数控车床滚珠丝杠副的选型计算
2023-5-5 来源: 南京工艺装备制造有限公司 作者:冯宇
摘要 : 基从一般滚珠丝杠副的螺母选择、螺母安装及支撑形式等角度介绍了车床滚珠丝杠副的选型思路,属于选型计算校核过程的前处理过程,能帮助车床设计者快速确定所需丝杠副的大类与螺母型号,具有参考与指导意义。
关键词 : 数控车床 ; 选型 ; 滚珠丝杠副
1. 序言
在卧式车床的数控化改造或数控车床的新设计中,滚珠丝杠副作为数控传动系统的关键部件之一,其选型及安装的合理性直接影响到数控车床(以下简称车床)的精度、寿命及性能。
目前,国内关于一般滚珠丝杠副的选型计算较为充分,如黄育全针对滚珠丝杠副的选型提出了一个初步成熟的算法。然而,车床行业的发展趋于功能专业化,如高速、高精度的要求或大型重载的情况等,此时需要在螺母选择、螺母安装及丝杠支撑形式等方面作针对性选型。
2. 滚珠丝杠副的螺母选择
2.1 循环方式选择
滚珠丝杠副按循环方式的不同分为内循环和外循环,滚珠在循环过程中始终不离开丝杠表面的称为内循环 ; 反之,为外循环。常见的浮动式、矩阵式结构为内循环,插管式及端块式或端盖式结构为外循环,如图 1 所示。
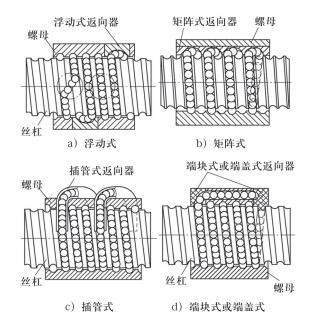
图 1 常见滚珠螺母结构形式
在相同导程与承载滚珠圈数的情况下,内循环存在无滚珠的滚道区域,故在轴向尺寸上较长 ;而外循环在轴向尺寸上结构相对紧凑,但滚珠的循环路线需要额外占用螺母的径向区域,即在相同情况下螺母的直径会增大,需要根据车床的具体安装部件的配合尺寸取舍。值得注意的是,同等条件下,外循环方式的 Dn 值比内循环方式更大,相同负载工况下能获得更高的寿命。
2.2 预紧方式与预紧力选择
为了保证丝杠副在车床上的重复定位精度,需保证滚珠螺母与丝杠之间无间隙,能够根据旋转角度和导程间接测量轴向行程。此时在滚珠螺母与丝杠之间需维持预紧转矩。螺母按预紧方式分为双螺母垫片预紧、单螺母增大滚珠直径预紧和单螺母变位导程预紧等。
车床大多数情况受力为单向,即可不考虑对反向间隙的控制,出于对成本及车床安装空间的考虑,推荐使用单螺母,预紧方式可以为增大滚珠直径预紧。
虽然存在反向切削力,但相比正向时要小得多,在高精度的应用场景下,可以使用非对称的双螺母预紧方式。预紧方式仍为垫片式,但法兰螺母与直筒螺母的圈数可以不同,能在不影响正向进给预紧转矩需求的同时降低螺母副长度,如图 2 所示。
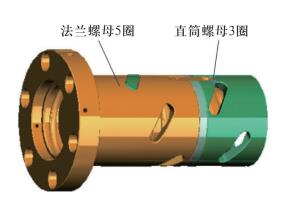
图 2 非对称双螺母预紧方式
在相同条件下单螺母能节省安装空间,但双螺母有着方便调整预紧力的优势,即在一定使用年限后,能通过更换预紧垫片重新调整预紧力的方式延长滚珠丝杠副的使用寿命。
