加工中心上定位基准的确定
2018-5-17 来源:转载 作者:郭伟民,武同,李义龙,蒋亚杰
摘要: 在明确定位基准概念及其遵循原则的基础上,结合加工中心的优点,具体分析长方体件、回转体件和异形件各自定位基准的确定方法,说明定位基准的正确选择有利于加工中心效能的发挥和产品质量的提高。
关键词: 定位基准; 加工中心; 长方体件; 回转体件; 异形件
基准按其作用不同,分为设计基准和工艺基准两大类。按用途不同,工艺基准又分为定位基准、测量基准和装配基准。定位基准指加工时使工件在机床或夹具中占据一正确位置所用的基准,若无特别说明,文中的定位基准均指轮廓要素。定位基准又可分为粗加工基准和精加工基准.加工中心具有工序集中等优势,客观上要求所选定位基准应尽量满足 “一次装夹,全部 ( 或大部分)加工”,所以加工前很有必要去认真筛选定位基准,以发挥加工中心的优势,减少装夹次数,提高产品质量,降低生产成本。
下面结合一些典型零件,初步分析在加工中心上如何确定其定位基准。
1、典型件定位基准的确定
1. 1 长方体件
如图 1 所示的某模具型芯,有 3 个面需要加工( 底面、左侧面和上表面) ,其下料尺寸为 281 mm ×261 mm × 331 mm ( 锯切下料,单边各留约 0. 5 mm 余量,各表面粗糙度基本一致) 。该形状适合用三平面定位方式,那么,选哪些面作定位基准? 哪个面作主基准呢?
首先分析一下加工工艺,可以分为三大步:
(1) 热处理前的粗加工及局部精加工,在三轴立式加工中心上需装夹 3 次 ( 选四轴卧式加工中心的话,可一次装夹完成全部加工; 只是底面在深孔加工时冷却效果不及在立式加工中心上的好) ;
(2) 热处理;
(3) 精加工包括左侧面和上表面在内的 6 个面,其中大平面的精加工可以安排在磨床上,局部狭窄凹槽等难铣削区域宜电火花加工,其余仍在加工中心上进行精加工。
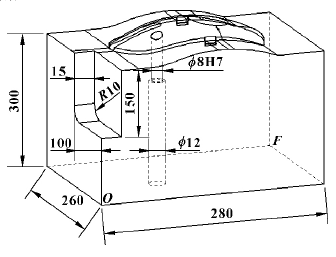
图 1 模具型芯
选择粗基准时,重点考虑如何保证各个加工面都能分配到合理的加工余量,保证加工面与不加工面的位置尺寸和位置精度,同时还要为后续工序提供可靠精基准。
选择平面作基准一般应考虑:
(1) 自身定位能力强弱,主要包括: 面域大小、平整程度、粗糙度、装夹难度、稳定程度 ( 不易变形、持久性) 等; 面积越大、粗糙度越低、装夹越方便的平面优先考虑。
(2) 相关定位能力强弱,主要是指对尺寸公差关系的影响程度和对基准原则的体现程度。尽量使定位基准与设计基准、测量基准和编程原点统一起来。在综合考虑上述因素的基础上,确定 3 个基准面的主次关系时,还应尽量避免主要定位基准与待加工面同方位,将其安排在待加工面的对面能有效抵抗切削力,也有利于精简夹具结构。选择第二定位基准应考虑其导向作用,与主定位基准的垂直度、粗糙度,以及同待加工面的位置关系。
加工上述模具型芯的 3 步中,每一步都存在着确定基准的问题,而且这么多工序,势必要统一基准。由于主要形状都在上表面,故与其对应的底面宜作主基准。另外,构成点 F 的两个侧面的面域较大,支撑效果好; 但再看设计尺寸的标注情况,在构成点 O的 3 个面上尺寸标注多,可视点 O 为设计基准,同时其面域用来支撑也是可以的,故从基准重合的角度,选构成点 O 的 3 个面作热处理前的定位基准。通常一套模具设计图上只有一个中心,各零部件的尺寸由此铺开。加工某具体零部件的时候,在该件具体的点、线、面上确立基准,依据尺寸关系,建立坐标系。如果 3 个面相互不很垂直 ( 一般情况下,毛坯都达不到这个要求) ,则可以在加工底面 ( 通常先加工底面) 的时候,以底面为主基准,在另外两个侧面上,根据需要,分别铣出一定长度的基准带供后续加工用,保证基准统一,如图 2 所示。
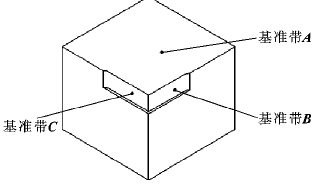
图 2 型芯毛坯定位基准
