小径深孔钻削钻头位置同步检测系统
2018-2-9 来源: 中北大学 机械与动力工程学院 作者:李川怀 王 彪 杨福合 董文心
摘 要: 针对加工小径深孔时检测装置无法放入深孔内部进行钻头位置检测和检测结果受工件表面形状影响较大的实际问题,提出了基于超声波检测技术和激光位移传感器检测技术的同步位移检测方法,建立了以PLC、上位工控机和同步检测装置组成的检测系统。设计了同步检测装置和检测系统,并对检测系统进行了分析。从而为提高小径深孔加工质量供了一种新检测技术,该系统能满足检测要求,对深孔钻头位置检测具有一定的前景。
关键词: 深孔; 钻头位置; 超声; 激光位移传感器; 检测
深孔通常是指长度大于直径 5 倍以上的孔,深孔加工在切削领域占有重要的位置,尤其是小直径深孔的加工,钻头在半封闭或封闭状态下进行加工,排屑困难,切削热不易扩散,刀杆细长且强度低,钻头易走偏。
检测装置不能进入深孔内部进行实时检测,因此,无法观察钻头的实际位置,导致加工过程中出现大量不合格产品或钻头折断。另外,由于检测装置受到检测工件外形的影响,检测结果误差较大,不能准确反映钻头的位置,在加工小径深孔过程中,实时检测钻头的走偏情况,采取合理措施对钻头进行纠偏具有重要意义。
本文基于超声波的工作原理和激光位移传感器测量技术 ,设计了一种以超声波检测和激光检测为基础的小径深孔加工钻头位置检测系统。系统通过超声波测量孔的壁厚,用激光位移传感器对测量误差进行补偿,及时反馈钻头在测量方向的实际位置,为小径深孔加工过程中刀具纠偏提供指导,提高小径深孔加工的质量.
1 、超声波和激光位移传感器的检测原理
1. 1 超声波检测的工作原理
超声波是一种频率高于两万赫兹的声波,传导方向性好,无法被人耳接收。当超声波频率达到兆赫兹以上时,在金属和液体中的传播性很好,但在空气中很难传播,因而可以用超声波来检测金属材料物体。其原理如图 1 所示,若已知超声波在被测金属材料中的传播速度,当超声波探头发出的超声波脉冲通过被测物体到达金属材料与空气的分界面时,脉冲波被反射回探测头,通过测定超声波发射时间 T 和接收到反射超声波的时间 B 计算出超声波在物体中传播的时间,进一步计算出物体的厚度。
在小径深孔加工过程中,采用脉冲式超声波测厚仪,其通过超声波的反射原理来测量深孔壁的厚度,间接测量钻头在此方向的位置。通过超声波测量物体厚度的原理,超声波探头( 换能器) 发出的超声波在深孔工件内部传播时,当遇到孔壁,反射的超声波波幅会增大,其中一部分反射回探头,另一部分沿轴向在零件内反复折射而消耗掉。
假设超声波在被测零件中的传播速度为 C,超声波由外表面反射回探头用的时间是 T1,由内表面反射回探头用的时间为 T2,通过时间延迟,可计算出超声波在孔壁间传播的时间,那么工件在所 测 方 向 的 壁 厚 L =C( T2- T1) /2,对数据进行分析处理即可反映钻头在此方向上的位置。
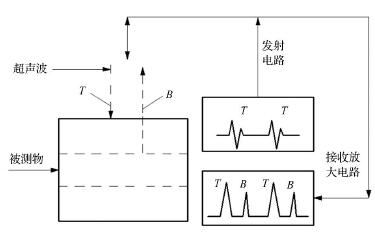
图 1 超声波检测原理图
1. 2 激光位传感器的工作原理
激光位传感器在机械工程的测量领域得到广泛的应用,主要通过激光 三 角 法 对 被检测的形状、位移、厚度等进行测 量。 激光位移传感器检测原理如图 2所示,激光发射器发出的激光线经过会聚透镜,投射到被测物体表面,会聚透镜的光轴与接收透镜的光轴交于参考面上的 O 点,并将 O 点经接收透镜成像于探测器的 O'点,当被测物体高度发生变化时( 以表面下移为例) ,导致光斑将沿入射光轴移动,像点将在探测器敏感面上发生位移。
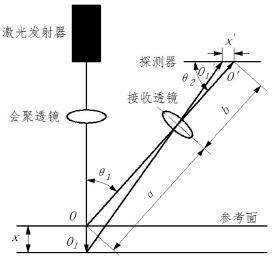
