高速拉床突变负载工况的液压冲击仿真分析
2018-10-23 来源:中南大学机电工程学院 作者:桂珍,柳波,刘琪,郭林林
摘要: 高速拉削因能够得到较高的表面质量而逐渐在制造工艺中得到重用。拉削开始和结束时,拉削力是突变载荷,必然会对高速拉床的高压大流量液压系统造成压力冲击,引起速度波动,进而影响拉削的尺寸精度和表面质量。基于拉床负载特性,利用 AMESim 软件对高速拉床液压系统的拉削过程进行仿真,分析了高速拉床在突变负载工况下,液压缸进油腔的压力变化和主溜板速度及加速度的变化,并根据仿真结果改进液压系统。结果表明: 在液压缸的进油腔放置低压蓄能器能有效降低系统启动时的压力冲击; 利用突变负载反馈 PID 控制,可以有效降低拉削开始和结束时的压力冲击和速度波动。
关键词: 高速拉床; 负载力; 压力冲击; 速度波动
0、 引言
拉床,是使用拉刀作为刀具加工孔类、齿轮、键槽和花键等成形表面的机床。工件经拉削后,具有较高的尺寸精度和表面质量。随着制造技术的不断发展,拉床速度不断提高,经过大量的实验证实,许多金属材料在高速拉削的条件下,具有更高的尺寸精度和表面质量。目前,许多学者对高速拉削进行了研究和探讨。姜雪梅对高速拉削工艺进行了分析和实验,为获取更高的表面质量提供了参考。倪敬等人对拉床双缸进行 IPSO-PID 伺服驱动,解决了双缸同步驱动问题。刘建强等人对高速拉削力和拉削热进行有限元分析,得出了齿升量对拉削力影响最大及速度对拉削温度影响最大的结论。当前,研究较多的是电气 -机械传动的高速拉床,对液压高速拉床探讨较少,大多只是针对液压元件进行分析和设计,没有对其突变负载工况进行研究。
对于高速拉床,高压大流量的液压系统是其主要的动力源,所以液压系统的稳定性对拉削的尺寸精度和表面质量有决定性作用。拉削开始和结束时,拉削力是突变载荷,必然会对高压大流量液压系统造成压力冲击,引起速度波动,影响液压缸的密封性能,降低拉削的表面质量,因此,对高速拉床拉削过程中的液压系统进行仿真分析,有较重要的工程意义和实用价值。本文以上拉式高速液压拉床为主要研究对象,利用 AMESim 软件建立液压系统模型,分析拉削过程中液压缸进油腔压力特性、主溜板速度及加速度特性,并提出相应的系统改进方案。
1 、高速拉床速度和负载特性分析
1. 1 高速拉削的定义
当拉削一种金属材料时,加工的表面质量与拉削速度呈现一定的关系: 第一阶段,拉削速度从零开始提高时,材料表面质量下降,并形成锯齿形切屑。第二阶段,当拉削速度继续提高,至某一数值后,材料表面质量不再下降,反而逐渐提高,锯齿形切屑逐渐消失。而后,随着速度不断提高,材料表面粗糙度值逐渐减小,直至某一值后趋于稳定。第三阶段,进一步提高拉削速度,材料表面质量快速下降,刀具磨损加快。由于每种材料的切削性能不同,适应的速度也不尽相同,所以高速拉削的“高速”定义不能按照拉削速度的绝对值来说明,而应该是使材料处于第二阶段的拉削速度。即使有些材料的拉削速度在 10m/min 以下,只要该速度使得材料处于第二阶段,就称其为高速拉削。对于一般材料,如结构钢,其高速拉削速度可达 30 ~ 60m/min 甚至更高。
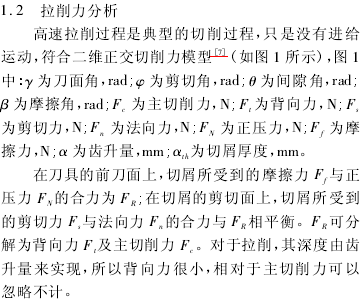
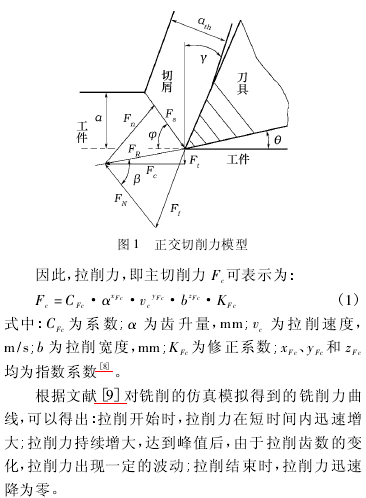
1. 3 高速拉床负载特性分析
