TA10 钛合金的深孔钻削技术研究
2018-4-20 来源:西安石油大学 机械工程学院 作者:赵 超
摘要: 本文通过实验分析了对 TA10 材料进行深孔加工的难点和解决方法,并进行了加工试验,优化了刀具角度,分析了加工刀具的磨损机理。取得了较好的加工效果,对 α 型钛合金的深孔钻削有一定的参考意义。
关键词: TA10 钛合金; 深孔钻削; 刀具设计; 磨损机理
TA10( Ti - 0. 3Mo - 0. 8Ni) 钛合金属于近 α 钛合金的一种,一般情况下以锻造、挤压、轧制和拉拔的钛合金圆棒、矩形棒形态。是 20 世纪 70 年代中期美国研究开发的 Ti - 12合金,具有很强的抗缝隙腐蚀能力。
在 300℃ 时抗拉强度是工业纯钛的将近两倍,抗还原性介质腐蚀能力强,在 150 ~200℃ 的氯化物中能够不发生腐蚀现象。并且 TA10 材料不含稀有金属,加工性能相对较好。在一些纯钛可能出现缝隙腐蚀的环境中得到广泛应用。TA10 钛合金工艺性能优良,可以在 850 ~ 950℃ 的范围内进行锻轧,在尽可能低的温度下进行热加工,可使表面污染减至最低,为了防止材料吸氢产生氢脆现象,需要在氧化环境中进行加热。其具有优良的可塑性和弯曲性能。在250℃ 环境中成型可以减小回弹。通常采用氩气保护钨极电弧焊,在焊接温度达到 430℃ 以上为避免 C、N、H、O 的污染需要特殊保护。TA10 材料具有以下特点:(1) 有较高的设计应力;(2) 在氧化性介质中具有等于或超越纯钛的耐腐蚀性能;(3) 在还原性介质中耐蚀性优于纯钛;( 4) 在高温氧化物中具有较好的抵抗缝隙腐蚀的能力;( 5) 成本较低。因此 TA10 材料作为热交换器、管式反应器、蛇形管、结晶器等在化工、轻工、核工业、环境保护等领域发展迅速。其机械性能与其他材料对比特性比较明显。

表 1 TA10 与 TA2 纯钛和 45#钢的机械性能对比
从表1 中可以看出 TA10 钛合金具有优良的机械性能,其强度在高温区域变化幅度较小,其密度只有 45#钢的一半,强度较纯钛类材料高,在硝酸蒸汽中耐腐蚀性远优于纯钛类材料。其弹性模量值较小,变形系数小于1,导致钛合金材料在进行加工时已加工表面回弹严重,钻削时会产生长薄卷曲型切屑,排屑困难,并且钛合金化学活性大,在加工表面容易形成硬化层,导致加工表面硬度和脆性提高,粘刀现象严重。其热传导系数只有 45#钢的一半左右,在进行钻削时散热困难,切削热过大,容易引起刀具磨损或者刀具失效。尤其在进行深孔加工这种特殊的加工方式时,对刀具的磨损严重,加工质量、加工效率无法保证。针对 TA10 材料的难加工性,本文从刀具角度出发进行了实验分析。
1、试验设备与工件
加工系统: 对 TA10 的深孔钻削试验采用 BTA 深孔钻削系统进行钻削试验,系统机床为 CW6163D 深孔加工机床; 钻头使用 φ54 mm 五齿深孔钻钻头,如图 1; 刀片材料为 YG8,刀具角度如图 2。该深孔钻系统是深孔加工常用的系统,加工范围广,加工质量较高。
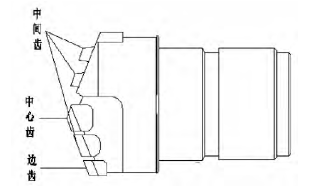
图 1 钻头结构示意图
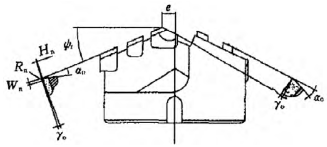
