如何在数控车床上车削多线蜗杆齿形
2018-4-28 来源: 湖南省湘西民族职业技术学院 作者: 方媛州
在车削加工培训实践中,车削蜗杆,特别是车削大模数、多线蜗杆,其主要难点在于齿形切削面积大、切削抗力大;另外,其多次周而复始、紧张单调的操作,使得劳动强度增大,并容易出现始料未及的问题,因此车削多线蜗杆往往令人望而生畏。在数控车床上车削多线大模数蜗杆时,如果我们采用普通车床的车削加工方法,不能充分利用数控机床的特点。为此,我们收集、总结蜗杆齿形车削刀具方面的经验,尝试利用数控车床的宏程序设计功能,解决车削多线大模数蜗杆这一加工难题。
数控系统宏程序,是以变量的组合,通过各种算术和逻辑运算、转移和循环等指令而编制的一种可以灵活运用的程序,其只需改变变量的值,即可实现同类型不同尺寸的加工和操作。以FANUC 0i数控系统为例,在数控车床上加工普通螺纹,一般使用的指令有G32单行程螺纹车削和螺纹切削循环与G92、G76等几种,但在车削大导程、多线蜗杆时,应用该指令编程其功能是不能实现的。因为该指令为斜进法切削,其适合切削的刀尖角度只有80°,60°,55°,30°,29°,0°共六种,而常用蜗杆的齿形角度为40°,如果使用直进法进刀G32指令和G92指令方式,则加工难度较大,容易出现“扎刀”现象。但如果使用宏程序功能即可解决这一问题。为此笔者探讨在数控车床上对车削蜗杆齿形的车刀与操作方法进行改进,以及用宏程序编制车削大导程、多线蜗杆的加工程序。多线蜗杆零件如图1所示。
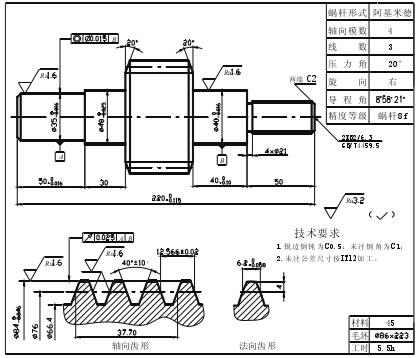
图1 多线蜗杆零件
一、多线蜗杆加工工艺要求及车削刀具分析
1.多线蜗杆加工工艺要求如图1所示,多线蜗杆为模数4m,线数3线,导程37.699mm、导程角8°58′21″、齿全高8.8mm的阿基米德蜗杆。该蜗杆切削面积大,要求工件刚性好,故需采用一夹一顶的装夹方式车削。
2.车削刀具分析多线蜗杆车削加工采取“分层切削”的方式,需法向安装车刀(阿基米德蜗杆齿形是一种轴向直廓齿形,精车时应轴向安装车刀,并且为正常发挥车刀各角度的作用、提高功效,需采用法向装刀方式)。车削刀具特点如下。
(1)蜗杆粗车刀。蜗杆齿形粗车刀采用W18Cr4V材料,刀具各角度如图2所示。为提高粗车刀刀尖强度,刀具切削刃的刀尖部分需用油石修研-5°倒棱。此倒棱宽度值视蜗杆模数、工件材料而定。在导程大、吃刀深度大、材料较硬时,倒棱则可取大些。粗车时,蜗杆粗车刀的刀尖角采用35°,这样粗车后便于用精车刀精车,其精车余量如图3所示。
