加工中心进给轴可靠性试验加载装置设计与应用
2016-8-17 来源:青海大学机械工程学院 畅青海一机数控机 作者: 张长 段广云 苟卫东
摘要: 进给轴作为加工中心的关键组成部件, 其可靠性水平的高低直接影响到加工中心的加工精度和整机可靠性。提出进给轴可靠性试验的快速试验方法, 完成了进给轴可靠性试验装置的试验方案设计。通过进给轴可靠性试验装置的搭建, 开展了进给轴可靠性的相关加载试验,并将该试验结果与加工中心其他可靠性试验结果相结合, 通过相应的数据分析软件, 评定出机床的可靠性量化指标, 暴露加工中心进给系统设计、制造与装配等方面的缺陷, 以便采取对策和措施指导进给轴单元的可靠性设计, 从而保证进给轴设计和使用过程中的可靠性增长。
关键词: 加工中心; 进给轴; 加载装置; 可靠性试验
近年来我国机床行业发展迅速, 国内机床整体水平不断提升, 取得了许多重要的成就。然而与欧美和日本等高水平机床厂家相比, 我们的产品还存在较大差距, 主要体现在加工精度、运行可靠性、多功能复合等方面。其中, 可靠性是衡量一个产品性能的关键指标, 国内机床在这方面的表现却很难令人满意, 可靠性水平较低, 在很大程度上影响并限制了加工质量, 从而使用户在购买加工中心时犹豫不决。欲解决国产加工中心的购买量和满意度问题, 通过不断的可靠性试验研究提高其可靠性是关键所在。
加工中心作为机床的典型代表, 其可靠性水平的高低直接影响产品的加工质量, 因此, 如何提高加工中心的可靠性是一个亟待解决的问题。只有不断地进行加工中心可靠性试验方法和规范的研究, 提升加工中心的可靠性, 才能不断提高产品加工的效率和质量。
进给轴单元作为加工中心的重要部件之一, 它承担了加工中心各直线、回转坐标轴的定位和切削进给, 其可靠性的高低直接影响加工中心的寿命及其加工工件的精度。因此, 进给轴的可靠性在较大程度上影响加工中心的质量、维修性和经济性, 提高进给系统的可靠性对加工中心整机使用具有重要的意义。通过对加工中心进给轴进行可靠性试验研究可以获得评定其性能的重要指标, 这些指标无论对设计制造进给系统还是对用户选购加工中心都具有重要的指导意义[1-2] 。
1、加工中心进给轴可靠性试验方案设计
1.1 加工中心进给轴可靠性试验的方法
可靠性试验是实现可靠性设计、评价与分析的一种可靠性研究手段。而对于加工中心这样复杂的产品, 一般在产品的设计和研制初期存在的潜在失效和故障的残余量较大, 这也给产品的可靠性提升提供了可观的空间。另外产品的研制周期已成为市场竞争的焦点, 并且研制产品的数量也较少, 为了在较短时间内获取可靠性, 不能按传统的可靠性试验方法、使用较长时间来获取,而是采用可靠性加速试验方式来实现, 通过系统地施加应力, 激发和暴露加工中心产品的薄弱环节。由于可靠性加速试验目的是引起失效,在试验样本数量极少的情况下就能进行, 因此非常适用于像加工中心这样小批量多品种的产品, 它可以在较短时间内获取加工中心的故障情况和可靠性特征值。
可靠性加速试验的目的是在较短的试验时间内激发出故障, 该技术最早源自20 世纪50 年代的老化试验, 其理论依据是故障物理学, 通过对故障或失效的研究, 发现和根治故障以达到提高可靠性的目的。在国外, 可靠性加速试验在电子产品和机电产品的应用和推广使得产品的可靠性得到很大的提高, 对电子设备采用了高加速寿命试验并获得满意的结果。国内的可靠性加速试验因为受到试验方法和试验设备的限制, 目前还处于探索阶段。但该技术在数控机床可靠性试验方面的应用研究很少。文中将可靠性加速试验技术应用于数控机床加工中心, 目的是在比较短的时间内找出并消除故障, 提高整机的可靠性。
