数控等离子切割技术在凸轮加工中的应用
2015-11-26 来源:数控机床市场网 作者:河北机电职业技术学院 魏志强 高峰 韩伟
摘 要: 基于数控等离子切割的优势,针对凸轮零件轮廓特点,提出了一种以割代铣的加工方法。通过制定等离子切割工艺,编写数控程序,提高切割质量,控制热变形等措施,缩短了凸轮制造周期。节约了生产成本,减少了能源消耗,经过试验验证,此工艺方法达到了预期效果。
关键词: 等离子 数控 加工工艺 切割变形
在机械装置中,为了实现一些特殊或复杂的运动而广泛应用凸轮机构。通常片状凸轮的制造是利用靠模加工,凸轮车削,线切割等工艺方法,而这些方法存在生产效率低,周期长,成本高的缺点。为了节约成本,降低能源消耗,试验探索一种以数控等离子切割代替零件粗铣加工的工艺方法。
1 凸轮零件以切割代铣的工艺分析
等离子切割技术适用于切割各种形状复杂的零件,以中厚板毛坯零件的切割为主。优点是切割速度快,效率高,运行成本低等缺点是在断面垂直度误差过大,切口容易硬化。随着等离子切割技术的发展,特别是精细等离子切割技术的应用,零件的切割精度已经有了显著的提高。
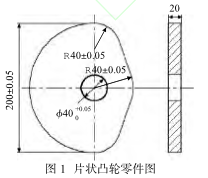
凸轮零件材料为 45 钢,厚度 20mm,零件如图 1所示。原工艺是板材手工切割下料,靠模粗铣,调质,精铣,新工艺是利用数控等离子精细切割代替手工下料和靠模粗铣。通过优化切割工艺,提高切割精度,控制变形量等方式来保证切割质量,凸轮零件新的工艺过程是切割下料,调质,零件精加工。
2 数控等离子切割工艺的制定
2. 1 切割机床的选择
根据零件毛坯材质和厚度,选择 TS-10B 型龙门式数控切割机作为零件粗加工设备。该型数控切割机为龙门式数控切割机中最小的一款,具有精度高,自重轻,运行稳定,价格实惠等优点。机床主要参数为有效切割宽度 2400mm,有效切割长度 2000 mm,等离子割,配置 1 组(可增配)移动精度 0.01mm/ 步,整机运行速度 3500 mm/min。
2. 2 切割轨迹的规划
凸轮零件轮廓由多段曲线组成利用CAD/CAM 软件能够更灵活的规划切割轨迹。具体操作如下:
(1) 导入零件模型,打开制造工程师 2013 软件,进入“文件”界面,利用“打开”功能查找凸轮三维模型,单击“打开”按钮,导入凸轮零件模型图,如图 2 所示。
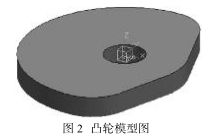
(2) 轨迹参数设置。进入“制造工程师 2013”加工界面,双击“毛坯”按钮进入定义毛坯对话框,单击“参照模型”,然后单击“确定”按钮设置零件毛坯,设置切割起始点(35,-126,100)。根据切割 20mm 厚板材割缝宽度,设置刀具类型立铣刀,刀具名称 R1刀具半径 1mm。
选择“平面零件精加工”进行加工参数设置。考虑切割热变形的影响,凸轮切割要为轮廓的精加工预留足够的余量,要在加工参数中进行设置,如图 3所示。在切削用量中选择慢下刀速度 400mm/min,切削速度 600mm/min,退刀速度 800mm/min。
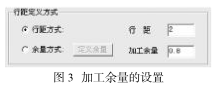
(3) 切割轨迹与程序的生成。工艺参数设置完毕,选择凸轮边界线作为轨迹生成的轮廓线。凸轮外侧为加工侧,经计算选择(34.4,-125.2)点作为进刀点袁选择(-50.9,-116.8)作为退刀点,生成切割轨迹,如图 4 所示。
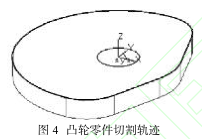
通过后处理文件生成数控切割程序,根据机床特点,调整后的程序如下:
01200\N12G90G54 G0X34.435 Y-125.174 \N14G43H0Z100.M07\N16Z10.
N18 G1 Z0. F600 \N20 X0. Y-100.8\N22 G17 G2Y100.8I0.J100.8
N24 X38.467 Y73.6 I0. J-40.8\N26 G1 X57.323Y20.267
N28 G2 Y-20.267 I-57.323 J-20.267\N30 G1 X38.467Y-73.6
N32G2X0.Y-100.8I-38.467J13.6\N34 G1X-50.971Y-116.819\N36Z10.
N38G0Z100.\N40M30
3 保证凸轮切割质量的措施
凸轮毛坯厚度要大于 20mm。 为提高数控等离子切割凸轮的精度,工艺实施要注意以下几点。
(1) 适当的切割电流。在凸轮切割过程中切割电流是切割速度的决定因素,但是切割电流过大会造成喷嘴损伤,影响切割质量。因此,综合试切情况,选择切割电流为 120A。
(2) 合理的切割速度。等离子切割的最佳切割速度可参照设备说明书经过试验来确定,适度的提高切割速度能改善切口质量,经试切验证,切削速度为600mm/min。
(3) 准确的电弧电压遥等离子弧切割机通常有较高的空载电压和工作电压,当电流一定时,电压的提高意味着电弧焓值和切割能力的提高。根据机床说明,选择空载电压 136V。
(4) 正确选择工作气体压力。工作气体包括切割气体和辅助气体,切割气体既要保证等离子射流的形成,又要保证去除切口中的熔融金属和氧化物。因此,气体流量一定要与切割电流尧,切割速度很好相匹配,根据 TS-10B 型龙门式数控切割机推荐的数据,切割 20mm 的 45 钢,选择 0.4 MPa 的气压。
4 零件切割变形的控制
为了减小切割变形对凸轮粗加工的影响,切割前必须对板材进行准确定位,充分的校平处理。切割的起点,方向,顺序等也是引起凸轮切割变形的主要因素,具体措施如下。
(1) 起弧点设置。根据凸轮零件的特点袁起弧点应设置在在板材边缘。起弧点距离板材距离太大或太小都会影响零件的正常切割袁距离太大会出现不起弧或断弧的情况距离过小会出现短路并且烧坏喷嘴的情况。经过实践验证,喷嘴距离工件的高度在6mm为宜。
(2) 切割方向的影响遥正确的切割方向应该保证最后一条割边与母板大部分脱离, 而且能够将切割质量好的侧面留在零件侧。在 CAD/CAM 软件中设置“顺铣”的方式规划切割轨迹,根据此设置,凸轮轮廓会留在沿割炬行走方向的右边,以此来保证凸轮轮廓面切割质量。
5 结论
本文在充分分析凸轮零件原有制造工艺的基础上结合数控等离子切割技术,提出了一种以割带铣的加工方法。利用等离子精细切割代替零件下料和粗加工,缩短了制造周期,节约了生产成本,减少了能源消耗。经过试验验证,此方法是合理可行的。
投稿箱:
如果您有机床行业、企业相关新闻稿件发表,或进行资讯合作,欢迎联系本网编辑部, 邮箱:skjcsc@vip.sina.com
如果您有机床行业、企业相关新闻稿件发表,或进行资讯合作,欢迎联系本网编辑部, 邮箱:skjcsc@vip.sina.com
更多相关信息