国产主轴单元在加工中心上的应用
2022-7-18 来源: 宝鸡机床集团有限公司 作者:罗海军
摘要:为了使国产主轴单元更好地应用于加工中心上,通过对机床典型工况的分析,确定出主轴部件所能承受的最大切削力。利用有限元分析软件对加工中心的箱体结构进行了优化,加装热传感器并进行了系统热补偿,有效提高了整机刚度与精度。结合北一机整体式主轴特有的气幕保护、锥孔吹气等功能,设计出具有干燥气体、保护主轴锥孔的气动系统,为最大限度地发挥主轴可靠性、稳定性提供保证。
关键词:国产主轴单元;最大切削力;有限元分析;系统热补偿;气幕保护
0 引言
我国的机床行业最近几年有了长足的进步,但是核心功能部件与欧美等品牌有一定的差距。主轴系统性能与机床的加工精度精密相关,是机床最重要的功能部件,主轴单元的动静态性能的优劣对加工精度和运行可靠性影响非常大。
本文详细地阐述了国产主轴在立式加工中心上的设计和应用方案,机床样机试制完成后做了大量热补偿和可靠性试验,并且汇总了一些问题反馈给主轴部件配套单位(北京北一机床厂),为其后续的改进、批量生产提供理论依据。打造质量过硬、结构先进的机床功能部件是提高我国机床行业整体水平的重要组成部分,是保障制造业核心竞争力、产业结构升级的必经之路。
1、VMC850L立式加工中心典型工况及主轴选型分析
1.1 低速大转矩铣平面
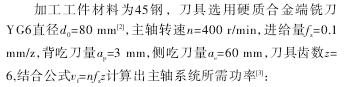

1.2 大切削力及功率铣槽
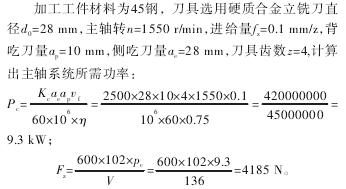
1.3 主轴功能部件选型结果分析
根据专项要求使用北一机床厂提供的TZ041A20001型直联主轴,该主轴最高转速为12 000 r/min,最大转矩为96.5 N,最大输出功率12 k W。这些数据都大于机床的典型工况加工计算值,并且大于本次机床的设计最大功率11 k W和最大转矩值75 N·m,主轴电动机选用FAUNC βi I8/12000来满足使用要求。
1.4 对主轴箱体进行有限元分析及静态刚度计算
立铣刀在铣槽时,主轴系统所受轴向抗力是造成主轴箱变型的重要因素,如图1所示。根据1.2节大切削力铣槽工况中所计算出的切削力Fz=4185 N,根据公式F0≈(0.50~0.55)·Fz,可计算出铣削时的轴向抗力F0≈2300 N。
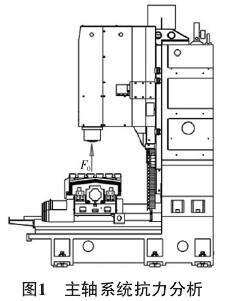
在F0载荷作用下进行主轴部件刚度K0计算[4],变形是由主轴箱自身和导轨接触变形两部分组成的。箱体自身负载处变形量(如图2)为10.7 μm,根据转矩平衡、变几何关系与Z轴导轨副刚度参数,计算出Z轴滑动导轨副接触变形所引起切削点位移为5.17 μm。主轴部件刚度K0=2300÷(10.72+5.17)=145 N/μm。
Simulation是Solid Works 附带的有限元分析插件,该插件在实践应用中较为成功,能满足单个零部件静态应力、应变和位移等的有限元分析。利用该软件为此次课题设计主轴箱体提供很好的仿真依据,对箱体的结构设计
