龙门加工中心丝杠组件热态性能与温度场实验研究
2016-3-14 来源:四川理工学院 机械工程学院 作者:杨海栗 田建平 胡勇 付磊 张良栋
摘要:龙门加工中心丝杠热变形是影响机床加工精度的重要因素。为减小丝杠热变形对机床加工精度的影响,以丝杠的实际工况为基础,建立了丝杠温度场及热 - 结构耦合分析模型,运用有限元分析法获得了丝杠表面的温度场分布及丝杠重力和进给方向的热变形规律。运用 M7500 红外摄像仪进行了丝杠温度场实验,验证了一定时间段内温度场分析的准确性,并结合实验对仿真参数进行修正,提高了温度场仿真分析的准确性,为丝杠进给过程中控制系统的热误差补偿和整机润滑散热系统的结构改进提供了理论依据。
关键词:龙门加工中心;丝杠;温度场;热变形;温度场实验
0 引言
在精密加工中,机床热变形所造成的热误差是影响机床加工精度的重要因素。滚珠丝杠是其中重要的精密传动部件,其热变形将直接影响机床进给方向的加工精度。因此,减少丝杠热变形所造成的误差,并在传动过程中进行热误差补偿是提高机床加工精度的关键所在。
本文以四川某公司 GMC1600A 龙门加工中心 Y向滚珠丝杠传动系统为研究对象,结合其实际工况,建立丝杠分析模型,并将丝杠螺母对丝杠的作用等效为移动热载荷及移动力载荷,进行温度场及热- 结构耦合分析研究,得到丝杠表面的温度场分布及热变形规律,并结合温度场实验对仿真分析参数进行修正,提高了温度场仿真分析的准确性,为丝杠进给过程中控制系统的热误差补偿和整机润滑散热系统结构的改进提供了理论依据。
1 Y 向丝杠传动系统模型
本文针对该型号龙门加工中心 Y 向滚珠丝杠传动系统建立分析模型,其三维模型如图1 所示。结合该加工中心的实际工况,考虑以常用进给速度 8000mm/min 来进行分析研究。该丝杠传动系统的运动采用螺母旋转而丝杠固定方式进行,丝杠螺母自身旋转并带动十字滑座及其上部件沿轴向移动。丝杠螺母转动惯性小,易于实现高转速运动。
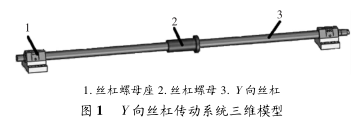
1.1 滚珠丝杠传动系统的热力学模型
(1)边界条件与发热量计算
滚珠丝杠系统的热源主要来自于丝杠螺母的循环移动摩擦生热和两端轴承的旋转摩擦生热。丝杠与外界的热交换主要为丝杠表面与周围空气间的热交换。滚珠丝杠螺母的热生成率计算

式中: Q1为滚珠丝杠螺母单位时间产热量,W ; M 为滚珠丝杠螺母的摩擦力矩,N·m; n 为滚珠丝杠螺母转速,r/min。
轴承热生成率的计算:

式中: Q2为轴承单位时间产热量, W; M 为轴承的摩擦力矩,N·m; n 为轴承的转速,r/min。对流换热系数的计算:
丝杠传动系统与空气间的对流换热问题,可采用大空间自然对流换热关系式

式中: α 为对流换热系数,W/m2·K; d 为管壁直径:m; λ 为导热系数, W/m·K; Nu 为努谢尔特数。
考虑滚动轴承、丝杠及丝杠螺母上的热量分配,并假设三者间的接触为面接触,计算所得参数如表 1 所示。
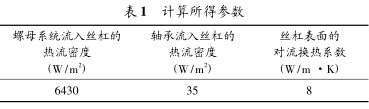
(2)温度场基本方程
由于丝杠的热载荷为轴对称形式,且无内热源。
假设导热系数是常数,且满足圆柱坐标系下的导热程

其中 2为拉普拉斯算符。在圆柱坐标系中,2T 的形式为: 

其中 α = k/ρc; ρ 是密度,单位为 kg/m3; c 为比热容,单位为 J/(kg·K); T 为瞬态温度,r、i、z 为空间变量。
(3)热变形的基本方程
对于丝杠温度分布不均的情况, 热变形满足下列公式

