新能源汽车电驱动总成及制造技术
2023-7-5 来源: 上海市汽车行业协会 作者:张书桥
1. 序言
发展新能源汽车是我国从汽车大国迈向汽车强国的必由之路,新能源汽车概念最早于 “863”计划中提出。在新能源汽车发展规划中提出了“三纵三横” 的技术研发布局,即以纯电动车、插电式混合动力(含增程式)汽车、燃料电池汽车为“三纵”,布局整车技术创新链,强化整车集成控制创新。以动力电池和管理系统、驱动电动机与电力电子、网联化与智能化技术为 “三横”,构建关键零部件技术供给体系,提升产业基础能力。2022 年中国新能源汽车持续爆发式增长,全年销量 680 万辆,市场渗透率 25.6%。2023 年预计为 900 万辆,同比增长 35%。我国新能源汽车市场培育了全球最大的电动车市场,电池供应链体系远远领先美国和欧洲,但是品牌竞争力弱,尚未被全球市场广泛接受。
2. 电驱动总成
电驱动总成是新能源电动车的心脏,等同于传统燃油车的动力总成——发动机 + 变速器,作用是把化学能转化成电动车的动能,是直接决定车辆动力、能耗等性能的核心部件。
电驱动总成是以电动机作为动力能源的驱动系统,包括电动机控制器、电动机及传动机构。电驱动总成是电动车中至关重要的机构,直接影响到汽车寿命以及驾驶员的安全。
纯电动车的电驱动总成有四种形式,分别为传统布置、电动机 & 驱动桥组合式、电动机 &驱动桥整体式、轮边 / 轮毂电动机。四种电驱动总成的特点见表 1。
表 1 四种电驱动总成的特点
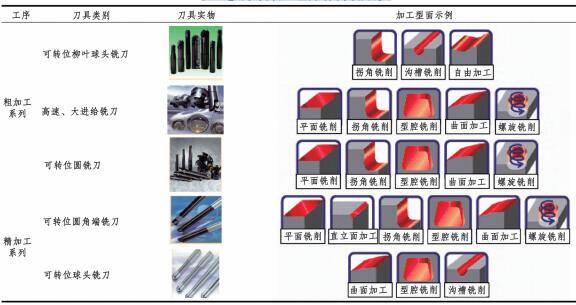
电动车驱动系统是电动车中最关键的系统,电动车运行性能主要决定于电动机驱动系统的类型和性能。电动车驱动系统一般由牵引电动机、控制系统(包括电动机驱动器、控制器及各种传感器)、机械减速和传动装置、车轮等构成。它有四种组合形式,分别为机械驱动系统、机电集成化驱动系统、机电一体化驱动系统及轮毂电动机驱动系统。四种驱动系统的特点见表 2,几种典型的驱动系统如图 1 所示。
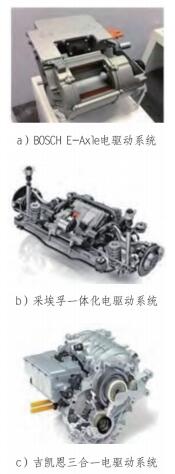
图 1 典型的电驱动系统
表 2 四种驱动系统的特点
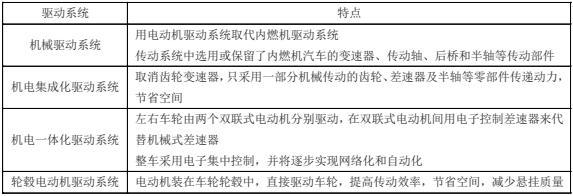
随着中国新能源汽车销量的逐步增加,电动化将催生电驱动总成成为继电池系统之后的第二个赛道,预计2025—2030年中国新能源汽车电驱动市场规模将达到 866 亿 ~1572 亿元。纵观全球新能源汽车研发方向,由于受到车辆空间限制和使用环境的约束,电动汽车对电驱动总成提出了更高的要求 : ①更高的性能,低速大扭矩,宽恒功率等。②耐环境温度更高,寿命更长,噪声更低。③耐高强度振动,结构坚固,质量轻,体积小。④成本低。⑤参与整车热管理。