起到至关重要的作用。
如图2所示,主轴系统在受到2300 N的轴向抗力时,其变形量最大为0.0107 mm,这时主轴中心距导轨安装面的距离为570 mm。如图3所示,将此距离变为500 mm,主轴系统在承受同样的轴向抗力时,变形量最大值为0.0104 mm,有 了明显的减少。通过仿真模拟和对主轴部件刚度K0的计算,在箱体结构设计过程中适当减小了箱体中心孔到导轨面的距离,在保证Z轴行程的前提下导轨支撑尽量下移 ,可有效地提高主轴系统的刚度。
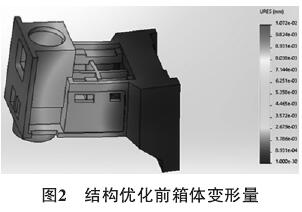
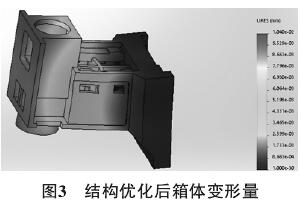
2、机床主轴功能部件的设计
2.1 主轴功能部件的气动系统设计
气动设计为本次主轴系统关键组成部分,直联主轴气路较为复杂,对气流的压力和干燥度有着相应的要求。如图4所示,主气源通过气动三联件4分为三路:一路接压力检测开关5监控整个系统的压力,如果过低机床就会报警;一路接圆盘刀库,刀库上自带电磁换向阀,控制刀套旋转;最后一路在进入高分子干燥器6前又分为三路,第一路通过电磁阀7控制主轴箱上竹节管加工吹气,起到清理和冷却工件的作用;第二路连接气液转化打刀缸9,打刀缸把气压转化为油压控制松刀,并且同时控制主轴拉刀与主轴锥孔吹气;第三路通过高分子干燥器6过滤后,依次通过调压阀3和电磁阀2来控制主轴上的气幕保护功能。
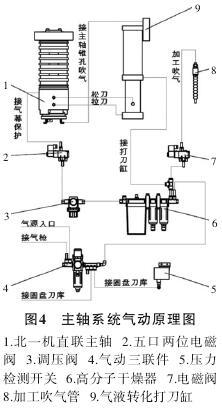
2.2 主轴功能部件的结构设计
主轴系统的优劣直接影响着整个机床的性能。区别于以往传统分体式结构,由图5可以看出,伺服电动机1直接连接在主轴箱体2上,减少了中间环节,提高了主轴系统整体精度和刚度,主轴箱采用高强度铸铁,经过多次时效处理,有效抑制了加工过程中切削力导致的变形及应力。外冷却管3集成在主轴箱右侧,结构紧凑,为加工提供大流量的冷却液。Z轴导轨防护罩4采用不锈钢材质,运行稳定可靠,保护立柱导轨淬硬面免受极端工况的破坏。导轨压板及镶条5配合贴塑、刮研工艺,使摩擦阻力小,负荷能力高,精度保持性长久。
高强度丝杠螺母座6配合大转矩交流伺服电动机与滚珠丝杠直接传动,保持了零件加工高精度;导轨、滚珠丝杠副采用中央集中自动稀油润滑,各个节点配有定量式分油器7,定时定量向各润滑部位注油,保证各滚动面均匀润滑,有效地减小摩擦阻力,提高了运动精度,保证了滚珠丝杠副和导轨的使用寿命。高刚性联轴器8连接主轴和电动机,保证主轴在高速运转的过程中平稳、可靠地传递转矩。
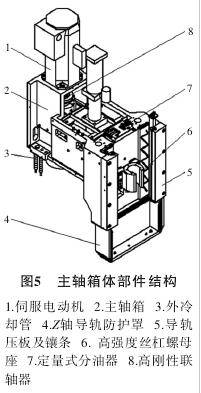
3、 机床主轴功能部件的热补偿及可靠性试验
3.1 主轴系统热误差形成的原因
由温升引起的热误差占总误差的40%~60%,是影响加工精度的主要因素。如图6所示,主轴高速旋转时,主轴轴承内外环高速摩擦产生大量热量,这些热量使主轴空间姿态发生变化,产生热伸长、热倾斜和热漂移等形变,这些形变又引起刀具与工件相对位置发生变化,导致工件加工精度变差。
