提高齿轮精滚齿加工精度的措施
2019-7-16 来源:山推工程机械股份有限公司 作者:张朝彪,李涛涛,宋 超,李相楠
摘 要:推土机终传动中一级和二级大齿轮的表面硬度为 55~62 HRC,在采用硬质合金刮削滚刀干切的方式进行精滚齿加工时,存在齿形和齿向误差超差的问题。从滚刀制造精度、安装精度、机床刚性等加工技术层面进行细致分析和研究,找出影响精滚齿加工精度的主要原因,通过加强过程控制并制定实施相应对策,使齿形和齿向误差合格率由改善前的 76%和 80%提升为 100%。
关键词:齿轮;精滚齿加工;齿形误差;齿向误差
推土机的工作环境复杂,承载大,因此对终传动系统中零部件的要求较高。齿轮是推土机终传动中重要的零件,其加工精度直接影响推土机终传动的质量和整机使用寿命。
其中,一级和二级大齿轮作为终传动中重要零部件,传递转矩大,正反转切换频繁,对齿轮的加工精度和表面硬度有严格要求。
我公司推土机终传动一级和二级大齿轮的表面硬度为 55~62 HRC,属于硬齿面齿轮,目前采用硬质合金刮削滚刀干切的方式进行精滚齿加工。因此分析研究精滚齿加工中影响齿轮精度的因素,并制定提升对策,对提高齿轮加工精度和整机质量具有重要意义。
1 、硬齿面齿轮精滚齿加工中存在的问题
齿轮误差检查项目主要包括:齿形误差、齿向误差、齿距极限误差、公法线长度变动误差和径向跳动误差,只有以上所述检测项目符合设计要求,才能保证齿轮传递运动的准确性、平稳性和载荷分布的均匀性。目前,我公司推土机终传动中一级和二级齿轮均采用超硬滚刮削工艺,由于受设备使用年限增加、刀具等各种因素的影响和制约,不能完全满足图纸规定的齿形、齿向误差的 8 级精度要求。
在现有加工条件下,以某型号推土机一级大齿轮为研究对象进行了工艺试验,该齿轮模数为 12 mm,齿数为 42,压力角为 20°,齿宽为 112 mm,材料为 S48C,齿部表面硬度为 55~62 HRC。对加工的某批次齿轮随机抽检 25 件,其检测结果如表 1 所示,其中图纸要求:齿形误差为 Fα≤40 μm,齿向误差 Fβ≤32 μm,齿距极限误差 Fp≤40 μm,径向跳动误差 Fr≤112 μm,公法线长度变动误差 Fw≤63 μm。由表 1 可知,Fα合格率为76%,Fβ合格率为 80%,Fp、Fr和 Fw合格率为 100%
表 1 齿轮检测结果
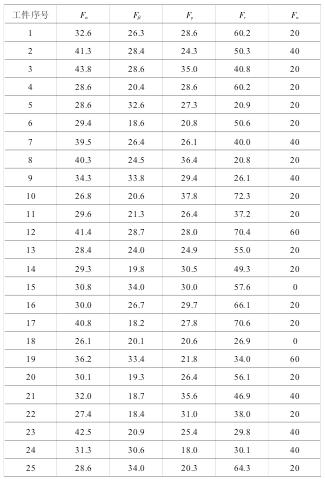
2 、影响硬齿面齿轮精滚齿加工精度的原因分析
齿形误差是指在齿轮端截面上,齿形工作部分内(齿顶倒棱部分除外),包容实际齿形的两条设计齿形间的法向距离。齿向误差则是指在分度圆柱面上(允许在齿高中部测量),齿宽工作部分范围内(端部倒角部分除外),包容实际齿向的两条最近的设计齿向线之间的端面距离。在实际滚齿加工过程中,不可能完全获得与理论齿形完全吻合的渐开线齿形,总会存在各种误差。
