丝杠磨损对数控机床进给系统摩擦特性的影响研究
2021-4-1 来源:东方电气集团东方电机 华中科技大学 作者: 陈文平 潘捷
摘要: 摩擦是影响数控机床进给系统传动精度的主要因素之一。丝杠磨损会改变进给系统摩擦,降低其传动精度,影响加工产品质量。本文针对丝杠磨损引起的摩擦特性变化,基于 Stribeck 摩擦模型对比分析了丝杠未磨损和磨损区域的摩擦曲线。结果表明: 丝杠磨损后中低速阶段的摩擦呈现强烈非线性,与 Stribeck 模型描述不相符; 模型相对误差高达 13. 0% ,远高于未磨损区域的 3. 2% 。因此,摩擦特性的变化能反映丝杠磨损状态变化。
关键词: 数控机床; 滚珠丝杠; 磨损; 摩擦特性
1、引言
丝杠长时间使用时,受工件的切削负载冲击和零部件间的摩擦等因素影响,滚道表面金属疲劳脱落,滚珠与滚道间接触发生改变,造成进给系统摩擦特性变化。摩擦的存在降低了工作台运动的平稳性,使跟随误差偏大。对于摩擦引起的运动精度问题,学者们多通过建立精确的摩擦模型来估算摩擦,并以此为基础进行摩擦补偿,以减小摩擦的影响。
傅莹等[1]基于Lu Gre 摩擦模型,建立机器人转动关节的摩擦模型,并通过实验验证了模型的正确性。Shubo Wang等[2]针对伺服系统的摩擦特性,建立非线性连续可微摩擦模型,并提出相应的自适应补偿方法来提高系统的控制性能。Alexander Keck 等[3]对线性驱动轴的摩擦,建立 Elasto Plastic 摩擦模型,并作为摩擦前馈补偿的参考来提高系统运动性能。Zhang Libin 等[4]以 CFSM 模型来描述机器人关节的滞后效应,与 Stribeck 模型相比,提高了慢动作机器人关节扭矩的预测精度。Qing Pan 等[5]针对液压系统的摩擦,结合滞后薄膜动力学 和 Bouc-Wen 型对Stribeck 和 Lu Gre 模型进行修正,实验结果表明,在流体润滑状态下,修正后的模型在描述摩擦力 - 速度环的滞后行为方面更精确。陈浩等[6]针对直线电机滑台的摩擦特性,提出考虑加速度影响的 Stri-beck 摩擦模型,并通过实验验证摩擦模型的准确性。
上述研究多是针对特定系统,采用相应模型去描述系统的摩擦特性,但是丝杠磨损引起的摩擦变化尚未可知,摩擦模型能否适用还有待验证。为探究丝杠磨损对进给系统摩擦的影响,本文在丝杠特性测试平台上设计相关实验,通过丝杠磨损和未磨损区域实测摩擦力矩的对比分析,得到丝杠磨损对进给系统摩擦的影响规律。"
2、经典摩擦模型
Lu Gre 模型是目前应用较为广泛摩擦力模型,该模型利用摩擦接触面间弹性鬃毛形变的平均量来描述摩擦的动态行为[7]。如图 1 所示,将两接触面看作是充满弹性鬃毛的刚性表面,接触面产生相对位移后,接触面上鬃毛发生不同程度变形,此时接触摩擦是鬃毛弹性变形产生回复力的合力。
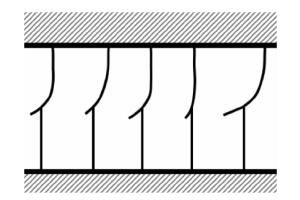
图 1 Lu Gre 模型中的接触鬃毛
Lu Gre 摩擦模型的数学表达式为
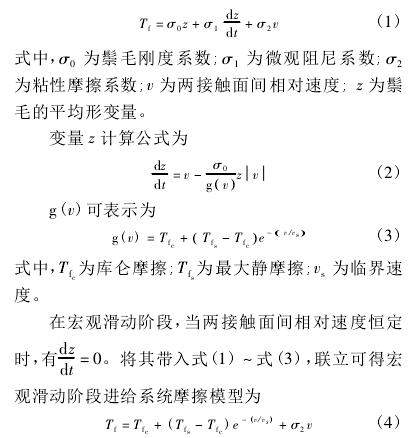
该模型也是 Stribeck 模型。
在速度较低时,摩擦力与速度呈非线性关系,摩擦力随速度增大而先减小后增大; 在速度较高时,摩擦力与速度几乎呈线性关系。Stribeck 模型曲线变化见图
