FANUC 数控系统机床返回参考点功能的应用研究
2020-10-30 来源:上汽通用五菱汽车股份有限公司 等 作者:於双月,黄晓敏,蒙旭喜
摘要:数控机床能精确控制零件的加工精度,而它的加工是要基于一个固定的参考点,而参考点的位置就是以机床出厂零点为基准的。通过研究使用 FANUC 数控系统的数控机床建立参考点的方式,研究返回参考点的三种方式,并结合现场应用案例,总结了数控机床无法正常返回参考点的原因并给出了响应解决思路,并分析返回参考点过程中常见的问题,可以有效解决数控机床无法返回零点的问题。
关键词:数控机床;参考点;零点;返回参考点
众所周知,数控机床能精确控制零件的加工精度,而它的加工是要基于一个固定的参考点,参考点即为机床加工程序坐标的起始位置。在对数控机床的使用和维修时,经常会遇到无法正常返回参考点的故障,返回参考点是机床正常加工的必要条件,它的用途很简单,就是将数控系统的记忆位置与设备的某个机械位置统一。各种数控系统回参考点方式有差异。但无论使用哪种数控系统,建立参考点都是必不可少的步骤,以下仅以 FANUC 数控系统作为研究对象。见图 1。
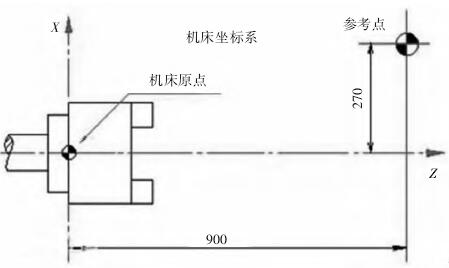
图 1 机床参考点示意图
1、返回参考点的必要性
数控机床位置检测通常使用位置编码器或光栅尺,分为增量式与绝对式,而数控机床的加工必须依靠坐标位置,如果使用绝对式编码器或光栅尺,在机床出厂时执行建立参考点的步骤后,位置数据已经存储好,再次开关机时不需要重复执行返回参考点操作,但这位置数据记录需要电池保持,如果电动电量耗尽没有及时更换,则位置数据就会丢失,坐标数据也就失去记忆,因此必须要让各轴回到一个标记好的固定位置,也就是机床的参考点,重新记录位置信息,这样才能保证工件的加工尺寸,而且机床使用的各种刀具、探针、测头及补偿,都是依赖参考点的建立的坐标执行对应关系的,如果没有回到参考点,则这些数据也就失去了意义,所以数控机床要正常使用必须要确定好参考点。见图 2。
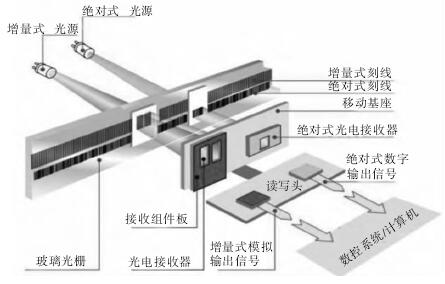
图 2 光栅尺内部结构图
2、返回参考点情况分类
根据数控机床选择的数控系统及位置反馈元件和控制方式的差异,返回参考点方式也各不一样,一般分为开机后需要返回参考点和开机后不需要返回参考点两种情况。
2.1 无挡块方式回参考点
回参考点的方式无需挡块,用绝对位置编码器或光栅尺的方式记录位置信息,这种方式在现在的多轴联动机床上比较常见,由于采用的是能记录位置信息的装置,因此需要用到电池作为能源用于保存信息,由于有位置信息的记录,之后再开机就无需执行返回参考点操作,如果电池没电则会导致位置信息丢失,机床无法使用,需要更换电池再次返回参考点才能正常使用。
2.2 挡块方式回参考点
回参考点的方式为挡块方式,通常使用增量式的编码器或光栅尺记录位置信息,由于该方式比较简单,也没有后备电池记录位置信息,因此电后位置信息即会丢失,无法保存,后续再开机则需要重新执行返回参考点操作,这种回参考点的方式在一些数控车床等相对没那么复杂的机床上使用较多。
3、返回参考点方式
一般情况下,不同厂家使用不同的数控系统,其返回参考点的方式与原理都会有所不同,但都是先通过挡块之类的减速行程开关粗定位,然后再由码器或光栅尺之类的检测装置精定位两个步骤。根据回参考点的动作步骤不同,有以下三种回参考点方式:
(1) 在返回参考点时,伺服轴先向预定方向运动,挡块压下后正向减速运动,挡块脱离后,数控系统开始寻找零点,当接收到第一个零点脉冲时,便已确定参考点位置。
(2)在返回参考点时,伺服轴先快速按预定方向运动,挡块压下后,反向减速运动,脱离零点开关时,再改变方向正向向参考点移动,当挡块再次压下时,数控系统开始寻找零点,当接收到第一个零点脉冲,便已确定参考点位置。
(3)在返回参考点时,伺服轴先快速按预定方向运动,挡块压下后,不需等待挡块脱离立即减速,降为设定低速后,即开始寻找零点,当接收到第一个零点脉冲时,立即停止。无论采用何种方式或如何运动,系统都是通过程序编制和数控系统的机床参数设定决定的,轴的运动速度也是在机床参数中设定的,数控机床回参考点的过程是 PLC 系统与数控系统配合完成的。
机床在执行返回参考点操作时,每一步的动作都根据接收到的信号指令进行,因此,清楚数控系统在整个过程中需要哪些信号就非常重要,如下为与返回参考点有关的对接信号点:
(1)挡块使用方式信号:1005#1 DZLX,选择 0为无挡块,选择 1 为有挡块。
(2)手动返回参考点方向信号:1006#5,选择 0 为正方向,选择 1 为负方向。