预紧力根据车床进给系统的最大额定动载荷的一定比例选取。以我公司的企业标准为例,按预紧转矩取额定动载荷(Ca)的 3%、5% 和 7%,定为轻度、中度和重度预紧。轻度预紧多用于半精车、粗车等精度要求不高的车床上,大型车床为了避免预紧转矩的衰减可选用重度预紧。但是,预紧力过大会使摩擦力矩增大,从而增大温升,反而不利于精度保持,一般情况下选用中度预紧。
3. 螺母安装方式
3.1 螺母法兰方向
单螺母滚珠丝杠副在采用一端固定、另一端的支撑的支撑方式时,螺母有两种具体安装方式 :一种是螺母和工作台的联接法兰靠近支撑端、远离固定端 ; 另一种是螺母和工作台的联接法兰靠近固定端、远离支撑端。以向左运动为例,两种安装方式的受力如图 3 所示。
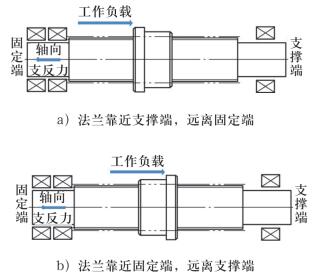
图 3 法兰两种方式受力
研究表明,螺母与工作台的联接法兰远离固定端相比靠近固定端的安装方式,钢球法向载荷与实际接触角的波动减小,有助于减少疲劳磨损,提高车床的精度保持性与寿命,但对滚珠丝杠轴向刚度的影响不显著。
对于双螺母滚珠丝杠,由于预紧力的作用,工作螺母承担大部分的轴向载荷,预紧螺母的受力不随安装方式变化,其安装方式的选择与单螺母类似。
3.2 双法兰螺母安装
(1)双法兰螺母 “背靠背” 安装形式(见图 4)常规双螺母垫片预紧方式的受力如图 5 所示。图中 P A、PB 为通过厚垫片使螺母 1、螺母 3 发生轴向位移,使滚珠分别与丝杠滚道的两个侧面接触时,一个滚珠给予丝杠的作用力向左,另一个
给予的向右。
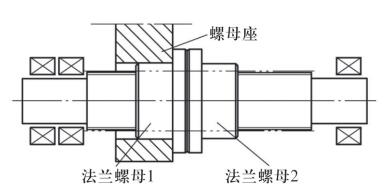
图 4 双法兰螺母“背靠背”安装形式
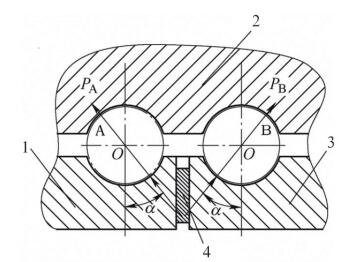
1、3—螺母 2—丝杠 4—垫片
图 5 双螺母垫片预紧方式受力
摩擦力矩与滚珠丝杠副的预紧力 FP 为正相关关系 ; 预紧力 FP 受两螺母之间的间隙控制,两螺母之间的连接刚度会严重影响预紧力,导致摩擦力矩波动,最终影响返程精度。图 4 所示的双法兰螺母安装形式可以显著提高两螺母之间的连接刚度,进而提高了车床的返程精度。如果车床设计上对圆弧插补有高精度要求,就可使用该安装方式。
(2)双法兰螺母 “面对面” 安装形式在大负载长丝杠的情况下,此时分散到螺母的受载滚珠上的载荷仍会很大,当螺母运行到远离固定端时,丝杠的弯曲将会很大,会出现精度漂移,此时宜采用 “面对面” 双法兰螺母安装形式。与单法兰安装丝杠形式受力(见图 6)不同,双法兰螺母“面对面” 安装形式中,丝杠的受力点由一个点变为一段区域,可以显著提高丝杠的抗弯能力,如图7 所示。但此时丝杠的预紧需通过调整螺母与螺母座之间的间隙实现,即需要主机厂配磨垫片完成。此安装方式多见于大型数控车床、龙门立式铣床。
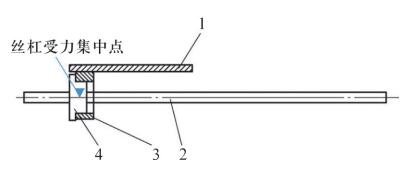
