普通组合机床上深孔加工技术的研究
2018-12-14 来源:广西玉柴机器股份有限公司 作者:冯基
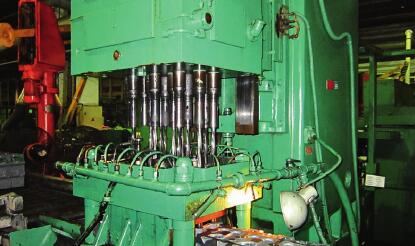
本文提出了基于普通组合机床上加工深孔(阶梯深孔)一系列加工技术,解决了加工柴油机发动机气缸盖过钉孔、导管底孔、喷油器安装孔等深孔(阶梯深孔)位置度、孔径难保证的难题,提高了产品的加工质量,降低了生产成本。
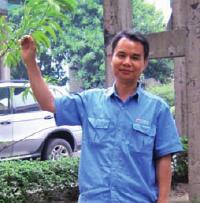
作者:冯基 广西玉柴机器股份有限公司三发厂技术科主任工程师,从事机加工现场工艺技术的工作已经有20多年,对解决机加工工艺技术疑难问题有着丰富的工作经验和较深的造诣。
普通组合机床上深孔(阶梯深孔)的加工是公认的难题,其位置度(特别是出口位置度)以及孔径精度很难保证。目前国内外对深孔加工一般采用枪钻(或枪铰),但是枪钻(或枪铰)对于小孔距的深孔(阶梯深孔)的孔系由于其结构的限制不能一次加工完成,需要采用多工位加工,因此,降低了生产效率,增加了加工成本。同时其对设备精度要求较高,普通组合机床不能胜任,因此投入大,不利于广泛应用。因此,必须突破普通组合机床上传统加工技术的局限性,发展出全新的深孔(阶梯深孔)加工技术。
前、后同时导向深孔加工技术柴油发动机气缸盖过钉孔深9 6 m m ,孔径φ 1 5 m m ,长径6.4,属深孔,采用的加工技术为第一道工序钻φ14mm孔,第二道工序扩φ15mm孔。普通组合机床上传统的扩孔技术采用如图1所示的后导向方式,其目的是为了修正第一道钻孔工序的位置,但是由于扩孔刀在开始切削时受到第一道钻孔工序位置偏差大的影响而造成加工余量不均匀,受到不对称的径向力挤向余量小的方向,因此刀具开始切削就有倾斜的趋势。随着加工孔的深度增加,扩孔刀的悬伸也随之增加,其刚性变得来越差,并且开始出现变形弯曲,越来越倾斜。当加工到达出口时其位置偏移达到最大。可见,传统的后导向的扩孔技术由于无法解决刀具的刚性问题,因此对过钉孔位置的修正是有限的。
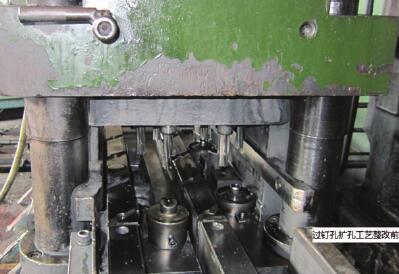
图1
因此,要解决过钉孔出口位置偏的加工难题,必须解决扩孔刀刚性差的问题。图2是对扩孔专机的夹具、刀具进行改进,夹具上增加了前导向装置(由前导向模板、前导向套等组成),扩孔刀增加了前导向。加工时刀具前后导向分别进入前后导向套定位,然后开始切削加工。由于在切削加工过程中刀具始终有前后导向套的支撑定位,因此其刚性得到了显著加强,从而有效地克服了刀具的变形弯曲,保证了过钉孔入口、出口的位置度。为了解决排屑及掉刀问题,将扩孔刀设计成左旋右切(见图3),这样刀具自然形成的负前角可以使切屑顺利地向前排出,同时左旋的螺旋槽可以使刀具在回转时受到一个沿轴向向后的推力,防止刀具退回时被从接杆拉下来卡在工件里。
