新能源车用电驱动桥的设计
2022-8-30 来源: 江西江铃底盘股份有限公司 作者: 黄苏刚 邹兵凤
摘要:随着新能源汽车电动化步伐的加快,且电驱动桥具备高集成度、低成本、高传动效率和轻量化等诸多优点,传统汽车上的发动机、传动系统将逐渐被电驱动桥取代。本文先后介绍新能源汽车用电驱动桥的种类和设计开发,同时列举实例对设计过程加以说明,为汽车相关从业人员提供借鉴。
关键词 : 新能源汽车 ; 电驱动桥 ; 齿轮 ;轴承 ; 设计
电驱动桥是新能源汽车的动力系统和传动系统,有着为整车提供动力、承受负载、降低转速、增大扭矩和保证左右车轮差速等功能。通常包括电动机、减速器(含差速器、齿轮、轴承)、驱动半轴、刚性桥壳及轮毂轴承这些关键零部件。通过合理的设计优化及系统可靠的台架试验,可实现产品的紧凑化、轻量化、高效率和高寿命。
电驱动桥的种类
新能源汽车电动机的布置形式可分为电动机直连式、平行轴式和同轴式。直连式是采用电动机取代燃油车的发动机和变速器,所采用的电驱动桥,是从传统燃油车的驱动桥上通过加大齿轮速比以及提升齿轮精度衍变而来。因其保留了传动轴、整车电池布置空间受限,同时受速比最大为 7 的限制,导致无法采用高速小型化的电动机,因此该电驱动桥在国家新能源汽车发展战略中属于过渡技术产品,这种驱动桥称为第一代电驱动桥(见图 1)。
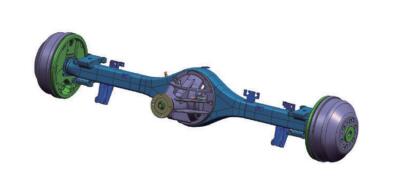
图 1 第一代电驱动桥
平行轴式结构是采用电动机取代燃油车的发动机、变速器和传动轴,将电动机集成为电驱动桥的一个子零件,并与电驱动桥的输出半轴呈平行布置,这种驱动桥称为第二代电驱动桥(见图2)。
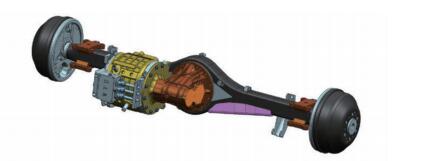
图 2 第二代电驱动桥
同轴式结构是在第二代电驱动桥基础上,将电动机与电驱动的输出半轴做同轴布置,这种驱动桥称为第三代电驱动桥(见图 3)。
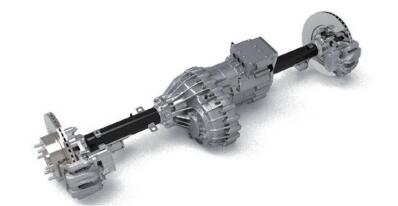
图 3 第三代电驱动桥
还有一种在乘用车基础上衍变出的产品,它也是将电动机轴与输出半轴呈平行布置,并且将车桥的承载功能独立出让刚性桥壳承担,而减速器配合球笼半轴传递扭矩。这种驱动桥称为承载与承受扭分离型电驱动桥(见图 4)。
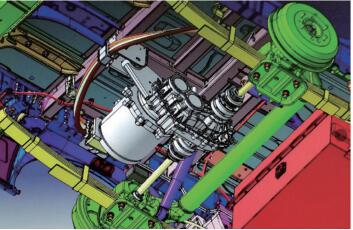
图 4 承载与承扭分离型电驱动桥
从目前各整车厂及车桥企业的研究方向看,第二代以及第三代电驱动桥可减轻电动机质量,降低整车成本,提升整车续驶里程。其中第二代电驱动桥因其前期投入低、技术易实现及性价比高,而备受市场青睐,本文将以实例着重介绍。
众所周知,全浮式驱动桥较半浮式驱动桥有着更好的刚度和更高的承载能力,轴承失效和油封漏油的故障率更低。电驱动桥相较传统驱动桥的簧下质量和设计载荷均有所增加,对驱动桥的各项性能要求也更为严格。故在此摒弃半浮式驱动桥而优选全浮式第二代电驱动桥进行设计。
电驱动桥的设计主要包括以下步骤 :
1)整车动力性仿真确定电驱动桥主要设计参数。
2)减速器齿轮及轴承的布置校核。
3)差速器强度设计校核。
4)半轴强度的设计校核。
5)轮毂轴承的设计校核。
6)刚性桥壳的设计校核。
