多品种微机电伺服机构小直径销孔高效加工工艺技术研究
2018-4-13 来源:中北大学 山西省深孔加工工程技术研究中心 作者:张煌,沈兴全,李耀明,翟宁
摘 要: 针对微电机轴与配套齿轮副销孔加工过程中,自动化程度低,定位精度差,成品率低及刀具磨损严重等多重问题。深入分析系统工装特性及产品互换性,优化加工工艺,着重研究产品设计要点。基于深孔加工理论,采用配钻工艺,创新研制精密高效电机轴与配套齿轮副微销孔配打专用装置。通过实验研究,对比分析工艺优化前后加工销孔的位置精度和加工效率,验证优化工艺及装置的明显优势,对实际应用提供良好的指导、借鉴作用。
关键词: 电机轴; 销孔; 配钻; 加工工艺; 优化设计; 定位装夹
在军事和航空航天领域中的设备装置需承受高加速产生的惯性附加载荷 。随着科学技术的迅猛发展,微电子技术、电机制造工艺水平的不断提高,结构紧凑、性能稳定、效率高的微型伺服电机在航空、航天领域得到了越来越广泛的应用。
微型伺服电机轴与微小齿轮直接装配连接,其作为直接驱动部件,在航天某系统中承担着关键性任务。所以,电机轴与配套齿轮副销孔的精准配合及可靠性保障显得至关重要,现代加工技术的发展,使得上述要求逐一变为可能。销孔装配是机械产品常见的装配形式,且在特定的性能要求下对销孔装配质量要求较高。其不仅影响到产品的位置精度、装配精度,而且影响到相关装配件的稳定性、安全性及寿命等。特别对于精密齿轮副的定位,如若销孔加工误差大,极易引起齿轮装配不当,或局部应力集中,甚至齿轮不啮合,造成动力传输失效; 还会引起齿轮副振动明显,系统稳定性急剧下降。郝长中针对活塞异形销孔加工,利用磁致伸缩材料特性和弹簧板弹性产生镗刀的径向微位移达到设计要求。杨博通过调整机床精度、加工参数实现高精度小直径定位销孔的加工.卢娜利用有限元的方法进行了机车电机轴与小齿轮轴配合的模拟分析。张凯基于压电陶瓷提出了一种新型活塞异形销孔数控加工方法。史涛、边境等人采用卧式加工中心,提出了一种新型的齿圈销孔加工方法。
大多数研究人员对销孔进行了多方位的研究,但是对于多工件配钻 方法的研究还极其稀少,其适用工艺还需有针对性研究,将各向功能结构的产品集成于一体,其装配形式、功能实现便需要新工艺、新技术的保障。本文针对微伺服电机、锥齿轮、轴承集成于一体的结构,完成定位销孔的加工,深入研究销孔配钻加工工艺技术,通过不同工艺的实验对比,优化加工工艺,创新设计适应多品种、大批量产品的互换性、精密加工要求的装置。
1 、工件系统特性及工艺优化分析
1. 1 工件系统特性
如图 1 所示,系统由微伺服电机 1、轴承 5、锥齿轮 6 集成于一体,系统中具有端面凸台 2 及端面间隙 3,依靠定位销 4来保证齿轮的高度,并实现动力传输。
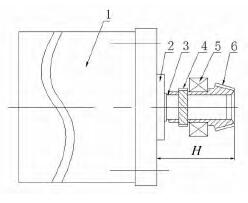
图 1 微机电伺服机构装配系统结构
( 1) 因系统装配集约性,并且微定位销孔靠近电机端面,再加之轴承的干涉,阻碍了普通装夹装置、定位辅助装置等的应用,导致普通刀具无法满足加工要求,必须使用加长硬质合金刀具,这无疑使得刀具悬伸太长,刚度系统差。
( 2) 微伺服电机系统固有特性的限制。电机轴不宜承受轴向力,且锥齿轮尾端面与电机端面凸出台有间隙。
( 3) 针对不同产品定位销孔的尺寸要求不同,微伺服电机尺寸、外伸轴长、各功能部件的装配要求也各不相同,这样使得产品互换性要求较高。
