,采矿设备和电力设备等。变速箱对加工精度要求较高,通常使用数控机床实现对变速箱的高精度加工。数控机床的多轴同步运动的控制精度是影响变速箱加工精度的主要因素[1-3]。传统的数控机床都使用机械传动链来控制直线运动和旋转运动,以实现运动轴的准确跟随运动[4-6]。因此传动链上每个部件的磨损、热偏转、参数设置误差都会降低连续运动精度[7-8]。
一些研究成果表明,利用嵌入式系统的巨大运算能力能够有效补偿机床动态误差,提高数控机床的控制精度。文献[8]中提出了一种基于关键实时任务输出抖动的模糊反馈调度算法,以解决嵌入式系统实现中,由系统资源和处理器使用限制引起的不确定性因素。文献[9]将可重构逻辑被应用在高速CNC数字控制器中,以满足数控机床中伺服回路的实时性要求。文献[10]在CNC中利用以太网Power-link通信总线实现了控制组件接口在实时操作系统下运行。文献[11]针对不同的应用领域,基于嵌入式技术引入了一些专用数控系统硬件和软件结构。该研究表明,与通用机床相比,专用机床对齿轮等特殊部件的加工具有效率高和精度好的优点。基于上述研究,在传统数控系统中引入嵌入式硬件平台,开发了变速箱加工专用数控系统。该系统基于变速箱齿轮加工工艺的特点,设计出具有柔性加工功能的电子齿轮箱(EGB)功能模块,以充分适应不同变速箱齿轮加工 工艺 的要求。该系 统 通过参数化自动编程,实现自动生成加工数控程序的功能。并利用专家数据优化加工参数,提高数控程序的可靠性。最后通过实验对所设计的数控系统的有效性进行验证。
1、硬件平台和软件框架
对于高性能嵌入式数控系统而言,数控系统开发人员可以将新技术集成起来,具有很强的适用性和开放性,用户可以轻松地 进行二次开发,扩 展 系统的功能。根据实际加工要求,可以将结构切割成各种齿轮加工数控系统[12-14]。本文的ARM和DSP组成的数控系统的硬件结构如图1所示。
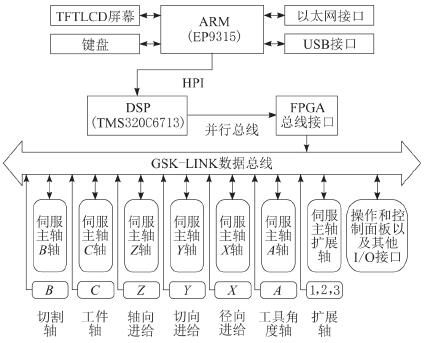
图1数控系统平台的硬件结构
2个芯片的型号分别为 ARMEP9315和DSPTMS320C6713。DSP芯片完成复杂的数学运算和实时任务,包括位置控制,插值计算和 PLC 控制。ARM 芯片完成人机交互和界面管理,如代码编程,参数设置和状态显示。系统前台 ARM 与后台DSP之间的数据交换通过HPI实现。
完整的数控系统包括各种类型的任务:周期性的实时任务,如位置控制、插补计算和 PLC控制;非周期性的实时任务,如系统状 态 显示、报 警检测和数据交换;非实时任务,如参数管理、代码编译和文件管理。 实时任务具有并发性特征,并且同时执行。因此,需要一个实时操作系统(RTOS)来管理和调度多 任务环 境中的实 时 任务[15-16]。为 了完成数控系统,除了硬件结构之外,还应该设计软件。
图2所示的软件分为前台系统软件和后台软件2部分,运行在具有不同工作频率和不同处理器的内存上。通过使用不 同的芯 片 可以充分 发挥其优点,从而获得高性能。将 WinCE 操作系统移植到具有强大事务管理能力的ARM内核。ARM 芯片上运行的应用软件 包括参数 管理、文件管 理、状态和报警信息显示、自动编程和图形模拟功能。内核层实时控制软件运行在DSP(