进给轴是机床的关键组成部件之一, 其性能优劣直接影响着整个机床的使用。从加工中心的故障统计和分析中可以看出, 加工中心进给系统的故障率较高, 仅次于刀库系统和主轴系统, 是加工中心的关键薄弱环节之一。因此开展进给轴可靠性试验可以采用模拟机床的实际工作状态。机床在进行实际加工时,切削力主要为: 主切削力、径向力、轴向力。如果能模拟实际的主切削力(切削合力), 如图1 (a) 所示, 对X 轴、Y 轴、Z 轴同步运动进行加载, 实现联动加载, 可以较真实地反映出机床实际承载状态。但由于机床空间、试验装置(体积、功能)、试验位置(加载点)、程序控制等因素的影响, 模拟主切削力(切削合力) 不易实现。如果分别对X 轴、Y 轴、Z轴进行单向加载, 如图1 (b) 所示, 虽然同实际状态有差距, 但通过加大施加载荷力度和变换加载方式, 在一定程度上也能反映出机床的承载状态, 而且也可达到可靠性试验的目的, 同时该方法操作方便、容易实现。所以对进给轴进行可靠性试验采用单向加载方案[3-4] 。
为了减少可靠性试验的周期, 系统采用加速试验的方法, 即对加工中心进给轴加载比实际载荷大的机械应力, 以期激发机床的潜在故障, 从而暴露设计中的薄弱环节, 通过分析手段, 找出故障原因,性增长。
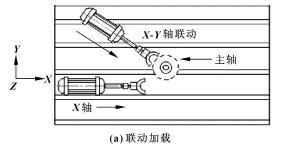
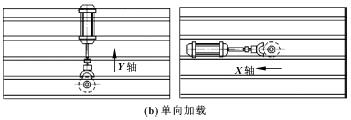
图1 进给轴可靠性试验加载方式示意图
1.2 加工中心进给轴加载试验总体方案
通过以上分析, 加工中心进给轴可靠性试验采用加速试验的方法, 在模拟工况载荷条件下, 用可靠性试验装置分别对机床的3 个进给轴X、Y、Z 轴进行单项加载, 以求最大程度地激发进给轴的潜在故障。图2 为该试验装置的组成框图, 主要包括: 加载气缸、压力传感器、加载计数器、气动控制系统等。该装置的工作原理是: 气缸在气动系统的控制下, 将模拟载荷施加到主轴上的模拟刀具; 通过力、加载计数器等传感器, 将试验机床参数和加载试验数据传输到电气控制装置, 经由数据采集卡传输到试验PC 机进行进一步的数据分析和处理, 得到相关的可靠性数据; 并将这些数据通过分析软件建模、拟合、归纳、运算, 从而预测出机床的可靠性指标, 找出发生故障的主要原因和模式, 实现进给系统的整体可靠性增长[5] 。
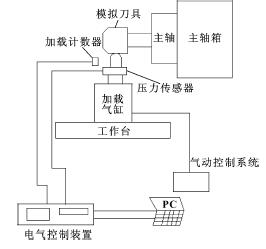
图2 进给轴可靠性试验装置设计方案
2、加工中心进给轴加载试验装置的实现
2.1 试验装置气动系统控制原理
气缸作为进给轴可靠性试验装置的主要设备, 在气动系统的控制下, 利用活塞的伸缩来实现对3 个进给轴施加载荷, 以期实现加载可靠性试验的目的。该气动系统以压缩空气为能源, 主要包括三联件(空气过滤器、减压阀、油雾分离器)、电磁阀、电气比例阀、单向节流阀、消音器等, 其工作原理是: 加载时, 压缩空气经由三联件过滤后, 得到相对纯净干燥的压缩空气, 经由电磁换向阀的左腔流出, 经电气比例阀的调节, 再经单向节流阀进入气缸的无杆腔, 推动活塞向右运动, 实现进给轴的加载。当加载时间到,电磁阀得电, 机床主轴推动活塞杆缩回, 完成一个循环的加载试验。具体气动控制原理如图3 所示。
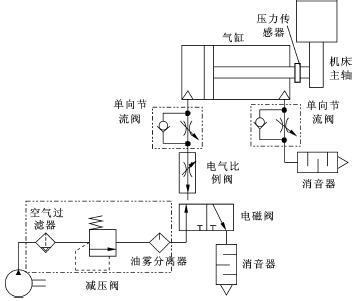
图3 进给轴可靠性试验装置气动系统控制原理
2.2 进给轴可靠性试验装置设计
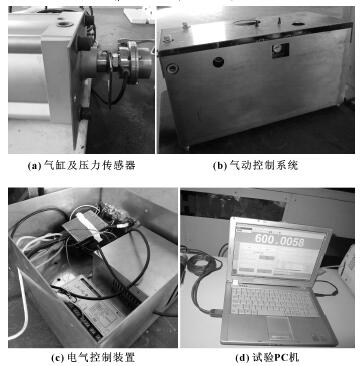
图4 加工中心进给轴可靠性加载试验装置
进给可靠性试验装置除了气动控制系统外, 还包括电气控制装置、试验PC 机及温度传感器、压力传感器等。其中, 温度传感器主要检测试验过程中机床电气柜的温度情况; 压力传感器用来检测试验过程中施加给主轴的实际载荷; 电气控制装置主要接收来自传感器的采集数据, 并把这些数据转换为PC 机能够识别的数据形式, 同时也将机床试验时的扭矩、功率等参数传送到试验PC 机。最终完整的主轴可靠性试验装置如图4 所示。
3、加工中心进给轴可靠性试验
进给轴可靠性试验装置设计完成后, 结合数据采集处理软件, 即可以开展可靠性的相关试验。根据加工中心可靠性试验规范, 在进行进给轴可靠性试验之前, 首先应该完成以下相关试验内容: 机床预运行检查(主要包括机床各安全防护装置是否安装和启用,并检验功能是否正常); 机床精度检验(测量X、Y、Z 等轴的位置精度和各轴快速移动速度)。
