浅谈 3D 打印与切削混合制造工艺的原理与应用
2022-4-22 来源: 山东理工大学机械工程学院 作者: 高希坤
1. 引言
3D 打印增材制造成形的最大特点是分层制造,从原理上就使得采用 3D 打印所制作工件的几何尺寸精度和表面质量比着传统减材制造的工件较差。如图 1(a)所示,可以直观地看到 3D打印成型表面微观结构表面的粗糙度在不同的特征上差异较大,如图 1(b)所示,采用激光或电子束 3D 打印成型的工件,由肉眼可清晰观察到 3D 打印工件的表面纹路。
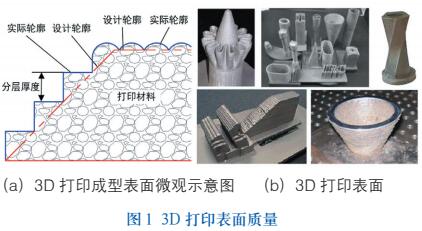
目前,应用 SLM 技术 3D 打印的零件尺寸精度为 20~50μm,表面粗糙度为 5~50μm。因此,由 3D 打印制造的零件,还需要根据具体要求进行整形、切削(磨削)、抛光或喷丸等后续处理。如果仅考虑工件的外形几何尺寸和外表面质量,可以将 3D 打印完毕的工件进行数控切削加工,以获得满足要求的零件。但是,对于同时具有较高精度要求内外几何特征的零件,典型的如随形模具,则以上工艺难以实现。因此,为了同时获得 3D 打印高效制造的能力与减材制造的高精度,有必要研究与开发各种形式的增减材混合
制造技术。
2. 增减材混合制造原理
增减材混合制造的工作原理是将 3D 打印技术与数控切削技术相结合,在同一台机床上实现加法和减法的制造。增减材混合制造一般采取将3D 打印装置安装在数控切削机床上,实现工件的快速 3D 打印,并在同一台机床上进行数控切削加工,工件表面粗糙度可以达到纳米级。增减材混合制造不仅避免了原本在 3D 打印机床与数控切削机床转换时时工件的夹持和取放所带来的定位误差,提高制造精度与生产效率,而且也节省设备的占地面积,降低制造成本。
考虑到数控铣削加工的灵活性,切削机床多采用数控铣削机床,也有采用磨削或其他类型的机床。
根据具体的工件要求,可以采取少层 3D 打印 + 切削、多层 3D 打印 + 切削、3D 打印完毕+ 切削等增减材混合制造的方式。其中,少层或多层 3D 打印 + 切削的方式主要用于制造含有复杂内外型面特征的零件,使得 3D 打印完毕之后难以切削的工件特征得以精密切削,获得高尺寸精度和高表面质量的全工件特征。3D 打印完毕 + 切削等增减材混合制造的方式适合于没有复杂内外型面特征的零件制造,这一方式与 3D 打印完毕之后再进行切削加工类似,但是由于工件不用二次装夹,有效减少定位误差,提高制造效率和制造精度。基于目前的技术,从生产成本上看,采用少层或多层 3D 打印 + 切削的方式,在机床内反复进行 3D 打印造型与切削的复合加工,生产成本最高。采用 3D 打印完毕 + 切削等增减材混合制造的方式,3D 打印造型后在机床内做一次性切削精加工,生产成本适中。不具备增减材混合制造机床条件下,对于精度要求一般的工件,3D 打印造型后,在其他机床上做切削精加工,生产成本最低。应该指出的是,虽然各种制造方式的生产成本差异较大,但是,从制造质量上看,费用较高的制造方式,质量也比较高。
3. 增减材混合制造应用
增减材混合制造的用途非常广,理论上讲,3D 打印制造的应用领域,也就是增减材混合制造的应用领域,只不过根据不同的 3D 打印方式制作,所采用的具体减材制造的工艺和工装会是多种多样的。采用各种不同 3D 打印方式制作的零件,均可以采用增减材混合制造的方式来提高尺寸精度和表面质量。以 DMG-MORI 公司的增减材混合机床制造为例,如图 2 所示,可以用作零件修复、零件加工和零件直接制造。
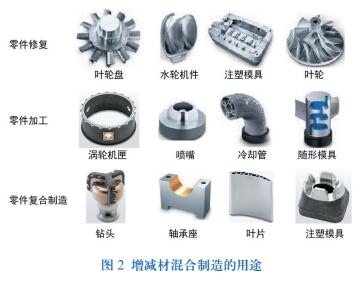
带有随形冷却水道的模具组件制造是增减材混合制造的一个重要应用领域。冷却水道在模具中的形状不是直线型,而是随着注塑制品的外形变化。注塑模具冷却的常用办法是在模具内开设冷却水通道,利用循环流动的冷却水带走模具的热量。传统的模具组件是采用交叉钻孔等工艺技术来制造注塑模具的冷却水路,而随形冷却水路通道是自由弯曲的,能够与注塑零件的几何形状紧密贴合,使得注塑过程中能够更加快速的带走热量,显著缩短冷却时间。带有随形冷却水路的模具组件使得注塑模具的循环时间减少 10%至40%,在制造塑料部件时能够增加 30%~50%的产量,大幅度降低注塑生产的成本,同时,由于采用了随形冷却水道,注塑生产的零件整体质量得以提高,并大幅度减少了翘曲变形。采用传统制造工艺,随形冷却水路难以采用和制作,采用 3D 打印技术,则完全没有技术障碍。
但是,单纯采用 3D 打印技术并不能够保证模具的质量,而且随形流道在 3D 打印完成之后,没有工艺可以采用以有效地进行精密加工,流道的表面质量不可控,尤其是一些细微直径尺度的流道,长时间通冷却水之后会造成流道的堵塞,有可能会提前使得模具报废。而采用增减材混合制造技术,这一问题迎刃而解,可以获得具有同样精度和表面质量的内表面和外表面,完全满足所需设计要求。
船舶用零部件制造是增减材混合制造的另外一个重要应用领域。由于船舶配套零部件批量小,较多的属于非标产品,如螺旋桨、螺旋销、箱式热交换器等,特别适合增减材混合制造。其中,增减材混合制造的船用螺旋桨直径为 1.35m,重量为 400kg,材料为镍铝青铜合金,这种螺旋桨已经通过了船级社认可和批准使用。
根据 3D 打印方式的不同,增减材混合制造的类型有多种,主要材料有热塑性塑料、金属、石膏、陶瓷等,材料类型主要有粉末和线材,所用造型方式有激光、电子束、热熔等。根据减材方式的不同,主要有 3D 打印与车削、铣削、磨削等的增减材混合制造方式。
4. 结语
增减材混合制造技术将 3D 打印技术与数控切削技术有机的集成在一起,从原理上提高了生产效率、降低了生产成本、拓宽了产品原材料的加工范围,并有利于减少原材料消耗和切削液的使用,有利于环境保护,大力推动着 3D 打印技术在多个领域的实用化发展进程。因此,增减材混合制造具有广阔的应用前景,必将得到越来越广泛的应用。
投稿箱:
如果您有机床行业、企业相关新闻稿件发表,或进行资讯合作,欢迎联系本网编辑部, 邮箱:skjcsc@vip.sina.com
如果您有机床行业、企业相关新闻稿件发表,或进行资讯合作,欢迎联系本网编辑部, 邮箱:skjcsc@vip.sina.com
更多相关信息