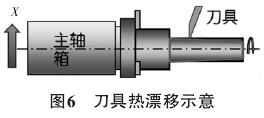
3.2 温度测量
在VMC850L立式加工中心的3个进给轴各布置2个温度传感器,其中一个靠近X、Y、Z轴丝杠螺母位置,另外一个远离丝杠电动机端;在主轴和机床底座(环境温度)上分别布置了2处温度传感器,采集相应的温度场信息并反馈到误差补偿系统,以实现对全闭环热态定位误差的实时补偿,温度传感器在数控机床上的安装如图7所示。
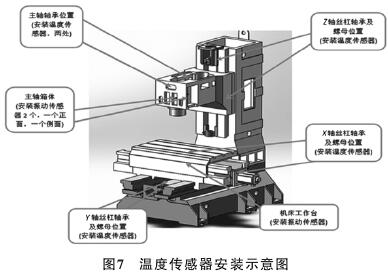
3.3 数控系统的补偿功能分析
根据机床工况和关键点温度预测热误差,数控系统反向调节机床坐标系原点或进给轴参数,来抵消或减少热误差。智能补偿模块采集机床热敏感点的实时温度,并根据补偿模型计算补偿参数,将补偿参数传送给PLC,再由PLC通过通信接口将补偿参数写入NC系统,改变CNC中热误差补偿参数,实现热误差补偿。
图8所示为五点法测量机床主轴热漂移,主轴空运转加热误差补偿功能和不加补偿各5 min,记录X向主轴热变形数据。补偿后热漂移明显减小,补偿效果良好。
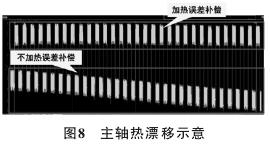
3.4 主轴的最大转矩及功率试验
在机床恒转矩区范围内选取主轴转速n=400 r/min,采用直径d0=80 mm六齿YG6硬质合金钢端铣刀进行铣削试验,通过改变进给速度或切削深度,使机床达到设计最大转矩T=70 N·m,此次试验过程中主轴及过载保护装置工作正常、可靠。
在机床恒功率区范围内选取主轴转速n=1550 r/min,采用直径d0=28 mm四齿硬质合金钢端铣刀进行铣削试验,通过改变进给速度或切削深度,使机床达到设计最大功率11 k W,此次试验过程中主轴同样工作正常、可靠。
按照GB/T 18400.2-2010《加工中心 检验条件 第2部分:立式或带垂直主回转轴的万能主轴头机床几何精度检验(垂直Z轴)》中G10和G11项复查负荷试验后主轴单元的精度,实测精度均优于国家标准。
4、结语
数控加工中心本身功能需求的扩大,需要与之配套的功能部件水平也要大幅度提高, 甚至很多功能的增加和提高需要通过功能部件来完成,通过本次主轴功能部件在加工中心上的应用试验,可以充分地了解和挖掘国产功能部件的性能和特点,为以后的改进和功能部件品牌提升打下基础。在面对国外竞争时不被制约,是我国基础制造业的重中之重。机床推向市场面对终端用户,主轴等功能部件对机床的精度保持性、可靠性、稳定性方面发挥着巨大的作用,随着国产部件质量和匹配度的增高,机床行业也会焕发出新的活力,国产机床的整体性价比将会大大提高。
投稿箱:
如果您有机床行业、企业相关新闻稿件发表,或进行资讯合作,欢迎联系本网编辑部, 邮箱:skjcsc@vip.sina.com
如果您有机床行业、企业相关新闻稿件发表,或进行资讯合作,欢迎联系本网编辑部, 邮箱:skjcsc@vip.sina.com
更多相关信息