上述定位基准用在热处理之前的加工过程中。热处理之后,必须检测该基准自身的变形程度,以及形状面相对于基准的变形; 有时候会出现由于变形大而不能再作为基准使用的情况。因此,在热处理之前,应考虑并预留更可靠的精加工定位基准。选择精基准时,重点考虑的是如何减少工件的定位误差,保证零件的加工精度,同时也要考虑零件装卸方便,夹具结构简单。
一般应遵循以下原则: 基准重合、基准统一、自为基准、互为基准及装夹方便等。此例中,8 mm 孔经过铰刀精加工,表面质量好,因热处理而引起的变形也较小,可以作为精加工基准用。这就是随后要说到的一种比较典型的方法 -利用孔或轴的轮廓 ( 中心线) 作定位基准。以上说的是以模具型芯为代表的单件生产。长方体件在批量生产的时候,通常要利用夹具把 3 个基准面的位置固定下来,以提高效率。这样的例子很常见,文中不再赘述。
但如图 3 所示的长方体工件的基准确定,稍微有些特殊。该件形状并不复杂,突出特点是尺寸公差要求很小 ( ± 0. 01 mm) 。属来料加工,其下料尺寸为 76 mm × 45 mm × 51 mm,为了减少装夹次数,生产中将长度方向的定位块采用了活动量块,装夹 ( 如图 4 所示) 时定位,装夹好后移走,这样在一次装夹下加工完两端面和顶面,实现了工序集中最大化,减少了装夹次数,充分发挥了加工中心的优势,也保证了 ( 75 ± 0. 01) mm 等尺寸要求。由于加工过程中长度方向上不存在定位,所以属于不完全定位; 不过实际加工效果还好,几乎很少有攒动。关于该件的加工,随后将专门介绍。
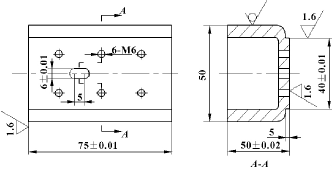
图 3 滑块
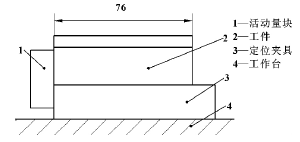
图 4 滑块装夹示意图
1. 2 回转体件
回转体件的定位基准通常选择其内 ( 外) 表面。基本方法是: 利用百分表的针头 ( 或光电感应器的触头等) ,沿十字形测出 4 个点的中心即为中心线位置,详见图 5。具体测量时,应先在孔的正上方 2 ~ 3mm 处旋转表针,使针头大致在被测孔径外侧 ( 轴的话,应偏向内侧) ,然后轻压表针使之进入孔内,首先找出某一方向上对称两点 (如点A和C 或与 AC 线平行的某一位置上的两点) 的对称中心,在此中心线 ( CD 线) 上再找点 C 与 D 的等分点O ( 期间需要调整针头位置) ,找出之后再旋转一周,查看表针跳动情况,以检查刚才确定的AC 线是否经过点O,从而最终找出圆心O 的机床坐标 ( 旋转一周,表针静止不动或轻微震颤) 。
在确定过程中应注意,表针静止不动有 3 种可能:
(1) 未接触内表面;
(2) 与内表面之间的压力太大而不能跳动;
(3) 主轴在圆心位置。
由于最终记录的是圆心位置,视轴线为定位基准也未尝不可。关文献研究证明二者无实质差别。
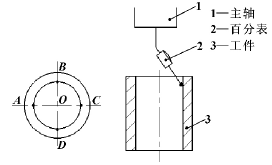
图 5 回转体件基准孔找正
Z方向的基准可优先考虑上表面。至于哪一个为主基准,应结合加工余量和表面粗糙度确定。通常,以回转体为主要特征的零件,内 ( 外) 表面的定位作用更重要一些,因为它往往会是设计基准,尺寸公差关系多,限制工件自由度数目多。
由于杠杆百分表与工件接触的顶端直径为 3 mm,所以只要孔径大于 6 mm,就可以使用; 小于 6 mm时,可以考虑插入心轴,测外径。在通过 CAPP 系统选择定位基准的时候,为了确保正确决策和加工精度,这些影响因素也应被考虑。同理,用键槽作定位基准的时候,由于量块可以塞进去,所以理论上,宽度 1 mm 以上的键槽都是可能的定位基准,在利用CAPP 系统选择定位基准的时候,亦不应被忽略。
1. 3 异形件
若工件上缺少可作为定位基准的恰当表面,就有必要人为地制造一些基准面,使其在加工中起定位作用,这类基准称为辅助基准。
图 6 为某产品示意图,批量生产,除了 “成型面”部分之外,其余 5 个面均为配合面,都需要精加工,精度要求高,同时成型面上无法装夹。那么该怎样装夹、定位好呢?