TMS320C6713)上,BIOS部署在DSP内核上,以获得较高的控制精度。控制软件主要由3个周期性实时任务:位置控制;插补和PLC控制组成,其运行周期分别设置为0.25
ms,1ms和10ms。
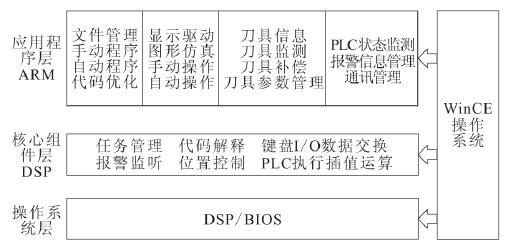
图2数控系统的软件架构
2 、参数化自动编程
参数化智能自动编程功能模块的结构如图3所示。用户只需设置齿轮参数(如齿轮类型,齿轮特征参数),刀具参数(如刀具类型,刀具特征参数 )和切削循环参数。然后通过自动编程模块获取加工程序,通过图形仿真验证NC代码的正确性。齿轮可以加工包括圆柱齿轮,鼓齿轮,小锥齿轮,非圆齿轮,螺旋锥齿轮和齿条。特征参数包括齿数、模数、压力角、螺旋角和齿宽等。不同齿轮对象的刀具参数不同。生成并通过动态验证后,加工代码将通过 HPI下载到指令缓冲区,数据结构可由 DSP识别。这些代码将在DSP中得到执行。通过编译预处理,加减速实时处理,插补实时计算得到用于控制机床轴运动的实时位置控制数据。根据插补数据,齿轮轮廓将被加工。
在获得加工代码之前,可以通过手动模式或自动查询模式输入切削参数。在过程数据库的支持下,可以自动选择切削参数,如主轴转速、进给速率和切削方式。对于具有不同力学性能的各种齿轮,使用专家知识选择的参数将是最佳的,并且它们将提供最理想的精度和效率。
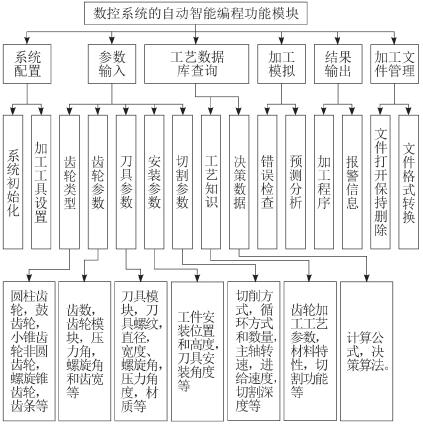
图3智能自动编程模块的软件体系结构
3、变速箱加工工艺专家数据库
齿轮加工过程数据库是一个数据管理软件,包括齿轮刀具信息,齿轮零 件信 息 和切削过程信息。它具有数据定义、数据输入、数据修改、数据 删除、数据查询、数据输出、数据管理和数据分析等功能,为齿轮加工提供帮助。该数 据库主要由用户前台操作界面和后台数据操作功能组成,作为功能模块内置于数控系统软件中。其结构如图4所示。
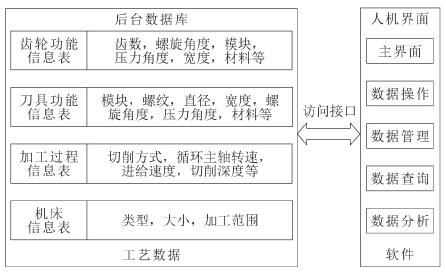
图4变速箱加工工艺专家数据库功能模块
数据和模型是专家数据库系统的2个重要组成部分。数据是变速箱加工的基础信息,数据模型是获得最佳切削工艺参数的分析方法。在数据库中,通过加工过程手册,实验和实际生产收集数据。采用关系模型分析齿 轮、刀具、机床 和 切削工艺参数的相关性。与网络模型和层次模型相比,关系模型的结构简单,并且使用二维关系表来描述实体之间的关系。它基于严格的数学基础,每个属性又是不可分割的,因此可以更好地保证数据的完整性和数据的一致性。