3. 电动机
美国汽车行业指定了电动机发展路线图,到2025 年效率> 97%,功率密度 5.7kW/kg,成本3.3$/kW。按照这样的发展方向,今后电动机的改进有以下几方面。
3.1 发卡电动机——Hair-pin扁线电动机技术
相对圆线电动机,采用 Hair-pin 扁线电动机(见图 2)可以明显减小电动机体积、减轻电动机质量、增加电动机功率密度及转矩密度。通常可将槽满率提高至 70% 以上,超过普通绕组 20%~30%,有效降低绕组电阻,从而降低铜耗,产生更强的磁场强度,提升电动机功率密度。扁线之间接触面积大,可提高散热效率。绕组端部更短,可以降低电动机端部空间用铜量15%~20%。
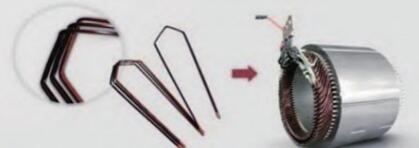
图 2 Hair-pin 扁线电动机
3.2 永磁同步电动机
永磁同步电动机(见图 3)的优势是体积小、质量小、功率密度高、运行效率高、结构简单紧凑、扭矩大且平顺、调速性能好。劣势是弱磁控制问题、反电动势及高温振动环境下的退磁问题。
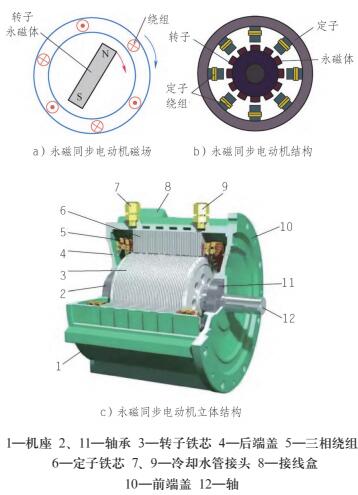
图 3 永磁同步电动机
转子转速与定子磁场的转速保持同步。降低定子、转子的铁耗也非常重要,定子、转子硅片内部会因为电流磁场等变化而产生涡流,为了减少这部分的涡流损耗,硅钢片的厚度越来越薄,从 0.35mm 降到 0.3mm 以下。为了优化电动机内部的磁场分布,提高电动机效率,针对转子铁芯的磁道设计也得到越来越多的关注。
3.3 混合磁铁技术
混合磁铁技术就是用烧结永磁铁 + 永磁体粉末与黏合剂混合。美国 Lucid Air 公司电动机每英里的能耗为 218W · h,特斯拉 Model S 每英里能耗为 250W · h,续航里程美国 Lucid Air公司超过特斯拉 Model S100 余英里(1 英里=1609.344m)。
混合磁铁技术把一切空间利用到极致,磁铁填满所有的空隙。钕铁硼烧结永磁体是难加工成异型的,就是在烧结永磁铁的基础上,将永磁体粉末与黏合剂混合,直接填满整个空间,既解决磁铁固定的问题,又增加了磁通量,如图 4 所示。
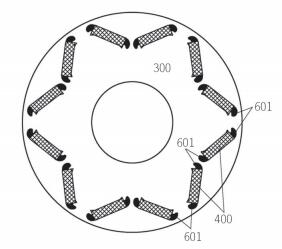
图 4 混合磁铁技术
3.4 碳纤维套筒
高转速隔磁桥的设计一直是难点,转子高速旋转,转速大,离心率大,转子边缘的部位容易受压破裂。如果加厚隔磁桥,会产生闭合磁场,在转子内部,没有与定子磁场产生相互作用,磁场就会浪费,效率被限制,产生铁耗、增加发热,高热加剧转子的膨胀和解体的风险。
特斯拉在电动机转子上增加了碳纤维保护套,其核心作用是加强电动机和转子的结构强度,防止高速工况下永磁铁的脱落。特斯拉碳纤维转子如图 5 所示。