由于过钉孔是深孔,刀具的后导向部分必须得进入已加工孔内,且其长度随着加工孔深度的增加而增加,故后导向部分与孔壁的摩擦力越来越大,严重时刀具被“抱死”,甚至被扭断,同时电动机因为过载而跳闸。因此,为了减少刀具后导向部分与已加工孔的摩擦力,刀具后导向部分的直径必须比切削部分的直径小,优选小0.02~0.03mm,不能小太多,否则会影响导向精度。同时刀具切削部分的材料要选择耐磨性较好的合金,防止刀具磨损过多后出现“抱死”现象。经过使用验证, 合金YS8或YS10使用效果很好,新刀加工件数多达9 000件以上,而且可以反复刃磨利用。为了解决定位销的定位、导向、排屑的问题,如图3所示,在定位销上设置了排屑孔、导向孔及让刀孔。其工作原理如下:前后导向刀具的前导向穿过工件的待加工孔,并进入定位销中心的导向孔,同时刀具的后导向也进入夹具后导向模板的导向套,接着刀具开始对工件的待加工孔进行切削,产生的切屑的一部分通过刀具前导向的螺旋槽排出,一部分通过定位销法兰的3个排屑斜孔排出。当刀具切削刃部分进入定位销避开刀具的让刀孔时,整个加工过程完成。
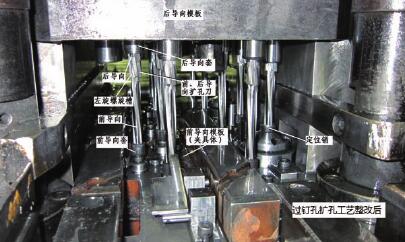
图2
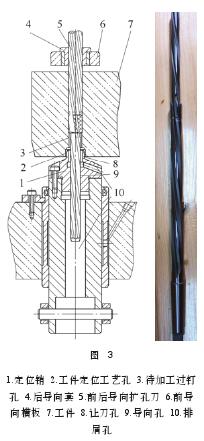
图3
前导向深孔加工技术柴 油 机 气 缸 盖 导 管 底 孔φ15.2mm及气门座孔组成阶梯深孔(其中导管底孔是深孔),为了修正上道工序加工误差,普通组合机床上其半精加工如图4所示采用传统的镗孔加工技术。但由于导管底孔镗刀杆直径小,悬伸长(小镗刀到气门座孔镗刀距离约86mm),刚性不足,加工时受力时摆动大,因此加工的导管底孔孔径有锥度,直线度、位置度、垂直度等变动大。特别是与气门座孔不同轴,经常因为这些问题影响精加工工序精铰导管底孔的精度,如铰不出,位置度、垂直度、特别是同轴度差等。
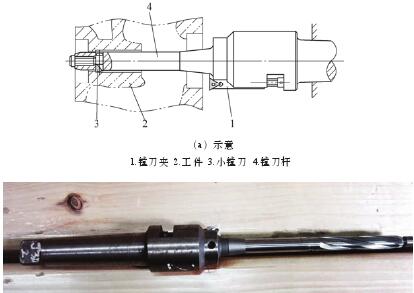
图4
为了有效解决上述问题,必须将φ15.2mm导管底孔的镗刀杆的刚性加强,因此,如图5所示,改进了模板及镗刀杆。为了降低镗刀杆的制造难度、制造费用,将其设计成组合装配式,即将其设计成加工细长导管底孔部分的前导向镗刀杆及加工较大气门座孔部分的气门座孔镗刀杆,然后将前导向镗刀杆安装到气门座孔镗刀杆上,两者采用H6/h5配合联接,并用夹紧螺钉压紧前导向镗刀杆的斜面。一方面可以传递转矩,一方面产生的轴向分力可以使它们的端面紧密贴合,保证装配后它们的同轴度及刚性;为了提高前导向镗刀杆抗疲劳强度,将安装小镗刀的安装槽设计成圆形;为了解决小镗刀的紧固和定位问题,采用了通过螺钉压分段顶杆去压小镗刀的扁位实现,同时也解决了细长螺钉加工困难的问题;为了减少前导向镗刀杆与导向套的摩擦力,在前导向镗刀杆上加工出四条15°螺旋槽,形成四条宽度为4~5mm圆柱导向带。进行加工时,前导向镗刀杆导向部分部首先进入导向套,然后开始加工细长导管底孔,加工完细长导管底孔后,接着加工较大气门座孔。