变速箱加工过程 数 据库设计工作主要包括需求分析,概念设计,结构设计和物理设计。根据齿轮加工应用要求,首 先要建立齿 轮特征信息表,切削刃特征信息表,切削过程参数表,机床信息表。主要特征需要包含在这些表格中,以便获得最佳结果。物理设计是在系统资源的限制下,开发适合嵌入式数控系统的存储结构和方法。对于所提出的硬件结构,数据库是通过基于SQLite3的Visual Studio VC ++编程环境进行设计和开发的。如前所述,CNC内置的数据库可以支持自动编程模块以获得最佳加工程序。此外,还可以用来为技术人员提 供 一个独立 模 块的指导。对于用户来说,它可以带来足够 的 便利来保 存、管理和优化加工参数。同样,系统也可以通过积累加工大数据来实现智能化数控加工。
4 、高精度软件电子变速箱
电子齿轮 箱 (EGB)通过高性 能 微处理器取代了机械传动链,大大提高了机械系统的灵活性和传动精度。EGB软件是用来取代复杂的硬件逻辑电路,任何传动率都可以在理论上被 EGB所实现。值得注意的是,数控系统的稳定性和静态误差并没有在EGB中得到有效解决。对于变速箱加工,变速齿轮形状可以通过刀具主轴、工件主轴和进给轴的同步运动形成。变速箱齿轮加工精度主要取 决 于同步精 度。为 了实现多轴同步,采用了复合结构 EGB。在 EGB中,根据安装在刀轴上的编码器的反馈数据和其他进给轴的指令数据,计算出从动轴 的 下列位置 和 速 度指令。然后,所有轴的实时指令被发送到位置控制器以驱动这些轴。每种齿轮加工方法都对应于 EGB结构。
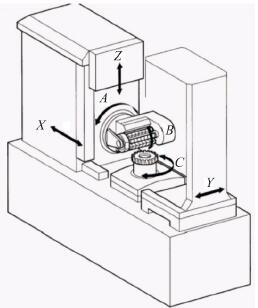
图5滚齿机的整体结构
提出了适用于齿轮加工数控系统的齿轮铣削,成型、滚铣、磨削和研磨加工过程的 EGB。在此,将阐述用于变速箱滚齿的EGB。滚齿机的整体结构如图5所示。图5中,滚刀主轴B、工件主轴C 和轴向进给轴Z是最上面的成形运动轴。Y 是用于更换刀片的滚刀末端轴。X 是实现全齿深切的径向进给轴。A 是滚刀安装角度调整轴,它是具有不同螺旋角度的齿轮的变体。C 轴主要跟随滚刀轴B 的运动,B 与C 之间的关系满足:

nB为滚刀主轴B的速度;nC为工件主轴C的跟随速度;ZB为滚刀的螺纹数;ZC为工件齿轮的齿数;KB的值是根据旋转滚刀主轴的方向来确定。当变速箱齿轮达到设计齿宽时,滚刀需要沿进给轴Z移动,此时在C轴上增加一个额外的运动,可以根据Z轴的行程距离获得附加的值。类似地,当采用对角线滚边加工方法时,Y 轴引起附加的运动。在C轴上的附加运动值为:

ΔθC是由Z轴和Y轴引起的附加移动;Δz是Z轴的移动距离;Δy是Y轴的移动距离;ZC是齿轮齿数;β为加工齿轮的螺旋角;λ为滚刀安装角度;KZ和KY的值根据β,Δz和 Δy
分别取“+1”或“-1”。结合式(1)和式(2),滚刀 EGB同步关系为:

θC,θB,z和y分别表示C 轴的跟随角度位置、滚刀主轴的移动角度位置、Z 轴的移动距离和Y 轴的移动距离。θB,z和y 的值可以从插值结果中获得,因此只需要定义ZB,ZC
,mn,β和λ的指令在内的指令即可通知CNC系统,并且θC可以是自动获得。特殊代码G81定义为打开EGB并限制所有机床轴的运动关系。G80被 定义为关闭EGB并取消同步约束。
当EGB有效时,C轴随动Y 轴、Z轴和B 轴的运动,其关系符合式(3)。如果 G81无效,C 轴将是一个通用轴。因此,变速箱数控加工系统也可以作为传统的通用数控系统,如车床、铣床和加工中心。EGB的实现过程如图6所示。