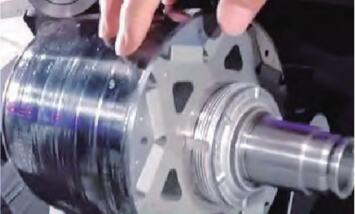
图 5 特斯拉碳纤维转子
3.5 油冷却
随着电动机功率密度和转速的不断提升,以及集成化使单体部件体积逐渐缩小,传统电动机的风冷或者外壳水冷方式已经无法满足散热需求,油冷电动机技术路线逐渐兴起。冷却油可直接与电动机发热部件接触,散热效率高于传统的水冷和风冷,且油介质具有绝缘性好、介质常数高、凝固点低和沸点高等优势,可提升电动机的效率密度。对原有的热管理系统进行重新设计,将电动机腔体和减速器打通,然后通过电子油泵或机械设计,使减振器内部原有的冷却润滑油能够进入到电动机内腔,实现定子、转子的物理降温。另外对油品的性能和清洁度有更高的要求。扁线油冷电动机转子如图 6 所示。
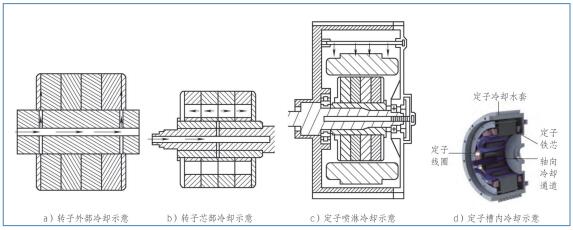
图 6 扁线油冷电动机转子
4. 二级变速器
电动车电动机的工作范围广,转速一般在0~20000r/min,甚至可以达到30000r/min。相对来说,中低转速的情况下,电动机的扭矩非常足,工作效率相对较高 ; 在高速的情况下,电动机的效率和扭矩则会急速下降。而二级变速器的作用就是使电动机尽量工作在高效率的转速区间,从
而降低损耗,提高续航里程,可节省的电量高达13%。二级变速器的电动机效率如图 7 所示。
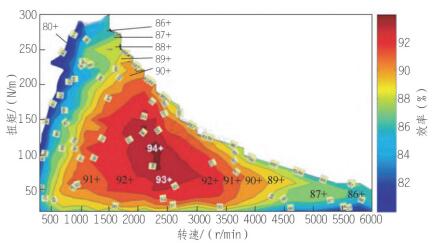
图 7 二级变速器的电动机效率
5. 高压化
美国汽车行业三电控制器发展路线图中提出,到 2025 年电控效率> 98%,密度 100kW/L,成本 2.7$/kW。对于电动车来说,高压化可大大减少同等功率需求条件下电驱动总成内组的损耗,提高系统效率,继而可进一步减少达成同样续航里程条件下的电池电量。减少电池成本的同时降低整车质量。另外,高压化还能提高充电效率。因此,提高电动车整车电压至800V,甚至1000V是行业的发展方向。
例如保时捷 Taycan 是首款 800V 高压平台的量产车型,同等功率下,当电压从 400V 提升到 800V 时,工作电流将降低一半,进而线束体积、功率损耗均有下降。与奥迪 e-tron 400V 电压平台对比,系统能耗损失降低 5%,续航里程增加10%,质量减少 20%,系统尺寸优化 30%,其中电动机尺寸可优化 35%。
6. 电驱动总成制造技术
电驱动总成不断发展,其新的制造技术主要围绕轻量化、高速化、低噪声及一体化。
6.1 一体化压铸
三电系统通常占新能源汽车质量的30%~40%,因此三电系统是新能源汽车轻量化的主要方向。与传统汽车相比,新能源汽车三电系统将导致整车质量增加,三电系统会额外增加200~300kg 的质量。新能源汽车动力总成系统比传统燃油车重 1.5~4.0 倍。目前三电系统的电子壳体、电动机壳体、电控壳体、电池构件及电池箱都在使用铝压铸产品,双电动机桶和电控壳体如图 8、图 9 所示。