(3)各轴参考计数器容量信号:1821,指定为执行栅格方式的返回参考点的栅格间隔。
(4)各轴参考点偏移量信号:1850,设定每个轴参考点位置偏移的栅格量或参考点的偏移量。
(5)机械位置与绝对位置建立关系信号:1815#4,使用绝对位置检测器时,第一次使用先设为 0,再次通电后执行手动返回参考点操作后,绝对位置检测器原点设立后,及位置关系建立后,改信号会自动设为 1。
4、 应用案例分析
4.1 应用案例 1
车间返修区一台使用 FANUC 数控系统的数控车床,各轴应用的都是绝对式光电脉冲编码器,一直处于正常加工状态,但在经过一次长假后,开机无法正常使用。其故障现象为机床开机后出现 306 号报警,反复断电重启也无法消除,同时伴随报警为 300号需要返回参考点。故障检诊断:由于该数控机床位置检测采用的是绝对式位置检测装置,断电开机时是不需要再返回参考点的,询问操作人员放假前情况,答复出现307 号报警,由于不影响生产故未上报。见表 1。
表 1 相关参数及报警号说明

由于最开始出现的是 307 号报警,机电池电压下降报警,出现该报警时,是提醒后背电池电压已经不足,需要在 1~2 周内更换电池以保证电机编码器正常运行的,而现场没有及时更换电池,导致经过一次长假后电池耗尽,无法正常保存伺服轴位置信息,这时候出现的报警为 306 号报警,即电池零报警。故障处理过程:首先替换电池,需要注意的是,如果在出现 307 号报警电磁电压下降报警时更换电池,即使切断电源,只要在 10 min 内将电池更换好也不会出现位置信息丢失的情况,也无需再执行返回参考点操作,因为内部电容能保证短时间内存储的位置信息不回丢失,更换检测编码器供电电池后,可以重新返回机床参考点,设定机床参考点位置。步骤如下:
(1) 把下面的 PRM 设置为 0 :PRM 1240、PRM1883。
(2)PRM 1815 Bit 4 (被自动通过 PRM 1883 设置为 0)。
(3)设 PRM 1819 Bit 2 = 1。
(4)选择 Reference,选择轴键,按 Plus- 或者 Mi-nus-键,轴开始运行基准点,3 个标记 (3 x 停止)后被选择轴的基准点运行完毕。
(5)PRM 1819 Bit 2 重新为 0,PRM 1815 Bit 4= 1。
(6) 在 PRM 1883 中有系 统 内 部 的 基 准 值 ,PMC-诊断% IF 961 Bit x(= 轴) 为= 1 ,定义轴的终点位置。
(7)机床关机,重新启动后故障解除。
最后,根据长期现场使用经验,一般数控机床发生返回参考点故障时主要检查以下项目:
1) 首先检查回参考点的模式及故障报警信息,根据报警提示对应处理。
2)然后检查硬件,减速挡块、减速开关的位置及状态一定要正确。
3)最后检查参数,看参数设置是否合理。
4.2 应用案例 2
车间返修区一台使用 FANUC 数控系统的数控车床,在某次更换完丝杆后执行回参考点步骤,回参考点运行时动作正常,但每次回的位置都有差异,参考点位置不固定,每次定位均不同。
故障诊断:由于机床数控系统并无报警,且返回参考点也能正常执行,判断机床回参考点功能是没有问题的。再进一步分析,参考点的位置虽然每次都不一样,但总能停在离开减速挡块的位置上。因此,可以初步锁定问题点出在脉冲编码器没有及时检测到零位检测信号或丝杠与电机之间的联轴器未安装好导致出现相对滑动造成的问题。
故障处理过程:为确认问题的原因,先脱开了电动机与丝杠间安装的联轴器,并通过手动方式触发参考点减速开关信号,再进行回参考点验证,通过此种方式,返回参考点总能固定停在某位置上,这说明编码器没有问题,它能正常并及时检测到零位信号,问题的原因很可能出在电机与丝杠的机械连接上。经过仔细检查,原来是丝杠与联轴器间的配合存在间隙,并没有完好连接导致出现松动。重新安装后,执行返回参考点正常,位置也固定,机床故障解除。
5 、结束语
在机加工领域,在出现无法返回参考点故障时,应该根据返回参考点的方式原理,从理论上进行故障现象分析诊断,再根据步骤来排除故障,否则使用时会直接影响到零件的尺寸加工精度,另一个重要的是要清楚出现无法返回参考点故障的可能原因及处理步骤,毕竟导致无法返回参考点的原因很多,但原理相对简单,只要按流程处理定能将故障解除。本文通过原理与实例分享了返回参考点故障的排除方法,希望能将返回参考点问题处理经验分享到其它工厂。
投稿箱:
如果您有机床行业、企业相关新闻稿件发表,或进行资讯合作,欢迎联系本网编辑部, 邮箱:skjcsc@vip.sina.com
如果您有机床行业、企业相关新闻稿件发表,或进行资讯合作,欢迎联系本网编辑部, 邮箱:skjcsc@vip.sina.com
更多相关信息