图 2 激光位移传感器检测原理图
若光斑在探测器敏感面上的位移为x',利用相似三角形各边之间的比例关系,可以求出被测表面的位移:

式中: x 为被测表面到参考表面的位移; x'为光斑在探测器敏感面上的位移; α 为投影光轴和成像光轴的交点 O 到接收透镜中心的距离; b 为接收透镜中心到探测器敏感面点 O'的距离; θ1为成像光轴与参考面法线的夹角; θ2为成像光轴与探测器敏感面的夹角。若被测面位于参考面的上方,则式( 1)分母取“+ ”。由式( 1) 可知,只要测出光斑在探测器敏感面上的位移,就可以计算出被测面的位移。
2 、钻头位置检测系统的组成和原理
加工小径深孔时,钻头位置检测系统采用超声波测量物体厚度技术实现了小径深孔加工钻头位置的无损检测,利用超声波探头发射、接收超声波,用激光位移传感器进行测量误差补偿。小径深孔加工钻头位置检测系统总体布局,如图3 所示,主要由数控深孔钻床床身、超声波发射接收探头、同步位移装置、激光位移传感器、上位机、PLC 等组成。
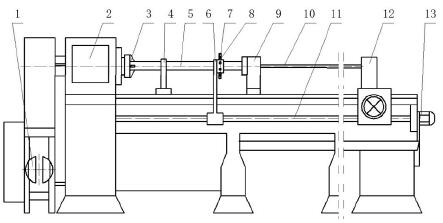
1. 主轴电机 2. 触摸屏 3. 三抓卡盘 4. 中心架 5. 工件6. 同步位移装置 7. 激光位移传感器 8. 探头 9. 喷雾装置10. 钻杆 11. 丝杠 12. 负压排屑装置
13. 进给电机
图 3 钻头位置检测总体结构示意图
钻头位置检测系统以数控深孔钻床为基础平台,无需停止机床的加工过程,即可实现同步检测,其检测原理如图 4所示,在机床导轨上安装同步位移装置,将超声波探头和激光位移传感器固定在同步位移装置的相应位置。根据工件的外形尺寸,在探头自由伸缩状态下,调整探头到 H 高度,以钻头理论中心为圆心、探头高度调整值 H 为半径画圆,得到深孔的虚拟参考外壁,通过钻头半径 R 和探头高度调整值 H计算出虚拟参考孔壁的厚度:
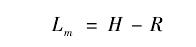
加工过程中,用带动钻头做进给运动的电机驱动同步位移装置,检测装置和钻头作同步运动,在图示位置对探头所在方向上的钻头位置进行检测,用超声波探头和激光位移传感器分别测量当前位置实际孔壁厚 L1和探头的位移量 S1,由L1、S1计算出实际深孔被检测母线到虚拟参考外壁的厚度

由式( 2) 和式( 3) 可计算出深孔在被检测位置偏离理论位置的偏移量( 即钻头位置的偏移量) :

若 S2> 0,则表明钻头向靠近探头的方向偏移; 若 S2<0,则表明钻头向背离探头的方向偏移。用上述方法测量钻头的偏移量,避免了因工件外形的直线度、圆度、表面缺陷等产生的测量误差。
在加工小径深孔过程中,为了更精确的检测钻头的实际位置,在 360°圆周范围内,每隔 45°作为一个检测方向,采用单个点测量的方法,沿进给方向每间隔 10 mm,8 个探头同时对深孔的 8 个方向的壁厚进行测量,根据测量结果计算出孔在各个方向上的偏移量,对偏移量进一步处理,即检测出钻头在 8 个检测方向上各自母线的位置,反映出钻头的实际位置。
3 、钻头位置检测装置结构
小径深孔加工过程中,同步位移装置带动钻头位置检测装置与钻头进行同步轴向移动,因此要求钻头位置检测装置适应工件外形的直线度和圆度的变化,能自动进行探头位置调整,并对超声波测量结果的误差进行补偿,其结构如图 5所示,在结构中采用复位弹簧自动调整探头的位置,即探头可根据偏差沿径向进行自由伸缩,为适应不同尺寸的工件,可对刻度导套的位置进行调整,迅速地将探头调到最佳位置,探头保护罩上的小孔可向探头和工件之间注入传声耦合剂( 甘油) ,使探头和被测工件间没有空气间隙,方便超声波传播。