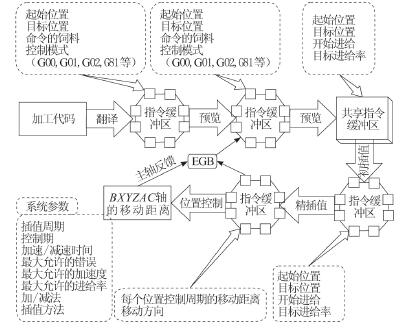
图6EGB的实现过程
当检测到EGB指令时,同步数据信息被存储在环形指令缓冲器中。最 终的位置 控 制数据被发送到位置控制器以驱动机床,在预见计数过程,加速/减速控制,粗略插补和精细插补之后。被存储在环形指令缓冲器中。最 终的位置 控 制数据被发送到位置控制器以驱动机床,在预见计数过程,加速/减速控制,粗略插补和精细插补之后。
5 、性能验证
所提出的关键技术在水平六轴 滚齿机的滚齿试验中得到验证。该滚齿机用内部开放式嵌入式齿 轮加工数控系统,采用 “ARM + DSP”硬件结构。滚齿机实验平台的整体结构如图7所示。
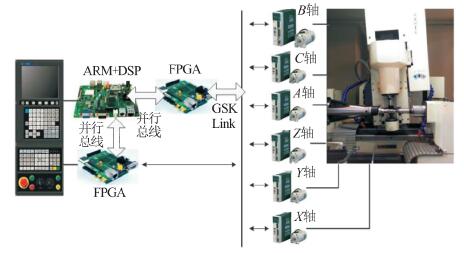
图7 实验平台的整体结构
所有轴均由交流伺服电机驱动,其控制方式为速度控制方式。数控 系统的 硬 件和软件 结构在前一节中介绍。数控系 统的主 要 功能是精 确控制机床完成滚齿,包括加工程序生成、信息管理、机床监控状态显示、发送运动控制指 令、接收反 馈信息控制滚齿机。表1总结了伺服电机参数以及每个机床轴的机床结构参数。
表1每个机床轴的伺服电机和结构参数
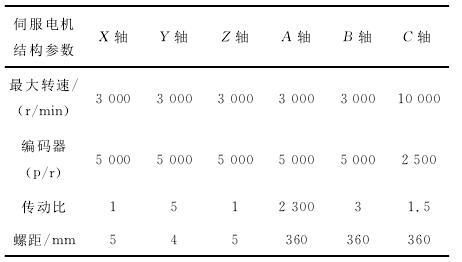
进给和主轴伺服编码器分别产生2000和1000个脉冲,而编码器信号通过四倍频电路进行细分。数控系统基于 使用右向滚刀加工右轴齿轮进行性能测试。对变速箱齿轮进行机械加工时,主轴转速达到1000r/min,并分别以10mm/min和5mm/min的轴向和径向进给速度进行切削。表2给出了待加工变速箱齿轮的参数和相应使用的滚刀参数。
表2实验齿轮和刀具参数
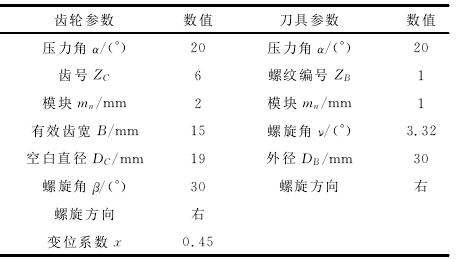
5.1空气切割实验
在自动编程功能模块中输入这些参数后,将自动生成加工代码。采用 轴向 滚齿加工方法来验证变速箱齿轮加工数控系统的有效性。
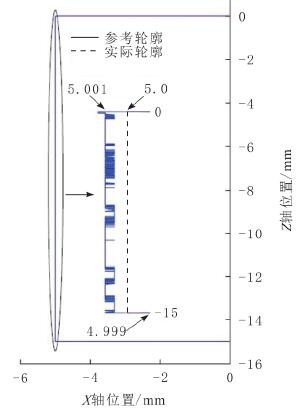
图8 X-Z平面参考与实际轮廓
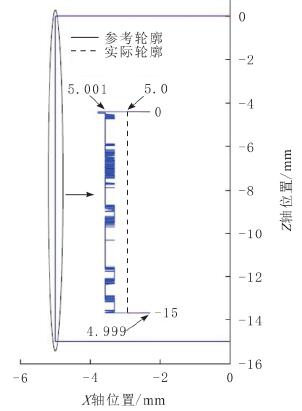
图9 C轴理论与实际位置
在测试过程中,记录和比较关节轴所需的指令信号和编码器反馈信号。X 轴、Z 轴和C 轴的理论和实际轮廓分别如图8和图9所示。对图8和图9中的实验加工结果进行分析,可以看出,所有的理论位置和实际位置都略有不 同,但是每个轴都能够精确地跟随位置指令。实 验 中工件的测量值满足式(1)和式(2)的同步控制要求。
实验中X轴和Y轴的编码器的脉冲分辨率为0.25μm,C轴编码器的脉冲分辨率为0.006°。整个轴向滚齿加工过程数控系统 的X轴 和Z轴平均跟踪误差 都 小于0.75μm,C 轴 平 均 跟 踪 误 差 为0.0153°,这些误差都分别小于对应的编码器脉冲。很显然,实验数控平台能够满足变速箱加工的精度要求,可以用来实现变速箱的齿轮高精度加工。对于用于变速箱加工的多轴轮廓控制系统,轮廓误差都是评估控制系统性能的重要评估指标。轮廓误差有螺旋偏差和螺距偏差2方面。