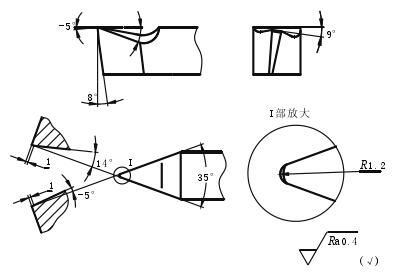
图2 蜗杆粗车刀
如图2所示,蜗杆粗车刀刀尖特点是:①采用圆弧形刀尖,增强了刀尖强度,刀尖散热得到了改善;②采用圆弧形排屑槽,增大了实际前角,改善了排屑条件;③刀尖的倒棱可在很大程度上防止冲击损坏刀尖,且不易崩刃。
蜗杆粗车刀可直接压装或安装在普通弹簧刀柄上车削。
(2)蜗杆半精车、精车车刀。蜗杆半精车和精车刀如图4所示,该刀头采用圆弧前角。此前角是在內圆磨床上用指形砂轮磨出的,如图5所示。其刀尖宽度略小于蜗杆牙底槽宽度。车削时采用“单边直进刀”,只切削蜗杆牙形的一个面,一面车完后再车第二个面。此时如加注合适的切削液,会使切削变得更加轻快,从而达到较小的表面结构值和较高的表面质量。
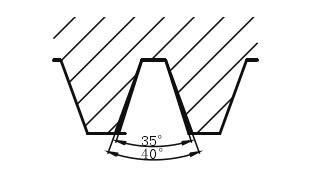
图3 精车刀牙形角与精车余量的关系
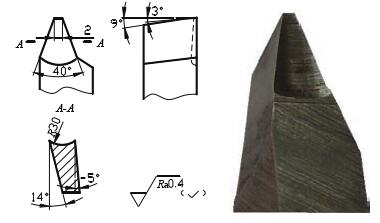
图4 蜗杆齿形精车刀
蜗杆精车刀刀尖各角度,如图4所示。刀头材料选用W18Cr4V或W6Mo5Cr4V2。此刀特点是,刀头强度好,刃口锋利,排屑顺畅,切屑变形小,散热条件好。装刀时可用样板或万能角尺对刀,使车刀两刀刃夹角的平分线与蜗杆轴线垂直。
(3)半精车和精车刀安装于弹簧刀杆上。弹簧刀杆选用弹性和强度较好的材料,如图6所示,这样半精车和精车时不需扳角度。
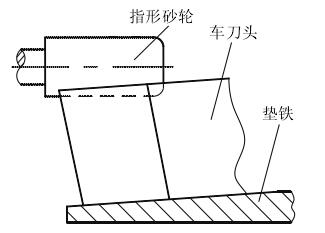
图5 车刀头前刀面刃磨
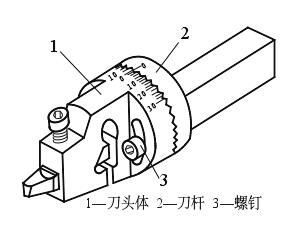
图6 弹性刀杆
普通弹性刀杆在较大的轴向切削力影响下会发生扭转变形,使所车蜗杆的轴向齿形角和螺距发生变化产生误差,从而降低加工精度。而现在,采用弹性和强度较好的刀杆则大大提高了刀体的刚性。刀体上选用12mm×12mm方孔,该方孔用线切割加工,这样用12mm×12mm高速钢刀头与刀体方孔配合,提高了刀头与刀体方孔的配合精度,从而减小了加工过程中刀头在刀体中的扭转、窜动。
二、多线蜗杆加工方法及走刀方式
在车削蜗杆时切除的金属量大,而且粗车时一般是刀具的几个切削刃同时工作,使得排屑不畅,切削力较大。因此,利用宏程序和G92指令结合编程,变换进给方式,可以实现不同齿形和深度的蜗杆加工,这对降低切削力,提高切削效率,保证加工质量十分重要。
1.粗车车削时,使用粗车刀,主轴转速n=200r/min。
