基于 FANUC 数控系统的信号跟踪功能的实现
2024-9-3 来源: 北京发那科数控工程有限公司 作者:王宝平 王卫红
一、信号跟踪功能的内涵
随着数字技术的发展,发那科数控系统采用的 CPU 计算处理速度越来越快,数控系统的内置 PMC 的扫描时间也越来越短,技术人员对于 PMC 很多信号的快速变化已经无法通过肉眼的观察得到,需要采用信号跟踪的方法加以记录后才可以用于信号时序确认和故障报警的精确分析。
信号跟踪功能主要应用为记录信号的瞬时变化、记录信号随时间变化的周期、记录信号间时序关系等等,该功能对于调试和维修人员有着非常大的用途 , 下面介绍其使用方法并以案例的方式分享在实际工作中的应用与作用。
二、信号跟踪功能的使用方法
本文以数控机床普遍使用的 FANUC 0i-F 系统为例加以说明。
1.信号跟踪功能的方式选择
首先按下 MDI 面板上的功能键 [SYSTEM],再依次按下扩展软键 [+]、[PMC 维护 ]、扩展软键 [+]、[ 跟踪设定 ] 软键后,显示 PMC 信号追踪 ( 参数设定 ) 画面页面 1 采样设定画面如图 1 所示。其中主要参数设定如下 :
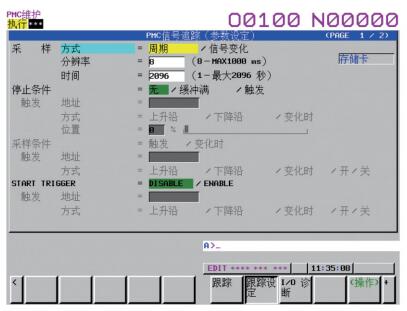
图 1 PMC 信号追踪(参数设定)页面 1 采样设定画面
(1)采样方式分为 : 周期和信号变化两种方式,周期方式为按采样的时间记录信号 ; 信号变化方式为按采样地址信号的变化记录信号。
(2)分辨率设定范围为(8~1000ms), 一般采用为 8ms。该值设定越大对信号变化的敏感度会降低,造成可能追踪不到小于分辨率的信号的变化。
(3)采样时间为采样方式为周期方式时,可以根据需要设定的采样时间,当分辨率为 8ms时设定范围为(1~2096s)。
(4) 停止条件、采样条件(采样条件只有在信号变化方式时才有效)、START TRIGGER( 触发开始 ) 依据实际需要设定地址的变化方式。
2.信号跟踪功能的采样地址的设定
信号跟踪功能的采样地址的设定有如下的两种方法 :
(1)在采样地址页面直接输入跟踪信号地址例如根据跟踪图 2 中线圈 A0.2 报警的相关地址可在采样地址页面依次输入 X70.1、F1.1、K0.2、A0.2 得到如图 3 所示的内容。
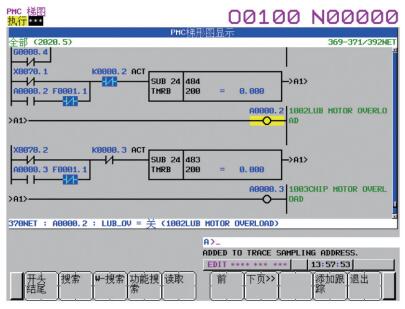
图 2 追踪线圈 A0.2 报警相关信号地址梯形图
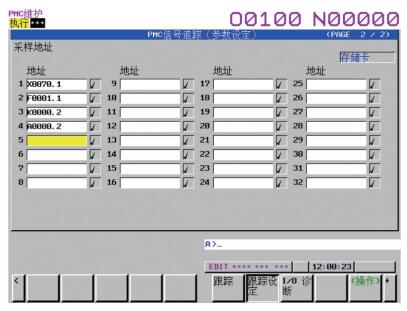
图 3 PMC 信号追踪(参数设定)页面 2 采样地址
(2)在梯形图搜索菜单中通过光标选中地址添加跟踪的方法
例如在图 2 先通过 [W- 搜索 ] 搜索到线圈A0.2,通过按下 [ 添加跟踪 ] 软键把 A0.2 添加到采样地址页面中,依次移动光标选中 K0.2、F1.1、X70.1 分别按下 [ 添加跟踪 ] 软键,也可以得到如图 3 所示的采样地址内容。
3.信号跟踪功能启动与停止
(1)手动跟踪
在[PMC配置]下级菜单[设定]中设定[跟踪启动]为手动,那么在[跟踪]画面中的[操作]中 , 通过按下 [ 开始 ] 或者 [ 停止 ] 软键来手动控制跟踪信号的启动和停止。
(2)自动跟踪
在[PMC配置]下级菜单[设定]中设定[跟踪启动 ] 为自动或者在 [PMC 维护 ] 下级菜单 [K参数 ] 中设定 K906.5 为 1,那么在系统上电后就可以自动启动信号跟踪功能了。