滚齿加工是展成运动,渐开线齿形主要靠滚刀与工件之间保持一定的分齿来保证,因此,滚刀齿形直接决定了齿轮的齿形误差。新滚刀的齿形由滚刀的制造精度决定,滚刀的制造精度越高,加工出工件的齿形精度也越高。
新滚刀经过使用后需要进行重磨,以保证其锋利及减少急剧磨损,滚刀经过重磨后其齿形误差主要由滚刀的重磨精度所决定,因此滚刀重磨精度的高低决定了加工出工件的齿形精度。另外,滚刀的安装精度(径向跳动和轴向窜动)也对齿形误差产生影响。
影响齿向误差的主要因素有:机床垂直进给导轨与工作台轴线平行度超差,工件安装误差以及加工让刀等。经对我公司现有滚齿机和工装的精度进行检测发现,滚齿机垂直进给导轨与工作台轴线平行度和工装端径跳均符合加工要求。
产生加工让刀的原因主要为加工余量过大和滚齿机刚性无法满足现有切削参数两方面,因此对淬火前后齿轮的公法线进行了测量,检测结果表明部分齿轮由于热处理变形出现了局部公法线余量过大的问题。
另外,对滚齿机在目前切削参数下其刚性能否满足加工要求也进行了研究。结果表明在目前切削参数下,数控滚齿机的机床刚性能满足要求,而普通滚齿机则不能完全满足加工要求。
通过分析得出,在现有条件下,影响我公司硬齿面齿轮齿形精度的主要原因为:滚刀制造精度、滚刀重磨精度和滚刀的安装精度(刀杆端径跳);影响齿轮齿向精度的主要原因为:热处理变形导致局部余量过大和机床刚性无法满足现有切削参数。
3 、提升齿轮加工精度的对策
为了提升硬齿面齿轮精滚齿加工的齿形和齿向误差,针对上述影响因素,决定通过加强精滚齿加工过程中的过程控制来提升齿轮加工精度。
3.1 滚刀制造精度
滚刀分为多个精度等级,不同精度等级的滚刀可以加工出相应精度等级的齿轮,如表 2 所示。目前,我公司采用 A 级精度普通硬质合金刮削滚刀进行精滚齿加工,由于滚刀自身存在制造误差和刃磨误差,且随着滚刀刃磨次数的增加,难以保证加工的齿轮达到 8 级精度。
表 2 滚刀与所加工齿轮精度等级对照表
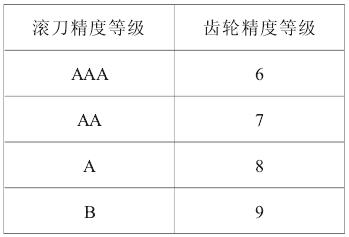
改善前,我公司所使用的滚刀为国内某刀具厂商(记做刀具厂商 1)的 A 级精度硬质合金滚刀,对刀具厂商 1的 8 把滚刀加工的首件的齿形结果进行了统计,如图 1所示。从统计结果中可以看出刀具厂商 1 的滚刀精度不够稳定,新刀加工出的首件不能完全符合齿形误差要求。为减少滚刀制造精度对齿轮齿形精度的影响,我公司又引进了另外一家国内某刀具厂商(记做刀具厂商 2)的 A 级硬质合金刮削滚刀,对刀具厂商 2 的 8 把滚刀与刀具厂商 1 的滚刀在相同条件下进行了工艺试验,刀具厂商 2 的 8 把滚刀加工的首件的齿形结果如图 2 所示。
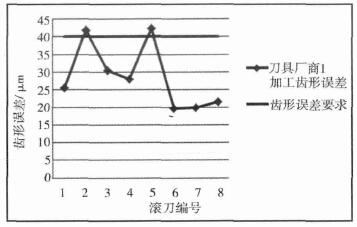
图 1 刀具厂商 1 滚刀的加工齿形误差
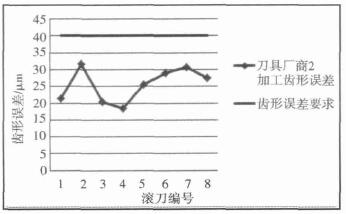
图 2 刀具厂商 2 滚刀的加工齿形误差
从统计结果可以看出,刀具厂商 2 的滚刀精度较刀具厂商 1 的滚刀精度稳定,能满足使用要求。为此,决定逐步将硬质合金刮削滚刀切换为刀具厂商 2 的滚刀,以此消除滚刀制造精度对齿形误差精度的影响。