图 2 钻头角度示意图
扫描电子显微镜 JSM - 6390A: 扫面电子显微镜是一种利用电子束扫描样品表面从而获得样品信息的电子显微镜。
它能产生样品表面的高分辨率图像,且图像呈三维,扫描电子显微镜能被用来鉴定样品的表面结构。它由三大部分组成: 真空系统,电子束系统以及成像系统。本文主要利用其进行两方面试验,一是对刀片表面形貌进行观测,二是对刀具表面进行能谱分析通过成分残留来分析刀具的磨损机理。手持式粗糙度仪: 用于测量多种机加工零件的表面粗糙度,根据选定的测量条件计算相应的参数,在液晶显示器上清晰地显示全部测量结果及图形。试验工件为近 α 类钛合金 TA10,为 Φ290 mm × 2700 mm的钛棒。
2 、试验方案
本实验对 TA10 棒料进行钻削,钻削采用 54 mm 直径的深孔钻钻通孔,通过改变钻头前角、后角进行钻削,采用单因素变量法收集数据,观察加工过程中出现的振动情况,利用粗糙度仪测量工件的内孔壁粗糙度,并且通过电子显微镜观察刀具的磨损状况来取得最佳的工艺参数,通过研究钻头的磨损、残留成分情况分析刀具磨损原因得到 TA10 材料进行深孔钻削时的磨损机理。具体加工参数:
(1)加工系统: 基于 CW6163D 深孔加工机床的 BTA 深孔加工系统;
(2) 加工刀具: φ54 五齿型错齿深孔钻钻头,刀片材料YG8 硬质合金;
(3) 刀具角度: 前角 3°、7°,后角 8°、12°,余偏角 18°,钻尖偏心量 4 mm;
(4) 工件材料: Φ290 mm × 2700 mm 的 TA10 钛棒;
(5) 切削液: 乳化液;
(6) 运动方式: 刀具进给,工件旋转;
(7) 切削参数: 钻孔深度 2700 mm,孔直径 φ55 mm,刀具转速 145 r/min,进给量 0.12 mm/r。
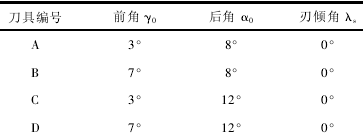
表2 试验刀具角度
3 、实验结果
实验得到的实验数据见表3。
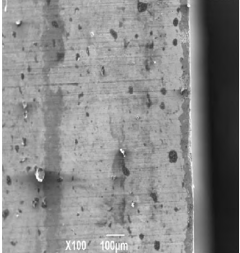
图3 前刀面磨损现象
综合考虑相关加工情况,可以得知,由于材料的塑性变形能力差,刀具前角取小值 3°时,相比于前角取 7°切屑与前刀面接触长度增加,前刀面的磨损相对来讲有所增加,刀具耐用度有所下降; 但由于前刀面所受应力集中现象有所减缓,刀具的切削温度和受力强度降低。同时对比发现,由于钛合金材料在深孔钻削时由于变形系数小,弹性模量小,在加工过程中材料回弹现象严重,导致刀具后刀面取小角度时与工件摩擦严重造成切削热急剧上升,引发系统异响和振动,刀具的磨损现象比较严重,甚至出现打刀、崩刃等现象,因此刀具后角需要增大,选取 12°为佳。另外通过对比发现,在切削钛合金时,刀具后角的作用相对于前角来讲影响比较显著,因此增大后角可以在保证刀具强度的前提下更有效的提高刀具耐用度。因此选用前角 3°,后角 12° 加工状态良好。其道具磨损电镜显微结果见图 3 ~ 图 4。可见在对 TA10 材料进行深孔钻削时,由于材料的回弹现象,刀具的后刀面磨损程度远远比前刀面严重,利用扫面电子显微镜对后刀面的深色和浅色分区进行取点能谱分析。