。

图 2 Stribeck 模型曲线变化
3、丝杠特性测试平台
在丝杠特性测试平台上开展相关研究工作( 见图 3) 。由图可知,控制系统主要有 PMAC 运动控制卡和安川∑7 系列伺服驱动器,机械组成部分有安川∑ 7 系列伺服电机、梅花形联轴器、轴承座、Rexroth 滚珠丝杠副、直线导轨和工作台。测试平台配有多种传感器,见图 3b 椭圆框。由图可知: 在两联轴器间安装有 Kistler 4501A100R 扭矩传感器,用于测量丝杠的扭矩信号; 在直线导轨旁安装有海德汉公司的 LS477 光栅尺,用于测量工作台的位置; 丝杠螺母上贴有温度传感器,用于实时监测丝杠螺母的温度。

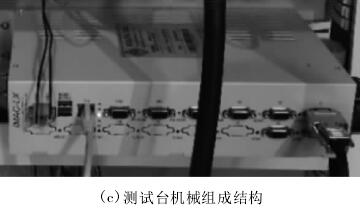
图 3 丝杠特性测试平台
测试平台上安装的丝杠在 150 ~ 300mm 区域滚道表面磨损严重,并在长时间放置后该区域已经出现锈蚀( 见图 4b) 。由图 4 可知,丝杠未磨损区域的滚道表面光滑,而磨损区域的滚道表面存在许多金属锈斑,且分布不均匀 。
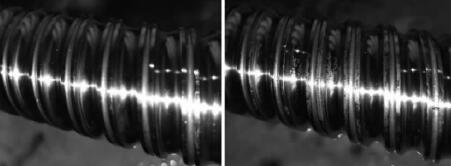
图 4 丝杠未磨损区域和磨损区域比较
4、丝杠磨损对摩擦的影响分析
测试平台中,安装在不同位置上的丝杠磨损程度不同,可用于对比分析丝杠磨损对摩擦的影响。为得到进给系统的摩擦曲线,在测试平台上进行多组恒速空运行实验。工作台的运动速度为 60 ~20000mm / min,且速度间隔不等,共计进行 70 组实验。为保证实验过程进给系统各零部件间充分润滑,在实验前或泵油后令工作台先往返运动多次。
为降低温度变化对摩擦力矩测量的影响,实验过程采用 Agilent 的 34972A 数据采集仪对螺母温度进行实时监控,以保证实验温度波动范围较小。处理数据时,丝杠两端预留一定距离,以减小加减速和丝杠反向间隙对摩擦力矩的影响。取丝杠行程 50~ 450mm 的数据作为有效数据信号,并将其按位置区间划分为若干段,分别统计速度和丝杠扭矩信号均值。取丝杠未磨损区域和丝杠磨损区域的实测摩擦力矩进行比较,结果见图 5。
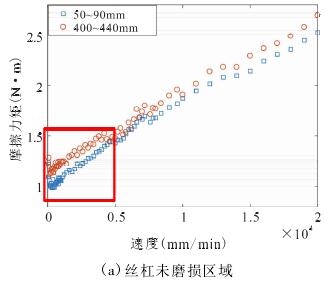
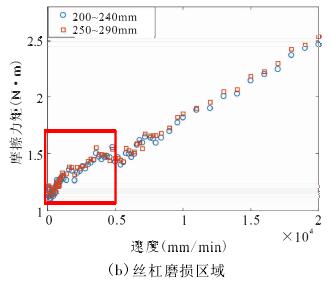
图 5 丝杠未磨损区域和磨损区域的实测摩擦力矩比较
由图 5 可以看出,丝杠磨损后进给系统的摩擦曲线出现明显分段。在中低速阶段,丝杠磨损区域的摩擦曲线较未磨损区域表现出强烈的非线性,这与Stribeck 模型曲线不符; 在高速阶段,两者趋势相同,摩擦力矩与速度几乎呈线性关系,这与高速阶段Stribeck 模型曲线相一致。由此可知,在中低速阶段丝杠磨损对进给系统的摩擦有较大影响。
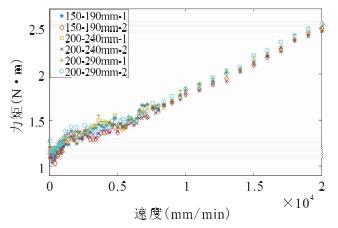
图 6 丝杠磨损区域的实测摩擦力矩
图 6 为丝杠磨损区域的实测摩擦力矩。摩擦特性测试平台进给系统的速度分割点选取可参考图 6。可知,摩擦曲线的速度分割点在 5000mm /min 左右。因此,本文选取 5000 mm / min