上拉式内拉床一般是刀具不动,工件随着主溜板运动从而在拉刀上形成拉削效果。拉床启动后,工件和主溜板跟随液压缸向上加速运动,直至预定速度后,开始匀速上升。由于加速行程短,目标速度大,所以主溜板需要较大的加速度,这会使液压缸有较大的惯性负载,引起进油腔压力变化。工件和主溜板匀速上升时,液压缸所受的负载力为主溜板、工件和液压缸活塞杆的合重力 G。当液压缸到达一定高度后,工件接触固定拉刀,开始拉削。拉削过程中,液压缸所受的负载力为合重力 G 与拉削力之和。随着参与工作的拉削齿数量迅速增加,拉削力极速上升,直至最多的拉削齿参与拉削,此时拉力达到最大,液压缸所受的负载力也达到最大。但是由于拉削齿数量的微小变化,拉削力出现一定的波动。拉削结束时,拉削齿退出工件,拉削力迅速降为零,此时液压缸负载力突然减小,使进油腔压力迅速减小。
2 、高速拉床建模
2. 1 高速拉床液压系统
根据实际生产要求,基于 L55720 型机床,设计最大拉 削 速 度 为 60m/min,即 1m/s,最 大 拉 削 力 为100k N。拉刀长度为 1 000mm,进刀行程为 100mm,退刀行程为 150mm。高速拉床液压系原理如图 2 所示。
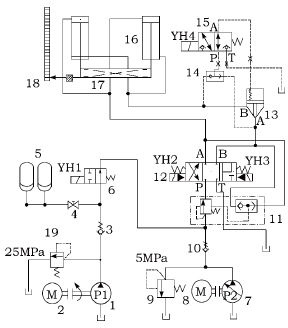
图 2 高速拉床液压系统原理图
1. 高压泵 2、8. 电动机 3、10. 单向阀 4. 截止阀 5. 高压蓄能器6. 二通换向阀 7. 低压变量泵 9. 低压溢流阀 11. 压力补偿阀12. 电磁比例换向阀 13. 二通插装阀 14. 梭阀 15.二位三通阀16. 液压双缸 17. 主溜板 18. 传感器 19. 高压溢流阀
在拉削过程中,由于负载力较大,而且拉削速度快,需要向液压系统提供高压、大流量的油液,所以由高压泵 1 和两个高压蓄能器 5 供油。此时电磁比例换向阀 12 处于左位,二通换向阀 6 处于右位,二位三通阀 15 处于左位,二通插装阀 13 的背压口泄油,其 A、B口相通。油液经过电磁比例换向阀 12、二通插装阀 13到达液压双缸 16 的下腔,即有杆腔,推动活塞上升,带动主溜板和工件向上运动。此时,系统压力较高,低压变量泵 7 通过低压溢流阀 9 卸荷。当主溜板下降时,系统由低压变量泵 7 供油。液压油经过电磁比例换向阀 12 到达液压双缸 16 的无杆腔。有杆腔的液压油经过二通插装阀 13 及电磁比例换向阀 12 的 P 型机能,与低压变量泵 7 的油液汇合流回液压双缸 16 的无杆腔中。同时,高压泵1 向两个高压蓄能器 5 供油,使其充能,为下一次拉削作准备。表 1 所示为高速拉床液压系统主要技术参数。
2. 2 高速拉床液压系统数学模型
本文研究的高速拉床液压系统是通过电磁比例换向阀控制非对称液压缸的运动方向,其基本模型为阀控非对称缸模型。本文主要分析高速拉床液压系统拉削工作过程的动态。
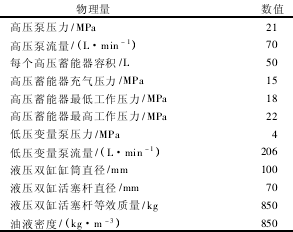
表 1 高速拉床液压系统主要技术参数
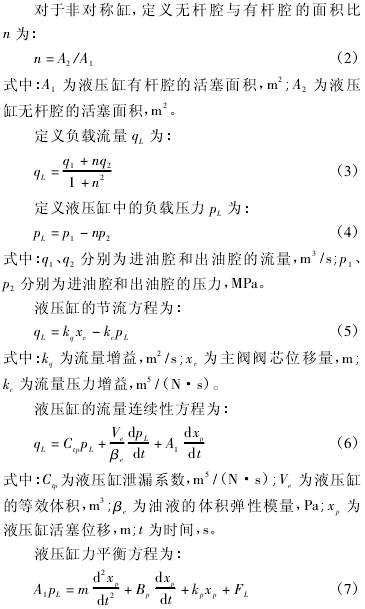

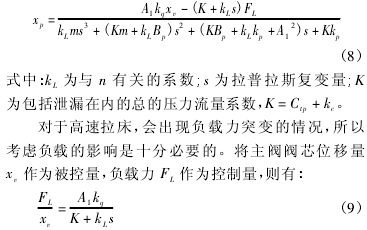
2. 3 高速拉床