1—托板 2—丝杠 3—螺母座 4—法兰螺母
图 6 单法兰安装丝杠形式受力
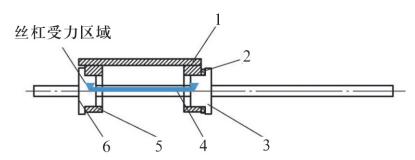
1—托板 2—垫片 3、6—法兰螺母 4—丝杠 5—螺母座
图 7 双法兰螺母“面对面”安装形式受力
4. 丝杠支撑及轴承选用
4.1 丝杠支撑方式
滚珠丝杠安装形式的优劣很大程度上决定车床的运动精度与加工精度。常见安装方式有 4 种(见图 8): ①一端固定,另一端自由。②两端支撑。③一端固定,另一端支撑。④两端固定。各安装方式所适用的加工情况如下 : 方式①适用于低速回转、丝杠较短的情况 ; 方式②适用于中速回转、精度不高的情况 ; 方式③适用于中速回转、高精度的情况 ; 方式④适用于高速回转、高精度的情况。
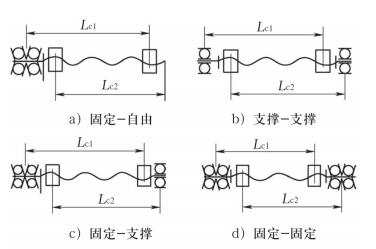
图 8 支撑方式
基于高速高精的车床发展方向,现采用一端固定支撑或者两端固定的方式居多。研究表明,两端固定的丝杠轴向刚度随着长度按抛物线规律变化,最大变形值在丝杠的中点,一端固定、另一端支撑的形式则变形量随着远离固定端的距离线性增大 ; 相同情况下,两端固定的轴向最大变形量要小,轴向刚度大,但存在安装零部件增多、安装调试复杂等问题。
在采用两端固定方式的情况下,为了提高刚度,减少因丝杠热膨胀带来的影响,需对丝杠采取预紧拉伸。一般建议每 1000mm 行程补偿值C 取-(0.02~0.03)mm。但考虑到轴承的受力,丝杠直径超过 50mm 则不宜预拉伸。
4.2 丝杠安装轴承选用
车床上滚珠丝杠副的安装轴承推荐使用滚珠丝杠副专用轴承,即 60°接触角的角接触球轴承。其中,“固定 - 自由” 与 “固定 - 支撑” 方式的固定端根据轴向力大小可选择三联或多联轴承组合。以受到向左的轴向力为例,三联轴承组合常见方式如图 9 所示。
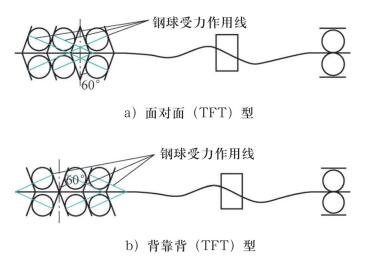
图 9 常见固定端轴承安装形式(三联)
面对面组配受力作用线向内收敛,轴承间的有效支点距离缩小,承受倾斜力矩的能力较差。背靠背组配受力作用线向外发散,轴承间的有效支点距离增大,有较大的承受倾斜力矩的能力。“固定 - 自由” 与 “固定 - 支撑” 支撑方式下依靠固定端的精确安装保证精度,故建议采用面对面型,但在精度要求不高或者其余零件易干涉的情况下,也可采用背靠背型,以降低安装难度。多联轴承的联配方式以车床主要切削力方向决定是否对称配置。以 “固定 - 自由” 与 “固定 -支撑” 方式下的固定端采用四联轴承为例,车床正向切削力为主时,四联轴承采用三正一反形式的非对称安装,保证轴承的单向最大承载能力 ;车床正反切削力差距不大时,采用二正二反对称配置,具体如图 10 所示。面对面与背靠背安装方式的选择参考上述的三联轴承安装。