在以上试验完成后, 即可开展进给轴可靠性加载试验, 即在模拟实际工况条件下加大加载载荷, 利用进给轴可靠性试验装置对X、Y、Z 3 个进给轴分别进行加载; 并记录试验结果。在全部加载试验结束后,需要立即进行各项精度检验, 以验证加载试验后机床精度的稳定性。
3.1 试验内容
(1) 在主轴运转条件下, 分别对X 轴、Y 轴、Z轴反复施加轴向载荷, 从而考核机床各动作可靠性;
(2) 在机床空运行下, 考核机床规定的换刀、工作台快速移动和交换动作的可靠性;
(3) 记录加载各轴时间、机床运行时间;
(4) 检查机床各类故障, 记录故障数并分析故障产生的原因;
(5) 试验结束时完成相关几何精度和X、Y、Z轴位置精度检验, 以检验加载试验后机床精度的稳定性。
3.2 试验条件及方法
(1) 加工中心处于正常状态, 润滑系统、气动系统、液压系统和电气系统均正常;
(2) X 轴加载力应大于0畅75 倍的X 轴最大轴向抗力, 即大于5 100 N; Y 轴加载力应大于0畅75 倍的Y 轴最大轴向抗力, 即大于6 000 N; Z 轴加载力应大于0畅75 倍的Z 轴最大轴向抗力, 即大于3 150 N;
(3) 各轴加载试验时, 机床空运行和加载工作累计时间约48 h, 包括故障修复时间, 不包括安装辅助时间;
(4) X、Y、Z 轴加载时的进给速度应不小于300mm/min, 加载刀具转速应不小于500 r/min;
( 5) 空运行过程中, 加工中心能够实现最大直径、最大质量、最大长度的刀具换刀动作, 以期检验换刀动作的准确性;
(6) 活塞、加载气缸、测量装置等安装与使用应遵照仪器设备使用规定;
(7) 只有全部加载试验结束后, 才能进行各项精度检验, 并且先检验几何精度, 然后检验坐标轴的位置精度;
(8) 进给轴加载装置及测试数据报表见图5 (图中以X 轴为例, Y、Z 可靠性试验及结果输出类似X 轴)。
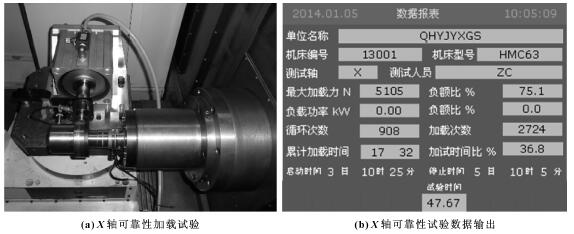
图5 加工中心进给轴可靠性试验现场图
3.3 试验结果及评定
(1) X 轴可靠性试验结果及评定见表1, Y 轴、Z 轴可靠性试验结果类似于X 轴, 在此省略;
(2) 记录加工中心几何精度和位置精度检验结果, 用来评价加工中心的精度稳定性。
表1 X 轴加载试验结果汇总及评定
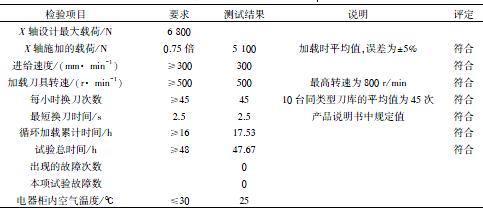
备注: 以上试验结果数据要参与最终可靠性指标计算, 应力求准确!
将以上X、Y、Z 3 个进给轴可靠性试验结果与其他可靠性试验结果相结合, 通过分析软件建模、拟合、归纳、运算,从而预测出机床的可靠性指标, 评定进给轴系统的设计和制造装配质量, 同时找出发生故障的主要原因, 实现进给轴整体可靠性的增长。
4、结论
系统阐述了加工中心可靠性试验的必要性和试验方法, 针对影响加工中心可靠性的关键薄弱环节之一进给轴, 提出了进给轴可靠性试验装置方案, 完成了试验装置的搭建, 并通过对3个进给轴进行一系列的加载试验, 记录相应的试验结果, 并将该试验结果与加工中心其他可靠性试验相结合, 通过分析软件的建模、运算, 评定出机床的可靠性量化指标, 从而评定出进给系统的设计和制造装配质量。同时可靠性试验结果可以帮助选择高可靠度和高安全性的零件, 再通过试验验证和不断改进完善, 提出相应的可靠性增长措施, 以此指导进给系统的可靠性设计, 从而保证进给轴设计和使用过程中的可靠性增长, 对于提高加工中心的整体可靠性有着重要的意义。
投稿箱:
如果您有机床行业、企业相关新闻稿件发表,或进行资讯合作,欢迎联系本网编辑部, 邮箱:skjcsc@vip.sina.com
如果您有机床行业、企业相关新闻稿件发表,或进行资讯合作,欢迎联系本网编辑部, 邮箱:skjcsc@vip.sina.com
更多相关信息