AMESim 模型根据上述对高速拉床液压系统的分析,在拉削过程中,系统由高压泵和两个高压蓄能器供油,电磁比例换向阀处于左位,二通插装阀的 A、B 口相通。高速拉床拉削过程的液压系统 AMESim 模型如图 3 所示。图 3 中,使用液压缸 8 来模拟拉床的主油缸,质量块 9 模拟液压缸活塞杆的等效质量。负载力 10 模拟拉削过程的拉削力。按匀加速运动预估拉刀达到最大速度的时间为 0. 2s,为了便于观察结果,设置拉削力在拉削开始 0. 3s 后用时 0. 02s 由 0 增加到最大值100k N,保持最大值 0. 4s 后,用时 0. 03s 降为 0。根据实际物理模型,设置电磁比例换向阀 6 主阀频响为120Hz; 质量块 9 的质量为 850kg,其与水平方向的角度为 90°( 表示竖直放置) ; 其他参数与液压系统参数相同。根据软件设置习惯,设置仿真步长为 0. 001s,仿真时间为 1. 2s。
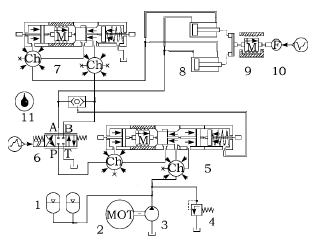
图 3 高速拉床拉削过程的液压系统
AMESim 模型1. 高压蓄能器 2. 电动机 3. 高压泵 4. 溢流阀 5. 压力补偿阀6. 电磁比例换向阀 7. 插装阀 8. 液压缸 9. 质量块10. 负载力 11. 液压油
2. 4 仿真结果分析
根据上述 AMESim 模型,在 AMESim 软件中运行仿真,得到液压缸进油腔压力曲线( 如图 4 所示) 、主溜板速度及位移曲线( 如图 5 所示) 及主溜板的加速度曲线( 如图 6 所示) 。从图 4 中分析可知,系统启动时,液压缸进油腔压力峰值是正常空载压力的近 3 倍,液压缸压力冲击大,会引起噪声和振动,并给液压缸密封元件带来不利影响。拉削开始和结束时,液压缸进油腔压力瞬间增大和瞬间减小,产生压力冲击和空穴现象,均会影响液压缸寿命。由图 5 中分析可知:主溜板启动不平稳,速度波动较大,会产生抖动; 速度波动时间长,达到稳定速度的行程较长,为0. 162m,比预定的进刀行程 100 mm,即 0 . 1 m 长。 拉削开始时,主溜板速度瞬间降低,产生迟滞现象,使零件加工时产生锯齿形切屑,材料的表面粗糙度值增大,尺寸精度降低,废品率增加。
拉削结束时,主溜板速度瞬间增大,出现突跳,影响主溜板两端的平衡,从而影响拉削精度。由图 6 中分析可知: 系统启动时,主溜板的瞬时加速度绝对值超过了 100m /s2,加速度过大会影响液压x的密封性能,甚至破坏拉床结构;拉削开始和结束时,加速度波动幅度大,直接影响了拉削的稳定性。
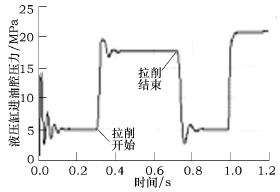
图 4 液压缸进油腔压力曲线
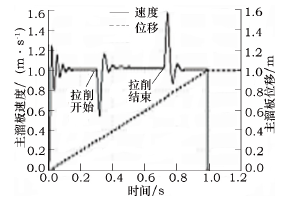
图 5 主溜板速度及位移曲线
3、 系统改进
3. 1 系统改进
由图 4、图 5 及图 6 中分析可知,系统启动时压力冲击较大,速度波动时间长。系统中虽然有高压蓄能401器,但是由于高压蓄能器是动力源,不能吸收冲击,所以拉削开始和结束时,速度波动较大,影响拉削的尺寸精度。根据以上分析,对液压系统进行改进,改进后的液压系统如图 7 所示。
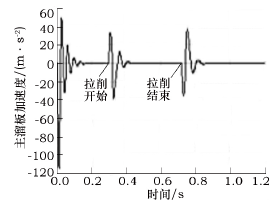
图 6 主溜板加速度
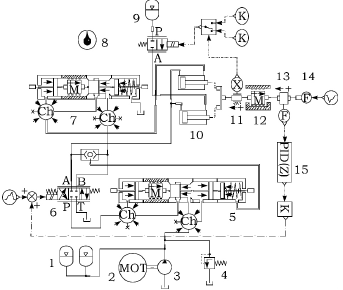
图 7 改进后的液压系统
1. 高压蓄能器 2. 电动机 3. 高压泵 4. 溢流阀 5. 压力补偿阀6. 电磁比例换向阀 7. 插装阀 8. 液压油 9. 低压蓄能器 10. 液压缸11. 位移传感器 12. 质量块 13. 力传感器 14. 负载力 15. PID 控制器
