西门子828D数控系统在展刀上的应用研究
2024-1-23 来源: 万向钱潮股份公司 作者:张银桥 姚礼军
摘要:基于西门子828D数控系统,设计了一套带有展刀头的车加工机床控制系统,主要由西门子828D数控系统、基恩士高精度接触式传感器、输入/输出模块、S120伺服驱动器、伺服电机和绝对位置编码器组成。利用数控系统的轴耦合功能,使展刀径向位移与轴向进给能够在金属切削加工时做到插补运算,满足外圆、圆弧、倒角等加工要求。与普通数控车床相比,应用展刀技术的车床具有加工效率和精度高,刚性好,机床结构紧凑,操作方便等特点。
关键词:展刀头;展刀动力头结构;虚拟轴;轴耦合;伺服控制
0 引言
展刀头是一种在随主轴旋转时还驱动刀具进行径向位移的装置,常用于非标准专用切削类机床。其动作与原理如下:通过驱动位移拉杆向后位移来带动滑块移动,主要是位移拉杆驱动斜柄使滑块做径向位移,从而带动安装在滑块上的刀架在旋转的同时做径向运动进行切削。双刀展刀头(图1)应用广泛,适用于圆孔内外加工、车铣、车牙、搪沟槽、锥形、凹面或凸面等圆球面加工。
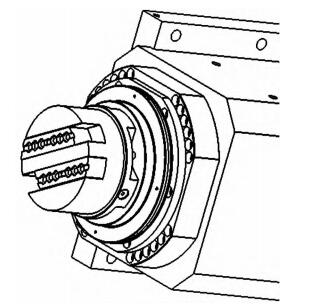
图1 展刀头示意图
1、驱动方式分类及展刀动力头结构
针对展刀盘滑块径向运动,目前有两种驱动方式,一种是靠液压传动来控制展刀径向行程,另一种是通过伺服来控制展刀径向行程。其中,液压控制展刀响应速度慢、精度低,应用场合有限;而伺服控制展刀响应速度快、精度高,可以利用现有数控技术的插补功能,
实现圆弧面加工。
文献[1]的专利提供了一种展刀动力头结构(图2),其由双伺服驱动分别驱动展刀头旋转和展刀滑块相对移动,主要包括主轴、丝杆、滑块、展刀盘和主轴箱体,主轴通过两只主轴轴承支承在主轴箱体上,外部的伺服电机通过驱动带轮驱动主轴旋转,带动展刀盘上的刀具做旋转运动。具体传动方式如下:展刀盘22中心的滑块7沿主轴轴向做前后运动时,滑块7两侧的斜齿结构驱动径向的刀体滑轨21做径向运动,从而驱动安装在其上面的刀具进行径向调节,主轴3前端安装丝杆6用于驱动滑块7,丝杆6由螺母座套筒8后端的展刀带轮5驱动,通过控制展刀带轮5与主轴3之间的差速,实现对丝杆6精确的位置控制。
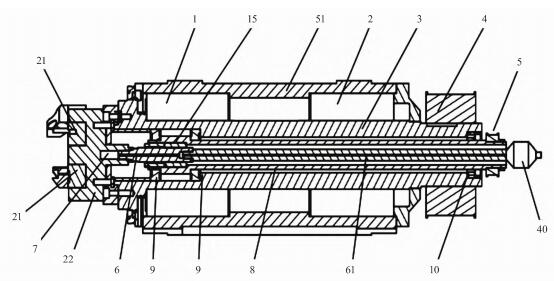
1—主轴轴承A;2—主轴轴承B;3—主轴;4—主轴带轮;5—展刀带轮;6—丝杆;7—滑块;8—螺母座套筒;9—轴承;10—支撑轴承;
15—螺母;21—滑轨;22—展刀盘;40—配油器;51—主轴箱体;61—配油管。
图2 展刀动力头结构
2、伺服驱动的具体实现方法
2.1 系统配置
设备控制采用西门子828D数控系统,配备3个驱动器和3个伺服电机。其中一个伺服控制主轴带动展刀盘旋转;一个伺服控制刀体滑块移动,需要配合主轴做同步运动才能控制展刀位置稳定不变,当需要改变展刀径向位置时,要求当前伺服电机在耦合主轴同步转速的基础上进行位置控制,耦合技术详见文献[2];剩下的一个伺服控制整个展刀动力头做轴向往复运动。在选择828D数控系统车床版本时,要注意选择能够兼容四轴及以上的版本,因为控制设备运行时用到虚拟轴技术,占用一个轴的位置,它是由主轴和控制展刀的伺服轴耦合出来的,在系统上表示展刀径向位移,并且在数控系统里要对虚拟轴进行NC参数设定。数控系统需配置“电子齿轮”功能选项,使用辅助功能“电子齿轮”可以控制跟随轴运动,使之按照线性运动偏移与最多五个引导轴相关联运动,引导轴和跟随轴之间的关联按照每个引导轴通过耦合系数进行定义,算出的跟随轴运动分量是由单个引导轴运动分量乘各自的耦合系数通过加法构成。