3.2 滚刀重磨精度
硬质合金刮削滚刀的滚齿切削过程是轮齿包络过程,由于滚刀滚削时只加工轮齿的渐开线齿形部分,其刀齿的磨损主要是齿侧磨损,一般应限制在 0.3 mm 以内。滚刀的重磨是在前刀面上进行的,通过刃磨前刀面,将齿侧磨损、后角磨损和刀尖磨损消除。硬质合金刮削滚刀采用大负前角设计,如图 3 所示,主要目的是增加刚性,提高抗崩刃能力。改善前,采用定偏位置方式对滚刀进行重磨,但是随着滚刀重磨量的增加,发现滚刀齿形急剧衰变,如图 4 所示。
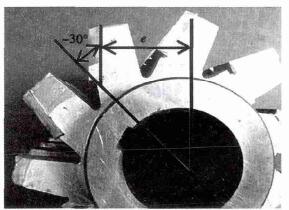
图 3 硬质合金刮削滚刀
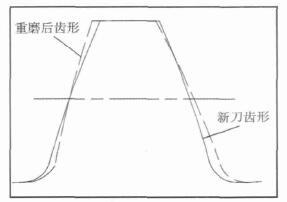
图 4 滚刀重磨后的齿形变化
为了保证重磨后得到理想的齿形精度,必须不断地调整滚刀前角,即变偏位置重磨。通过设计制作滚刀外径测量工装和滚刀偏位置检测标准量块,可以实现重磨后测量滚刀外径(如图 5 所示)和偏位置(如图 6 所示),从而实现了变偏位置重磨。通过试验跟踪分析,按照变偏位置重磨后,滚刀齿形精度虽然仍有所下降,但却是缓慢的,即使刃磨到极限,齿形的变化也基本是对称分布的。
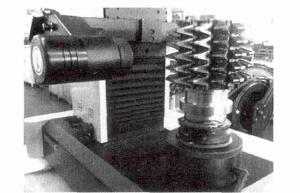
图 5 测量滚刀外径
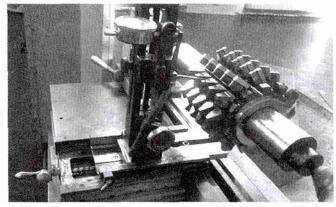
图 6 测量滚刀偏位置
3.3 刀杆端径跳
滚刀是安装在刀杆上工作的,因此,刀杆的制造精度及安装精度对滚刀的安装精度有着直接的影响,其中刀杆端跳误差的 75%和径跳误差的 25%会反映到齿形上。刀杆装入滚齿机刀架后应校正其径向跳动量和轴向窜动量。为保证加工精度,刀杆端跳需控制在 0.01 mm 以内,刀杆径跳需控制在 0.02 mm 以内。利用同一台滚齿机、同一把滚刀(相同条件下进行重磨),两把不同的刀杆分别加工 10 件工件,齿形结果如图 7 所示,两把刀杆装入滚齿机刀架后端径跳数据如表 3 所示。
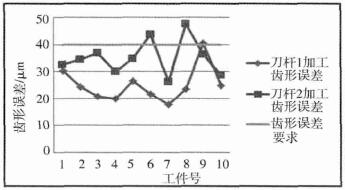
图 7 两把刀杆加工齿形结果统计
表 3 两把刀杆端径跳数据
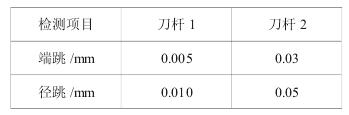
从齿形统计结果中可以看出,由于受限于滚刀制造精度,两把刀杆加工出的工件虽然齿形误差都不能完全符合要求,但刀杆 1 加工齿形精度明显优于刀杆 2 加工齿形精度。
对影响齿形加工精度的刀杆端径跳原因进行细化分析,并定期对滚齿机刀杆的端径跳进行检查,对于端径跳超出工艺要求的设备,按照表 4 所示的相应对策予以实施。
表 4 刀杆端径跳原因细分
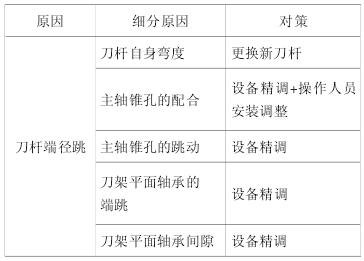
3.4 热处理变形