由于高速拉床液压系统空载时液压缸进油腔压力远小于拉削时的压力,故在图 7 中可以利用低压蓄能器 9 吸收液压缸启动时的压力冲击。根据系统正常启动后的空载压力,设置低压蓄能器的充气压力为4MPa,工作压力为 5MPa; 根据蓄能器吸收能量与超调能量相平衡的原则,计算得到低压蓄能器的体积为5L。系统处于拉削状态时,低压蓄能器不能与主油路连通,否则高压系统会向低压蓄能器充液,破坏低压蓄能器,所以需要利用位移传感器 11 反馈主溜板的位移来控制低压蓄能器的接入状态。拉削开始及结束时,由于负载力变化大且快,导致液压缸速度波动大,所以需要根据负载力的变化补偿主阀阀芯的位移量,以满足速度稳定所需的流量,故在系统中增加 PID 控制器 15。根据式( 9) 计算及试凑法可以得到,当 PID控制器中的比例系数 Kp= 3,积分系数 Ki= 2,微分系数 Kd= 10. 3 时,系统状态能达到最优。
3. 2 改进后系统仿真分析
仿真设置与改进前仿真设置保持一致。改进前后液压缸进油腔压力对比曲线如图 8 所示。
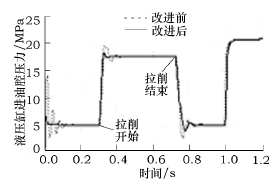
图 8 改进前后液压缸进油腔压力对比
由图 8 中分析可知,改进后系统启动时,由于低压蓄能器吸收冲击,液压缸进油腔压力波动明显减小,此时压力峰值为 7. 33MPa,比改进前的峰值 13. 81MPa减少了 6. 48MPa。相对正常空载压力 4. 95MPa,波动幅度减少了 131. 1% ,从而使噪声源明显减弱。而且,波动时间短,改进后的系统,启动 0. 032s 后压力基本稳定,比改进前的 0. 172s 缩短了 0. 140s,可以使系统快速进入稳定状态。拉削开始和结束时,由于根据负载力变化对主阀阀芯位移量进行了补偿,液压缸进油腔压力波动明显减小,拉削开始时进油腔压力波动由10. 5% 降为 4. 1% ,拉削结束时由 46. 5% 降为22. 1% ,可降低油液对液压缸的冲击,增加密封元件的寿命。改进前后主溜板速度及位移对比如图 9 所示。
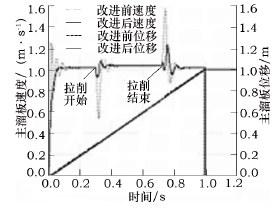
图 9 改进前后主溜板速度及位移对比
由图 9 中分析可知,改进后系统启动平稳,速度基本无波动,位移为 0. 079m 时,速度基本稳定在1. 01m/501s 左右,达到稳定速度的行程小于预定的进刀行程100mm,即 0. 1m,给调整刀具留有一定空间。拉削开始后,在 PID 控制下,将负载力的变化传递给主阀,增加主阀阀芯的位移量,补偿由于负载力增大产生的迟滞现象,使液压缸速度波动减小,此时的最低速度为0. 93m / s,波动幅度由原来的 46. 6% 降为 9. 7% ,使拉削速度尽可能保持在高速拉削的范围内,减小锯齿形切屑形成的几率,保证拉削的表面质量。改进后的系统,速度波动时间为 0. 102s,比改进前的波动时间0. 140s 大幅减小,减小了主溜板的抖动时间。拉削结束时,负载力突然减小,PID 控制使主阀阀芯位移量减小,从而减小液压系统流量,避免液压缸出现较明显的突跳现象,这阶段波动行程约 0. 140m,小于预定的退刀行程 150mm,即 0. 15m,使主溜板在停止前能平稳运行。改进前后主溜板加速度对比曲线如图 10 所示。
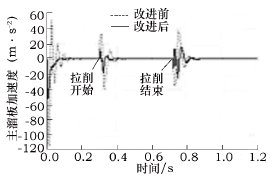