为速度分割点。以 Stribeck 摩擦模型作为基础,利用遗传算法对中低速阶段和高速阶段的摩擦力矩和速度进行参数辨识,结果见图 7 和图 8。由图 7 可知: 在中低速阶段,丝杠未磨损区域的实测摩擦力矩随速度提升先减小后增大,增长速率几乎保持稳定,这与 Stri-beck 模型描述相符,模型最大相对误差为 3. 2% ; 丝杠磨损区域的实测摩擦力矩随着速度提升先减小后逐渐增大,但是增长速率却逐渐减小,摩擦曲线趋于平缓,这与 Stribeck 模型描述不符,此时模型最大相对误差达 12. 9% 。
由图 8 可知,在高速阶段,丝杠未磨损区域和磨损区域的实测摩擦力矩与速度几乎呈线性关系,最大模型相对误差分别 3.3% 和3. 5% ,因此 Stribeck 摩擦模型可以描述高速阶段实
测摩擦力矩的变化。
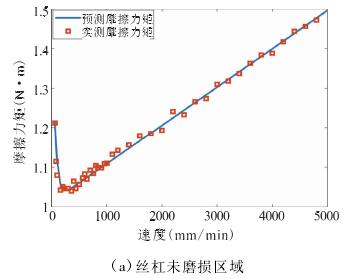
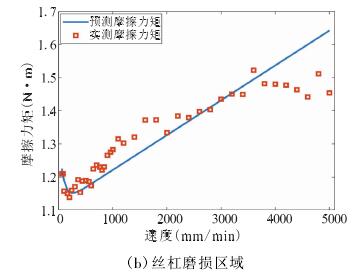
图 7 中低速阶段摩擦力矩的预测值与实测值比较
对不同位置上的实测摩擦力矩和速度数据进行参数辨识,中低速阶段的模型及最大相对误差见表1。由表 1 可知,受丝杠磨损影响,中低速阶段 Stri-beck 摩擦模型无法描述磨损区域的摩擦变化,其最大相对误差达 13. 0% ,远高于未磨损区域的最大相对误差 3. 2% 。
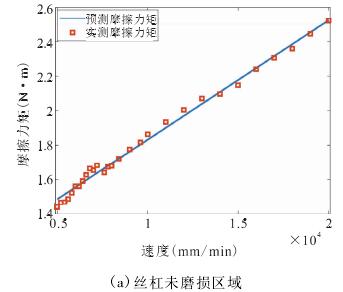
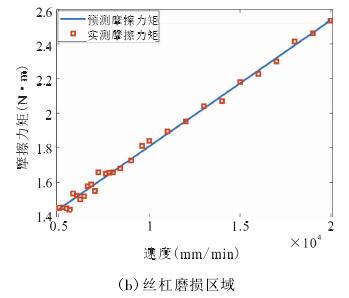
图 8 高速阶段摩擦力矩的预测值与实测值比较
表 1 中低速阶段摩擦模型及其最大误差
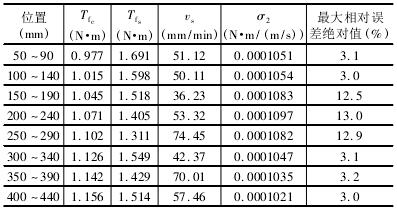
表 2 高速阶段摩擦模型及其最大误差
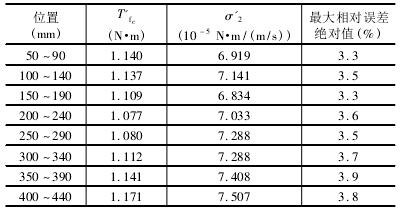
由于高速阶段 Stribeck 模型中( Tfs- Tfc) e- ( v / vs)项取值较小且实测数据无法体现低速阶段摩擦的变化,该项参数值难以辨识,因此本文引入等效库伦摩擦力矩 T'fc,将高速阶段摩擦模型视为 Tf= T'fc+σ'2v,其辨识参数和最大相对误差结果见表 2。由表可知,丝杠磨损对摩擦的影响较小,经典摩擦模型可以描述摩擦力矩的变化趋势,模型相对误差在 4.0%
以下。在高速阶段,由于润滑油在丝杠转速较高时会在接触面间形成动压油膜,丝杠磨损引起表面质量的改变对摩擦特性的影响明显降低。%
结语
本文针对丝杠磨损引起的摩擦变化,通过丝杠特性测试平台的相关实验数据,以 Striebck 摩擦模型为基础,对比分析了丝杠磨损和未磨损区域的摩擦曲线,得到丝杠磨损主要在中低速阶段对进给系统的摩擦影响较大,且摩擦表现为非线性,这时经典Stribeck 模型无法描述其摩擦力矩的变化,模型相对误差达 13.0% ,远高于未磨损区域的模型误差3. 2% 。后续可对丝杠磨损状态下的摩擦特性进行建模,为摩擦补偿提供参考来提高传动精度。也可以结合大量实验数据,利用摩擦特性的改变来表征丝杠的状态改变。
投稿箱:
如果您有机床行业、企业相关新闻稿件发表,或进行资讯合作,欢迎联系本网编辑部, 邮箱:skjcsc@vip.sina.com
如果您有机床行业、企业相关新闻稿件发表,或进行资讯合作,欢迎联系本网编辑部, 邮箱:skjcsc@vip.sina.com
更多相关信息