基子实B寸检测的飞机对合面加工系统设计和研究
2016-8-26 来源:陕西飞机工业(集团)公司等 作者: 马二萍 谭小群 李树军 罗喜东 梁泽荣
摘要:在研究飞机大部件对合面加工过程中,通过分析对合面加X-工艺流程.借助激光轮廓扫描仪获取加工面形状以及基准孔位置,计算出待加工面的平面度和孔位关系。实时检测对合面的加工状况,建立精确的飞机对合面加工工艺流程,以提高对合面加工精度和加工效率,从而提高飞机大部件装配精度。
关键词:加工中心激光轮廓扫描仪工艺流程加工精度
近几十年来,随着计算机技术、通信网络技术以及信息化技术的发展。飞机大部件数字化设计制造技术迅速提高n]。在飞机装配过程中,对大部件对合面进行精加工的目的是为了消除之前工序的累积误差,保证对接装配的协调性与互换性,进而保证飞机的装配质量。传统的飞机大部件对接装配方法采用人工强迫定位与装夹,且无法实现高效精确的对接面测量,导致对合面加工存在较大风险。大部件对合面在装夹状态下进行精加工,加工完成放松后会产生回弹变形,使相对理论尺寸发生偏移,导致对接困难,而且由人工进行精加工.精度和效率都非常低。
为了在飞机大部件数字化对接装配中实现以数控加工方法取代传统方法,笔者以某型飞机中外翼发房x,-J-接中对合面的加工系统设计和研究为例,详细说明飞机对合面加工过程中的基准检测和工艺过程,通过激光轮廓扫描仪对加工前对合面的平面度、轮廓、孑L位基准等进行检测,经过计算得出加工量和加工位置,为主轴铣平面和钻孔提供位置运动参数依据,完成对合面的完全对合。
1、对合面的加工特性分析
飞机大部件数字化装配系统中对合面的精加工包括面加工和孑L加工两部分.其中对合面的面加工主要为铣平面,使两个对合面可以完全贴合。对合面的孑L加工需要经过钻孔、扩孑L以及铰孑L等工艺步骤,必须保证精确的孔位、孔径和表面质量,才可以实现对合面的精确对合连接装配。对合面的材料类型对于精加工也有重要影响,主要包括铝合金7050、钢衬套30CrMnSiA等,不同材料的切削加工性能也存在较大差异。
2、对合面加工系统设计
对合面精加工设备采用专用加工中心.有4个独立的坐标运动,具备可在X、l,、Z 3个方向运动的联动控制单元。另外绕y轴进给方向有一回转工作台,可保证对合面的两侧加工。加工设备坐标轴的确定如图1所示。
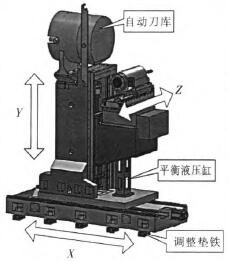
▲图1 加工设备结构示意
图1中,X向通过伺服电机控制运动,以实现加工单元沿对接面平行方向直线运动.采用精密的导轨丝杠系统保证其运动精度。y向通过带制动器的伺服电机实现同步运动,为防止进给机构在重力作用下下滑,配合平衡油缸实现y轴的平滑运动。Z轴由伺服电机驱动,并通过丝杠导轨进行传动.带动电主轴完成对合面的加工。
3、对合面加工检测系统
3.1 测量仪器选择
本测量系统采用德国MICR0一EPSILON高速激光轮廓扫描仪执行检测工作,其技术规格见表1。激光轮廓扫描仪与电主轴同轴安装在精加工设备上,其位置如图2所示。
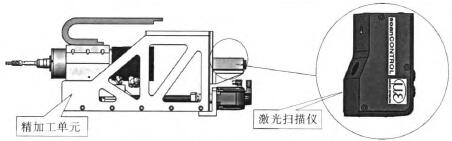
▲图2 激光轮廓扫描仪安装位置
3.2测量步骤
第一步,执行机翼对合端面的平面度和轮廓检测。加工设备快速移动到检测位置,激光轮廓扫描仪随着加工设备的移动扫描机翼对合端面轮廓信息并输人到控制系统。控制系统计算出中#1-翼八字板对
合端面加工量和钻孔位置。扫描过程示意如图3所示。
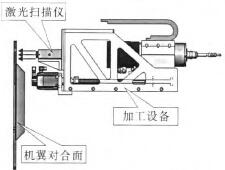
▲图3 机翼对合面扫描过程示意
第二步。执行发房对合端面平面度、轮廓检测。加工设备回转1800,移动至相应工位定位,激光轮廓扫描仪开始工作,扫描该对合端面轮廓信息并输人到系统,系统计算对合端面加工量和制孔位置。扫描过程如图4所示。
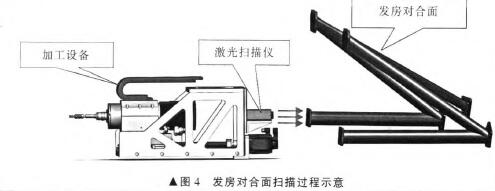
3.3测量结果
激光轮廓扫描仪在检测完成后会生成位置数据文件,数据文件中包含大量的测量数据信息。因为输出的测量数据格式为TXT文本文件.此格式文件可以采用程序方式顺序读取并转换为数据库文件。精加工设备实现自动化检测,需要对激光轮廓扫描仪进行应用软件的二次开发,进行待检测物三维轮廓信息的扫描以获取三维位置信息数据,如图5所示.最后对必要的面特征或孑L特征数据进行提取,解算需要的位置参数。