2.2 系统输入/输出分配及作用
系统的输入/输出配置如表1所示,其中DI0.1~DI0.4接的是基恩士GT2-70系列接触式位移传感器,该传感器有5路输出,分别为良、H、L、HH、LL,表示传感器将量程分成了5段,测头位于相应的分段内,传感器就给出对应的信号,把“良”信号接入系统背面X242.6接口,用于快速响应,其余传感器输出接入PLC输入口。
该传感器安装在展刀动力头末端,用于测量展刀滑块的移动量,尽管展刀滑块在展刀盘内部,无法直接测量,但是可以通过测量连接展刀滑块的丝杆的相对位置的移动,通过换算间接测得展刀滑块径向移动的距离,测得的丝杆的位置变化与展刀径向位置变化成线性关系。设备在进行车削加工前需确定一个基准点,在基准点这个位置,测量得出展刀盘上两把车刀刀尖距离,这个具体同位置传感器当前读数对应,当每次找到这个基准点时,设备总是能知道当前车刀刀尖距离。但设备实际运行过程中,传感器测到这个基准点时会有信号传递上的误差,如果以控制系统收到这个信号为基准点,时间上的差异将导致基准的重复精度不够,满足不了设备加工要求。联想到传统的带相对位置编码器的伺服回零方案,也是先找到回零信号,再寻找编码器零点信号完成回零动作。设备主轴和同步轴都采用了单圈绝对位置编码器,当找到传感器的基准点后,接着让同步轴往固定方向转动,直到主轴和同步轴角度数值完全一致,这样就可以非常精确地对零。
表1 IO输入/输出表
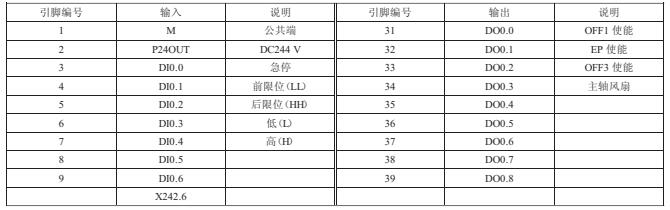
2.3 系统的连接和功能调试
系统的连接根据西门子提供的828D简明调试手册进行,在数控系统里将所有NC轴配置完成,并根据828D数控系统参数手册设置好对应轴的NC参数,X轴是伺服进给轴,U轴是同步主轴,SP是主轴,V轴是主轴和同步轴耦合出来的虚拟轴,代表径向位置,V轴的位置0表示寻零位后的参考位置,不代表展刀盘上的两个刀尖实际距离为0,因此需要在设备回零后,测量两把刀尖实际距离,并把对应的数值换算后写入V轴偏置设定中,这样设备在实际加工作业时,X轴和V轴是两个互为插补轴。
同步功能的启用,根据828D工作准备部分编程手册,首先在“制造商循环”目录下导入CYCPE_MA文件,类型为SPF,用记事本打开内容为:
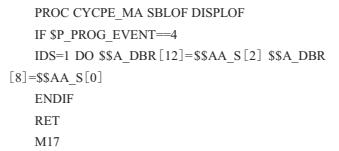
每次系统重启上电就执行同步动作,将主轴和同步主轴的速率实时提取出来,分别赋值给DB4900.DBD8和DB4900.DBD12,PLC通过对这两个数据的处理,可以实时监控这两个轴的转速和同步功能执行情况,并做出相应的应答处理。在系统上电完成,未运行任何程序的情况下,主轴和同步主轴还没有处于耦合状态,只是PLC程序对两个轴的速度进行了监控。要想耦合轴数控系统需要运行一段加工程序,在该程序中,还要完成展刀的寻零动作,保证每一次设备断电重启之后找到的都是同一个零点,也就是找到零点时,双展刀的刀尖距离都是同一个数值。以下是运行的加工程序:
1.EGOFS(U1)
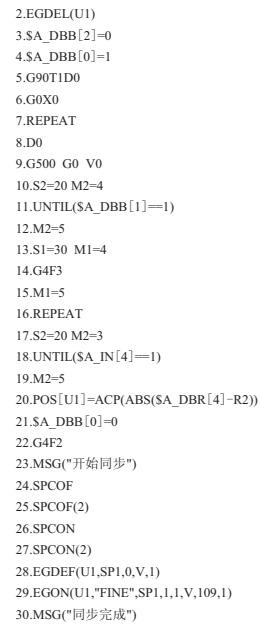
程序运行原理如下:
第一步,取消耦合功能,让主轴和同步主轴处于能够自由运动状态,理由是当设备完成耦合功能时,可能需要再次进行回零操作,这时候如果没有取消耦合功能的话,同步主轴处于耦合状态,只能跟随主轴同步运行,无法实现自由转动,也就不能执行寻找零位。
第二步,取消展刀滑块到达限位就触发系统复位的限制,然后执行同步主轴往展刀张开方向转动,当展刀滑块达到张开最大限位时(即传感器测头位于LL区域)同步主轴停止,主轴往反方向转动3 s停止,使展刀滑块往回收缩,接着同步主轴往反方向转动,使展刀滑块进一步收拢,一直到零点信号(即传感器测头位于“良”区域)触发停止。零点信号直接接入系统背后的快速输入/输出点X242.6,提高零点信号的系统响应速度。接着,定位同步主轴使同步主轴角度跟随主轴角度持一致,至此,整个寻零动作完成。
第三步,改变限位功能,$A_DBB[0]=0,通过PLC对这个信号的处理,当展刀滑块运行到设定的最大距离(即传感器测头位于“LL”区域)和最小距离(即传感器测头位于“HH”区域)时,系统能做出复位的应答反应并进行报警提示,目的是保护展刀头,由于展刀头上
的滑块有机械位置限制,在到达机械限位之前先触发软限位,可以起到保护机械机构的作用。
第四步,应用轴耦合指令开启轴同步功能,并对耦合关系进行参数设定,当前程序中,使用了一个跟随轴U与两个引导轴(分别是SP1轴和V轴)的耦合关系,SP轴为实际主轴,耦合类型为0,V轴为虚拟轴,耦合类型为1,并在下一行指令中对电子齿轮比值进行了设定,当完成同步功能后,不能对页面上的同步主轴U进行单独控制,它是跟随主轴SP1和V轴的位置关系分量进行耦合计算后得到的,在加工程序中,X轴表示进给,V轴表示展刀径向位置,SP是主轴,加工程序的编写跟普通车床类似,具体如下:
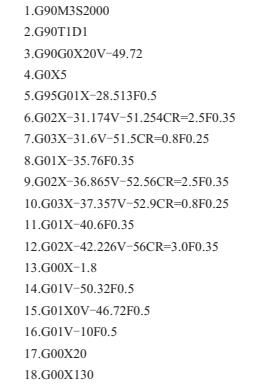

这是一段车外圆并有圆弧台阶衔接的圆柱体的程序,X坐标是圆柱体轴向位置,V坐标是车刀径向位置,两把车刀对称布置,切削径向力可以相互抵消,加大一次走刀量,大大提高加工效率。
3、结语
通过引进先进的展刀结构理念,本文分析设计了展刀动力头传动机构,结合西门子828D虚拟轴耦合技术,将展刀复杂的控制运算化简为一台普通车床的编程逻辑,并进行实物制作和实践应用,取得圆满成功。应用了展刀技术的车床跟普通数控车床相比,具有加工效率和精度高,设备刚性大,加工尺寸稳定,编程简单等特点,相信类似的应用在金属加工行业中会越来越广泛。
投稿箱:
如果您有机床行业、企业相关新闻稿件发表,或进行资讯合作,欢迎联系本网编辑部, 邮箱:skjcsc@vip.sina.com
如果您有机床行业、企业相关新闻稿件发表,或进行资讯合作,欢迎联系本网编辑部, 邮箱:skjcsc@vip.sina.com
更多相关信息