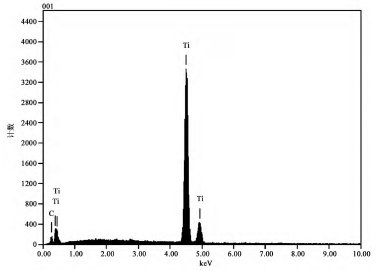
图5 深色区能谱图
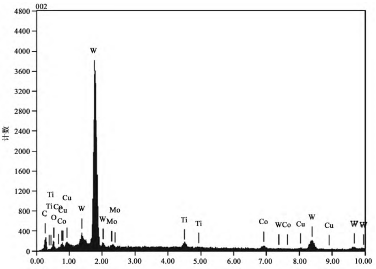
图6 浅色区能谱图
可以发现在贴近刀刃的深色区域富集了大量的 Ti 元素,而在距离刀刃较远的浅色区域,为以 W、Co 等刀具材料为主,Ti 元素只有极少量,说明在加工过程中工件材料在高温高压下出现了明显的粘结现象,综合研究发现,在对 TA10进行深孔加工时由于切削力和切削温度比较高,工件材料的硬度不大,亲和性强,因此硬质合金刀具的磨损主要以粘结磨损为主。
本次试验利用 TR200 手持式粗糙度仪对加工孔的粗糙度进行测量分析,由于孔深较大,因此采用工件末端出钻口粗糙度采样进行对比分析。
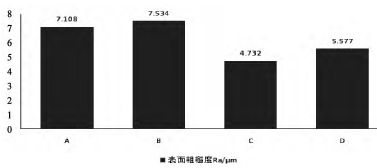
图7 不同刀具角度下的内孔表面粗糙度
由图 7 能够发现,在保证刀具强度的前提下,当刀具的前角和后角越大时,刀具越锋利,能够穿过材料的加工硬化层进行切削,从而加工孔的表面质量比较高。针对 TA10 钛合金的硬度相对较低的特点,在加工时选用大的刀具角度有利于切削的顺利进行。并且可以看出 C 型角度的深孔钻头加工质量也相对较好。
4、结论
本文通过对 TA10 钛合金的物理性能和切削加工性研究分析,并与纯钛 TA2 和 45 号钢进行对比,结合深孔加工的特点对 TA10 材料进行深孔钻削试验。针对 TA10 材料的切削加工特点,选用了Φ290 mm × 2700 mm 的钛棒进行深孔加工试验,通过不同角度钻头的试验对比,得出了以下几点结论:
(1) TA10 具有优越的塑性和相对较好的高低温强度,并且比强度高,耐腐蚀性强。其切削加工性和纯钛类似。在对其进行加工时也有很多不利因素,加工硬化严重、刀具磨损快等降低了其的应用性。在切削时,由于工件材料的弹性模量低,变形系数小的特点,已加工面回弹现象严重,对刀具后刀面产生剧烈磨损; 同时切屑与前刀面接触时间短,导致前刀面单位面积切削力大、切削温度高; 另外钛元素的化学活性大,容易产生加工硬化层,同时与刀具产生粘附现象。这一系列的加工特点加速了刀具的磨损,尤其在深孔加工时,加工环境更加恶劣,加工效率和效果均不理想。
(2) 在对 TA10 材料进行深孔加工时,根据加工材料的尺寸和特点,选用五齿型错齿内排屑深孔钻进行加工,刀片材料选用 YG8 硬质合金比较合理,其具有较高的强度和硬度,并且不容易与工件发生亲和(3) 根据钻削过程中的振动以及刀具的磨损情况,在对Φ290 mm × 2700 mm 的 TA10 钛棒时,刀具角度取前角 3°,后角 12°时刀具耐用度较好,加工效果较好。(4) 加工 TA10 材料时,刀具后刀面的磨损相对于前刀面严重,后刀面的磨损情况决定了刀具的耐用度,因此刀具后角比其他角度影响明显。刀具的磨损形式以粘接磨损为主。
投稿箱:
如果您有机床行业、企业相关新闻稿件发表,或进行资讯合作,欢迎联系本网编辑部, 邮箱:skjcsc@vip.sina.com
如果您有机床行业、企业相关新闻稿件发表,或进行资讯合作,欢迎联系本网编辑部, 邮箱:skjcsc@vip.sina.com