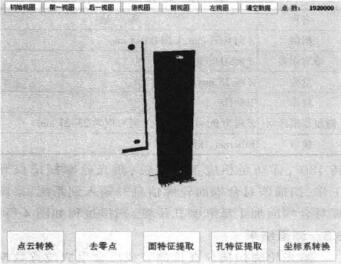
▲图5 扫描三维型面数据采集过程
3.3.1 对舍面平面度检测
基于三维点云数据进行曲面拟合,将数据中那些非实体上的点全部剔除,否则会对分析带来失真。在针对不同特征提取数据时所用的剔除算法也是不同的,针对基于点云进行平面拟合的需求,笔者采用的方法是:先拟合出实体所在的表面,然后根据点到拟合平面的距离来判断是否剔除。拟合平面使用最小二乘法拟合,该方法具有误差小、稳定性好的特点。特征提取过程如图6所示。
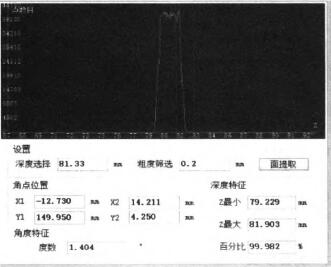
▲图6面特征提取及处理软件实现
基于最小二乘法拟合平面的思想.结合空间平面测量的点云数据求解后,平面曲面方程为:三=似+6,,+c,然后剔除离平面距离大于0.2 mm(软件中的粗度筛选值)的点,得到data zn数据点,再次经过曲面拟合的迭代计算,去除个别杂点.最后根据计算式:90。一arccos f1/
),可计算出检测平面与主轴的法平面之间的夹角,从而为主轴加工提供数据依据。

3.3.2 对合面基准孔特征检测
基于轮廓扫描仪配合伺服驱动实现孑L特征的三维型面扫描,以采集的点云数据为对象,提出了一种三维点云中圆的提取方法。此方法是结合点云的边界特征来提取的方法,并充分利用了点云和图像的对应投影关系特性以及图像处理中成熟的圆检测算法.如图7所示,提取出了三维点云中的圆。此方法简便快捷,易于实现。
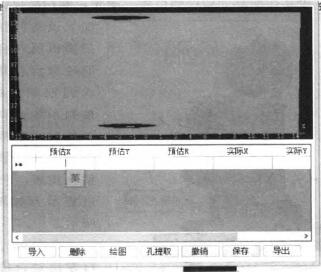
▲图7 7L特征提取及处理软件实现
4、对合面加工过程
通过激光轮廓扫描仪对机翼和发房两侧对合面进行扫描,计算得出对合面的加工余量和孑L位关系,采用精加工设备进行对合面加工,加工工艺流程如下。
(1)精加工设备移动到被加工端面再定位。
(2)激光轮廓扫描仪对发房对合接头平面以及连接孔进行检测。精加工系统反转,激光轮廓扫描仪对机翼对合端面及连接孔进行检测,调用对合面加工算法,计算平面加工量和孑L位误差。
(3)通过计算机对加工量和孔位误差进行评价。
(4)上述工作完成后,精加工系统首先更换铣刀,对机翼对合端面按照加工量进行铣削,然后,精加工系统反转.对发动机上支架端面进行铣削。铣削结束后需对机翼与发房的对合端面进行对合,检测对合度。
(5)对合度满足需求后,将精加工设备移回加工工位.对发房和机翼两侧对合端面的连接孔进行加工。
(6)完成连接孔的精加工后,将加工系统移动至下一个工位.进行下一个工位的加工。
5、对合面加工试验
为验证基于实时检测的飞机对合面加工系统的可行性,利用激光轮廓扫描仪对加工面进行扫描预处理,计算出对合面的加工余量.利用精加工设备进行对合面的精铣和钻孑L试验。对合面加工试验如图8所示,其中图8(a)为机翼对合面精铣结果;图8(b)为机翼对合面钻孔现场。精铣对合面后的平面度<0.05 mm,表面粗糙度R。3.2斗m。对合面孔加工结果为孑L径精度H7,表面粗糙度为|Rj.2“m,钻孔定位精度0.10 mm,重复定位精度0.05 mm,钻孑L垂直度偏差<0.3。,完全满足加工要求。
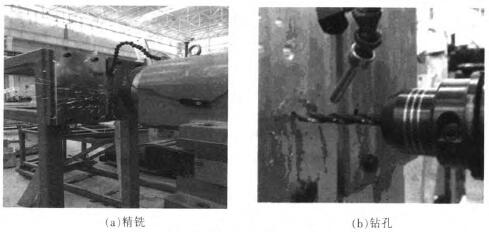
▲图8 对合面加工现场试
6、结束语
笔者提出了一种满足飞机对合面加工的实时检测方法。根据对合面的加二r:特点,对对合面的精加工系统实现数字化加一[,通过激光轮廓扫描仪确定对合面的加工余量。采用精铣平面和钻、扩、铰孔的孑L加工方法,并通过对合面试切加工试验,对加工方法的可行性进行了验证.实验结果满足对合面加工公差要求。
投稿箱:
如果您有机床行业、企业相关新闻稿件发表,或进行资讯合作,欢迎联系本网编辑部, 邮箱:skjcsc@vip.sina.com
如果您有机床行业、企业相关新闻稿件发表,或进行资讯合作,欢迎联系本网编辑部, 邮箱:skjcsc@vip.sina.com
更多相关信息