图 10 改进前后主溜板加速度对比
由图 10 中分析可知,改进前的主溜板启动加速度绝对值高达 112. 86m/s2,而改进后的加速度降低了一半,其绝对值最大为 52. 25m/s2,减小了对液压缸密封元件的冲击,可增加密封元件的寿命。改进前,拉削开始 和 结 束 时 的 加 速 度 绝 对 值 最 大 分 别 达 到37. 76m / s2和 35. 73m/s2,而改进后的加速度也都明显降低,其绝对值最大分别为 17. 57m/s2和 25. 77m/s2,分别减小了 53. 5% 和 27. 9% ,增加了拉削稳定性,减小了拉削速度的波动,使拉削速度尽量保持在高速拉削的范围内,从而保证其表面质量,减少废品率。
4 、实验验证
虽然仿真分析能在很大程度上呈现出系统的动态特性,但是仿真模型是将物理模型简化和理想化,并作出一系列假设得到的,所以还需要用实验验证仿真结果的合理性和正确性。利用 L55720 型机床进行改装,组成了高速拉床实验样机,如图 11 所示。实验以最大速度拉削 45 钢为例,液压缸进油腔压力与主溜板速度实验曲线分别如图 12、图 13 所示。将两个曲线分别与图 8、图 9 的曲线对比经分析可知,整个拉削过程中,液压缸进油腔的压力变化和主溜板速度变化趋势均与其对应的仿真结果基本一致。特别是在系统启动、拉削开始和结束时,两者的变化与其对应的仿真结果基本一致,只是实验的波动幅度比仿真结果略大,这主要是因为仿真分析将液压管路、液压缸等理想化,而实际情况并非如此。在平稳拉削过程中,液压缸进油腔压力和主溜板速度都有一定波动,这主要是由于拉削过程中实际拉削齿数量变化导致拉削力变化造成的,而仿真中则假设拉削力不变。整体而言,仿真结果比较符合实际工况,较真实地反映了高速拉床在突变负载工况下的动态特性。
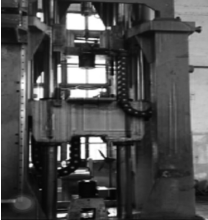
图 11 高速拉床实验样机
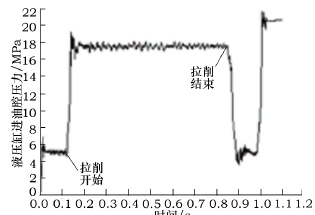
图 12 液压缸进油腔压力实验曲线
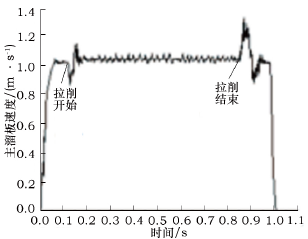
图 13 主溜板速度实验曲线
5、 结语
1) 本文通过对高速拉床液压系统仿真分析可知:系统启动压力波动大,波动时间长,不能快速进入稳定状态; 拉削开始时速度降低较明显,易产生锯齿形切屑,影响拉削精度; 拉削结束时,速度明显上升,出现突跳现象。
2) 对系统进行改进: 利用液压缸行程反馈控制低压蓄能器吸收系统启动冲击,能有效降低液压缸进油腔压力波动、噪声和振动,避免对液压缸密封元件产生较大破坏,减小波动时间,使液压缸快速稳定地达到预定速度,为拉削工作做好准备; 通过 PID 控制将负载力的变化反馈到主阀阀芯的位移上,使液压系统的流量得到补偿,降低液压缸的压力冲击和速度波动。结果表明: 系统改进后,拉削开始时,速度波动明显减小,速度基本保持在高速拉削的范围内,可以避免产生锯齿形切屑,从而保证拉削的尺寸精度和表面质量,减少废品率; 拉削结束时,有效减少了主溜板的突跳现象,避免产生空穴现象而影响液压缸密封元件的寿命。
投稿箱:
如果您有机床行业、企业相关新闻稿件发表,或进行资讯合作,欢迎联系本网编辑部, 邮箱:skjcsc@vip.sina.com
如果您有机床行业、企业相关新闻稿件发表,或进行资讯合作,欢迎联系本网编辑部, 邮箱:skjcsc@vip.sina.com