三、信号跟踪功能的作用与应用
1.调试或者维修工作中PMC输入点的对点在调试或者维修工作中需要确认数控设备外设的到位开关、操作按钮等进入数控系统的 I/O模块的输入信号状态的好坏,如果数控设备体积较大一般需要两人来进行确认,一人在数控系统显示屏上观察输入点的状态,可通过 [PMC 维护 ]中的 [ 信号状态 ] 中的到位开关、操作按钮等输入信号相应的 X 地址的变化来进行确认 ; 而另一人在设备外设(远端)来进行到位开关、操作按钮等硬件输入信号的接通或者闭合工作,通过两人密切配合很方便快捷的进行确针对大型设备而言,如果只有一名技术人员时用以上确认的方法就有些顾此失彼了。因此可以采用先在数控系统上,把需要确认外设的输入点地址依次通过信号跟踪画面来进行设定(一般选择信号变化方式),启动信号跟踪后,技术人员再去大型设备的外围依次进行到位开关、操作按钮等硬件输入信号的接通或者闭合工作,再在数控系统上进行信号跟踪的停止,通过移动光标很方便的观察到刚才接通的输入信号的状态如图4 所示,从而方便的完成硬件输入点的对点工作。
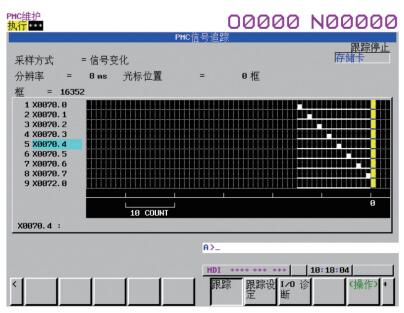
图 4 PMC 信号追踪用于 PMC 输入点确认
2.PMC调试工作中动作时序的确认
上海某知名汽配厂 1 条汽车制动盘自动化生产线是依靠日本发那科机器人来完成钻孔、精车、动平衡工序的上下料、检测及钢印道序,以取代传统的人工上下料。其中 2 台数控立车(配置 FANUC 0i-TF 系统), 现在通过增加 PMC I/O 点的方式与上下料的机器人控制电柜(内有三菱外装 PLC)进行协议通讯,以实现机器人参与的工件自动上下料的功能。
前期设计依据机器人上下料动作流程结合机床本体的加工工艺流程,编制了数控立车机器人上下料 PMC 动作序图如图 5 所示。在原系统PMC 的基础上依据时序图增加了机器人上下料的相关内容。加工程序中增加了联机方式下执行的 M95 代码(机器人上下料)。
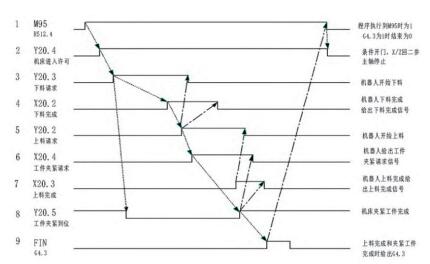
图 5 机器人上下料系统 PMC 动作时序图
在改造现场调试时,我们应用信号跟踪功能对更改后的数控系统 PMC 程序及加工程序编制的正确性进行验证,跟踪在执行 M95 相关的PMC I/O 点时序是否和图 5 一致,通过不断在线修改 PMC 程序,直到信号跟踪画面显示正确的相关信号时序如图 6 所示(和图 5 所示时序保持一致)。
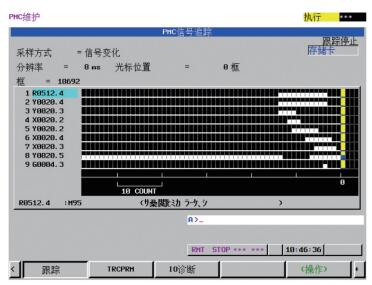
图 6 PMC 信号追踪用于机器人上下料 PMC 动作时序确认
通过对相关信号进行信号追踪,可以快速验证改造技术设计方案、PMC 程序、调用的动作宏程序的正确性,并能快速查找出动作信号时序上存在的各种问题,并通过不断分析、完善、优化直到满足设计要求,节约了现场调试时间,提高了工作效率。
3.在提升机床加工效率方面的应用
在拥有数控机床从事机械加工的企业,如何提升数控机床的加工能力,提高加工效率是一个永恒的课题。