导致局部加工余量过大为了保证精滚齿的加工精度,齿轮齿厚余量在 0.5mm 以内的可以使用硬质合金刮削滚刀一次切除,当齿厚余量超过 0.5 mm 采用一次切除时,由于加工抗力增大,会导致振动增加,从而降低了加工精度。我公司推土机终传动中一级和二级大齿轮在精滚齿加工之前,需要对齿部进行感应淬火处理,经热处理后工件不同程度上会出现变形,个别工件的齿厚余量已超出 0.5 mm,变形大的已达 0.8 mm。
针对该问题,要求操作者精滚齿加工之前对工件公法线余量进行测量,对于公法线余量大和变形量大的工件,分为多刀加工,确保单次齿厚切除量在 0.5 mm 以内,从而减小加工抗力,减小振动,确保工件精度。
3.5 机床刚性无法满足现有切削参数
硬齿面齿轮的加工要求滚齿机要有较好的刚性,需要在专门的高刚性滚齿机上进行。目前,我公司硬齿面滚齿机主要为普通硬齿面滚齿机和数控硬齿面滚齿机。其中普通硬齿面滚齿机,随着使用年限的增加,部分滚齿机出现精度降低,刚性不足的现象。
为此,制定了两项对策:
①对刚性差的设备进行大修精调;
②适当降低刚性差的设备切削参数。
通过该两项对策的配合实施,消除了机床刚性不足对齿向精度的影响。
4 、改善后加工精度效果分析
为检验改善后的加工效果,按照改善后的加工方法,对加工的该批次齿轮随机抽检 25 件,并对 25 件工件进行了测量和统计,统计结果如图 8~ 图 12 所示。从结果中可知,齿形和齿向误差合格率由改善前的 76%和 80%提升为 100%。
另外,受益于加强过程控制的影响,齿距极限误差、径向跳动误差和公法线长度变动误差的精度也得到了提升。
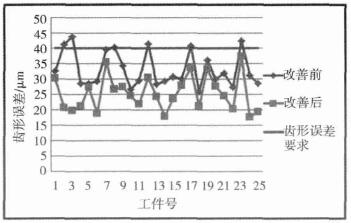
图 8 改善前后齿形误差统计结果
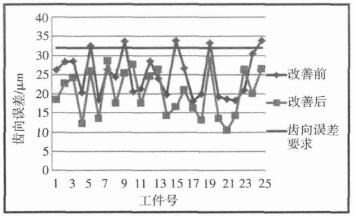
图 9 改善前后齿向误差统计结果
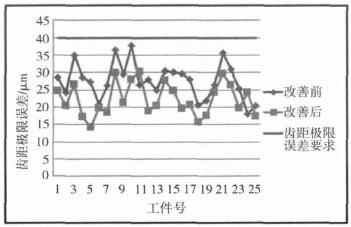
图 10 改善前后齿距极限误差统计结果
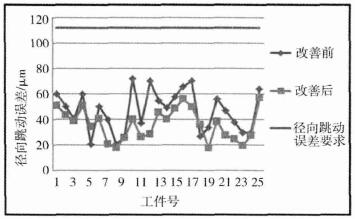
图 11 改善前后径向跳动误差统计结果
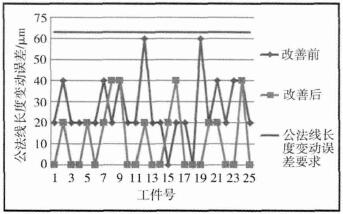
图 12 改善前后公法线长度变动误差统计结果
5 、结束语
针对我公司硬齿面齿轮精滚齿加工中出现的齿形误差和齿向误差无法完全满足图纸要求的问题,通过对影响精滚齿加工精度的因素进行细致分析,制定实施了相应的提升对策。实际应用表明,改善后通过加强过程控制,大幅度提高了精滚齿加工精度。本文所述的提高齿轮加工精度的措施,对提升精滚齿工艺水平和整机质量,发挥了积极作用,具有重要意义。
投稿箱:
如果您有机床行业、企业相关新闻稿件发表,或进行资讯合作,欢迎联系本网编辑部, 邮箱:skjcsc@vip.sina.com
如果您有机床行业、企业相关新闻稿件发表,或进行资讯合作,欢迎联系本网编辑部, 邮箱:skjcsc@vip.sina.com
更多相关信息