式中: α 为线膨胀系数; l 为丝杠的长度,m; T(x) 为丝杠温度分布函数; Δx 为丝杠的伸长量,m。
2 丝杠温度场及热- 结构耦合分析
2.1 模型的简化
该丝杠传动系统结构并不复杂,但考虑丝杠螺纹节距较小及丝杠螺母在丝杠上的循环往复运动,如在ANSYS 中进行螺纹绘制并网格划分会造成网格过密及运算量急剧增大的现象。因此,对螺纹部分进行省略,在分析中将丝杠与丝杠螺母的接触简化为面接触;丝杠螺母及轴承对丝杠的作用在温度场及热- 结构耦合分析中以载荷的形式进行加载,从而在分析时可对丝杠螺母、轴承及丝杠两端螺母座进行忽略, 只针对丝杠本身进行分析研究。
在 ANSYS 中进行丝杠建模以后,采用三维十节点热实体单元 SOLID 90 进行自由网格划分,为更精确地模拟丝杠螺母在丝杠上的往复运动及观察各节点的温度、位移变化,对各边线和丝杠表面进行了网格细化,划分单元后单元总数为 37686 个,模型网格划分结果见图 2。分析丝杠材料采用轴承钢,其参数见表 2。
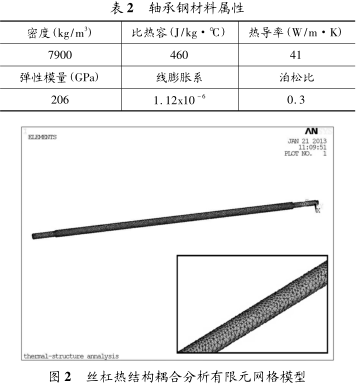
2.2 模型加载
(1)温度场分析模型加载
在施加移动循环热载荷的过程中,丝杠初始温度与外界环境温度均设置为 20℃,并采用载荷子步的方法模拟丝杠随时间的温度变化情况,热源均以热流密度的形式加载。在求解过程中,假设丝杠与空气的对流换热系数、丝杠螺母和轴承对丝杠的热流密度均保持不变,热边界条件的加载过程如下:
① 由 Y 向进给速度计算出移动热源的加载速度,同时设定每个载荷步的移动距离和加载时间长短;并计算丝杠与空气间的对流热载荷及轴承传热。
② 采用 ANSYS 中* DO 与* IF 命令流实现热载荷的移动及往复运动。因 ANSYS 仅读取最后施加的面载荷进行计算,因此在热流加载过程中,每移动一步都需在热源所达表面施加热源载荷,并在完成该次运算后将其删除,同时加载该表面与空气的对流载荷。
(2)热- 结构耦合分析模型加载
由于该 Y 向丝杠在运动过程中会受到重力的作用,而丝杠螺母连接在十字滑座上,在其连接处会受到一方向向上的支撑力的作用,分析同时考虑两载荷作用,从而更为准确的描述了丝杠的实际变形情况。结构分析边界条件加载过程如下:
①对丝杠的两端进行全约束,并加载重力加速度;
②采用* DO 与* IF 命令流实现集中力载荷的移动及往复运动,每次循环中需读取对应时间点的温度场分析结果;
③在移动力的加载过程中,每移动一步都要在受力丝杆表面形成刚性区域并施加集中力载荷,完成该次运算后,删掉已施加的集中力载荷与刚性区域。
2.3 计算结果分析
(1)温度场结果分析