一般工件的完整加工时间包含切削时间和非切削时间。切削时间为刀具加工接触工件的时间,而非切削时间由机床工件或者刀具快速定位时间和机床辅助动作(如刀具交换、工作台交换、自动门开关等)时间组成。在确保安全可靠的前提下如何减少机床辅助动作的时间,提高机床的使用性能也是提升机床加工效率的一个非常重要的有效途径。利用 FANUC 数控系统的信号跟踪功能的周期采样方式可以精准跟踪到机床辅助动作例如换刀动作的完整时间和分部动作的时间,加以分析研究找到制约总体换刀时间的关键因素,对该分步动作的执行器件和到位检测开关等多方面进行针对性的分析和有效调整,以减少该分步作的动作时间,从而达到减少机床总体的换刀时间提升机床加工效率的目的。下面以一台配置 FANUC 数控系统的斗笠式换刀的立式加工中心为例进行简要说明。
主轴上无刀,换刀位为 1 号刀具,主程序执行 T2M06,T 代码调用 O9000 号宏程序(以下程序经过简化)将刀库上的 2 号刀装载到主轴上。O9000 号换刀宏程序如下(左边为宏程序内容,右边为内容注释)。
O9000
N10M19; 主轴定向
N20 T#149G91G00G28Z0;执行T代码找新
刀结束 ,Z 轴回 1 参
N30M20; 刀盘移到主轴侧
N40M25; 主轴刀具松开并吹气
N50G91G00G30P2Z0;Z 轴回 2 参
N60M26; 主轴刀具夹紧
N70M21; 刀盘移到待机侧
N80 G91G00G28Z0;Z 轴回 1 参
N90M99; 返回主程序
PMC 信号追踪(参数设定)页面 1 采用如图 7 所示的周期采样方式 ; 分辨率采用 168ms;触发开始条件为地址 F94.2 的上升沿 ; 停止条件为地址 X79.0 信号的上升沿。记录的相关信号在换刀过程中的随时间变化的周期如图 8 所示。
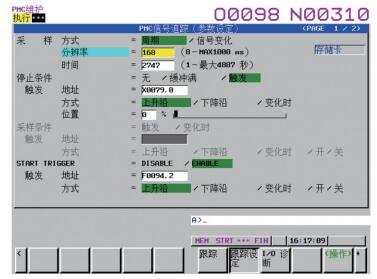
图 7 斗笠式刀库换刀 PMC 信号追踪(参数设定)页面 1
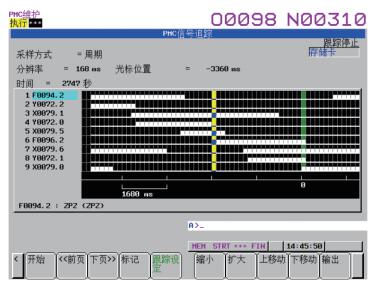
图 8 斗笠式刀库换刀时 PMC 信号追踪图
相关信号说明如表 1 所示 ; 斗笠式刀库换刀时 PMC 信号追踪计算时间表如表 2 所示。
表 1 斗笠式刀库换刀时 PMC 信号追踪含义说明表
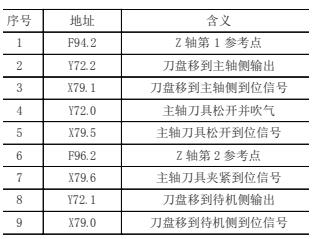
表 2 斗笠式刀库换刀时 PMC 信号追踪计算时间表
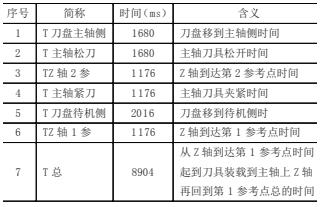
从表 2 计算分析出 ; 从 Z 轴到达第 1 参考点的时间算起、到刀具装载到主轴上、随后 Z 轴再回到第 1 参考点,总的换刀时间为 8.904s,组成为三部分分别为 :Z 轴从 1 参往返 2 参时间 ; 主轴刀具松开 / 夹紧时间 ; 刀库移动到主轴侧 / 待机侧的时间。综合分析该立式加工中心斗笠式换刀的机械结构和气动部件动作特点 : 主轴松拉刀动作打刀气缸动作行程较短,调整可节省时间非常有限,非影响换刀时间的关键因素 ; 刀库移动到主轴侧/待机侧的时间分别为1.68s和2.016s,基于刀库移动到主轴侧 / 待机侧气缸行程较长的特点,在动作平稳可靠的前提下通过调节 2 个动作气缸端部的气流调节阀,使刀库移动到主轴侧/ 待机侧的时间分别提速到 1.3s 和 1.4s,合计比原来节省了0.996s;Z轴从1参往返2参的动作执行的 G00 快速移动的速度,在运动平稳可靠的前提下,将参数 1420 即 Z 轴的快速移动速度由原来的 4000mm/min 提高到 6000mm/min,使 Z轴从1参往返2参的时间合计比原来节省了0.7s。总的节省时间为 1.696s,从而节约了该机床的换刀时间,提高了该机床加工效率,使该机床日加工能力得到小幅提升。
4.维修工作中的故障原因分析