图 8 双电动机桶 图 9 电控壳体
6.2 强力珩齿
由于电动车中电动机要求更高的转速——15000~30000r/min,更严苛的噪声限制NVH(噪声、振动与声振粗糙度),更高精度的动力齿轮要求——4~5 级,更高的波纹度和表面粗糙度,更高的几何公差来降低不稳定性,所以要采用强力珩齿工艺。强力珩齿工艺的特点是机床对于磨齿具有更小的退刀间隙,齿面加工为鱼刺纹,区别于传统磨齿的直线型纹路,此外具有更好的NVH 特性,降低噪声,适合高速旋转的电动机轴。
6.3 行星齿轮
锥齿轮结构跟传统的差速器差别很大,采用行星齿轮可实现小型化,多个外部齿轮绕着中间齿轮旋转,行星齿轮承载能力大、体积小,多个行星齿轮相互配合作用,每个齿轮传动之间的效率损失只有 3%,几乎无反冲。行星齿轮如图 10 所示。行星齿轮加工工艺流程为 : 锻造→车削→强力刮削→热处理→磨孔珩孔→平面磨→珩齿→清洗。
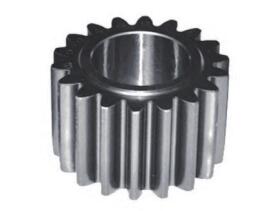
图 10 行星齿轮
6.4 切削技术
电动机是新能源汽车的核心部件,其制造要求高精度、高效率和高可靠性,特别是切削精度直接影响汽车的质量。很多刀具企业针对驱动电动机壳可提供整体解决方案,例如森泰英格的镗刀(见图 11)采用合金钢整体轻量化设计,刀体质量控制在 18kg 以内,多台阶 PCD 导条式可调镗铰刀,多切削刃,内冷设计。相较于单刃镗刀,可提高效率 6 倍以上。另外森泰英格自主研发的可转位强力车齿刀(见图 12),采用高刚性精密定位接口技术和复合基多熵纳米涂层技术,刀片耐磨性更好,寿命更长。
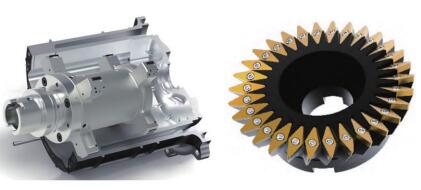
图 11 镗刀 图 12 车齿刀
电动机轴花键的加工方法有很多,以往主要采用车削、铣削、滚切和磨削等加工方法。滚轧刀通过数控机床进给的优点是刀具可以在任意位置切入工件,而不像传统的搓齿工艺工件成形圈数受齿条长度限制。如图 13 所示为恒锋工具股份有限公司开发的滚轧刀。
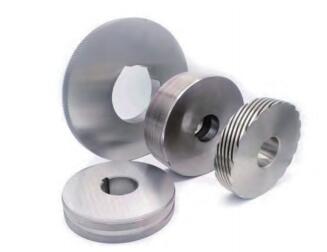
图 13 滚轧刀
随着电驱动的一体化,电动机轴最受青睐的加工方式还是冷挤压成形工艺,冷挤压的工件尺寸准确、强度高。从生产厂家角度讲,冷挤压工艺节约材料,生产效率高,适用面广。
投稿箱:
如果您有机床行业、企业相关新闻稿件发表,或进行资讯合作,欢迎联系本网编辑部, 邮箱:skjcsc@vip.sina.com
如果您有机床行业、企业相关新闻稿件发表,或进行资讯合作,欢迎联系本网编辑部, 邮箱:skjcsc@vip.sina.com