针对本次研究的丝杠传热系统,考虑传动速度及热载荷加载时间长短,对丝杠螺母 12 次循环后丝杠表面温度分布进行分析。为更直接的了解丝杠表面的温度分布情况,沿丝杠表面轴向每隔 50mm 取点,得到其温度分布。由图 3 可以发现,丝杠的工作温度梯度较为明显,轴承支撑处及丝杠中段有较大温升,丝杠工作部分温度基本趋于一致,但出现局部温度较高点,最高温度值达 25.53℃,这是由于丝杆螺母正好移动到该处所致;同时可以发现丝杠中部的温度在一定范围内出现小幅波动,这是由于丝杠表面移动热载荷的经过所造成的散热不均匀现象。丝杠左右两端的温度变化趋势相近,但不完全相同,这是丝杠两端的结构差异所造成的。
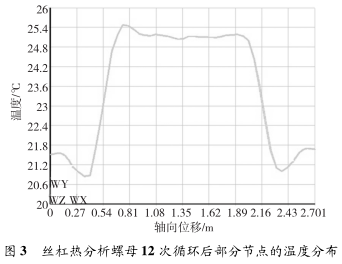
为了观察丝杠上某节点的温度变化趋势,在丝杠中部取一节点,得到该点随时间变化的温度曲线,如图4 所示由图可知,该点的温度整体成上升趋势,但每次循环期间会出现波动,其原因在于移动热源的往复运动。这一节点在一定程度上反应了前12 次循环工作区域各点的温度变化趋势。
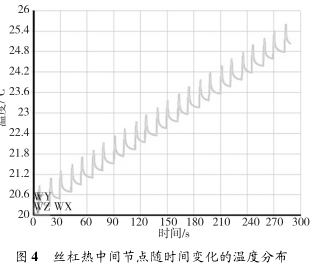
(2)热- 结构耦合结果分析
在温度场分析的基础上进行热- 结构耦合分析,考虑重力及丝杠螺母的支撑力作用,得到丝杠螺母往复循环12 次后丝杠表面的各节点的位移情况。本文沿丝杠表面轴向每隔50mm 取点,得到丝杠螺母往复循环 4、8、12 次及静力情况下,丝杠螺母处于丝杠中部时,丝杠轴向及重力方向的位移结果如图 5、图 6 所示。由图 5 可知,轴向最大变形发生在丝杠工作行程靠近两端处,循环12 次后螺母运动到丝杠中部时丝杠的最大伸长量约为15μm。随着循环次数的增加,丝杠轴向热变形的增长趋势较快,变形量也逐渐增大,最大值均出现在丝杠工作行程靠近两端处,相较于静力情况,12 次循环后轴向最大位移处位移增加 11.3μm,相对变化量较大。其变形原因主要为:丝杠的安装方式为两端固定,同时受到了重力和十字滑座对其竖直向上的支撑力作用。
当丝杠螺母运动到丝杠中部时,丝杠表面温度近似对称分布,热力学零点出现在靠近中点处,变形量为零。当丝杠螺母移动到不同的位置时,其热力学零点是在不断变化的。同时发现,丝杠在热变形最大点处易产生不均匀变化,对机床的进给传动精度和稳定性有不利影响,加工时应尽量在丝杠中部进行加工。
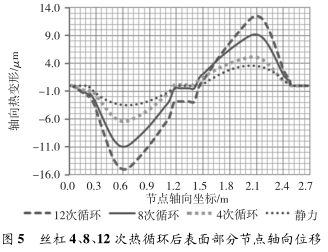
由图 6 可以发现,重力方向的最大变形发生在丝杠中部,12 次循环后,其最大伸长量为 86.2 μm,变形量较大。相较于静力情况,12 次循环后重力方向最大位移处位移增加 10.4μm,相对变化量较大。对于实际的丝杆安装过程中已加载预紧力的情况,其形变量会小于分析值,但其相对的变化量依然存在,最终影响重力方向的传动精度。
由分析结果可以看出,在发热区域适当增加油冷;加工时避开轴向变形较大处;将所得到的轴向及重力方向的热变形趋势和规律引入控制系统,从而为控制系统的误差补偿提供数据支持,是提升整机加工精度的关键所在。