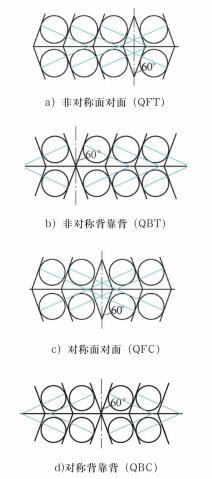
图 10 常见固定端轴承安装形式(四联)
“固定 - 固定” 方式下同样需根据车床切削力的方向确定两侧轴承组配方式,如图 11 所示。图11a 所示丝杠两侧的轴承均为两个朝右一个朝左布置,相比图 11b 的对称布置,可以承受更多的朝左边轴向载荷。图 11b 的对称布置对车床刀具正向移动和反向移动可以提供一致的承载能力。
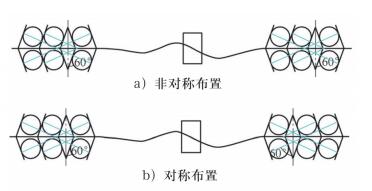
图 11 固定 - 固定方式两侧轴承布置
5. 选型思路
针对车床的应用行业与被加工件的状态可以优化滚珠丝杠副的选型。
5.1 数量原则
在被加工对象量少但对精度要求相对很高的情况下,更推荐使用双螺母预紧方式,可在长生命周期内保持滚珠丝杠副的预紧力,维持较长的精度保持期。
在被加工对象量大且对单位时间内产量提高有强烈诉求的情况下,推荐在满足精度的情况下增大导程,同时可以考虑端块式循环方式,能最大程度地提升返程速度。
5.2 材料原则
被加工件为有色金属如铜、铝时,对应的载荷相对较小,但对精度要求较高,故在丝杠副选型时从低载荷、高精度情况考虑。
被加工件为钢铁等较硬材质时,需判断车床所在的工艺流程位置,一般情况下,粗车与半精车可以选低精度、高载荷的丝杠副,此时切削量大,但对精度要求不高。精车情况则是低载荷、高精度。
5.3 车床结构
出于可以安排更多的刀位考虑,很多先进的数控车床采用斜床身布局。斜床身数控车床的布局可以直接影响 X 方向滚珠丝杠的间隙,重力直接作用于丝杠的轴向,使传动时的反向间隙几乎为零。此时 X 轴向滚珠丝杠副可以选择安装尺寸更小的单螺母。
5.4 选型流程图
滚珠丝杠副的选型过程可以简化为图 12 所示流程图,可以初步判定车床用滚珠丝杠副的直径范围、预紧方式及循环方式,对应到具体的丝杠副大类型号。然后可以参考各丝杠副供应商的样品目录进行精确选型,完成后续的校核计算。具体计算过程此处不再赘述。
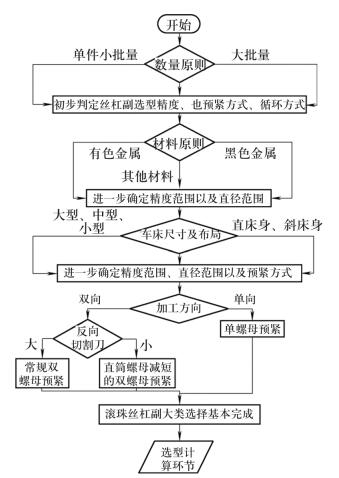
图 12 初步选型流程
6. 结束语
本文从滚珠丝杠副的安装角度,为车床丝杠副的选型思路提供了新的方向。从滚珠螺母的选择、滚珠螺母的安装形式和丝杠在车床上的安装形式等方面分析了常见选择的使用场景。提出了从车床使用场景出发,如加工零部件数量规模、被加工件的材质等角度的车床用丝杠选型思路,这属于丝杠副选型计算的前处理过程,为车床从业者的滚珠丝杠副选型提供了参考。
投稿箱:
如果您有机床行业、企业相关新闻稿件发表,或进行资讯合作,欢迎联系本网编辑部, 邮箱:skjcsc@vip.sina.com
如果您有机床行业、企业相关新闻稿件发表,或进行资讯合作,欢迎联系本网编辑部, 邮箱:skjcsc@vip.sina.com
更多相关信息