1. 2 传统工艺分析
传统的加工工艺,首先在锥齿轮上根据技术要求测量尺寸,并钻孔; 其次,将锥齿轮、轴承与电机装配,用胶粘接。等待强力胶起作用后,人工手动利用小型钻床,逐个工件完成销孔制作; 最终装配销钉,完成系统集成。不难看出其加工效率、精度、可靠性保障等与精密动力系统的严格要求,截然背道而驰。
( 1) 自动化程度低,定位精度差,需多次重复测量因普通装夹、定位系统受到限制,电机的装夹仅靠人工及测量工具装夹于台虎钳。并需多次重复测量,累积误差大大增加。由于寻找定位的试钻凹陷点的存在,钻头刚性较差,当高速钻床主轴转动,使得再次对刀定位电机径向轴线时,极易重复定位到凹陷点处,准确定位更加不易。再加之采用的粘接配钻法,微小零件装配接触面积小,可用于涂敷粘胶的表面积相应的也小,施胶量少,连接强度必然受到影响。
(2) 钻头易断,增加了经济成本电机轴采用高硬度材料,为光滑圆柱形,使得刀具与电机轴径向轴线难以严格同轴,略微的偏斜都会使得电机轴转动,再加之系统刚度系统差,导致刀具极易折断,更换钻头后又需重复之前工作。
( 3) 效率不高,还需丰富经验多次不断重复的测量,找正定位及刀具的易折断,完成一次钻孔需要耗费相当多的时间、精力,经济成本太高,效率太低。人工钻孔还需要有足够丰富经验的操作者才可顺利完成。
另外,由于小齿轮的最终装配高度精度差异大,即一致性、互换性差,导致整机性能也存在一定的差异。
1. 3 工艺优化
针对多品种、多干涉小直径工艺销孔的研制,深入分析传统工艺技术的缺陷,基于深孔加工系统理论,设计研究专用多工位工件装夹系统、钻模辅助支撑装置、气动定位机构等,采用配钻工艺对集成于一体的微伺服电机系统完成销孔加工。
以配钻工艺一次性完成销孔的制作代替传统工艺中的测、粘、固等工序; 以专用钻模弥补传统工艺中刚度系统差的缺点; 以送料机构、定位机构、及自动夹紧机构代替原有人工装夹。既减少了加工工艺,又提高了销孔的位置精度等级,增加了产品的互换性,实现了从送料,定位,夹紧,加钻孔为一条龙的自动化连续运转,因而有效增强加工精密度,提高生产效率。
2 、优化设计
2. 1 设计理论基础
优化设计中主要考虑工件的定位装夹、配钻对工件装夹稳定性的影响及系统本身固有特性( 电机轴的转动) 的影响,着重研究麻花钻的影响效果。而 v型铁具有天然的自定心性能,主要用来安放轴、套筒、圆盘等圆形工件,以便定位中心线。微电机的外形结构与此不谋而合,故应用 V 型铁为基准,方便确保工件的精确定位。

图 2 麻花钻切削受力情况
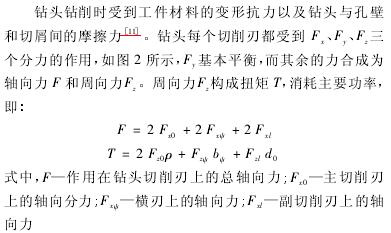
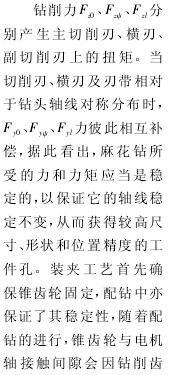
轮后产生的切屑而起到粘固的功用,同时,在设计中确保钻模中心与电机轴径向中心线严格对齐,以此保证钻削过程中电机轴的稳定。
2. 2 总体方案设计
精密高效电机轴与配套齿轮副微销孔配打专用装置总体方案包括两部分: 机械系统方案设计和控制系统设计。
其中,专用装置的机械系统由六工位回转台、钻削动力系统、工件装夹系统、气动装置四个主要部分组成。如图 3 所示的电机轴与配套齿轮副销孔配打专用装置,包括底座 1,其上设有回转工作台 3、薄型气缸 5、钻削动力系统( 包括竖向同轴的高精度台钻 8 和可换式钻模 10) 和限位组件( 包括钻模支架 14 和其上水平安装的限位块 13) ,回转工作台 3 下方设有数控分度盘 2,回转工作台 3 上均布设有若干安装电机 11 的 V 型铁组件 7,薄型气缸 5 通过气缸支架4 固定于底座 1 上。