3 丝杠热态性能实验研究
在实际加工中,为使机床的热变形趋于稳定,常需花费较多时间进行预热,降低了机床生产效率。本文运用米克朗 M7500 红外摄像仪进行丝杠温度场实验,将 ANSYS 模拟值与实际的温度测量结果进行对比分析,修正理论模拟数据,从而为机床控制系统在加工时进行补偿和结构优化提供更具实际价值的理论依据。
由于课题所分析的加工中心在该公司中没有实体可用于温度场实验, 因此本次实验采用该公司提供的另一型号数控机床进行 Y 向丝杠的温度场实时测量。
3.1 温度场实验
实验在恒温 20℃环境下进行,机床 Y 轴以 8000mm/min 的进给速度运行,测量机床从启动到丝杠表面达到热平衡时的温度变化情况,测量循环次数为400 次,并进行多次重复实验。温度场测量系统的软件控制流程及测量现场如图 7、图 8 所示。
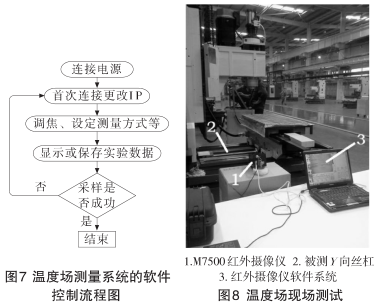
3.2 实验与仿真结果数据对比分析
由于温度实验的丝杠与课题分析丝杠不同,因此按前述相同方法对实测丝杠进行了模拟分析,用于实验参数对比。
由图 9 可以发现,经丝杠螺母 365 次循环后,丝杠中部温度较高,两端较低,与仿真温度分布情况类似;在丝杠中部取点,该点温度场仿真与实测结果对比曲线图如图 10 所示。由实测温度场曲线不难发现,前200s 温度上升较快,200s 后温度的增长速度逐渐减缓,最后在 31℃左右徘徊。由实测温度平均值与模拟值对比可以发现,前 120s 的曲线温升趋势相近,丝杠中部一点的仿真与实际测量值在丝杠螺母 12 次循环后分别为 25.8℃与 25℃,温度偏差小于 0.032%,该分析结果基本符合实际,一定程度上的验证了前温度场分析结论的准确性。
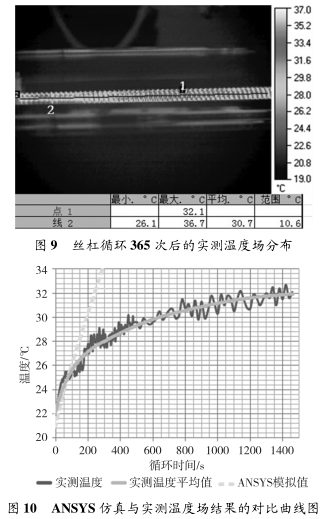
但随着循环次数的增加仿真分析数值几乎成直线上升的趋势,与实际温度开始趋于平缓的状况有很大偏差。分析发现造成这一结果原因在于:分析中假设热流密度与对流换热系数保持不变,而实际情况下随丝杆温度升高,空气对流加剧,在恒温环境下,对流换热系数将不断增大;丝杠螺母带动工作台移动,也其加剧了空气流动,使换热速率增大;丝杠表面的温升使通过丝杠螺母传入丝杠的热量减小,热流密度降低,当丝杠表面热量的流入与流出达动态平衡状态时,丝杠温度趋于稳定,即实验状态。只有随着温升改变相应仿真分析的热边界条件,才能最终使分析结果与实际相符。
3.3 方案改进与结果对比
将丝杠螺母的热流密度和对流换热系数都设置为随温度而变化的数值,前 40 次丝杠螺母循环的温度边界条件的设定如表 3 所示。
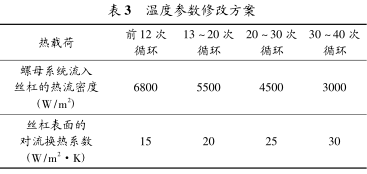
修改方案后,丝杠中部一点随时间变化的温度场仿真结果与实测温度场结果的对比曲线图如图 11 所示,图中不难发现前 320s 的温度分布与实测温度变化趋势相近,各点的温度误差不超过 0.05%,很好的模拟了丝杠温度场随时间变化的规律,为后续的热变形分析提供了更为准确的温度场理论数值。
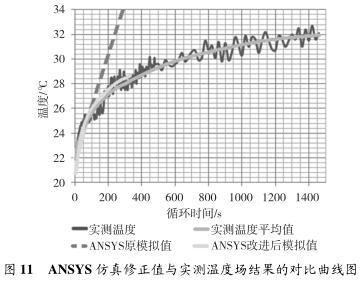
4 结论
本文为了解丝杠组件的热态性能对整机加工精度的影响,进行了 Y 向丝杠传动系统的热- 结构耦合分析。在前人的基础上考虑了重力及丝杠螺母对丝杠的支持力作用,同时在厂区进行了该结构的温度实验,最终得出以下结论:
(1)对 Y 向丝杠传动系统进行热- 结构耦合分析发现:在同时考虑移动热源、重力、螺母对丝杆支撑力作用的情况下,根据实际工况,施加不同循环次数的移动热载荷后,丝杠轴向位移变化量较小,重力方向位移变化量较大。但相较于无热源的情况其相对变化量均超过10μm,直接影响了该向加工精度值,因此改善散热和润滑条件、集中于丝杠中部进行加工、根据分析结果运用控制系统进行热误差补偿是减小丝杠热变形对加工精度影响的关键所在。
(2)对丝杠进行温度实验,将其与仿真计算结果对比分析,验证了部分温度场分析的合理性,同时也发现不足,并对分析边界条件进行改进,得到更为符合实际的理论分析结果,为企业高速高精度数控机床的温度补偿提供了可行的理论依据。
参考文献:略
投稿箱:
如果您有机床行业、企业相关新闻稿件发表,或进行资讯合作,欢迎联系本网编辑部, 邮箱:skjcsc@vip.sina.com
如果您有机床行业、企业相关新闻稿件发表,或进行资讯合作,欢迎联系本网编辑部, 邮箱:skjcsc@vip.sina.com
更多相关信息