配置 FANUC 数控系统的数控机床在实际维修工作中,经常遇到出现系统 PMC 报警时,要根据电气故障现象综合分析系统 PMC 逻辑关系才能最终锁定故障源头的情况,而往往无法用常规的用肉眼来观察 PMC 的逻辑关系和信号流向,因为有些信号是一闪而过,很难用肉眼来锁定它。尤其对于可能几个小时或者一、两天才出现一次的软故障而言,事后靠常规检修方法和分析 PMC 时可能存在多种可能性,很难及时准确判断故障点。而熟练使用 FANUC 数控系统的信号跟踪功能可以帮助维修人员快速跟踪故障报警的相关信号来源和流向,通过精准分析信号时序关系,有助快速的锁定故障源头,快速修复故障。空调曲轴生产线上 1 台配置 FANUC 数控系统的止推面磨床,在其生产过程中不定期的出现 EX1015 CLAMP PRESSURE LESS! 的报警信息,含义为夹紧压力低,同时出现报警后磨床退回到 X 轴机械零点的故障现象。磨床的作流程为 : 空调曲轴生产线的机械手先拿走主轴夹具上的已经加工完的工件,再放置未加工的工件,靠尾架前进来进行定位后主轴夹具再夹紧,夹具夹紧后尾架后退到位后,磨床前进进行磨削加工。维修人员现场分析认为 : 轴夹具的夹紧 / 松开、尾架前进 / 后退的液压执行元件、相应的到位检测开关都和该EX1015号报警相关。
维修人员检测相关线路接线和接触正常,报警复位消除后手动分部操作,动作和到位开关检测都正常,因此怀疑可能是联线生产加工过程尾架前进到位检测开关(PMC 地址为 X1.4)性能不良引起的报警信息。
为了精准锁定故障来源验证分析的正确性,采用数控系统的信号跟踪功能,选择 “信号变化”采样方式,对和 EX1015 号报警相关的 X、Y、R、A、G 地址进行信号跟踪。在启动跟踪开始后该磨床继续联线生产加工,在加工几个小时后再次出现 EX1015 号报警和磨床退回到 X 轴机械零点的故障现象,此时跟踪结果画面如图 9 所示。维修人员结合 PMC 逻辑关系进行了分析,Y1.2 尾架前进动作到位后,到位检测信号 X1.4 未发出,2 秒后 R251.3 信号接通,A1.5 报警(画面出现
EX1015 号报警)随后接通 G66.4(X 轴退回机械零点 )。至此将故障原因精准锁定为尾架前进到位开关性能不良所致,随即进行了该开关的更换,后经长时间生产检验没有再次出现该故障报警。
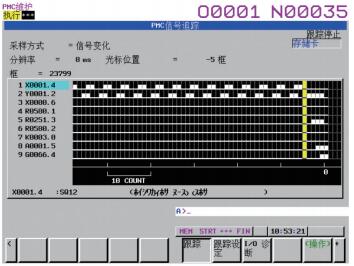
图 9 止推面磨床报警 PMC 信号追踪图
四、结语
本文简要介绍了 FANUC 数控系统的信号跟踪功能的内涵、使用方法及应用方面的具体案例,供大家在学习、科研、生产中加以参考和借鉴,这种方法有助于大家对 PMC 程序的相关信号的状态和时序关系进行精准微观的分析,可以结合常规检测、PMC 程序分析,依据实际情况加以酌情使用,进而在多个方面提高工作效率及设备的加工效率,更好的为科研生产服务。本文基于 FANUC 数控系统的信号跟踪功能的实现使用的是 FANUC 0i-F 系统,其原理方法也适用于 FANUC 0i-D、0i-F Plus、30i/31i/32i/35i 等系列系统。
投稿箱:
如果您有机床行业、企业相关新闻稿件发表,或进行资讯合作,欢迎联系本网编辑部, 邮箱:skjcsc@vip.sina.com
如果您有机床行业、企业相关新闻稿件发表,或进行资讯合作,欢迎联系本网编辑部, 邮箱:skjcsc@vip.sina.com
更多相关信息