车削方法主要是以“分层车削”的方式,如图7所示。这种分层加工方法,每次走刀的切削深度不大,刀尖受力状态和散热情况均得到较大的改善,而且利于排屑,不易“扎刀”,同时可以选用较高的切削用量,使切削效率得以成倍提高。

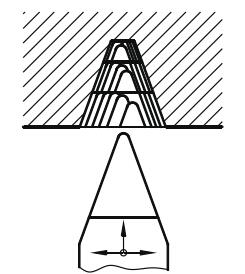
图7 粗车分层车削法
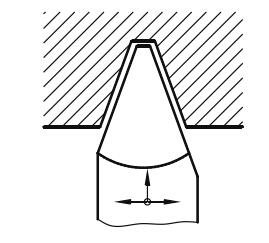
图8 精车两侧面直进刀方法
2.半精车、精车
在半精车、精车蜗杆齿形,安装车刀头时,利用蜗杆牙形样板或万能角度尺对刀。采用的进刀方式为直进刀方式,分别精车蜗杆齿形的侧面,如图8所示,这样可以保证得到较高的加工精度和较小的表面结构值。
在半精车蜗杆齿形时,可将齿底圆车至齿根圆尺寸φ66.4mm,并用游标卡尺测量控制齿厚尺寸,留精车余量0.2~0.5mm。
三、多线蜗杆数控加工程序设计
在FANUC 0i数控系统上,利用G92螺纹加工指令,编制蜗杆切削加工宏程序,分粗加工和半精加工、精加工几部分。车削如图1所示的多线蜗杆实例,对蜗杆齿形部分的车削进行程序编制,见表1、表2、表3。蜗杆加工成型后的三维图如图9所示。
表1 蜗杆加工(主程序)实例程序及说明
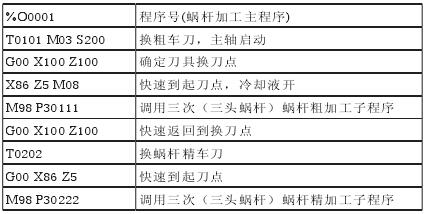

表2 蜗杆粗加工(子程序)实例程序及说明
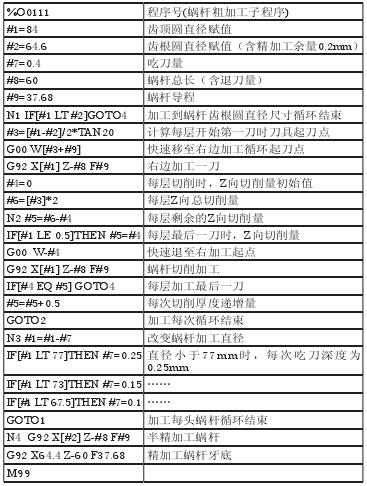
表3 蜗杆精加工(子程序)实例程序及说明
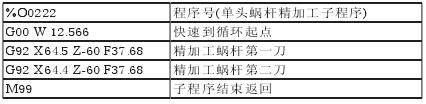
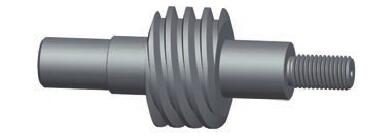
图9 多线蜗杆车削三维图
四、小结
在车削蜗杆的实际生产和教学中,我们采用改进刀具,大胆改变编程思路,通过用G92数控指令结合宏变量、分层编程加工蜗杆的方法,比较成功地解决了在数控车床上车削大导程、多线蜗杆的技术难题,从根本上解决了“扎刀”“闷车”等问题,提高了蜗杆的尺寸精度、分线精度,极大地提高了生产效率,大幅度减轻了操作者的劳动强度。实践说明,我们不但要借鉴前人传承下的极其宝贵的丰富经验,而且还要结合目前的先进设备,不断学习、探讨,这样才能使我们的技术水平得到更大提高。
投稿箱:
如果您有机床行业、企业相关新闻稿件发表,或进行资讯合作,欢迎联系本网编辑部, 邮箱:skjcsc@vip.sina.com
如果您有机床行业、企业相关新闻稿件发表,或进行资讯合作,欢迎联系本网编辑部, 邮箱:skjcsc@vip.sina.com
更多相关信息