利用该装置钻孔时,首先将要钻孔的齿轮和 U 型垫 12装配到需要钻孔的电机轴上,然后将装配好的齿轮和电机安置在回转工作台 3 的 V 型铁组件 7 上,利用程序控制回转盘旋转,将待钻孔工件输送到指定的位置,由薄型气缸 5 自动输出作用力推动推杆 6,并组合 U 型垫 12、限位块 13
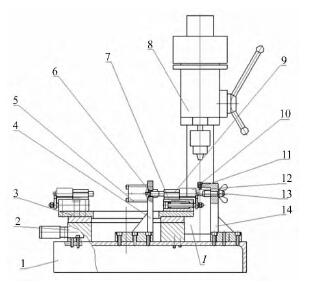
图 3 系统工作原理示意图
实现轴向夹紧,精确定位,再通过可换式钻模 10 精确地实现引导、钻孔。完成钻孔后,推杆 6 后撤,弹簧 71 收缩,复位板 74 弹簧恢复原状( 恢复至初始位置,即沿图 3 中向左方向复位) ,令装配好的电机和齿轮归位,自动回转盘使下一个需钻孔的电机和齿轮进入到工作位置。
2. 3 工件装夹系统的设计
工件装夹系统在设备中起到至关重要的作用,它不仅要实现工件的快捷、简便安装及自动化控制,而且要确保锥齿轮端面与电机安装面的高度尺寸。同时,还需要实现不同尺寸电机与齿轮要求的装夹功能,确保钻头中心与电机轴中心在同一垂直线上,实现电机与齿轮的自动装夹。这样就需要在设计中增加辅助装置,从而满足其多样化功能。为能最方便将配打电机既不做过多调整来满足不同规格电机的安装,同时使用同一台设备。有两种方案:
( 1) 方案一: 两种不同规格电机均以 V 型铁做为定位原件,然而其外形尺寸相差过大,必然导致中心高度变动较大,那么需要同时将气缸支架、钻模支架更换或增加调节中心高的装置; 并且要调节钻床主轴高度( 钻床主轴行程所限) 。
( 2) 方案二: 以 V 型铁做为定位原件,以大型号电机中心高为基准,增加辅助装置 V 型垫块,使小型号电机中心与其一致。只需更换钻套、限位块和钻头即可比较方便的解决两种不同型号电机在同一钻床的配钻工作。
综合分析上述两种方案,方案二不至于频繁的更换钻模支架,且方案二方便、快捷,明显优于方案一,因此,结构设计中采用方案二。
2. 3. 1 V 型铁组件的设计
V 型 铁 组 件如图 4、5 所示,包括 V 型 铁 73 以及水平安装于 V型铁 73 下段内的限位 杆 72,限位杆72上套装有弹簧 71,限位杆 72的悬出端安装有复位 板 74,复 位板 74 通 过 螺 母75 锁紧。复位板74 上端作用于电机外壳端面,U 型垫 12 用以保证齿轮的轴向定位。
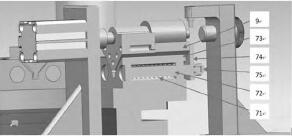
图 4 小型电机装夹图
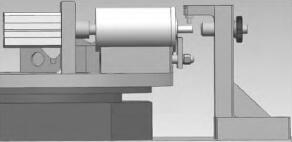
图 5 大型电机装夹图
为实现不同尺寸电机与齿轮要求的装夹功能,增加产品互换性,设计中采用方案二,以大型电机为基准,以 V 型铁 7为定位基座,保障其自动定位功能; 小型电机则通过增加 V型垫块 9 来增加中心高度,从而在不更换气缸支架 4、钻模支架 14 的基础上,使不同尺寸电机的中心高度保持一致。由于齿轮销孔位置和齿轮端面对电机端面也有要求的差别,不同型号电机的精确定位,只需更换相对应的钻模 10、U 型垫12、限位块 13 及刀具,并辅助相应的 V 型垫块 9 即可。带有复位功能的 V 型铁组件,避免了由于操作者的误安装,回转台转动后,导致电机与钻模支架的干涉碰撞。