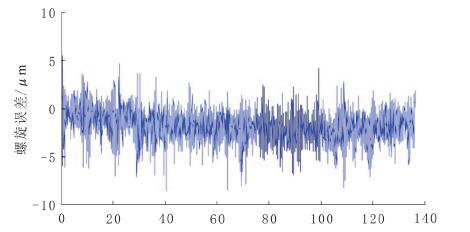
图10 螺旋误差
由图10可知,螺旋误差的最大值为9.5μm,平均螺旋误差为1.8μm,可以达到变速箱加工的要求。
从图10可以清楚地看到,参与切削过程的各轴跟踪误差足够小,可以证明实验数控平台的跟踪控制性能。因为齿轮螺旋线是由 Z 轴进给,工件主轴C轴和滚刀主轴B轴使用轴向滚齿方法同步运动而产生的。因此,齿轮加工精度不仅取决于C轴的跟踪性能,而且还取决于所有轴的同 步轮廓控制性 能。图11和图12分别分析了变速箱齿轮加工的节距误差和螺旋误差。图11中分析的螺旋误差可以满足变速箱齿轮切削的精度要 求。下一步将通过变速箱齿轮加工实验进一步说明数控系统的性能。
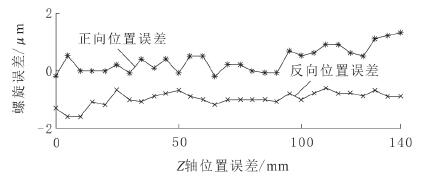
图11 Z轴位置误差/mm
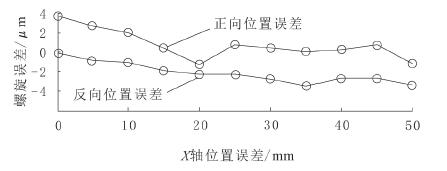
图12 X轴位置误差/mm
5.2 变速箱齿轮加工测试
在加工测试之前,嵌入式变速箱齿轮加工数控系统的性能通过前面提到的轴向滚齿方式进行验证。在变速箱齿轮加工之前,由于滚齿机采用了半闭环位置控制模式,因此使用激光干涉仪检测位置精度,并通过数控系统的螺距误差和齿隙补偿功能进行补偿。图11和图12中显示了2个主直轴的位置误差测量结果。结果表明,机床位置误差完全满足要求并且范围较小。参数如表2的齿轮和刀具用于加工实验。40Cr工件以4.5mm的切削深度一次切削循环切削。切割后,使用齿轮精度测试中心测量螺距误差和螺旋误差。从测试结果来看,左齿面的最大误差为6.3μm,右齿面的最大误差为5.1μm,满足设计要求。
6、结束语
提出了一个具 有可重构参数的 数控系统。变速箱齿轮数控加工系统可以通过简单的参数设置用于不同的加工机床。介绍 了应用于变速箱加工数控系统的关键技术,这些技术包括参数化智能自动编程、专家数据库和高精度 EGB。该系统的软件结构是在“ARM + DSP”硬件平台上构建和实现的。为了验证这些功能的有效性,实验在具有内部嵌入式数控系统的六轴卧式滚齿机上进行了空气切割状态和实际加工 测 试。实验 结果证明了系统能够有效地应用于变速箱的加工。
虽然所提出变速 箱 齿轮数控 系 统可以满足变速箱齿轮加工的要求,但齿轮的每个齿轮的轮廓误差存在一定的波动范 围。由于轮廓误差可以通过实时预补偿解决方案加以提高,因此下一步的研究是基于预补偿控制算法进一步提高 数控系统的加工性能。
投稿箱:
如果您有机床行业、企业相关新闻稿件发表,或进行资讯合作,欢迎联系本网编辑部, 邮箱:skjcsc@vip.sina.com
如果您有机床行业、企业相关新闻稿件发表,或进行资讯合作,欢迎联系本网编辑部, 邮箱:skjcsc@vip.sina.com
更多相关信息