由于镗刀在整个加工过程中(包括细长导管底孔、较大的气门座孔加工)前导向镗刀杆都有前导向套的定位导向,因此镗刀杆特别是细长导管底孔前导向镗刀杆的刚性得到显著增强,从而根本上解决了加工细长导管底孔因镗刀杆直径小、悬伸长刚性不足所引起的摆动,进而解决了加工细长导管底孔孔径有锥度,直线度、位置度、垂直度变动大,及其与较大气门座孔不同轴等加工难题。
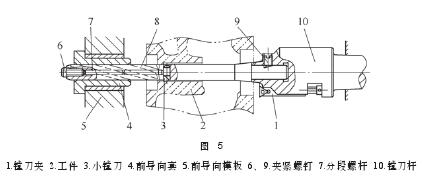
图5
先后导向,然后前、后导向深孔加工技术 如 图 6 所 示 , 柴 油 机 气 缸 φ25mm×φ12mm×φ9.3mm喷油器孔是阶梯深孔(其中φ12mm、φ9.3mm是深孔),上部φ25mm
孔与下部φ25mm之间是空腔,其轴线与气缸盖底面成67°夹角,普通组合机床上传统的精加工技术采用如图7所示的后导式复合精铰。由于是阶梯斜孔,加工时极易偏移,φ25mm孔中间的空腔降低了刀具在φ25mm孔内的自导作用,刀具φ9.3mm部分悬伸长(切削刃端面到导向套端面约90 mm),刚性不足、摆动大,因此φ9.3mm喷油器孔出口轴线与底面交点到定位孔的尺寸(83±0.1)mm很难保证,长期以来该尺寸都无法得到了有效控制,而该尺寸却是喷油器孔的关键尺寸,其加工的好坏直接影响喷油器安装的配合精度及位置精度,从而影响整机的性能和可靠性。
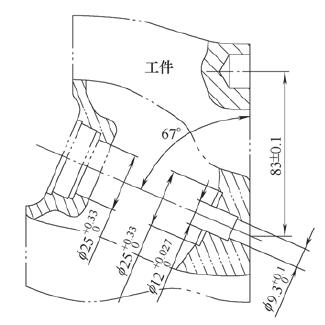
图6
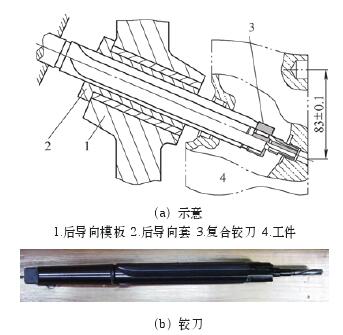
图7
针对上述阶梯喷油器孔精加工技术的缺陷,开发出了一种全新新的精加工技术,具体为,本技术采用前后导向型复合铰刀分两步进行精加工,加工上部φ25mm孔(见图6)时,如图8所示,由于上部φ 25m m孔靠近后导向套,前后导向型复合铰刀的导向精度高、刚性好,首先保证上部φ25孔的位置精度;加工下部φ25mm、φ12mm、φ9.3mm孔时,前后导型复合铰刀的前导向段已经伸入前导向套,此时,前后导向型复合铰刀不仅有后导向套的定位,而且有靠近下部孔的前导向套定位,刀具的刚性得到了加强,提高了定位精度,因此,保证了下部孔的位置精度。
结语
组合机床上深孔加工技术的开发应用成果适用于机加工行业深孔(阶梯深孔)的加工,解决深孔(阶梯深孔)加工位置度、孔径等难保证的难题,提高了产品的加工质量,降低了生产成本,提升了产品的市场竞争力,产生了巨大的直接、间接的经济效益、社会效益,在机加工行业有着广泛的推广价值。
投稿箱:
如果您有机床行业、企业相关新闻稿件发表,或进行资讯合作,欢迎联系本网编辑部, 邮箱:skjcsc@vip.sina.com
如果您有机床行业、企业相关新闻稿件发表,或进行资讯合作,欢迎联系本网编辑部, 邮箱:skjcsc@vip.sina.com
更多相关信息