仔细观察产品图可以发现,由 R1、R2、R3所形成的圆弧面以及构成尺寸 70 mm 的上下面都是潜在的定位基准选项。经过分析,最终确定了 R1、R3和上平面分别为不同工序的定位基准,但仅此还不能保证各工序的准确定位和装夹.
在不妨碍使用的前提下,在原产品图上增加工艺孔: 在顶面增加 M8 螺纹,在背面增加 3 × M8 ( 口部10H7 深 8 mm 作定位用) ,故修改产品图如图 7 所示。在此基础上,进而设计出如图 8 所示的铸造毛坯图,在铸件上又增加辅助定位基准面 A、B 和 C ( 这3 个基准属于增材,使用后都去掉) 。
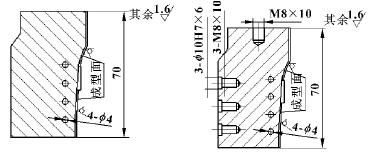
图6 某异形件产品图
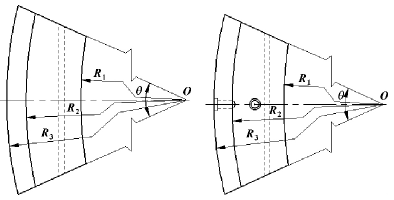
图7 带工件艺孔的异形件产品图
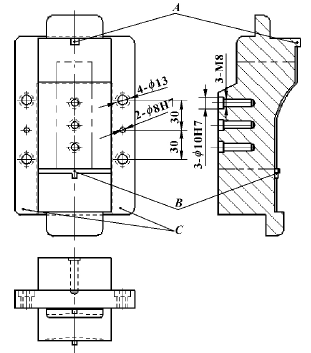
图8 异形件毛坯图
如前所述,这些基准分别在不同工序中使用,基准统一原则该如何保证呢? 解决办法是: 利用加工中心加工精度高且工序集中的优势,尽量在一次装夹中把所有可以加工的定位基准都加工出来; 确实暂不能加工的,则为其加工辅助定位基准。从实际加工结果看,这些定位基准有效地保证了产品质量。
这些辅助基准在加工后失去作用,属于增材的话,事后通常会被去掉; 减材类 ( 如工艺孔) 一般不影响产品使用,则保留。
从上例可以看出: 对于批量生产的异形件,在确定基准时,应紧密结合加工工艺,充分利用现有形状上的平面和圆弧面等; 必要时再通过增材或减材的办法,增加辅助定位基准,从而保证产品质量。
2 、结束语
加工中心具有工序集中、生产效率高和加工质量好等优点,在加工中心上确定工件定位基准的时候,应考虑如何充分发挥加工中心的优势,实现产品加工的高品质和高效率。文中对长方体件、回转体件和异形件定位基准选择的分析,虽然具体方法不同,但指导思想是一致的: 紧扣产品的加工特征,注重充分发挥加工中心的优势,寻求高效优质的加工过程。
不过,文中只是对加工中心上定位基准的确定方法做了一个初步总结,还不够全面,还有很多情况需要今后进一步总结、提炼.
来源:河南职业技术学院机电工程系,河南郑州 西北工业大学机电学院,华北水利水电大学机械学院
投稿箱:
如果您有机床行业、企业相关新闻稿件发表,或进行资讯合作,欢迎联系本网编辑部, 邮箱:skjcsc@vip.sina.com
如果您有机床行业、企业相关新闻稿件发表,或进行资讯合作,欢迎联系本网编辑部, 邮箱:skjcsc@vip.sina.com