在探头尾部用导杆连接,既可以对探头进行导向,又方便激光位移传感器进行探头径向位移测量,对工件外形的直线度和圆度产生的测量误差进行补偿。为减小摩擦力,尽量减小磨损,将探头保护罩前端接触部位设计成滚珠接触。
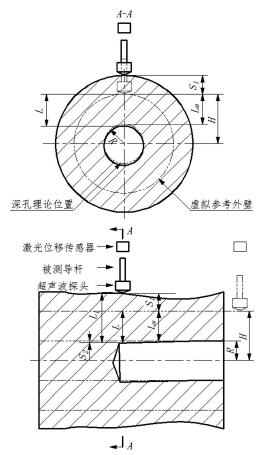
图 4 钻头位置检测原理图
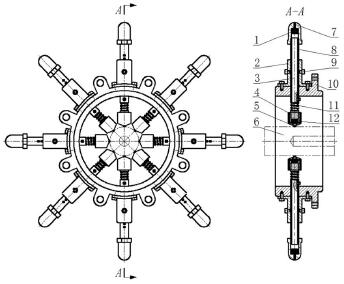
1. 激光位移传感器 2. 刻度导套座 3. 导杆 4. 探头保护罩5. 接触滚珠 6. 被测工件 7. 传感器固定座 8. 刻度导套 9.球头螺钉 10. 支座 11. 复位弹簧
12. 超声波探头
图 5 钻头位置检测装置结构图
4 、钻头位置检测控制系统结构
钻头位置检测控制系统结构,如图 6 所示,主要由 PLC、工控机、超声波测厚仪、数据采集卡、超声波接收电路、激光位移传感器等组成。超声波测厚仪利用压电效应制成的发射、接收探头进行孔壁厚度测量,超声波探头将发射、接收超声波产生的电脉冲经发射接收电路整形后提供给数据采集卡。同时,激光位移传感器将探头在测量方向上的位移转化成电信号,由数据采集卡接收输送给上位机。
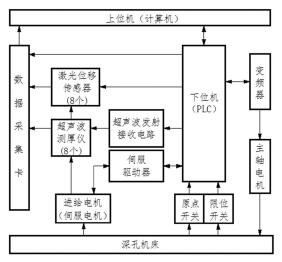
图 6 检测控制系统结构示意图
PLC 作为下位机主要用于触发超声波发射接收电路和A / D 数据采集卡工作,进行与上位机的数据通讯以实现检测控制。工控机作为上位机,处理采集卡接收的探头和激光位移传感器返回的电信号,转化成

所需要的参数,式中: S1n为第 n 个方向上探头的位移量;Un0、Un1分别为第 n 个激光位移传感器起始电压值和位移变化后电压值; S、U 分别为激光位移传感器的量程和最大量程时对应的电压值; L1n为第 n 个方向上探头测量的孔壁厚度;C 为超声波在被测工件中的传播速度; T1n、T2n分别为第 n 个探头发出的超声波经孔的内、外壁反射回探头所用的时间。
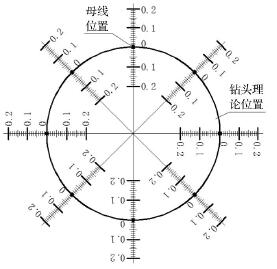
图 7 钻头位置的监控画面示意图
为了使钻头 8 个被测量方向上的母线,在法向平面上以亮点的形式呈现在二维坐标监控画面内,如图 7 所示,将式( 2) 、式( 3) 、式( 4) 、式( 5) 、式( 6) 整理后,得出 8 条母线在二维坐标监控画面内的坐标值:
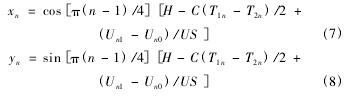
式中: xn、yn为第 n 个方向上钻头母线在法向平面上位置的坐标值; H 为探头自由伸缩状态下,应调整的 H 高度值( 根据工件外形确定) 。由式( 7) 、式( 8) 可以看出,只要测出 T1n、T2n、Un0、Un1的值,就可以求出母线在二维坐标监控画面内的坐标值。
5 结 论
小径深孔钻削钻头位置检测系统借助超声波检测技术和激光位移传感器技术,通过现代电子技术和数控技术应用到深孔加工过程中,与传统检测方法相比,具有分辨率高、响应速度快、信号处理简单、测量精度高,避免了因被测物体外形影响产生的测量误差,可以实时检测钻头的位置情况,解决了小深孔加工过程中钻头位置难测量和测量精度低的问题,降低了废品率,有效提高工件小深孔的加工精度,为小深孔加工钻头位置检测提供了新技术,有良好的应用和推广价值。
投稿箱:
如果您有机床行业、企业相关新闻稿件发表,或进行资讯合作,欢迎联系本网编辑部, 邮箱:skjcsc@vip.sina.com
如果您有机床行业、企业相关新闻稿件发表,或进行资讯合作,欢迎联系本网编辑部, 邮箱:skjcsc@vip.sina.com