2 . 3. 2 多工位回转台的设计
多工位回转台用于将电机齿轮组装后自动输送到指定打孔位置。其底座采用数控高精度伺服控制 系 统 分 度盘,回 转 精 度 达到 0. 01°,分度盘上量 60 度均均布装有 V 型铁。使得在回转台上一次可装夹六个工件,当前一个工件加工完毕后,按下切换按钮,自动切换到下一个工位并自动夹紧工件,可以直接进行下一个工件的加工,节省频繁更换工件的时间。多工位回转台如图 6 所示。

图 6 多工位回转台结构示意图
2. 3. 3 U 型垫的设计
因电机与齿轮装配完成后,在电机轴与电机端面结合处有微小凸台,且齿轮端面与电机端面有间隙高度。此间隙高度决定了齿轮的装配位置及钻孔位置,为此设计专用垫片来保障尺寸要求及定位要求。气缸、U 型垫、齿轮、限位块组成的轴向夹紧,增加了齿轮前端面与限位块的摩擦,保证电机前端因钻削进给力的作用而不至于倾斜,同时,使得锥齿轮得到可靠固定,避免其绕电机轴的转动。
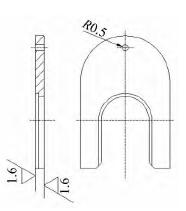
图 7 U 型垫结构示意图
3 、实验分析
实验针对电机外形直径为 Φ50 和 Φ29 的两种型号电机系统,分别利用传统工艺与优化工艺进行销孔加工,对比分析两种加工工艺后的销孔位置精度和加工效率。实验条件及具体参数如表 1。
表 1 实验参数
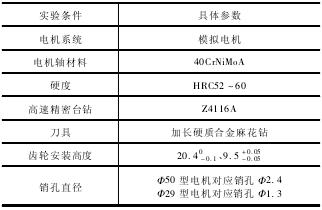
图 8( a) 为分别利用传统工艺及优化后工艺对 Φ50 型电机进行配钻销孔 Φ2. 4 所得七组实验结果对比图,高度值 H为齿轮端面距离电机安装面的距离。图 8( b) 为 Φ29
型电机进行配钻销孔 Φ1. 3 所得七组实验结果对比图。

图 8
从图 8( a) 、( b) 中均可看出,传统工艺与优化后工艺存在明显差距,优化后工艺所测高度值成正态分布于技术要求均值附近波动,微小的波动源于机床系统的固有振动及麻花钻本身特性所决定。而传统工艺误差过大,成品率低。对比分析图 8( a) 和( b) 可知,传统工艺完成钻孔后所得结果无规律,并且随着销孔直径的减小,偏差越大,这主要是由于刀具刚度系统差、工件定位不可靠所导致。
4 、结 论
( 1) 由于刀具刚度系统差、工件定位不可靠,导致扩孔现象、位置精度差、偏差无规律等恶劣现象的发生。
( 2) 为实现在同一台设备中满足多品种工件不同要求的加工,增加产品互换性,针对圆柱形工件,利用 V 型铁来对其进行装夹定位,以大型工件为基底,通过辅助 V 型垫块,即便捷又精准。
( 3) 考虑到工件的多样性、多干涉性,增加钻模辅助支撑,极大地增强了刀具系统刚度; 以多工位回转台并集成工件自动恢复原始状态功能,实现了工件的高效、精准装夹及自动化控制。
( 4) 通过对比分析传统工艺及优化后的实验效果,验证了优化工艺的高精度、自动化、简便快捷、多适应性的优点,对实践应用提供良好的指导、借鉴作用。
投稿箱:
如果您有机床行业、企业相关新闻稿件发表,或进行资讯合作,欢迎联系本网编辑部, 邮箱:skjcsc@vip.sina.com
如果您有机床行业、企业相关新闻稿件发表,或进行资讯合作,欢迎联系本网编辑部, 邮箱:skjcsc@vip.sina.com