以表 1 的整车参数和设计目标对某电驱动桥进行详细设计。
电驱动桥的设计开发
1.整车动力性校核
参考相关文献理论和计算方法,汇编基于EXCEL 的整车动力性计算表格。根据表 1 内相关参数,分别选取第一代和第二代电驱动桥进行动力性计算,计算结果分别见表 2 和表 3。
表 1 某纯电动轻客整车参数及设计目标
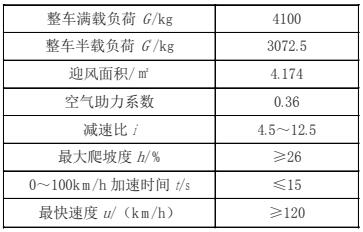
表 2 第一代电驱动桥动力性计算
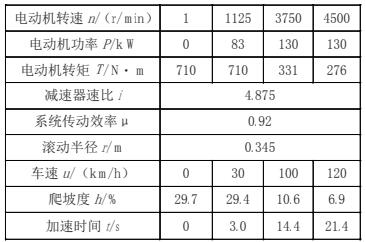
表 3 第二代电驱动桥动力性计算
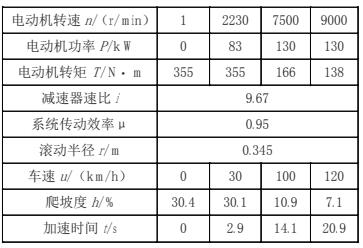
根据表 2 和表 3 的计算结果,采用同等功率的电动机,第二代电驱动桥将为整车带来更大的爬坡度、更快的加速时间和更高的传动效率。同时采用高转速电动机后省却传动轴,便于布置更多的动力电池,提高了整车能量密度及续驶里程,使电动机重量和整车成本下降。
2.减速器齿轮及轴承的布置校核
根据表 3 的整车动力性仿真计算结果,结合所选电动机的外形尺寸,对第二代电驱动桥减速器的齿轮及轴承做如图 5 所示布置。通过多次的软件分析和迭代修正,最终形成的齿轮及轴承参数见表 4 和表 5。
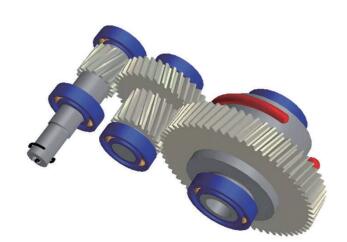
图 5 第二代电驱动桥减速器齿轮及轴承布置
表 4 各轴承参数
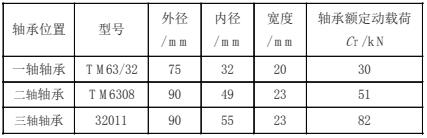
表 5 各齿轮参数
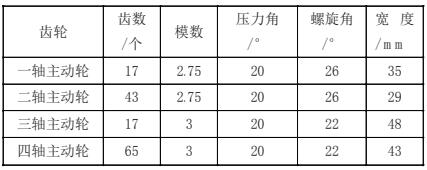
在最大输入扭矩工况下对齿轮及轴承强度和寿命进行 Romax 软件分析,分析结果见表 6 和表 7。
3.差速器强度设计校核
根据上述所选的第二代电驱动桥动力性计算结果,可得到该电驱动桥最大输出转矩 T。为保证电驱动桥应对快速升扭和其他冲击工况,在此给定输出转矩 1.8 的后备系数 ; 结合传统驱动桥所用的差速器承扭能力,按 1.8T 的承扭能力初选某型差速器总成。
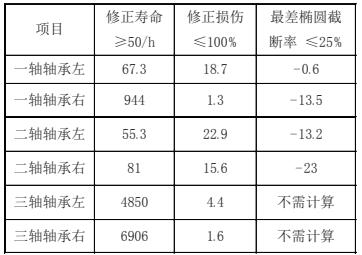
表 6 轴承分析结果
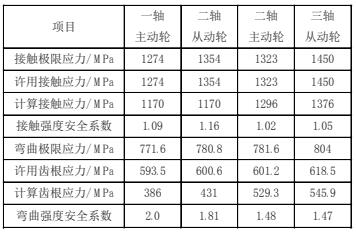
表 7 齿轮分析结果
结语
第二代平行轴式及第三代同轴式电驱动桥均不同程度的在传统驱动桥上衍变发展而来,是当下市场主流产品。
采用平行轴式电驱动桥可最大限度地借用传统驱动桥的刚性桥壳、半轴等相关资源,前期投入较低、技术易实现、性价比高,其技术难点集中在减速器总成的设计开发和相关台架试验上。采用第三代同轴式电驱动桥需将电动机作为承载件而借用不了传统驱动桥的刚性桥壳和半轴,开发高速中空电动机以及行星排齿轮的技术难度高、性价比低,然而高集成度和簧下质量轻的特性使它必然会成为电驱动桥的最终发展方向,推动汽车工业快速发展。
投稿箱:
如果您有机床行业、企业相关新闻稿件发表,或进行资讯合作,欢迎联系本网编辑部, 邮箱:skjcsc@vip.sina.com
如果您有机床行业、企业相关新闻稿件发表,或进行资讯合作,欢迎联系本网编辑部, 邮箱:skjcsc@vip.sina.com